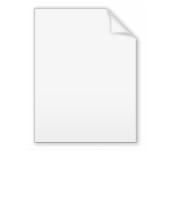
Hydroforming
Encyclopedia
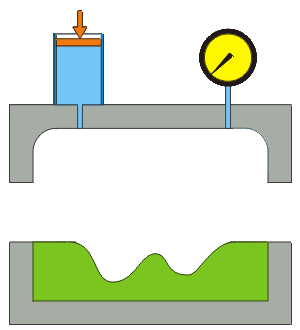
Metal
A metal , is an element, compound, or alloy that is a good conductor of both electricity and heat. Metals are usually malleable and shiny, that is they reflect most of incident light...
s such as aluminum or brass
Brass
Brass is an alloy of copper and zinc; the proportions of zinc and copper can be varied to create a range of brasses with varying properties.In comparison, bronze is principally an alloy of copper and tin...
into lightweight, structurally stiff and strong pieces. One of the largest applications of hydroforming is the automotive industry, which makes use of the complex shapes possible by hydroforming to produce stronger, lighter, and more rigid unibody structures for vehicles. This technique is particularly popular with the high-end sports car
Sports car
A sports car is a small, usually two seat, two door automobile designed for high speed driving and maneuverability....
industry and is also frequently employed in the shaping of aluminium tubes for bicycle frames.
Hydroforming is a specialized type of die
Die (manufacturing)
A die is a specialized tool used in manufacturing industries to cut or shape material using a press. Like molds, dies are generally customized to the item they are used to create...
forming that uses a high pressure hydraulic fluid
Fluid
In physics, a fluid is a substance that continually deforms under an applied shear stress. Fluids are a subset of the phases of matter and include liquids, gases, plasmas and, to some extent, plastic solids....
to press room temperature working material into a die. To hydroform aluminum into a vehicle's frame rail, a hollow tube of aluminum is placed inside a negative mold that has the shape of the desired end result. High pressure hydraulic pumps then inject fluid at very high pressure inside the aluminum which causes it to expand until it matches the mold. The hydroformed aluminum is then removed from the mold.
Hydroforming allows complex shapes with concavities to be formed, which would be difficult or impossible with standard solid die stamping. Hydroformed parts can often be made with a higher stiffness-to-weight ratio and at a lower per unit cost than traditional stamped or stamped and welded parts. Virtually all metals capable of cold forming can be hydroformed, including aluminum, brass, carbon and stainless steel, copper, and high strength alloys.
This process is based on the 1950s patent for hydramolding by Fred Leuthesser, Jr. and John Fox of the Schaible Company of Cincinnati, OH. It was originally used in producing kitchen spouts. This was done because in addition to the strengthening of the metal, hydramolding also produced less "grainy" parts, allowing for easier metal finishing.
Sheet hydroforming
In sheet hydroforming there are bladder forming (where there is a bladder that contains the liquid; no liquid contacts the sheet) and hydroforming where the fluid contacts the sheet (no bladder). A work piece is placed on a draw ring (blank holder) over a male punch then a hydraulic chamber surrounds the work piece and a relatively low initial pressure seats the work piece against the punch. The punch then is raised into the hydraulic chamber and pressure is increased to as high as 15000 psi which forms the part around the punch. Then the pressure is released and punch retracted, hydraulic chamber lifted, and the process is complete.Tube hydroforming
In tube hydroforming (THF) there are two major practices: high pressure and low pressure.With the high pressure process the tube is fully enclosed in a die prior to pressurization of the tube. In low pressure the tube is slightly pressurized to a fixed volume during the closing of the die (this used to be called the Variform process).
In tube hydroforming pressure is applied to the inside of a tube that is held by dies with the desired cross sections and forms. When the dies are closed, the tube ends are sealed by axial punches and the tube is filled with hydraulic fluid. The internal pressure can go up to a few thousands of bars and it causes the tube to calibrate against the dies. The fluid is injected into the tube through one of the two axial punches. Axial punches are movable and their action is required to provide axial compression and to feed material towards the center of the bulging tube. Transverse counterpunches may also be incorporated in the forming die in order to form protrusions with small diameter/length ratio. Transverse counterpunches may also be used to punch holes in the work piece at the end of the forming process. Many industrial applications of the process can be found, especially in the automotive sector.
Explosive hydroforming
For large parts, explosive hydroforming can generate the forming pressure by simply exploding a charge above the part (complete with evacuated mold) which is immersed in a pool of water. The tooling can be much cheaper than what would be required for any press-type process. The hydroforming-into-a-mold process also works using only a shock wave in air as the pressuring medium. Particularly when the explosives are close to the workpiece, inertiaInertia
Inertia is the resistance of any physical object to a change in its state of motion or rest, or the tendency of an object to resist any change in its motion. It is proportional to an object's mass. The principle of inertia is one of the fundamental principles of classical physics which are used to...
effects make the result more complicated than forming by hydrostatic pressure alone.
