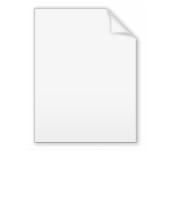
Thermal spraying
Encyclopedia
Thermal spraying techniques are coating
processes in which melted (or heated) materials are sprayed onto a surface. The "feedstock" (coating precursor) is heated by electrical (plasma or arc) or chemical means (combustion flame).
Thermal spraying can provide thick coatings (approx. thickness range is 20 micrometers to several mm, depending on the process and feedstock), over a large area at high deposition rate as compared to other coating processes such as electroplating
, physical
and chemical vapor deposition
. Coating materials available for thermal spraying include metals, alloys, ceramics, plastics and composites. They are fed in powder or wire form, heated to a molten or semimolten state and accelerated towards substrates in the form of micrometer-size particles. Combustion or electrical arc discharge is usually used as the source of energy for thermal spraying. Resulting coatings are made by the accumulation of numerous sprayed particles. The surface may not heat up significantly, allowing the coating of flammable substances.
Coating quality is usually assessed by measuring its porosity
, oxide content, macro and micro-hardness, bond strength
and surface roughness. Generally, the coating quality increases with increasing particle velocities.
Several variations of thermal spraying are distinguished:
In classical (developed between 1910 and 1920) but still widely used processes such as flame spraying and wire arc spraying, the particle velocities are generally low (< 150 m/s), and raw materials must be molten to be deposited. Plasma spraying, developed in the 1970s, uses
a high-temperature plasma jet generated by arc discharge
with typical temperatures >15000 K, which makes it
possible to spray refractory materials such as oxides, molybdenum
, etc.
Detonation Thermal Spraying Process
The Detonation gun basically consists of a long water cooled barrel with inlet valves for gases and powder. Oxygen and fuel (acetylene most common) is fed into the barrel along with a charge of powder. A spark is used to ignite the gas mixture and the resulting detonation heats and accelerates the powder to supersonic velocity down the barrel. A pulse of nitrogen is used to purge the barrel after each detonation. This process is repeated many times a second. The high kinetic energy of the hot powder particles on impact with the substrate result in a build up of a very dense and strong coating.
In plasma spraying process, the material to be deposited (feedstock) — typically as a powder
, sometimes as a liquid
, suspension
or wire — is introduced into the plasma jet, emanating from a plasma torch
. In the jet, where the temperature is on the order of 10,000 K, the material is melted and propelled towards a substrate. There, the molten droplets flatten, rapidly solidify and form a deposit. Commonly, the deposits remain adherent to the substrate as coatings; free-standing parts can also be produced by removing the substrate. There are a large number of technological parameters that influence the interaction of the particles with the plasma jet and the substrate and therefore the deposit properties. These parameters include feedstock type, plasma gas composition and flow rate, energy input, torch offset distance, substrate cooling, etc.
and modulus
, higher strain
tolerance, and lower thermal
and electrical conductivity. Also, due to the rapid solidification, metastable phases
can be present in the deposits.
), corrosion
, erosion
, wear
; they can also change the appearance, electrical or tribological properties of the surface, replace worn material, etc. When sprayed on substrates of various shapes and removed, free-standing parts in the form of plates, tubes, shells, etc. can be produced. It can also be used for powder processing (spheroidization, homogenization, modification of chemistry, etc.). In this case, the substrate for deposition is absent and the particles solidify during flight or in a controlled environment (e.g., water).
A polymer dispersion aerosol can be injected into the plasma discharge in order to create a grafting of this polymer on to a substrate surface. This application is mainly used to modify the surface chemistry of polymers.
Plasma jet generation:
Plasma-forming medium:
Spraying environment:
Another variation consists of having a liquid feedstock instead of a solid powder for melting, this technique is known as Solution precursor plasma spray
Vacuum plasma spraying (VPS) is a technology for etching and surface
modification to create porous layers with high reproducibility and for cleaning and surface engineering of plastics, rubbers and natural fibers as well as for replacing CFC
s for cleaning metal components. This surface engineering can improve properties such as frictional behavior, heat resistance, surface electrical conductivity, lubricity
, cohesive strength of films, or dielectric constant
, or it can make materials hydrophilic or hydrophobic.
The process typically operates at 39–120 °C to avoid thermal damage. It can induce non-thermally activated surface reactions, causing surface changes which cannot occur with molecular chemistries at atmospheric pressure. Plasma processing
is done in a controlled environment inside a sealed chamber at a medium vacuum, around 13–65 Pa
.
The gas
or mixture of gases is energized by an electrical field from DC
to microwave
frequencies, typically 1–500 W at 50 V. The treated components are usually electrically isolated. The volatile plasma by-products are evacuated from the chamber by the vacuum pump
, and if necessary can be neutralized in an exhaust scrubber
.
In contrast to molecular chemistry, plasmas employ:
Plasma also generates electromagnetic radiation
in the form of vacuum UV photons to penetrate bulk polymers to a depth of about 10 µm. This can cause chain scissions and cross-linking.
Plasmas affect materials at an atomic level. Techniques like X-ray photoelectron spectroscopy
and scanning electron microscopy
are used for surface analysis to identify the processes required and to judge their effects.
As a simple indication of surface energy
, and hence adhesion
or wettability, often a water droplet contact angle test
is used.
