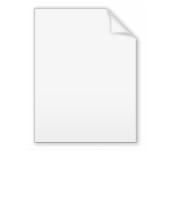
Industrial process
Encyclopedia
Industrial processes are procedures involving chemical
or mechanical
steps to aid in the manufacture of an item or items, usually carried out on a very large scale. Industrial processes are the key components of heavy industry
.
Most processes make the production of an otherwise rare material vastly cheaper in price, thus changing it into a commodity
; i.e. the process makes it economically feasible for society to use the material on a large scales, in machinery, or a substantial amount of raw materials, in comparison to batch or craft
processes. Production of a specific material may involve more than one type of process. Most industrial processes result in both a desired product(s) and by-product
s, many of which are toxic, hazardous, or hard to deal with. Very, very few processes are self-contained.
for reshaping a material by cutting, folding, joining or polishing, developed on a large scale from workshop techniques.
Example-planing,shaping,milling,punching,drilling,grinding
Distillation
was from meteorites, or as a by-product of copper
refining. Heating iron ore and carbon in a crucible at 1000 K produces wrought iron
. This process gained popularity during the Iron Age
. Temperatures of 1300 K were produced around the 8th century by blowing air through the heated mixture in a bloomery
or blast furnace
(12th century); producing a strong but brittle cast iron
. Furnaces were growing bigger, producing greater quantities; a factor contributing to the Industrial Revolution
. In 1740 the temperature and carbon content could be controlled sufficiently to consistently produce steel
; very strong and very workable. The 19th century saw the development of electric arc furnace
s that produced steel in very large quantities, and are more easily controlled.
A list by process:
Chemistry
Chemistry is the science of matter, especially its chemical reactions, but also its composition, structure and properties. Chemistry is concerned with atoms and their interactions with other atoms, and particularly with the properties of chemical bonds....
or mechanical
Mechanization
Mechanization or mechanisation is providing human operators with machinery that assists them with the muscular requirements of work or displaces muscular work. In some fields, mechanization includes the use of hand tools...
steps to aid in the manufacture of an item or items, usually carried out on a very large scale. Industrial processes are the key components of heavy industry
Industry
Industry refers to the production of an economic good or service within an economy.-Industrial sectors:There are four key industrial economic sectors: the primary sector, largely raw material extraction industries such as mining and farming; the secondary sector, involving refining, construction,...
.
Most processes make the production of an otherwise rare material vastly cheaper in price, thus changing it into a commodity
Commodity
In economics, a commodity is the generic term for any marketable item produced to satisfy wants or needs. Economic commodities comprise goods and services....
; i.e. the process makes it economically feasible for society to use the material on a large scales, in machinery, or a substantial amount of raw materials, in comparison to batch or craft
Craft
A craft is a branch of a profession that requires some particular kind of skilled work. In historical sense, particularly as pertinent to the Medieval history and earlier, the term is usually applied towards people occupied in small-scale production of goods.-Development from the past until...
processes. Production of a specific material may involve more than one type of process. Most industrial processes result in both a desired product(s) and by-product
By-product
A by-product is a secondary product derived from a manufacturing process or chemical reaction. It is not the primary product or service being produced.A by-product can be useful and marketable or it can be considered waste....
s, many of which are toxic, hazardous, or hard to deal with. Very, very few processes are self-contained.
General processes
These may be applied on their own, or as part of a larger process.- Liquefaction of gasesLiquefaction of gasesLiquefaction of gases includes a number of phases used to convert a gas into a liquid state. The processes are used for scientific, industrial and commercial purposes. Many gases can be put into a liquid state at normal atmospheric pressure by simple cooling; a few, such as carbon dioxide, require...
- for ease of transportation - Supercritical dryingSupercritical dryingSupercritical drying is a process to remove liquid in a precisely controlled way. It is useful in the production of microelectromechanical systems , the drying of spices, the production of aerogel, and in the preparation of biological specimens for scanning electron microscopy.As the substance in...
, Freeze dryingFreeze dryingFreeze-drying is a dehydration process typically used to preserve a perishable material or make the material more convenient for transport...
- removal of excess liquid - ScrubberScrubberScrubber systems are a diverse group of air pollution control devices that can be used to remove some particulates and/or gases from industrial exhaust streams. Traditionally, the term "scrubber" has referred to pollution control devices that use liquid to wash unwanted pollutants from a gas stream...
- removing of pollution from exhaust gases
Chemical processes
- SmeltingSmeltingSmelting is a form of extractive metallurgy; its main use is to produce a metal from its ore. This includes iron extraction from iron ore, and copper extraction and other base metals from their ores...
- chemically enhancing metals - DisinfectionDisinfectionDisinfectants are substances that are applied to non-living objects to destroy microorganisms that are living on the objects. Disinfection does not necessarily kill all microorganisms, especially nonresistant bacterial spores; it is less effective than sterilisation, which is an extreme physical...
- chemical treatment to kill bacteria and viruses - PyroprocessingPyroprocessingPyroprocessing is a process in which materials are subjected to high temperatures in order to bring about a chemical or physical change. Pyroprocessing includes such terms as ore-roasting, calcination and sintering...
- using heat to chemically combine materials, such as in cementCement kilnCement kilns are used for the pyroprocessing stage of manufacture of Portland and other types of hydraulic cement, in which calcium carbonate reacts with silica-bearing minerals to form a mixture of calcium silicates...
.
Heat processes
- Flash smeltingFlash smeltingFlash smelting is a smelting process for sulfur-containing ores including chalcopyrite. The process was developed by Outokumpu in Finland and first applied at the Harjavalta plant in 1949 for smelting copper ore. It has also been adapted for nickel and lead production.The process uses the...
