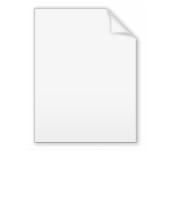
Industrial robot
Encyclopedia
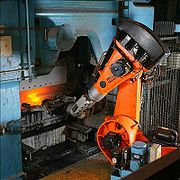
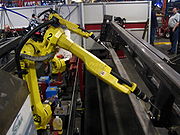
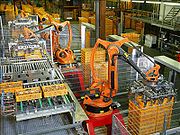
International Organization for Standardization
The International Organization for Standardization , widely known as ISO, is an international standard-setting body composed of representatives from various national standards organizations. Founded on February 23, 1947, the organization promulgates worldwide proprietary, industrial and commercial...
as an automatically controlled, reprogrammable, multipurpose manipulator programmable in three or more axes. The field of robotics may be more practically defined as the study, design and use of robot
Robot
A robot is a mechanical or virtual intelligent agent that can perform tasks automatically or with guidance, typically by remote control. In practice a robot is usually an electro-mechanical machine that is guided by computer and electronic programming. Robots can be autonomous, semi-autonomous or...
systems for manufacturing
Manufacturing
Manufacturing is the use of machines, tools and labor to produce goods for use or sale. The term may refer to a range of human activity, from handicraft to high tech, but is most commonly applied to industrial production, in which raw materials are transformed into finished goods on a large scale...
(a top-level definition relying on the prior definition of robot).
Typical applications of robots include welding
Robot welding
Robot welding is the use of mechanized programmable tools , which completely automate a welding process by both performing the weld and handling the part. Processes such as gas metal arc welding, while often automated, are not necessarily equivalent to robot welding, since a human operator...
, painting, assembly, pick and place (such as packaging, palletizing
Palletizer
right|thumb|250px|Palletizer using roboticsA palletizer or palletiser is a machine which provides automatic means for stacking cases of goods or products on to a pallet. The first palletizer was designed, built, and installed in 1948 by a company formerly known as Lamson Corp. There are specific...
and SMT
SMT Placement Equipment
SMT component placement systems, commonly called pick-and-place machines or P&Ps, are robotic machines which are used to place surface-mount devices onto a printed circuit board...
), product inspection, and testing; all accomplished with high endurance, speed, and precision.
Robot types, features
The most commonly used robot configurations are articulated robotArticulated robot
An articulated robot is a robot with rotary joints . Articulated robots can range from simple two-jointed structures to systems with 10 or more interacting joints....
s, SCARA
SCARA
The SCARA acronym stands for Selective Compliant Assembly Robot Arm or Selective Compliant Articulated Robot Arm.In 1981, Sankyo Seiki, Pentel and NEC presented a completely new concept for assembly robots. The robot was developed under the guidance of Hiroshi Makino, a professor at the University...
robots and Cartesian coordinate robot
Cartesian coordinate robot
A cartesian coordinate robot is an industrial robot whose three principal axes of control are linear and are at right angles to each other. Among other advantages, this mechanical arrangement simplifies the Robot control arm solution...
s, (aka gantry robots or x-y-z robots). In the context of general robotics, most types of robots would fall into the category of robotic arm
Robotic arm
A mechanical arm is a robotic, usually programmable, with similar functions to a human arm. The links of such a manipulator are connected by joints allowing either rotational motion or translational displacement. The links of the manipulator can be considered to form a kinematic chain...
s (inherent in the use of the word manipulator in the above-mentioned ISO standard).
Robots exhibit varying degrees of autonomy
Autonomous robot
Autonomous robots are robots that can perform desired tasks in unstructured environments without continuous human guidance. Many kinds of robots have some degree of autonomy. Different robots can be autonomous in different ways...