The lower the contact angle, the higher the surface energy and more hydrophilic the material is.
tends to occur more than chemical dissociations
. In a typical reactive gas, 1 in 100 molecules form free radicals whereas only 1 in 106 ionizes. The predominant effect here is the forming of free radicals.
Ionic effects can predominate with selection of process parameters and if necessary the use of noble gases.
and oxygen
is fed into a combustion chamber
, where they are ignited and combusted continuously. The resultant hot gas at a pressure close to 1 MPa emanates through a converging–diverging nozzle and travels through a straight section. The fuels can be gases (hydrogen
, methane
, propane
, propylene
, acetylene
, natural gas
, etc.) or liquids (kerosene
, etc.). The jet velocity at the exit of the barrel (>1000 m/s) exceeds the speed of sound
. A powder feed stock is injected into the gas stream, which accelerates the powder up to 800 m/s. The stream of hot gas and powder is directed towards the surface to be coated. The powder partially melts in the stream, and deposits upon the substrate. The resulting coating has low porosity
and high bond strength
.
HVOF coatings may be as thick as 12 mm (1/2"). It is typically used to deposit wear
and corrosion
resistant coatings on materials, such as ceramic and metallic layers. Common powders include WC
-Co, chromium carbide
, MCrAlY, and alumina. The process has been most successful for depositing cermet
materials (WC–Co, etc.) and other corrosion-resistant alloys (stainless steel
s, nickel-based alloys, aluminium, hydroxyapatite for medical implants, etc.).
) has been introduced. The method was originally developed in Russia with the accidental observation of the rapid formation of coatings, while experimenting with the particle erosion of the target exposed to a high velocity flow loaded with fine powder in a wind tunnel. In cold spraying, particles are accelerated to very high speeds by the carrier gas forced through a converging–diverging de Laval type nozzle
. Upon impact, solid particles with sufficient kinetic energy deform plastically and bond metallurgically to the substrate to form a coating. The critical velocity needed to form bonding depends on the materials properties, powder size and temperature. Soft metals such as Cu and Al are best suited for cold spraying, but coating of other materials (W, Ta, Ti, MCrAlY, WC–Co, etc.) by cold spraying has been reported.
The deposition efficiency is typically low for alloy powders, and the window of process parameters and suitable powder sizes is narrow. To accelerate powders to higher velocity, finer powders (<20 micrometers) are used. It is possible to accelerate powder particles to much higher velocity using a processing gas having high speed of sound
(helium instead of nitrogen).
However, helium is costly and its flow rate, and thus consumption, is higher. To improve acceleration capability, nitrogen gas is heated up to about 900 C. As a result, deposition efficiency and tensile strength of deposits increase.
Certain materials offer specific known hazards:
Coating
Coating is a covering that is applied to the surface of an object, usually referred to as the substrate. In many cases coatings are applied to improve surface properties of the substrate, such as appearance, adhesion, wetability, corrosion resistance, wear resistance, and scratch resistance...
processes in which melted (or heated) materials are sprayed onto a surface. The "feedstock" (coating precursor) is heated by electrical (plasma or arc) or chemical means (combustion flame).
Thermal spraying can provide thick coatings (approx. thickness range is 20 micrometers to several mm, depending on the process and feedstock), over a large area at high deposition rate as compared to other coating processes such as electroplating
Electroplating
Electroplating is a plating process in which metal ions in a solution are moved by an electric field to coat an electrode. The process uses electrical current to reduce cations of a desired material from a solution and coat a conductive object with a thin layer of the material, such as a metal...
, physical
Physical vapor deposition
Physical vapor deposition is a variety of vacuum deposition and is a general term used to describe any of a variety of methods to deposit thin films by the condensation of a vaporized form of the desired film material onto various workpiece surfaces...
and chemical vapor deposition
Chemical vapor deposition
Chemical vapor deposition is a chemical process used to produce high-purity, high-performance solid materials. The process is often used in the semiconductor industry to produce thin films. In a typical CVD process, the wafer is exposed to one or more volatile precursors, which react and/or...
. Coating materials available for thermal spraying include metals, alloys, ceramics, plastics and composites. They are fed in powder or wire form, heated to a molten or semimolten state and accelerated towards substrates in the form of micrometer-size particles. Combustion or electrical arc discharge is usually used as the source of energy for thermal spraying. Resulting coatings are made by the accumulation of numerous sprayed particles. The surface may not heat up significantly, allowing the coating of flammable substances.
Coating quality is usually assessed by measuring its porosity
Porosity
Porosity or void fraction is a measure of the void spaces in a material, and is a fraction of the volume of voids over the total volume, between 0–1, or as a percentage between 0–100%...
, oxide content, macro and micro-hardness, bond strength
Bond strength
In chemistry, bond strength is measured between two atoms joined in a chemical bond. It is the degree to which each atom linked to another atom contributes to the valency of this other atom...
and surface roughness. Generally, the coating quality increases with increasing particle velocities.