- a refinement on smelting, for sulfur-containing ores (produces copper, nickel and lead)
Electrolysis
The availability of electricity and its effect on materials gave rise to several processes for plating or separating metals.- GildingGildingThe term gilding covers a number of decorative techniques for applying fine gold leaf or powder to solid surfaces such as wood, stone, or metal to give a thin coating of gold. A gilded object is described as "gilt"...
, ElectroplatingElectroplatingElectroplating is a plating process in which metal ions in a solution are moved by an electric field to coat an electrode. The process uses electrical current to reduce cations of a desired material from a solution and coat a conductive object with a thin layer of the material, such as a metal...
, Anodization, ElectrowinningElectrowinningElectrowinning, also called electroextraction, is the electrodeposition of metals from their ores that have been put in solution or liquefied. Electrorefining uses a similar process to remove impurities from a metal. Both processes use electroplating on a large scale and are important techniques...
- depositing a material on an electrode - ElectropolishingElectropolishingElectropolishing, also known as electrochemical polishing or electrolytic polishing , is an electrochemical process that removes material from a metallic workpiece. It is used to polish, passivate, and deburr metal parts. It is often described as the reverse of electroplating...
- the reverse of electroplating - Electrofocusing - similar to electroplating, but separating molecules
- Electrolytic processElectrolytic processAn electrolytic process is the use of electrolysis industrially to refine metals or compounds at a high purity and low cost. Some examples are the Hall-Héroult process used for aluminium, or the production of hydrogen from water. Electrolysis is usually done in bulk using hundreds of sheets of...
- the generic process of using electrolysis - Electrophoretic depositionElectrophoretic depositionElectrophoretic deposition , is a term for a broad range of industrial processes which includes electrocoating, e-coating, cathodic electrodeposition, and electrophoretic coating, or electrophoretic painting...
- electrolytic deposition of colloidal particles in a liquid medium - ElectrotypingElectrotypingElectrotyping is a chemical method for forming metal parts that exactly reproduce a model. The method was invented by Moritz von Jacobi in Russia in 1838, and was immediately adopted for applications in printing and several other fields...
- using electroplating to produce printing plates - MetallizingMetallizingMetallizing is the general name for the technique of coating metal on the surface of non-metallic objects.Techniques for metallization started as early as mirror making. In 1835, Justus von Liebig discovered the process of coating a glass surface with metallic silver, making the glass mirror one of...
, PlatingPlatingPlating is a surface covering in which a metal is deposited on a conductive surface. Plating has been done for hundreds of years, but it is also critical for modern technology...
, Spin coatingSpin coatingSpin coating is a procedure used to apply uniform thin films to flat substrates. In short, an excess amount of a solution is placed on the substrate, which is then rotated at high speed in order to spread the fluid by centrifugal force...
- the generic term for giving non-metals a metallic coating
Physical processes
There are several physical processesPhysical change
Physical changes are changes affecting the form of a chemical substance, but do not change the chemical composition of that substance. Physical changes are used to separate mixtures into their component compounds, but can not usually be used to separate compounds into chemical elements or simpler...
for reshaping a material by cutting, folding, joining or polishing, developed on a large scale from workshop techniques.
- ForgingForgingForging is a manufacturing process involving the shaping of metal using localized compressive forces. Forging is often classified according to the temperature at which it is performed: '"cold," "warm," or "hot" forging. Forged parts can range in weight from less than a kilogram to 580 metric tons...
- the shaping of metal by use of heat and hammer - CastingCastingIn metalworking, casting involves pouring liquid metal into a mold, which contains a hollow cavity of the desired shape, and then allowing it to cool and solidify. The solidified part is also known as a casting, which is ejected or broken out of the mold to complete the process...
- shaping of a liquid material by pouring it into moulds and letting it solidify - MachiningMachiningConventional machining is a form of subtractive manufacturing, in which a collection of material-working processes utilizing power-driven machine tools, such as saws, lathes, milling machines, and drill presses, are used with a sharp cutting tool to physical remove material to achieve a desired...
- the mechanical cutting and shaping of metal - Progressive stampingProgressive stampingProgressive stamping is a metalworking method that can encompass punching, coining, bending and several other ways of modifying metal raw material, combined with an automatic feeding system....
- the production of components from a strip or roll - HydroformingHydroformingHydroforming is a cost-effective way of shaping malleable metals such as aluminum or brass into lightweight, structurally stiff and strong pieces. One of the largest applications of hydroforming is the automotive industry, which makes use of the complex shapes possible by hydroforming to produce...
- a tube of metal is expanded into a mould under pressure - Sandblasting - cleaning of a surface using sand or other particles
- SolderingSolderingSoldering is a process in which two or more metal items are joined together by melting and flowing a filler metal into the joint, the filler metal having a lower melting point than the workpiece...
, BrazingBrazingBrazing is a metal-joining process whereby a filler metal is heated above and distributed between two or more close-fitting parts by capillary action. The filler metal is brought slightly above its melting temperature while protected by a suitable atmosphere, usually a flux...
, WeldingWeldingWelding is a fabrication or sculptural process that joins materials, usually metals or thermoplastics, by causing coalescence. This is often done by melting the workpieces and adding a filler material to form a pool of molten material that cools to become a strong joint, with pressure sometimes...
- a process for joining metals - Tumble polishingTumble polishingTumble finishing, also known as tumbling or rumbling, is a technique for smoothing and polishing a rough surface on relatively small parts...
- for polishing - Precipitation hardening - heat treatment used to strengthen malleable materials
- Work hardeningWork hardeningWork hardening, also known as strain hardening or cold working, is the strengthening of a metal by plastic deformation. This strengthening occurs because of dislocation movements within the crystal structure of the material. Any material with a reasonably high melting point such as metals and...
- adding strength to metals, alloys, etc. - Case hardeningCase hardeningCase hardening or surface hardening is the process of hardening the surface of a metal, often a low carbon steel, by infusing elements into the material's surface, forming a thin layer of a harder alloy...