Typical tools
One advantage of hydroforming is the savings on tools. For sheet metal only a draw ring and punch (metalworking) or male die is required. The bladder of the hydroform itself acts as the male die eliminating the need to fabricate a matching male die. This allows for changes in material thickness to be made with usually no necessary changes to the tool. However, dies must be highly polished and in tube hydroforming a two-piece die is required to allow opening and closing.Geometry produced
Another advantage of hydroforming is that complex shapes can be made in one step. In sheet hydroforming (SHF) with the bladder acting as the male die almost limitless geometries can be produced. However, the process is limited by the very high closing force required in order to seal the dies, especially for large panels and thick hard materials. Small concave corner radii are difficult to be completely calibrated, i.e. filled, because too large a pressure would be required. Limits of the SHF process are due to risks of excessive thinning, fracture, wrinkling and are strictly related to the material formability and to a proper selection of process parameters (e.g. hydraulic pressure vs. time curve). Tube hydroforming (THF) can produce many geometric options as well, reducing the need for tube welding operations. Similar limitations and risks can be listed as in SHF; however, the maximum closing force is seldom a limiting factor in THF.Tolerances and surface finish
Hydroforming is capable of producing parts within tight tolerances including aircraft tolerances where a common tolerance for sheet metal parts is within 0.76mm (thirty thousandths of an inch). Sheet metal hydroforming also allows for a smoother finish as draw marks produced by the traditional method of pressing a male and female die together are eliminated.Effect on work material
When a blank is hydroformed the metal flows around the die rather than stretching, which produces less material thinning, and also reduces the rate of work hardening which helps eliminate the need for an annealing process on some parts that might otherwise require further forming operations.Examples
Notable examples include:- Satellite antennas up to 6 metres in diameter, such as those used in the Allen Telescope ArrayAllen Telescope ArrayThe Allen Telescope Array , formerly known as the One Hectare Telescope , was a joint effort by the SETI Institute and the Radio Astronomy Laboratory at the University of California, Berkeley to construct a radio interferometer that is dedicated to astronomical observations and a simultaneous...
. - The brass tube of YamahaYamahaYamaha may refer to:* Yamaha Corporation, a Japanese company with a wide range of products and services** Yamaha Motor Company, a Japanese motorized vehicle-producing company...
saxophoneSaxophoneThe saxophone is a conical-bore transposing musical instrument that is a member of the woodwind family. Saxophones are usually made of brass and played with a single-reed mouthpiece similar to that of the clarinet. The saxophone was invented by the Belgian instrument maker Adolphe Sax in 1846...
s. - The process has become popular for the manufacture of aluminium bicycle frames. The earliest commercially manufactured one being that of the Giant ManufacturingGiant ManufacturingGiant Manufacturing Co. Ltd. is a Taiwanese bicycle manufacturer which bills itself as the world's largest bicycle manufacturer. Giant has manufacturing facilities in Taiwan, Netherlands, and Mainland China.-History:...
Revive bicycle first marketed in 2003. - Many motor vehicles have major components manufactured using this technology, for example:
- The technique is widely used in the manufacture of engine cradles. The first mass produced one was for the Ford Contour and Mystique in 1994. Others from a long list include the Pontiac AztekPontiac AztekThe Pontiac Aztek was a mid-size crossover, the first offered by General Motors, that was produced by Pontiac from the 2001 model year to the 2005 model year. The Aztek was heavily criticized on its exterior styling, with Time magazine in 2007 calling the Aztek one of the worst cars of all time,...
, the Honda AccordHonda AccordThe Honda Accord is a series of compact, mid-size and full-size automobiles manufactured by Honda since 1976, and sold in a majority of automotive markets throughout the world....
and the perimeter frame around the Harley Davidson V-Rod motorcycle's engine. - As well as engine cradles, the main automotive applications for hydroforming are suspension, radiator supports and instrument-panel support beams. The first mass produced automotive component was in 1990 with the instrument panel support beam for the Chrysler minivan.
- Various vehicle bodies and body components, the earliest mass produced one being the 1997 Chevrolet CorvetteChevrolet CorvetteThe Chevrolet Corvette is a sports car by the Chevrolet division of General Motors that has been produced in six generations. The first model, a convertible, was designed by Harley Earl and introduced at the GM Motorama in 1953 as a concept show car. Myron Scott is credited for naming the car after...
. A selection from many examples are the current versions of the three major United States pickup trucks -- the Ford F-150, Chevrolet SilveradoChevrolet SilveradoThe Chevrolet Silverado , is the latest line of full-size pickup trucks from General Motors.-History:...
, and RamRam TrucksRam Trucks is a United States-based brand of light to mid-weight pickup trucks established in 2009 as a division of Chrysler Group LLC.-Background:...
-- which all have hydroformed frame rails, 2006 Pontiac SolsticePontiac SolsticeThe Pontiac Solstice is a small sports car from the Pontiac division of General Motors. Introduced at the 2004 North American International Auto Show, the Solstice roadster began production in Wilmington, Delaware, starting in mid-2005 for the 2006 model year. The exterior styling of the...
and the steel frame inside the John DeereJohn DeereJohn Deere was an American blacksmith and manufacturer who founded Deere & Company, one of the largest and leading agricultural and construction equipment manufacturers in the world...
HPX Gator Utility Vehicle.
- The technique is widely used in the manufacture of engine cradles. The first mass produced one was for the Ford Contour and Mystique in 1994. Others from a long list include the Pontiac Aztek