Several variations of thermal spraying are distinguished:
- Plasma spraying
- Detonation spraying
- Wire arc spraying
- Flame spraying
- High velocity oxy-fuel coating spraying (HVOF)
- Warm spraying
- Cold spraying
In classical (developed between 1910 and 1920) but still widely used processes such as flame spraying and wire arc spraying, the particle velocities are generally low (< 150 m/s), and raw materials must be molten to be deposited. Plasma spraying, developed in the 1970s, uses
a high-temperature plasma jet generated by arc discharge
with typical temperatures >15000 K, which makes it
possible to spray refractory materials such as oxides, molybdenum
Molybdenum
Molybdenum , is a Group 6 chemical element with the symbol Mo and atomic number 42. The name is from Neo-Latin Molybdaenum, from Ancient Greek , meaning lead, itself proposed as a loanword from Anatolian Luvian and Lydian languages, since its ores were confused with lead ores...
, etc.
System overview
A typical thermal spray system consists of the following:- Spray torch (or spray gun) - the core device performing the melting and acceleration of the particles to be deposited
- Feeder - for supplying the powderPowder (substance)A powder is a dry,thick bulk solid composed of a large number of very fine particles that may flow freely when shaken or tilted. Powders are a special sub-class of granular materials, although the terms powder and granular are sometimes used to distinguish separate classes of material...
, wireWireA wire is a single, usually cylindrical, flexible strand or rod of metal. Wires are used to bear mechanical loads and to carry electricity and telecommunications signals. Wire is commonly formed by drawing the metal through a hole in a die or draw plate. Standard sizes are determined by various...
or liquidLiquidLiquid is one of the three classical states of matter . Like a gas, a liquid is able to flow and take the shape of a container. Some liquids resist compression, while others can be compressed. Unlike a gas, a liquid does not disperse to fill every space of a container, and maintains a fairly...
to the torch - Media supply - gasGasGas is one of the three classical states of matter . Near absolute zero, a substance exists as a solid. As heat is added to this substance it melts into a liquid at its melting point , boils into a gas at its boiling point, and if heated high enough would enter a plasma state in which the electrons...
es or liquidLiquidLiquid is one of the three classical states of matter . Like a gas, a liquid is able to flow and take the shape of a container. Some liquids resist compression, while others can be compressed. Unlike a gas, a liquid does not disperse to fill every space of a container, and maintains a fairly...
s for the generation of the flame or plasma jet, gases for carrying the powderPowder (substance)A powder is a dry,thick bulk solid composed of a large number of very fine particles that may flow freely when shaken or tilted. Powders are a special sub-class of granular materials, although the terms powder and granular are sometimes used to distinguish separate classes of material...
, etc. - Robot - for manipulating the torch or the substrates to be coated
- Power supply - often standalone for the torch
- Control console(s) - either integrated or individual for all of the above
Detonation Thermal Spraying Process
The Detonation gun basically consists of a long water cooled barrel with inlet valves for gases and powder. Oxygen and fuel (acetylene most common) is fed into the barrel along with a charge of powder. A spark is used to ignite the gas mixture and the resulting detonation heats and accelerates the powder to supersonic velocity down the barrel. A pulse of nitrogen is used to purge the barrel after each detonation. This process is repeated many times a second. The high kinetic energy of the hot powder particles on impact with the substrate result in a build up of a very dense and strong coating.
Plasma spraying
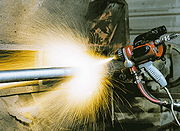
Powder (substance)
A powder is a dry,thick bulk solid composed of a large number of very fine particles that may flow freely when shaken or tilted. Powders are a special sub-class of granular materials, although the terms powder and granular are sometimes used to distinguish separate classes of material...
, sometimes as a liquid
Solution precursor plasma spray
Solution Precursor Plasma Spray is a thermal spray process where a feedstock solution is heated and then deposited onto a substrate. Basic properties of the process are fundamentally similar to other plasma spraying processes. However, instead of injecting a powder into the plasma plume, a liquid...
, suspension
Suspension Plasma Spray
In materials engineering, suspension plasma spray is a form of plasma spraying where the ceramic feedstock is dispersed in a liquid suspension before being injected into the plasma jet....
or wire — is introduced into the plasma jet, emanating from a plasma torch
Plasma torch
A plasma torch is a device for generating a directed flow of plasma. The plasma jet can be used for applications including plasma cutting, plasma spraying, and plasma arc waste disposal....
. In the jet, where the temperature is on the order of 10,000 K, the material is melted and propelled towards a substrate. There, the molten droplets flatten, rapidly solidify and form a deposit. Commonly, the deposits remain adherent to the substrate as coatings; free-standing parts can also be produced by removing the substrate. There are a large number of technological parameters that influence the interaction of the particles with the plasma jet and the substrate and therefore the deposit properties. These parameters include feedstock type, plasma gas composition and flow rate, energy input, torch offset distance, substrate cooling, etc.
Deposit properties
The deposits consist of a multitude of pancake-like lamellae called 'splats', formed by flattening of the liquid droplets. As the feedstock powders typically have sizes from micrometers to above 100 micrometers, the lamellae have thickness in the micrometer range and lateral dimension from several to hundreds of micrometers. Between these lamellae, there are small voids, such as pores, cracks and regions of incomplete bonding. As a result of this unique structure, the deposits can have properties significantly different from bulk materials. These are generally mechanical properties, such as lower strengthStrength of materials
In materials science, the strength of a material is its ability to withstand an applied stress without failure. The applied stress may be tensile, compressive, or shear. Strength of materials is a subject which deals with loads, deformations and the forces acting on a material. A load applied to a...
and modulus
Young's modulus
Young's modulus is a measure of the stiffness of an elastic material and is a quantity used to characterize materials. It is defined as the ratio of the uniaxial stress over the uniaxial strain in the range of stress in which Hooke's Law holds. In solid mechanics, the slope of the stress-strain...