, Differential hardeningDifferential hardeningDifferential hardening is a method used in forging swords and knives to increase the hardness of the edge without making the whole blade brittle. To achieve this, the edge is cooled more rapidly than the spine by adding a heat insulator to the spine before quenching. Clay or another material is...
, Shot peeningShot peeningShot peening is a cold working process used to produce a compressive residual stress layer and modify mechanical properties of metals. It entails impacting a surface with shot with force sufficient to create plastic deformation...
- creating a wear resistant surface - Die cuttingDie (manufacturing)A die is a specialized tool used in manufacturing industries to cut or shape material using a press. Like molds, dies are generally customized to the item they are used to create...
- A "forme" or "die" is pressed onto a flat material to cut, score, punch and otherwise shape the material. - machining-the process of giving desired shape which involves the loss of material.
Example-planing,shaping,milling,punching,drilling,grinding
Moulding
The physical shaping of materials by forming their liquid form using a mould.- CastingCastingIn metalworking, casting involves pouring liquid metal into a mold, which contains a hollow cavity of the desired shape, and then allowing it to cool and solidify. The solidified part is also known as a casting, which is ejected or broken out of the mold to complete the process...
, Sand castingSand castingSand casting, also known as sand molded casting, is a metal casting process characterized by using sand as the mold material.It is relatively cheap and sufficiently refractory even for steel foundry use. A suitable bonding agent is mixed or occurs with the sand...
- the shaping of molten metal or plastics using a mould - SinteringSinteringSintering is a method used to create objects from powders. It is based on atomic diffusion. Diffusion occurs in any material above absolute zero, but it occurs much faster at higher temperatures. In most sintering processes, the powdered material is held in a mold and then heated to a temperature...
, Powder metallurgyPowder metallurgyPowder metallurgy is the process of blending fine powdered materials, pressing them into a desired shape , and then heating the compressed material in a controlled atmosphere to bond the material . The powder metallurgy process generally consists of four basic steps: powder manufacture, powder...
- the making of objects from metal or ceramic powder - Blow moulding as in plastic containers or in the Glass Container Industry - making hollow objects by blowing them into a mould.
- Compression moldingCompression moldingCompression molding is a method of molding in which the molding material, generally preheated, is first placed in an open, heated mold cavity. The mold is closed with a top force or plug member, pressure is applied to force the material into contact with all mold areas, while heat and pressure are...
Separation
Many materials exist in an impure form, purification, or separation provides a usable product.- ComminutionComminutionComminution is the process in which solid materials are reduced in size, by crushing, grinding and other processes. It occurs naturally during faulting in the upper part of the crust and is an important operation in mineral processing, ceramics, electronics and other fields. Within industrial uses,...
- reduces the size of physical particles (it exists between crushing and grinding) - Froth flotationFroth flotationFroth flotation is a process for selectively separating hydrophobic materials from hydrophilic. This is used in several processing industries...
, flotation processFlotation processFlotation process is a method of separation widely used in the wastewater treatment and mineral processing industries.Various flotation processes include the following:* Dissolved air flotation...
- separating minerals through floatation - Solvent extraction - dissolving one substance in another
- Frasch processFrasch processThe Frasch process is a method to extract sulfur from underground deposits. It is the only economic method of recovering sulfur from elemental deposits...
- for extracting molten sulfur from the ground
DistillationDistillationDistillation is a method of separating mixtures based on differences in volatilities of components in a boiling liquid mixture. Distillation is a unit operation, or a physical separation process, and not a chemical reaction....
- Fractional distillationFractional distillationFractional distillation is the separation of a mixture into its component parts, or fractions, such as in separating chemical compounds by their boiling point by heating them to a temperature at which several fractions of the compound will evaporate. It is a special type of distillation...
, Steam distillationSteam distillationSteam distillation is a special type of distillation for temperature sensitive materials like natural aromatic compounds....
, Vacuum distillationVacuum distillationVacuum distillation is a method of distillation whereby the pressure above the liquid mixture to be distilled is reduced to less than its vapor pressure causing evaporation of the most volatile liquid...
- separating materials by their boiling point - Batch distillationBatch distillationBatch distillation refers to the use of distillation in batches, meaning that a mixture is distilled to separate it into its component fractions before the distillation still is again charged with more mixture and the process is repeated...
- Continuous distillationContinuous distillationContinuous distillation, a form of distillation, is an ongoing separation in which a mixture is continuously fed into the process and separated fractions are removed continuously as output streams. A distillation is the separation or partial separation of a liquid feed mixture into components or...
- Fractionating columnFractionating columnA fractionating column or fractionation column is an essential item used in the distillation of liquid mixtures so as to separate the mixture into its component parts, or fractions, based on the differences in their volatilities...
- Spinning coneSpinning coneSpinning cone columns are used in a form of steam distillation to gently extract volatile chemicals from liquid foodstuffs while minimising the effect on the taste of the product...
Iron and steel
Early production of ironIron
Iron is a chemical element with the symbol Fe and atomic number 26. It is a metal in the first transition series. It is the most common element forming the planet Earth as a whole, forming much of Earth's outer and inner core. It is the fourth most common element in the Earth's crust...
was from meteorites, or as a by-product of copper
Copper
Copper is a chemical element with the symbol Cu and atomic number 29. It is a ductile metal with very high thermal and electrical conductivity. Pure copper is soft and malleable; an exposed surface has a reddish-orange tarnish...
refining. Heating iron ore and carbon in a crucible at 1000 K produces wrought iron
Wrought iron
thumb|The [[Eiffel tower]] is constructed from [[puddle iron]], a form of wrought ironWrought iron is an iron alloy with a very low carbon...