:
- Some robots are programmed to faithfully carry out specific actions over and over again (repetitive actions) without variation and with a high degree of accuracy. These actions are determined by programmed routineRoutineRoutine may refer to:*Subroutine in computer science*Choreographed routine, orchestrated dance involving several performers*Comedy routine, comedic act or part of an act*Visual routine, visual cognitive means of extracting information from a scene...
s that specify the direction, acceleration, velocity, deceleration, and distance of a series of coordinated motions. - Other robots are much more flexible as to the orientation of the object on which they are operating or even the task that has to be performed on the object itself, which the robot may even need to identify. For example, for more precise guidance, robots often contain machine visionMachine visionMachine vision is the process of applying a range of technologies and methods to provide imaging-based automatic inspection, process control and robot guidance in industrial applications. While the scope of MV is broad and a comprehensive definition is difficult to distil, a "generally accepted...
sub-systems acting as their "eyes", linked to powerful computers or controllers. Artificial intelligenceArtificial intelligenceArtificial intelligence is the intelligence of machines and the branch of computer science that aims to create it. AI textbooks define the field as "the study and design of intelligent agents" where an intelligent agent is a system that perceives its environment and takes actions that maximize its...
, or what passes for it, is becoming an increasingly important factor in the modern industrial robot.
History of industrial robotics
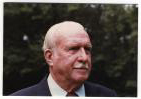
George Devol
George Charles Devol, Jr. was an American inventor who was awarded the patent for Unimate, the first industrial robot. Devol's patent for the first digitally operated programmable robotic arm represented the foundation of the modern robotics industry.As an inventor he had over 40 patents and was...
applied for the first robotics patent
Patent
A patent is a form of intellectual property. It consists of a set of exclusive rights granted by a sovereign state to an inventor or their assignee for a limited period of time in exchange for the public disclosure of an invention....
s in 1954 (granted in 1961). The first company to produce a robot was Unimation, founded by Devol and Joseph F. Engelberger
Joseph Engelberger
Joseph F. Engelberger is a physicist, engineer and entrepreneur who is referred to as the "Father of Robotics". Licensing the original patent awarded to inventor George Devol, Engelberger developed the first industrial robot in the United States, the Unimate, in the 1950s...
in 1956, and was based on Devol's original patents. Unimation robots were also called programmable transfer machines since their main use at first was to transfer objects from one point to another, less than a dozen feet or so apart. They used hydraulic
Hydraulics
Hydraulics is a topic in applied science and engineering dealing with the mechanical properties of liquids. Fluid mechanics provides the theoretical foundation for hydraulics, which focuses on the engineering uses of fluid properties. In fluid power, hydraulics is used for the generation, control,...
actuator
Actuator
An actuator is a type of motor for moving or controlling a mechanism or system. It is operated by a source of energy, usually in the form of an electric current, hydraulic fluid pressure or pneumatic pressure, and converts that energy into some kind of motion. An actuator is the mechanism by which...
s and were programmed in joint
Joint
A joint is the location at which two or more bones make contact. They are constructed to allow movement and provide mechanical support, and are classified structurally and functionally.-Classification:...
coordinates
Coordinate system
In geometry, a coordinate system is a system which uses one or more numbers, or coordinates, to uniquely determine the position of a point or other geometric element. The order of the coordinates is significant and they are sometimes identified by their position in an ordered tuple and sometimes by...
, i.e. the angles of the various joints were stored during a teaching phase and replayed in operation. They were accurate to within 1/10,000 of an inch (note: although accuracy is not an appropriate measure for robots, usually evaluated in terms of repeatability - see later). Unimation later licensed their technology to Kawasaki Heavy Industries
Kawasaki Heavy Industries
is an international corporation based in Japan. It has headquarters in both Chūō-ku, Kobe and Minato, Tokyo.The company is named after its founder Shōzō Kawasaki and has no connection with the city of Kawasaki, Kanagawa....
and Guest-Nettlefolds, manufacturing Unimate
Unimate
Unimate was the first industrial robot,which worked on a General Motors assembly line at the Inland Fisher Guide Plant in Ewing Township, New Jersey, in 1961.It was created by George Devol in the 1950s using his original patents...
s in Japan and England respectively. For some time Unimation's only competitor was Cincinnati Milacron Inc. of Ohio
Ohio
Ohio is a Midwestern state in the United States. The 34th largest state by area in the U.S.,it is the 7th‑most populous with over 11.5 million residents, containing several major American cities and seven metropolitan areas with populations of 500,000 or more.The state's capital is Columbus...
. This changed radically in the late 1970s when several big Japanese conglomerates began producing similar industrial robots.