, higher strain
Strain (materials science)
In continuum mechanics, the infinitesimal strain theory, sometimes called small deformation theory, small displacement theory, or small displacement-gradient theory, deals with infinitesimal deformations of a continuum body...
tolerance, and lower thermal
Thermal conductivity
In physics, thermal conductivity, k, is the property of a material's ability to conduct heat. It appears primarily in Fourier's Law for heat conduction....
and electrical conductivity. Also, due to the rapid solidification, metastable phases
Phase (matter)
In the physical sciences, a phase is a region of space , throughout which all physical properties of a material are essentially uniform. Examples of physical properties include density, index of refraction, and chemical composition...
can be present in the deposits.
Applications
This technique is mostly used to produce coatings on structural materials. Such coatings provide protection against high temperatures (for example thermal barrier coatings for exhaust heat managementExhaust heat management
Exhaust Heat Management is the means of lessening the negative effects of internal combustion engine exhausts by preventing heat from escaping the exhaust system on automobiles.-Overview:...
), corrosion
Corrosion
Corrosion is the disintegration of an engineered material into its constituent atoms due to chemical reactions with its surroundings. In the most common use of the word, this means electrochemical oxidation of metals in reaction with an oxidant such as oxygen...
, erosion
Erosion
Erosion is when materials are removed from the surface and changed into something else. It only works by hydraulic actions and transport of solids in the natural environment, and leads to the deposition of these materials elsewhere...
, wear
Wear
In materials science, wear is erosion or sideways displacement of material from its "derivative" and original position on a solid surface performed by the action of another surface....
; they can also change the appearance, electrical or tribological properties of the surface, replace worn material, etc. When sprayed on substrates of various shapes and removed, free-standing parts in the form of plates, tubes, shells, etc. can be produced. It can also be used for powder processing (spheroidization, homogenization, modification of chemistry, etc.). In this case, the substrate for deposition is absent and the particles solidify during flight or in a controlled environment (e.g., water).
A polymer dispersion aerosol can be injected into the plasma discharge in order to create a grafting of this polymer on to a substrate surface. This application is mainly used to modify the surface chemistry of polymers.
Variations
Plasma spraying systems can be categorized by several criteria.Plasma jet generation:
- direct currentDirect currentDirect current is the unidirectional flow of electric charge. Direct current is produced by such sources as batteries, thermocouples, solar cells, and commutator-type electric machines of the dynamo type. Direct current may flow in a conductor such as a wire, but can also flow through...
(DC plasma), where the energy is transferred to the plasma jet by a direct current, high-power electric arc - induction plasmaRadio-frequency inductionRadio-frequency induction or RF induction is the use of a radio frequency magnetic field to transfer energy by means of electromagnetic induction in the near field...
or RF plasma, where the energy is transferred by induction from a coil around the plasma jet, through which an alternatingAlternating currentIn alternating current the movement of electric charge periodically reverses direction. In direct current , the flow of electric charge is only in one direction....
, radio-frequency current passes
Plasma-forming medium:
- gas-stabilized plasma (GSP), where the plasma forms from a gas; typically argonArgonArgon is a chemical element represented by the symbol Ar. Argon has atomic number 18 and is the third element in group 18 of the periodic table . Argon is the third most common gas in the Earth's atmosphere, at 0.93%, making it more common than carbon dioxide...
, hydrogenHydrogenHydrogen is the chemical element with atomic number 1. It is represented by the symbol H. With an average atomic weight of , hydrogen is the lightest and most abundant chemical element, constituting roughly 75% of the Universe's chemical elemental mass. Stars in the main sequence are mainly...
, heliumHeliumHelium is the chemical element with atomic number 2 and an atomic weight of 4.002602, which is represented by the symbol He. It is a colorless, odorless, tasteless, non-toxic, inert, monatomic gas that heads the noble gas group in the periodic table...
or their mixtures - water-stabilized plasma (WSP), where plasma forms from waterWaterWater is a chemical substance with the chemical formula H2O. A water molecule contains one oxygen and two hydrogen atoms connected by covalent bonds. Water is a liquid at ambient conditions, but it often co-exists on Earth with its solid state, ice, and gaseous state . Water also exists in a...
(through evaporation, dissociation and ionization) or other suitable liquid - hybrid plasma - with combined gas and liquid stabilization, typically argon and water
Spraying environment:
- air plasma spraying (APS), performed in ambient air
- controlled atmosphere plasma spraying (CAPS), usually performed in a closed chamber, either filled with inert gasInert gasAn inert gas is a non-reactive gas used during chemical synthesis, chemical analysis, or preservation of reactive materials. Inert gases are selected for specific settings for which they are functionally inert since the cost of the gas and the cost of purifying the gas are usually a consideration...
or evacuated - variations of CAPS: high-pressure plasma spraying (HPPS), low-pressure plasma spraying (LPPS), the extreme case of which is vacuumVacuumIn everyday usage, vacuum is a volume of space that is essentially empty of matter, such that its gaseous pressure is much less than atmospheric pressure. The word comes from the Latin term for "empty". A perfect vacuum would be one with no particles in it at all, which is impossible to achieve in...
plasma spraying (VPS, see below) - underwater plasma spraying
Another variation consists of having a liquid feedstock instead of a solid powder for melting, this technique is known as Solution precursor plasma spray
Solution precursor plasma spray
Solution Precursor Plasma Spray is a thermal spray process where a feedstock solution is heated and then deposited onto a substrate. Basic properties of the process are fundamentally similar to other plasma spraying processes. However, instead of injecting a powder into the plasma plume, a liquid...