. This process gained popularity during the Iron Age
Iron Age
The Iron Age is the archaeological period generally occurring after the Bronze Age, marked by the prevalent use of iron. The early period of the age is characterized by the widespread use of iron or steel. The adoption of such material coincided with other changes in society, including differing...
. Temperatures of 1300 K were produced around the 8th century by blowing air through the heated mixture in a bloomery
Bloomery
A bloomery is a type of furnace once widely used for smelting iron from its oxides. The bloomery was the earliest form of smelter capable of smelting iron. A bloomery's product is a porous mass of iron and slag called a bloom. This mix of slag and iron in the bloom is termed sponge iron, which...
or blast furnace
Blast furnace
A blast furnace is a type of metallurgical furnace used for smelting to produce industrial metals, generally iron.In a blast furnace, fuel and ore and flux are continuously supplied through the top of the furnace, while air is blown into the bottom of the chamber, so that the chemical reactions...
(12th century); producing a strong but brittle cast iron
Cast iron
Cast iron is derived from pig iron, and while it usually refers to gray iron, it also identifies a large group of ferrous alloys which solidify with a eutectic. The color of a fractured surface can be used to identify an alloy. White cast iron is named after its white surface when fractured, due...
. Furnaces were growing bigger, producing greater quantities; a factor contributing to the Industrial Revolution
Industrial Revolution
The Industrial Revolution was a period from the 18th to the 19th century where major changes in agriculture, manufacturing, mining, transportation, and technology had a profound effect on the social, economic and cultural conditions of the times...
. In 1740 the temperature and carbon content could be controlled sufficiently to consistently produce steel
Steel
Steel is an alloy that consists mostly of iron and has a carbon content between 0.2% and 2.1% by weight, depending on the grade. Carbon is the most common alloying material for iron, but various other alloying elements are used, such as manganese, chromium, vanadium, and tungsten...
; very strong and very workable. The 19th century saw the development of electric arc furnace
Electric arc furnace
An electric arc furnace is a furnace that heats charged material by means of an electric arc.Arc furnaces range in size from small units of approximately one ton capacity up to about 400 ton units used for secondary steelmaking...
s that produced steel in very large quantities, and are more easily controlled.
- SmeltingSmeltingSmelting is a form of extractive metallurgy; its main use is to produce a metal from its ore. This includes iron extraction from iron ore, and copper extraction and other base metals from their ores...
- the generic process used in furnaces to produce steel, copper, etc. - Catalan forge, Open hearth furnaceOpen hearth furnaceOpen hearth furnaces are one of a number of kinds of furnace where excess carbon and other impurities are burnt out of the pig iron to produce steel. Since steel is difficult to manufacture due to its high melting point, normal fuels and furnaces were insufficient and the open hearth furnace was...
, BloomeryBloomeryA bloomery is a type of furnace once widely used for smelting iron from its oxides. The bloomery was the earliest form of smelter capable of smelting iron. A bloomery's product is a porous mass of iron and slag called a bloom. This mix of slag and iron in the bloom is termed sponge iron, which...
, Siemens regenerative furnace - produced wrought iron - Blast furnaceBlast furnaceA blast furnace is a type of metallurgical furnace used for smelting to produce industrial metals, generally iron.In a blast furnace, fuel and ore and flux are continuously supplied through the top of the furnace, while air is blown into the bottom of the chamber, so that the chemical reactions...
- produced cast iron - Direct Reduction - produced direct reduced ironDirect reduced ironDirect-reduced iron , also called sponge iron, is produced from direct reduction of iron ore by a reducing gas produced from natural gas or coal. The reducing gas is a mixture majority of hydrogen and carbon monoxide which acts as reducing agent...
- Crucible steelCrucible steelCrucible steel describes a number of different techniques for making steel in a crucible. Its manufacture is essentially a refining process which is dependent on preexisting furnace products...
- Cementation processCementation processThe cementation process is an obsolete technique for making steel by carburization of iron. Unlike modern steelmaking, it increased the amount of carbon in the iron. It was apparently developed before the 17th century. Derwentcote Steel Furnace, built in 1720, is the earliest surviving example...
- Bessemer processBessemer processThe Bessemer process was the first inexpensive industrial process for the mass-production of steel from molten pig iron. The process is named after its inventor, Henry Bessemer, who took out a patent on the process in 1855. The process was independently discovered in 1851 by William Kelly...
- Basic oxygen steelmakingBasic oxygen steelmakingBasic oxygen steelmaking , also known as Linz-Donawitz-Verfahren steelmaking or the oxygen converter process is a method of primary steelmaking in which carbon-rich molten pig iron is made into steel. Blowing oxygen through molten pig iron lowers the carbon content of the alloy and changes it into...
, Linz-Donawitz process - Electric arc furnaceElectric arc furnaceAn electric arc furnace is a furnace that heats charged material by means of an electric arc.Arc furnaces range in size from small units of approximately one ton capacity up to about 400 ton units used for secondary steelmaking...
Petroleum and organic compounds
The nature of an organic molecule means it can be transformed at the molecular level to create a range of products.- Cracking (chemistry)Cracking (chemistry)In petroleum geology and chemistry, cracking is the process whereby complex organic molecules such as kerogens or heavy hydrocarbons are broken down into simpler molecules such as light hydrocarbons, by the breaking of carbon-carbon bonds in the precursors. The rate of cracking and the end products...
- the generic term for breaking up the larger molecules. - AlkylationAlkylationAlkylation is the transfer of an alkyl group from one molecule to another. The alkyl group may be transferred as an alkyl carbocation, a free radical, a carbanion or a carbene . Alkylating agents are widely used in chemistry because the alkyl group is probably the most common group encountered in...
- refining of crude oil - Burton processBurton processThe Burton process is a thermal cracking process invented by William Merriam Burton and Robert Humphrey.The oil industry used it to double the production of gasoline in 1913. This thermal cracking process was patented on January 7, 1913 ....