In 1969 Victor Scheinman
Victor Scheinman
Victor Scheinman is a pioneer in the field of robotics. He is a graduate of the now-defunct New Lincoln High School in New York. In the late 1950s, and while in high school, Scheinman engineered a speech-to-text machine as a science fair project...
at Stanford University
Stanford University
The Leland Stanford Junior University, commonly referred to as Stanford University or Stanford, is a private research university on an campus located near Palo Alto, California. It is situated in the northwestern Santa Clara Valley on the San Francisco Peninsula, approximately northwest of San...
invented the Stanford arm, an all-electric, 6-axis articulated robot designed to permit an arm solution
Arm solution
In applied mathematics as used in the engineering field of robotics, an arm solution is a solution of equations that allow the calculation of the precise design parameters of a robot's arms in such a way as to enable it to make certain movements....
. This allowed it accurately to follow arbitrary paths in space and widened the potential use of the robot to more sophisticated applications such as assembly and welding. Scheinman then designed a second arm for the MIT
Massachusetts Institute of Technology
The Massachusetts Institute of Technology is a private research university located in Cambridge, Massachusetts. MIT has five schools and one college, containing a total of 32 academic departments, with a strong emphasis on scientific and technological education and research.Founded in 1861 in...
AI
Artificial intelligence
Artificial intelligence is the intelligence of machines and the branch of computer science that aims to create it. AI textbooks define the field as "the study and design of intelligent agents" where an intelligent agent is a system that perceives its environment and takes actions that maximize its...
Lab, called the "MIT arm." Scheinman, after receiving a fellowship from Unimation to develop his designs, sold those designs to Unimation who further developed them with support from General Motors
General Motors
General Motors Company , commonly known as GM, formerly incorporated as General Motors Corporation, is an American multinational automotive corporation headquartered in Detroit, Michigan and the world's second-largest automaker in 2010...
and later marketed it as the Programmable Universal Machine for Assembly
Programmable Universal Machine for Assembly
The PUMA is an industrial robot arm developed by Victor Scheinman at pioneering robot company Unimation...
(PUMA).
Industrial robotics took off quite quickly in Europe, with both ABB Robotics and KUKA Robotics
KUKA
KUKA is a leading German producer of industrial robots for a variety of industries - from automotive and fabricated metals to food and plastics...
bringing robots to the market in 1973. ABB Robotics (formerly ASEA) introduced IRB 6, among the world's first commercially available all electric micro-processor controlled robot. The first two IRB 6 robots were sold to Magnusson in Sweden for grinding and polishing pipe bends and were installed in production in January 1974. Also in 1973 KUKA Robotics built its first robot, known as FAMULUS, also one of the first articulated robot to have six electromechanically driven axes.
Interest in robotics increased in the late 1970s and many US companies entered the field, including large firms like General Electric
General Electric
General Electric Company , or GE, is an American multinational conglomerate corporation incorporated in Schenectady, New York and headquartered in Fairfield, Connecticut, United States...
, and General Motors
General Motors
General Motors Company , commonly known as GM, formerly incorporated as General Motors Corporation, is an American multinational automotive corporation headquartered in Detroit, Michigan and the world's second-largest automaker in 2010...
(which formed joint venture
Joint venture
A joint venture is a business agreement in which parties agree to develop, for a finite time, a new entity and new assets by contributing equity. They exercise control over the enterprise and consequently share revenues, expenses and assets...
FANUC Robotics
FANUC Robotics
FANUC or is a Japanese electromechanical manufacturer specializing in robotics. It is one of the largest maker of industrial robots in the world. It is part of the Furukawa Group. FANUC had its beginnings as part of Fujitsu developing numerical control and servo systems...
with FANUC LTD of Japan). U.S. startup companies included Automatix
Automatix
Automatix Inc., founded in January 1980, was the first company to market industrial robots with built-in machine vision. Its founders were Victor Scheinman, inventor of the Stanford arm; Phillippe Villers, Michael Cronin, and Arnold Reinhold of Computervision; Jake Dias and Dan Nigro of Data...
and Adept Technology
Adept Technology
Adept Technology, Inc. is a multinational corporation with headquarters in Pleasanton, California . The company focuses on industrial automation and robotics, including software and vision guidance. Adept has offices throughout the United States as well as in Dortmund, Germany, Paris, France, and...