Vacuum plasma spraying
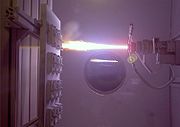
Surface
In mathematics, specifically in topology, a surface is a two-dimensional topological manifold. The most familiar examples are those that arise as the boundaries of solid objects in ordinary three-dimensional Euclidean space R3 — for example, the surface of a ball...
modification to create porous layers with high reproducibility and for cleaning and surface engineering of plastics, rubbers and natural fibers as well as for replacing CFC
Haloalkane
The haloalkanes are a group of chemical compounds derived from alkanes containing one or more halogens. They are a subset of the general class of halocarbons, although the distinction is not often made. Haloalkanes are widely used commercially and, consequently, are known under many chemical and...
s for cleaning metal components. This surface engineering can improve properties such as frictional behavior, heat resistance, surface electrical conductivity, lubricity
Lubricant
A lubricant is a substance introduced to reduce friction between moving surfaces. It may also have the function of transporting foreign particles and of distributing heat...
, cohesive strength of films, or dielectric constant
Dielectric constant
The relative permittivity of a material under given conditions reflects the extent to which it concentrates electrostatic lines of flux. In technical terms, it is the ratio of the amount of electrical energy stored in a material by an applied voltage, relative to that stored in a vacuum...
, or it can make materials hydrophilic or hydrophobic.
The process typically operates at 39–120 °C to avoid thermal damage. It can induce non-thermally activated surface reactions, causing surface changes which cannot occur with molecular chemistries at atmospheric pressure. Plasma processing
Plasma processing
Plasma processing is a plasma-based material processing technology that aims at modifying the chemical and physical properties of a surface.Plasma processing techniques include:*Plasma activation*Plasma etching*Plasma modification*Plasma functionalization...
is done in a controlled environment inside a sealed chamber at a medium vacuum, around 13–65 Pa
Pascal (unit)
The pascal is the SI derived unit of pressure, internal pressure, stress, Young's modulus and tensile strength, named after the French mathematician, physicist, inventor, writer, and philosopher Blaise Pascal. It is a measure of force per unit area, defined as one newton per square metre...
.
The gas
Gas
Gas is one of the three classical states of matter . Near absolute zero, a substance exists as a solid. As heat is added to this substance it melts into a liquid at its melting point , boils into a gas at its boiling point, and if heated high enough would enter a plasma state in which the electrons...
or mixture of gases is energized by an electrical field from DC
Direct current
Direct current is the unidirectional flow of electric charge. Direct current is produced by such sources as batteries, thermocouples, solar cells, and commutator-type electric machines of the dynamo type. Direct current may flow in a conductor such as a wire, but can also flow through...
to microwave
Microwave
Microwaves, a subset of radio waves, have wavelengths ranging from as long as one meter to as short as one millimeter, or equivalently, with frequencies between 300 MHz and 300 GHz. This broad definition includes both UHF and EHF , and various sources use different boundaries...
frequencies, typically 1–500 W at 50 V. The treated components are usually electrically isolated. The volatile plasma by-products are evacuated from the chamber by the vacuum pump
Vacuum pump
A vacuum pump is a device that removes gas molecules from a sealed volume in order to leave behind a partial vacuum. The first vacuum pump was invented in 1650 by Otto von Guericke.- Types :Pumps can be broadly categorized according to three techniques:...
, and if necessary can be neutralized in an exhaust scrubber
Scrubber
Scrubber systems are a diverse group of air pollution control devices that can be used to remove some particulates and/or gases from industrial exhaust streams. Traditionally, the term "scrubber" has referred to pollution control devices that use liquid to wash unwanted pollutants from a gas stream...
.
In contrast to molecular chemistry, plasmas employ:
- Molecular, atomic, metastable and free radical species for chemical effectsChemical substanceIn chemistry, a chemical substance is a form of matter that has constant chemical composition and characteristic properties. It cannot be separated into components by physical separation methods, i.e. without breaking chemical bonds. They can be solids, liquids or gases.Chemical substances are...
. - Positive ions and electrons for kinetic effectsKinetic energyThe kinetic energy of an object is the energy which it possesses due to its motion.It is defined as the work needed to accelerate a body of a given mass from rest to its stated velocity. Having gained this energy during its acceleration, the body maintains this kinetic energy unless its speed changes...
.
Plasma also generates electromagnetic radiation
Electromagnetic radiation
Electromagnetic radiation is a form of energy that exhibits wave-like behavior as it travels through space...
in the form of vacuum UV photons to penetrate bulk polymers to a depth of about 10 µm. This can cause chain scissions and cross-linking.