- cracking of hydrocarbons - Cumene processCumene processThe Cumene process is an industrial process for developing phenol and acetone from benzene and propylene. The term stems from cumene , the intermediate material during the process. It was invented by Heinrich Hock in 1944 and independently by R. Ūdris and P...
- making phenol and acetone from benzene - Friedel-Crafts reactionFriedel-Crafts reactionThe Friedel–Crafts reactions are a set of reactions developed by Charles Friedel and James Crafts in 1877. There are two main types of Friedel–Crafts reactions: alkylation reactions and acylation reactions. This reaction type is a form of electrophilic aromatic substitution...
, Kolbe-Schmitt reactionKolbe-Schmitt reactionThe Kolbe–Schmitt reaction/Kolbe process is a carboxylation chemical reaction that proceeds by heating sodium phenolate with carbon dioxide under pressure , then treating the product with sulfuric acid... - Olefin metathesisOlefin metathesisOlefin metathesis or transalkylidenation is an organic reaction that entails redistribution of alkylene fragments by the scission of carbon - carbon double bonds in olefins . Its advantages include the creation of fewer sideproducts and hazardous wastes. Yves Chauvin, Robert H. Grubbs, and Richard R...
, Thermal depolymerizationThermal depolymerizationThermal depolymerization is a depolymerization process using hydrous pyrolysis for the reduction of complex organic materials into light crude oil. It mimics the natural geological processes thought to be involved in the production of fossil fuels... - TransesterificationTransesterificationIn organic chemistry, transesterification is the process of exchanging the organic group R″ of an ester with the organic group R′ of an alcohol. These reactions are often catalyzed by the addition of an acid or base catalyst...
- organic chemicals - Raschig processRaschig processThe Raschig process is a chemical process for producing hydroxylamine...
, Ketazine processKetazine processThe Ketazine process is used commercially to produce hydrazine. It is a variation of the Raschig process, in which ammonia is oxidized by chlorine or chloramine in the presence of aliphatic ketones, usually acetone. The resulting ketazine is then hydrolysed to hydrazine....
, Peroxide processPeroxide processThe peroxide process produces hydrazine, it is a variant of the Raschig process in which hydrogen peroxide is used to oxidize ammonia in the presence of a ketone....
- part of the process to produce nylon - Oxo process - Produces aldehydes from alkenes.
Others
Organized by product:- AluminiumAluminiumAluminium or aluminum is a silvery white member of the boron group of chemical elements. It has the symbol Al, and its atomic number is 13. It is not soluble in water under normal circumstances....
- (Deville processDeville processThe Deville process was the first industrial process used to produce alumina from bauxite.The Frenchman Henri Sainte-Claire Deville invented the process in 1859. It is sometimes called the Deville-Pechiney process....
, Bayer processBayer processThe Bayer process is the principal industrial means of refining bauxite to produce alumina .Bauxite, the most important ore of aluminium, contains only 30–54% alumina, Al2O3, the rest being a mixture of silica, various iron oxides, and titanium dioxide. The alumina must be purified before it can...
, Hall-Héroult processHall-Héroult processThe Hall–Héroult process is the major industrial process for the production of aluminium. It involves dissolving alumina in molten cryolite, and electrolysing the molten salt bath to obtain pure aluminium metal.-Process:...
, Wöhler processWöhler processThe Wöhler process was the former way in which aluminium was extracted from its ore. However with the advent of more efficient means of electrolysis, this process all but become extinct...
) - AmmoniaAmmoniaAmmonia is a compound of nitrogen and hydrogen with the formula . It is a colourless gas with a characteristic pungent odour. Ammonia contributes significantly to the nutritional needs of terrestrial organisms by serving as a precursor to food and fertilizers. Ammonia, either directly or...
, used in fertilizer & explosives - (Haber processHaber processThe Haber process, also called the Haber–Bosch process, is the nitrogen fixation reaction of nitrogen gas and hydrogen gas, over an enriched iron or ruthenium catalyst, which is used to industrially produce ammonia....
) - BromineBromineBromine ") is a chemical element with the symbol Br, an atomic number of 35, and an atomic mass of 79.904. It is in the halogen element group. The element was isolated independently by two chemists, Carl Jacob Löwig and Antoine Jerome Balard, in 1825–1826...
- (Dow processDow processThe Dow process is the electrolytic method of bromine extraction from brine, and was Herbert Henry Dow's second revolutionary process for generating bromine commercially....
) - ChlorineChlorineChlorine is the chemical element with atomic number 17 and symbol Cl. It is the second lightest halogen, found in the periodic table in group 17. The element forms diatomic molecules under standard conditions, called dichlorine...
, used in chemicals - (Chloralkali processChloralkali processThe chloralkali process is an industrial process for the electrolysis of sodium chloride solution . Depending on the method several products beside hydrogen can be produced. If the products are separated, chlorine and sodium hydroxide are the products; by mixing, sodium hypochlorite or sodium...
, Weldon processWeldon processThe Weldon process is a process developed in 1866 by Walter Weldon for recovering manganese dioxide for re-use in chlorine manufacture. Commercial operations started at the Gamble works in St. Helens in 1869. The process is describe in considerable detailed in the book, The Alkali Industry, by J.R...
) - FatFatFats consist of a wide group of compounds that are generally soluble in organic solvents and generally insoluble in water. Chemically, fats are triglycerides, triesters of glycerol and any of several fatty acids. Fats may be either solid or liquid at room temperature, depending on their structure...
- (RenderingRendering (industrial)Rendering is a process that converts waste animal tissue into stable, value-added materials. Rendering can refer to any processing of animal byproducts into more useful materials, or more narrowly to the rendering of whole animal fatty tissue into purified fats like lard or tallow...