Plasmas affect materials at an atomic level. Techniques like X-ray photoelectron spectroscopy
X-ray photoelectron spectroscopy
X-ray photoelectron spectroscopy is a quantitative spectroscopic technique that measures the elemental composition, empirical formula, chemical state and electronic state of the elements that exist within a material...
and scanning electron microscopy
Scanning electron microscope
A scanning electron microscope is a type of electron microscope that images a sample by scanning it with a high-energy beam of electrons in a raster scan pattern...
are used for surface analysis to identify the processes required and to judge their effects.
As a simple indication of surface energy
Surface energy
Surface energy quantifies the disruption of intermolecular bonds that occur when a surface is created. In the physics of solids, surfaces must be intrinsically less energetically favorable than the bulk of a material, otherwise there would be a driving force for surfaces to be created, removing...
, and hence adhesion
Adhesion
Adhesion is any attraction process between dissimilar molecular species that can potentially bring them in close contact. By contrast, cohesion takes place between similar molecules....
or wettability, often a water droplet contact angle test
Contact angle
The contact angle is the angle at which a liquid/vapor interface meets a solid surface. The contact angle is specific for any given system and is determined by the interactions across the three interfaces. Most often the concept is illustrated with a small liquid droplet resting on a flat...
is used.
The lower the contact angle, the higher the surface energy and more hydrophilic the material is.
Changing effects with plasma
At higher energies ionizationIonization
Ionization is the process of converting an atom or molecule into an ion by adding or removing charged particles such as electrons or other ions. This is often confused with dissociation. A substance may dissociate without necessarily producing ions. As an example, the molecules of table sugar...
tends to occur more than chemical dissociations
Dissociation (chemistry)
Dissociation in chemistry and biochemistry is a general process in which ionic compounds separate or split into smaller particles, ions, or radicals, usually in a reversible manner...
. In a typical reactive gas, 1 in 100 molecules form free radicals whereas only 1 in 106 ionizes. The predominant effect here is the forming of free radicals.
Ionic effects can predominate with selection of process parameters and if necessary the use of noble gases.
Wire arc spray
Wire arc spray is a form of thermal spraying where two consumable metal wires are fed independently into the spray gun. These wires are then charged and an arc is generated between them. The heat from this arc melts the incoming wire, which is then entrained in air jet from the gun. This entrained molten feedstock is then deposited onto a substrate. This process is commonly used for metallic, heavy coatings.Plasma transferred wire arc
Plasma transferred wire arc is another form of wire arc spray which deposits a coating on the internal surface of a cylinder, or on the external surface of a part of any geometry. It is predominantly known for its use in coating the cylinder bores of an engine, enabling the use of Aluminum engine blocks without the need for heavy cast iron sleeves. A single conductive wire is used as "feedstock" for the system. A supersonic plasma jet melts the wire, atomizes it and propels it onto the substrate. The plasma jet is formed by a transferred arc between a non-consumable cathode and the type of a wire. After atomization, forced air transports the stream of molten droplets onto the bore wall. The particles flatten when they impinge on the surface of the substrate, due to the high kinetic energy. The particles rapidly solidify upon contact. The stacked particles make up a high wear resistant coating. The PTWA thermal spray process utilizes a single wire as the feedstock material. All conductive wires up to and including 0.0625" (1.6mm) can be used as feedstock material, including "cored" wires. PTWA can be used to apply a coating to the wear surface of engine or transmission components to replace a bushing or bearing. For example, using PTWA to coat the bearing surface of a connecting rod offers a number of benefits including reductions in weight, cost, friction potential, and stress in the connecting rod.High velocity oxygen fuel spraying (HVOF)
During the 1980s, a class of thermal spray processes called high velocity oxy-fuel spraying was developed: A mixture of gaseous or liquid fuelFuel
Fuel is any material that stores energy that can later be extracted to perform mechanical work in a controlled manner. Most fuels used by humans undergo combustion, a redox reaction in which a combustible substance releases energy after it ignites and reacts with the oxygen in the air...
and oxygen
Oxygen
Oxygen is the element with atomic number 8 and represented by the symbol O. Its name derives from the Greek roots ὀξύς and -γενής , because at the time of naming, it was mistakenly thought that all acids required oxygen in their composition...
is fed into a combustion chamber
Combustion chamber
A combustion chamber is the part of an engine in which fuel is burned.-Internal combustion engine:The hot gases produced by the combustion occupy a far greater volume than the original fuel, thus creating an increase in pressure within the limited volume of the chamber...
, where they are ignited and combusted continuously. The resultant hot gas at a pressure close to 1 MPa emanates through a converging–diverging nozzle and travels through a straight section. The fuels can be gases (hydrogen
Hydrogen
Hydrogen is the chemical element with atomic number 1. It is represented by the symbol H. With an average atomic weight of , hydrogen is the lightest and most abundant chemical element, constituting roughly 75% of the Universe's chemical elemental mass. Stars in the main sequence are mainly...
, methane
Methane
Methane is a chemical compound with the chemical formula . It is the simplest alkane, the principal component of natural gas, and probably the most abundant organic compound on earth. The relative abundance of methane makes it an attractive fuel...
, propane
Propane
Propane is a three-carbon alkane with the molecular formula , normally a gas, but compressible to a transportable liquid. A by-product of natural gas processing and petroleum refining, it is commonly used as a fuel for engines, oxy-gas torches, barbecues, portable stoves, and residential central...
, propylene
Propylene
Propene, also known as propylene or methylethylene, is an unsaturated organic compound having the chemical formula C3H6. It has one double bond, and is the second simplest member of the alkene class of hydrocarbons, and it is also second in natural abundance.-Properties:At room temperature and...