) - FertilizerFertilizerFertilizer is any organic or inorganic material of natural or synthetic origin that is added to a soil to supply one or more plant nutrients essential to the growth of plants. A recent assessment found that about 40 to 60% of crop yields are attributable to commercial fertilizer use...
- (Nitrophosphate processNitrophosphate processThe nitrophosphate process was a method for the industrial production of nitrogen fertilizers invented by Erling Johnson in the city of Odda, Norway around 1927....
) - GlassGlassGlass is an amorphous solid material. Glasses are typically brittle and optically transparent.The most familiar type of glass, used for centuries in windows and drinking vessels, is soda-lime glass, composed of about 75% silica plus Na2O, CaO, and several minor additives...
- (Pilkington processFloat glassFloat glass is a sheet of glass made by floating molten glass on a bed of molten metal, typically tin, although lead and various low melting point alloys were used in the past. This method gives the sheet uniform thickness and very flat surfaces. Modern windows are made from float glass...
) - GoldGoldGold is a chemical element with the symbol Au and an atomic number of 79. Gold is a dense, soft, shiny, malleable and ductile metal. Pure gold has a bright yellow color and luster traditionally considered attractive, which it maintains without oxidizing in air or water. Chemically, gold is a...
- (Bacterial oxidationBacterial oxidationBacterial oxidation is a biohydrometallurgical process developed for pre-cyanidation treatment of refractory gold ores or concentrates. The bacterial culture is a mixed culture of Thiobacillus ferrooxidans, Thiobacillus thiooxidans and Leptospirillum ferrooxidans...
, Parkes processParkes processThe Parkes process is a pyrometallurgical industrial process for removing silver from lead, during the production of bullion. It is an example of liquid-liquid extraction....
) - Heavy WaterHeavy waterHeavy water is water highly enriched in the hydrogen isotope deuterium; e.g., heavy water used in CANDU reactors is 99.75% enriched by hydrogen atom-fraction...
, used to refine radioactive products - (Girdler sulfide processGirdler sulfide processThe Girdler sulfide process, also known as the Geib–Spevack process, is an industrial production method for making heavy water , an important component of many nuclear reactors because it acts as a neutron moderator. It takes its name from Karl-Hermann Geib and Jerome S...
) - HydrogenHydrogenHydrogen is the chemical element with atomic number 1. It is represented by the symbol H. With an average atomic weight of , hydrogen is the lightest and most abundant chemical element, constituting roughly 75% of the Universe's chemical elemental mass. Stars in the main sequence are mainly...
- (Steam reformingSteam reformingFossil fuel reforming is a method of producing hydrogen or other useful products from fossil fuels such as natural gas. This is achieved in a processing device called a reformer which reacts steam at high temperature with the fossil fuel. The steam methane reformer is widely used in industry to...
, Water Gas Shift ReactionWater gas shift reactionThe water-gas shift reaction is a chemical reaction in which carbon monoxide reacts with water vapor to form carbon dioxide and hydrogen:The water-gas shift reaction is an important industrial reaction. It is often used in conjunction with steam reforming of methane or other hydrocarbons, which is...
) - LeadLeadLead is a main-group element in the carbon group with the symbol Pb and atomic number 82. Lead is a soft, malleable poor metal. It is also counted as one of the heavy metals. Metallic lead has a bluish-white color after being freshly cut, but it soon tarnishes to a dull grayish color when exposed...
(and BismuthBismuthBismuth is a chemical element with symbol Bi and atomic number 83. Bismuth, a trivalent poor metal, chemically resembles arsenic and antimony. Elemental bismuth may occur naturally uncombined, although its sulfide and oxide form important commercial ores. The free element is 86% as dense as lead...
) - (Betts electrolytic processBetts electrolytic processThe Betts electrolytic process is an industrial process for separating lead and bismuth. It is named for its inventor Anson Gardner Betts.-Process description for lead:...
, Betterton-Kroll processBetterton-Kroll processThe Betterton-Kroll process is an industrial process for removing bismuth from lead.Calcium and magnesium are added to a molten lead-bismuth bath. The resulting bismuth compounds have higher melting points and lower densities than the lead, and can be removed as dross. The compounds are treated...
) - NickelNickelNickel is a chemical element with the chemical symbol Ni and atomic number 28. It is a silvery-white lustrous metal with a slight golden tinge. Nickel belongs to the transition metals and is hard and ductile...
- (Mond processMond processThe Mond process, sometimes known as the carbonyl process is a technique created by Ludwig Mond in 1890 to extract and purify nickel. The process was used commercially before the end of the 19th century...
) - Nitric acidNitric acidNitric acid , also known as aqua fortis and spirit of nitre, is a highly corrosive and toxic strong acid.Colorless when pure, older samples tend to acquire a yellow cast due to the accumulation of oxides of nitrogen. If the solution contains more than 86% nitric acid, it is referred to as fuming...
- (Ostwald processOstwald processThe Ostwald process is a chemical process for producing nitric acid, which was developed by Wilhelm Ostwald . It is a mainstay of the modern chemical industry. Historically and practically it is closely associated with the Haber process, which provides the requisite raw material,...
) - PaperPaperPaper is a thin material mainly used for writing upon, printing upon, drawing or for packaging. It is produced by pressing together moist fibers, typically cellulose pulp derived from wood, rags or grasses, and drying them into flexible sheets....
- (Pulping, Kraft processKraft processThe kraft process describes a technology for conversion of wood into wood pulp consisting of almost pure cellulose fibers...
, Fourdrinier machineFourdrinier machineThis article contains a glossary section at the end.Most modern papermaking machines are based on the principles of the Fourdrinier Machine. It has been used in some variation since its inception...
) - RubberRubberNatural rubber, also called India rubber or caoutchouc, is an elastomer that was originally derived from latex, a milky colloid produced by some plants. The plants would be ‘tapped’, that is, an incision made into the bark of the tree and the sticky, milk colored latex sap collected and refined...
- (VulcanizationVulcanizationVulcanization or vulcanisation is a chemical process for converting rubber or related polymers into more durable materials via the addition of sulfur or other equivalent "curatives." These additives modify the polymer by forming crosslinks between individual polymer chains. Vulcanized material is...
) - SaltSaltIn chemistry, salts are ionic compounds that result from the neutralization reaction of an acid and a base. They are composed of cations and anions so that the product is electrically neutral...
- (Alberger processAlberger processThe Alberger process is a method of producing salt.It involves mechanical evaporation, and uses an open evaporating pan and steam energy. It results in a unique, three-dimensional flake salt of extremely light bulk density. It is highly prized in the fast food industry, due to its low sodium and...
, Grainer evaporation processGrainer evaporation processThe Grainer evaporation process is a method of producing salt.This method uses shallow open pans with steam-heated immersion coils to evaporate the brine into salt.Sometimes it is paired with a partial-vacuum, to speed evaporation.Compare Alberger process...
) - SemiconductorSemiconductorA semiconductor is a material with electrical conductivity due to electron flow intermediate in magnitude between that of a conductor and an insulator. This means a conductivity roughly in the range of 103 to 10−8 siemens per centimeter...
crystals - (Bridgeman techniqueBridgeman techniqueThe Bridgman–Stockbarger technique is named after Harvard physicist Percy Williams Bridgman and MIT physicist Donald C. Stockbarger...
, Czochralski processCzochralski processThe Czochralski process is a method of crystal growth used to obtain single crystals of semiconductors , metals , salts, and synthetic gemstones...
) - SilverSilverSilver is a metallic chemical element with the chemical symbol Ag and atomic number 47. A soft, white, lustrous transition metal, it has the highest electrical conductivity of any element and the highest thermal conductivity of any metal...
- (Patio processPatio processThe patio process was a process used to extract silver from ore. The process was invented by Bartolomé de Medina in Pachuca, New Spain , in 1554. The patio process was the first process to use mercury amalgamation to recover silver from ore. It replaced smelting as the primary method of extracting...
, Parkes processParkes processThe Parkes process is a pyrometallurgical industrial process for removing silver from lead, during the production of bullion. It is an example of liquid-liquid extraction....
) - Sodium carbonateSodium carbonateSodium carbonate , Na2CO3 is a sodium salt of carbonic acid. It most commonly occurs as a crystalline heptahydrate, which readily effloresces to form a white powder, the monohydrate. Sodium carbonate is domestically well-known for its everyday use as a water softener. It can be extracted from the...
, used for soap - (Leblanc processLeblanc processThe Leblanc process was the industrial process for the production of soda ash used throughout the 19th century, named after its inventor, Nicolas Leblanc. It involved two stages: Production of sodium sulfate from sodium chloride, followed by reaction of the sodium sulfate with coal and calcium...
, Solvay processSolvay processThe Solvay process, also referred to as the ammonia-soda process, is the major industrial process for the production of soda ash . The ammonia-soda process was developed into its modern form by Ernest Solvay during the 1860s...
, Leblanc-Deacon process) - Sulfuric acidSulfuric acidSulfuric acid is a strong mineral acid with the molecular formula . Its historical name is oil of vitriol. Pure sulfuric acid is a highly corrosive, colorless, viscous liquid. The salts of sulfuric acid are called sulfates...
- (Lead chamber processLead chamber processThe lead chamber process was an industrial method used to produce sulfuric acid in large quantities. It has been largely supplanted by the contact process....
, Contact processContact processThe contact process is the current method of producing sulphuric acid in the high concentrations needed for industrial processes. Platinum was formerly employed as a catalyst for the reaction, but as it is susceptible to poisoning by arsenic impurities in the sulfur feedstock, vanadium oxide is...
) - TitaniumTitaniumTitanium is a chemical element with the symbol Ti and atomic number 22. It has a low density and is a strong, lustrous, corrosion-resistant transition metal with a silver color....
- (Hunter processHunter processThe Hunter process was the first industrial process to produce pure ductile metallic titanium. It was invented in 1910 by Matthew A. Hunter, a chemist born in New Zealand, who worked in America....
, Kroll processKroll processKroll Process is a pyrometallurgical industrial process used to produce metallic titanium. It was invented by William J. Kroll in Luxembourg. After moving to the United States, Kroll further developed the method for the production of zirconium...
) - ZirconiumZirconiumZirconium is a chemical element with the symbol Zr and atomic number 40. The name of zirconium is taken from the mineral zircon. Its atomic mass is 91.224. It is a lustrous, grey-white, strong transition metal that resembles titanium...
- (Hunter processHunter processThe Hunter process was the first industrial process to produce pure ductile metallic titanium. It was invented in 1910 by Matthew A. Hunter, a chemist born in New Zealand, who worked in America....
, Kroll processKroll processKroll Process is a pyrometallurgical industrial process used to produce metallic titanium. It was invented by William J. Kroll in Luxembourg. After moving to the United States, Kroll further developed the method for the production of zirconium...
, Crystal bar processCrystal bar processThe crystal bar process was developed by Anton Eduard van Arkel and Jan Hendrik de Boer in 1925. This process was the first industrial process for the commercial production of pure ductile metallic zirconium. It is used in the production of small quantities of ultra-pure titanium and zirconium...
, Iodide process)
A list by process:
- Alberger processAlberger processThe Alberger process is a method of producing salt.It involves mechanical evaporation, and uses an open evaporating pan and steam energy. It results in a unique, three-dimensional flake salt of extremely light bulk density. It is highly prized in the fast food industry, due to its low sodium and...