, acetylene
Acetylene
Acetylene is the chemical compound with the formula C2H2. It is a hydrocarbon and the simplest alkyne. This colorless gas is widely used as a fuel and a chemical building block. It is unstable in pure form and thus is usually handled as a solution.As an alkyne, acetylene is unsaturated because...
, natural gas
Natural gas
Natural gas is a naturally occurring gas mixture consisting primarily of methane, typically with 0–20% higher hydrocarbons . It is found associated with other hydrocarbon fuel, in coal beds, as methane clathrates, and is an important fuel source and a major feedstock for fertilizers.Most natural...
, etc.) or liquids (kerosene
Kerosene
Kerosene, sometimes spelled kerosine in scientific and industrial usage, also known as paraffin or paraffin oil in the United Kingdom, Hong Kong, Ireland and South Africa, is a combustible hydrocarbon liquid. The name is derived from Greek keros...
, etc.). The jet velocity at the exit of the barrel (>1000 m/s) exceeds the speed of sound
Speed of sound
The speed of sound is the distance travelled during a unit of time by a sound wave propagating through an elastic medium. In dry air at , the speed of sound is . This is , or about one kilometer in three seconds or approximately one mile in five seconds....
. A powder feed stock is injected into the gas stream, which accelerates the powder up to 800 m/s. The stream of hot gas and powder is directed towards the surface to be coated. The powder partially melts in the stream, and deposits upon the substrate. The resulting coating has low porosity
Porosity
Porosity or void fraction is a measure of the void spaces in a material, and is a fraction of the volume of voids over the total volume, between 0–1, or as a percentage between 0–100%...
and high bond strength
Bond strength
In chemistry, bond strength is measured between two atoms joined in a chemical bond. It is the degree to which each atom linked to another atom contributes to the valency of this other atom...
.
HVOF coatings may be as thick as 12 mm (1/2"). It is typically used to deposit wear
Wear
In materials science, wear is erosion or sideways displacement of material from its "derivative" and original position on a solid surface performed by the action of another surface....
and corrosion
Corrosion
Corrosion is the disintegration of an engineered material into its constituent atoms due to chemical reactions with its surroundings. In the most common use of the word, this means electrochemical oxidation of metals in reaction with an oxidant such as oxygen...
resistant coatings on materials, such as ceramic and metallic layers. Common powders include WC
Tungsten carbide
Tungsten carbide is an inorganic chemical compound containing equal parts of tungsten and carbon atoms. Colloquially, tungsten carbide is often simply called carbide. In its most basic form, it is a fine gray powder, but it can be pressed and formed into shapes for use in industrial machinery,...
-Co, chromium carbide
Chromium carbide
Chromium carbide is an extremely hard refractory ceramic material. It is usually processed by sintering. It has the appearance of a gray powder with orthorhombic crystal structure. The orthorhombic Cr3C2 occurs extremely rarely as mineral tongbaite....
, MCrAlY, and alumina. The process has been most successful for depositing cermet
Cermet
A cermet is a composite material composed of ceramic and metallic materials. A cermet is ideally designed to have the optimal properties of both a ceramic, such as high temperature resistance and hardness, and those of a metal, such as the ability to undergo plastic deformation. The metal is used...
materials (WC–Co, etc.) and other corrosion-resistant alloys (stainless steel
Stainless steel
In metallurgy, stainless steel, also known as inox steel or inox from French "inoxydable", is defined as a steel alloy with a minimum of 10.5 or 11% chromium content by mass....
s, nickel-based alloys, aluminium, hydroxyapatite for medical implants, etc.).
Cold spraying
In the 1990s, cold spraying (often called gas dynamic cold sprayGas dynamic cold spray
Gas dynamic cold spray is a coating deposition method developed in the mid-1980s in the Soviet Union in by Papyrin and his team. The solid powders are accelerated in supersonic gas jets to velocities up to 500–1000 m/s. During impact with the substrate, particles undergo plastic deformation and...
) has been introduced. The method was originally developed in Russia with the accidental observation of the rapid formation of coatings, while experimenting with the particle erosion of the target exposed to a high velocity flow loaded with fine powder in a wind tunnel. In cold spraying, particles are accelerated to very high speeds by the carrier gas forced through a converging–diverging de Laval type nozzle
De Laval nozzle
A de Laval nozzle is a tube that is pinched in the middle, making a carefully balanced, asymmetric hourglass-shape...
. Upon impact, solid particles with sufficient kinetic energy deform plastically and bond metallurgically to the substrate to form a coating. The critical velocity needed to form bonding depends on the materials properties, powder size and temperature. Soft metals such as Cu and Al are best suited for cold spraying, but coating of other materials (W, Ta, Ti, MCrAlY, WC–Co, etc.) by cold spraying has been reported.
The deposition efficiency is typically low for alloy powders, and the window of process parameters and suitable powder sizes is narrow. To accelerate powders to higher velocity, finer powders (<20 micrometers) are used. It is possible to accelerate powder particles to much higher velocity using a processing gas having high speed of sound
Speed of sound
The speed of sound is the distance travelled during a unit of time by a sound wave propagating through an elastic medium. In dry air at , the speed of sound is . This is , or about one kilometer in three seconds or approximately one mile in five seconds....