, Grainer evaporation processGrainer evaporation processThe Grainer evaporation process is a method of producing salt.This method uses shallow open pans with steam-heated immersion coils to evaporate the brine into salt.Sometimes it is paired with a partial-vacuum, to speed evaporation.Compare Alberger process...
- produces salt from brine - Bacterial oxidationBacterial oxidationBacterial oxidation is a biohydrometallurgical process developed for pre-cyanidation treatment of refractory gold ores or concentrates. The bacterial culture is a mixed culture of Thiobacillus ferrooxidans, Thiobacillus thiooxidans and Leptospirillum ferrooxidans...
- used to produce gold - Bayer processBayer processThe Bayer process is the principal industrial means of refining bauxite to produce alumina .Bauxite, the most important ore of aluminium, contains only 30–54% alumina, Al2O3, the rest being a mixture of silica, various iron oxides, and titanium dioxide. The alumina must be purified before it can...
- the extraction of aluminium from ore - Chloralkali processChloralkali processThe chloralkali process is an industrial process for the electrolysis of sodium chloride solution . Depending on the method several products beside hydrogen can be produced. If the products are separated, chlorine and sodium hydroxide are the products; by mixing, sodium hypochlorite or sodium...
, Weldon processWeldon processThe Weldon process is a process developed in 1866 by Walter Weldon for recovering manganese dioxide for re-use in chlorine manufacture. Commercial operations started at the Gamble works in St. Helens in 1869. The process is describe in considerable detailed in the book, The Alkali Industry, by J.R...
- for producing chlorine and sodium hydroxide - Crystal bar processCrystal bar processThe crystal bar process was developed by Anton Eduard van Arkel and Jan Hendrik de Boer in 1925. This process was the first industrial process for the commercial production of pure ductile metallic zirconium. It is used in the production of small quantities of ultra-pure titanium and zirconium...
, Iodide process - produces zirconium - Dow processDow processThe Dow process is the electrolytic method of bromine extraction from brine, and was Herbert Henry Dow's second revolutionary process for generating bromine commercially....
- produces bromine from brine - FFC Cambridge ProcessFFC Cambridge ProcessThe FFC Cambridge Process is an electrochemical method in which solid metal compounds, particularly oxides, are cathodically reduced to the respective metals or alloys in molten salts. It is thought that this process will eventually be capable of producing metals or alloys more efficiently than...
- Girdler sulfide processGirdler sulfide processThe Girdler sulfide process, also known as the Geib–Spevack process, is an industrial production method for making heavy water , an important component of many nuclear reactors because it acts as a neutron moderator. It takes its name from Karl-Hermann Geib and Jerome S...
- for making heavy water - Hunter processHunter processThe Hunter process was the first industrial process to produce pure ductile metallic titanium. It was invented in 1910 by Matthew A. Hunter, a chemist born in New Zealand, who worked in America....
, Kroll processKroll processKroll Process is a pyrometallurgical industrial process used to produce metallic titanium. It was invented by William J. Kroll in Luxembourg. After moving to the United States, Kroll further developed the method for the production of zirconium...
- produces titanium and zirconium - Industrial rendering - the separation of fat from bone and protein
- Lead chamber processLead chamber processThe lead chamber process was an industrial method used to produce sulfuric acid in large quantities. It has been largely supplanted by the contact process....
, Contact processContact processThe contact process is the current method of producing sulphuric acid in the high concentrations needed for industrial processes. Platinum was formerly employed as a catalyst for the reaction, but as it is susceptible to poisoning by arsenic impurities in the sulfur feedstock, vanadium oxide is...
- production of sulfuric acid - Mond processMond processThe Mond process, sometimes known as the carbonyl process is a technique created by Ludwig Mond in 1890 to extract and purify nickel. The process was used commercially before the end of the 19th century...
- nickelNickelNickel is a chemical element with the chemical symbol Ni and atomic number 28. It is a silvery-white lustrous metal with a slight golden tinge. Nickel belongs to the transition metals and is hard and ductile... - Nitrophosphate processNitrophosphate processThe nitrophosphate process was a method for the industrial production of nitrogen fertilizers invented by Erling Johnson in the city of Odda, Norway around 1927....
- a number of similar process for producing fertilizer - Ostwald processOstwald processThe Ostwald process is a chemical process for producing nitric acid, which was developed by Wilhelm Ostwald . It is a mainstay of the modern chemical industry. Historically and practically it is closely associated with the Haber process, which provides the requisite raw material,...
- produces nitric acid - Pidgeon processPidgeon processThe Pidgeon process is one of the methods of magnesium metal production, via a silicothermic reduction. Practical production requires roughly 35-40 MWh/ton of metal produced, which is on par with the molten salt electrolytic methods of production, though above the 7 MWh/ton theoretical...
- produces magnesium, reducing the oxide using silicon - Steam reformingSteam reformingFossil fuel reforming is a method of producing hydrogen or other useful products from fossil fuels such as natural gas. This is achieved in a processing device called a reformer which reacts steam at high temperature with the fossil fuel. The steam methane reformer is widely used in industry to...
, Water Gas Shift ReactionWater gas shift reactionThe water-gas shift reaction is a chemical reaction in which carbon monoxide reacts with water vapor to form carbon dioxide and hydrogen:The water-gas shift reaction is an important industrial reaction. It is often used in conjunction with steam reforming of methane or other hydrocarbons, which is...
- produce hydrogen and carbon monoxide from methane or hydrogen and carbon dioxide from water and carbon monoxide - Vacuum metalising - a finishing process
- Perstorp Formox processFormox processThe Formox process produces formaldehyde. Formox is a worldwide registered trademark owned by Perstorp Specialty Chemicals AB, Sweden.Industrially, formaldehyde is produced by catalytic oxidation of methanol. The most commonly used catalysts are silver metal or a mixture of an iron oxide with...
- The oxidation of methanol to produce formaldehyde.