(helium instead of nitrogen).
However, helium is costly and its flow rate, and thus consumption, is higher. To improve acceleration capability, nitrogen gas is heated up to about 900 C. As a result, deposition efficiency and tensile strength of deposits increase.
Warm spraying
Is a novel modification of high velocity oxy-fuel spraying, in which the temperature of combustion gas is lowered by mixing nitrogen with the combustion gas, thus bringing the process closer to the cold spraying. The resulting gas contains much water vapor, unreacted hydrocarbons and oxygen, and thus is dirtier than the cold spraying. However, the coating efficiency is higher. On the other hand, lower temperatures of warm spraying reduce melting and chemical reactions of the feed powder, as compared to HVOF. These advantages are especially important for such coating materials as Ti, plastics, and metallic glasses, which rapidly oxidize or deteriorate at high temperatures.Applications
- CrankshaftCrankshaftThe crankshaft, sometimes casually abbreviated to crank, is the part of an engine which translates reciprocating linear piston motion into rotation...
reconditioning or conditioning - CorrosionCorrosionCorrosion is the disintegration of an engineered material into its constituent atoms due to chemical reactions with its surroundings. In the most common use of the word, this means electrochemical oxidation of metals in reaction with an oxidant such as oxygen...
protection - FoulingFoulingFouling refers to the accumulation of unwanted material on solid surfaces, most often in an aquatic environment. The fouling material can consist of either living organisms or a non-living substance...
protection - Altering thermal conductivityThermal conductivityIn physics, thermal conductivity, k, is the property of a material's ability to conduct heat. It appears primarily in Fourier's Law for heat conduction....
or electrical conductivity - Wear control: either hardfacingHardfacingHardfacing is a metalworking process where harder or tougher material is applied to a base metal. It is welded to the base material, and generally takes the form of specialized electrodes for arc welding or filler rod for oxyacetylene and TIG welding...
(wear-resistant) or abradable coatingAbradable coatingAn abradable coating is a coating made of an abradable material – meaning if it rubs against a more abrasive material in motion, the former will be worn whereas the latter will face no wear.... - Repairing damaged surfaces
- Temperature/oxidation protection (thermal barrier coatings)
- Medical implants
- Production of functionally graded materials (for either of the above applications)
Safety
Thermal spraying need not be a dangerous process, if the equipment is treated with care, and correct spraying practices are followed. As with any industrial process, there are a number of hazards, of which the operator should be aware, and against which specific precautions should be taken. Ideally, equipment should be operated automatically, in enclosures specially designed to extract fumes, reduce noise levels, and prevent direct viewing of the spraying head. Such techniques will also produce coatings that are more consistent. There are occasions when the type of components being treated, or their low production levels, requires manual equipment operation. Under these conditions, a number of hazards, peculiar to thermal spraying, are experienced, in addition to those commonly encountered in production or processing industries.Noise
Metal spraying equipment uses compressed gases, which create noise. Sound levels vary with the type of spraying equipment, the material being sprayed, and the operating parameters. Typical sound pressure levels taken 1 meter behind the arc.UV light
Combustion spraying equipment produces an intense flame, which may have a peak temperature more than 3,100°C, and is very bright. Electric arc spraying produces ultra-violet light, which may damage delicate body tissues. Spray booths, and enclosures, should be fitted with ultra-violet absorbent dark glass. Where this is not possible, operators, and others in the vicinity should wear protective goggles containing BS grade 6 green glass. Opaque screens should be placed around spraying areas. The nozzle of an arc pistol should never be viewed directly, unless it is certain that no power is available to the equipment.Dust and fumes
The atomization of molten materials produces a large amount of dust and fumes made up of very fine particles (about 80 – 95% of the particles by number <100 nm). Proper extraction facilities are vital, not only for personal safety, but to minimize entrapment of re-frozen particles in the sprayed coatings. The use of respirators, fitted with suitable filters, is strongly recommended, where equipment cannot be isolated.Certain materials offer specific known hazards:
- Finely divided metal particles are potentially pyrophoric and none should be allowed to accumulate.
- Certain materials e.g. aluminum, zinc and other base metals may react with water to evolve hydrogen. This is potentially explosive and special precautions are necessary in fume extraction equipment.
- Fumes of certain materials, notably zinc and copper alloys are unpleasant to smell, and, in certain individuals, may cause a fever-type reaction. This may occur some time after spraying and usually subsides rapidly. If it does not, medical advice must be sought.
Heat
Combustion spraying guns use oxygen and fuel gases. The fuel gases are potentially explosive. In particular, acetylene may only be used under approved conditions. Oxygen, while not explosive, will sustain combustion, and many materials will spontaneously ignite, if excessive oxygen levels are present. Care must be taken to avoid leakage, and to isolate oxygen and fuel gas supplies, when not in use.Shock hazards
Electric arc guns operate at low voltages (below 45 V dc), but at relatively high currents. They may be safely hand-held. The power supply units are connected to 440 V AC sources, and must be treated with caution.Further reading
- Pawlowski L, "The Science and Technology of Thermal Spray Coatings" (New York: Wiley, 1995)
- Papyrin A, Kosarev V, Klinkov S, Alkhimov A and Fomin V "Cold Spray Technology" (Oxford: Elsevier, 2007)
- Alternative Methods of Metal Deposition