, Inc. At the height of the robot boom in 1984, Unimation was acquired by Westinghouse Electric Corporation
Westinghouse Electric (1886)
Westinghouse Electric was an American manufacturing company. It was founded in 1886 as Westinghouse Electric Company and later renamed Westinghouse Electric Corporation by George Westinghouse. The company purchased CBS in 1995 and became CBS Corporation in 1997...
for 107 million U.S. dollars. Westinghouse sold Unimation to Stäubli Faverges SCA of France
France
The French Republic , The French Republic , The French Republic , (commonly known as France , is a unitary semi-presidential republic in Western Europe with several overseas territories and islands located on other continents and in the Indian, Pacific, and Atlantic oceans. Metropolitan France...
in 1988, which is still making articulated robots for general industrial and cleanroom
Cleanroom
A cleanroom is an environment, typically used in manufacturing or scientific research, that has a low level of environmental pollutants such as dust, airborne microbes, aerosol particles and chemical vapors. More accurately, a cleanroom has a controlled level of contamination that is specified by...
applications and even bought the robotic division of Bosch
Robert Bosch GmbH
Robert Bosch GmbH is a multinational engineering and electronics company headquartered in Gerlingen, near Stuttgart, Germany. It is the world's largest supplier of automotive components...
in late 2004.
Only a few non-Japanese companies ultimately managed to survive in this market, the major ones being Adept Technology
Adept Technology
Adept Technology, Inc. is a multinational corporation with headquarters in Pleasanton, California . The company focuses on industrial automation and robotics, including software and vision guidance. Adept has offices throughout the United States as well as in Dortmund, Germany, Paris, France, and...
, Stäubli-Unimation, the Swedish
Sweden
Sweden , officially the Kingdom of Sweden , is a Nordic country on the Scandinavian Peninsula in Northern Europe. Sweden borders with Norway and Finland and is connected to Denmark by a bridge-tunnel across the Öresund....
-Swiss
Switzerland
Switzerland name of one of the Swiss cantons. ; ; ; or ), in its full name the Swiss Confederation , is a federal republic consisting of 26 cantons, with Bern as the seat of the federal authorities. The country is situated in Western Europe,Or Central Europe depending on the definition....
company ABB Asea Brown Boveri and the German
Germany
Germany , officially the Federal Republic of Germany , is a federal parliamentary republic in Europe. The country consists of 16 states while the capital and largest city is Berlin. Germany covers an area of 357,021 km2 and has a largely temperate seasonal climate...
company KUKA Robotics
KUKA
KUKA is a leading German producer of industrial robots for a variety of industries - from automotive and fabricated metals to food and plastics...
.
Defining parameters
- Number of axes – two axes are required to reach any point in a plane; three axes are required to reach any point in space. To fully control the orientation of the end of the arm (i.e. the wrist) three more axes (yaw, pitch, and roll) are required. Some designs (e.g. the SCARA robot) trade limitations in motion possibilities for cost, speed, and accuracy.
- Degrees of freedom which is usually the same as the number of axes.
- Working envelopeEnvelope (mechanical engineering)In mechanical engineering, an envelope is a solid representing all positions which may be occupied by an object during its normal range of motion.Another word for this is a "flop".-Wheel envelope:...
– the region of space a robot can reach. - KinematicsRobot kinematicsRobot kinematics is the study of the motion of robots. In a kinematic analysis the position, velocity and acceleration of all the links are calculated without considering the forces that cause this motion. The relationship between motion, and the associated forces and torques is studied in robot...
– the actual arrangement of rigid members and jointJointA joint is the location at which two or more bones make contact. They are constructed to allow movement and provide mechanical support, and are classified structurally and functionally.-Classification:...
s in the robot, which determines the robot's possible motions. Classes of robot kinematics include articulated, cartesian, parallel and SCARA. - Carrying capacity or payloadCargoCargo is goods or produce transported, generally for commercial gain, by ship, aircraft, train, van or truck. In modern times, containers are used in most intermodal long-haul cargo transport.-Marine:...
– how much weight a robot can lift. - Speed – how fast the robot can position the end of its arm. This may be defined in terms of the angular or linear speed of each axis or as a compound speed i.e. the speed of the end of the arm when all axes are moving.
- Acceleration - how quickly an axis can accelerate. Since this is a limiting factor a robot may not be able to reach its specified maximum speed for movements over a short distance or a complex path requiring frequent changes of direction.
- Accuracy – how closely a robot can reach a commanded position. When the absolute position of the robot is measured and compared to the commanded position the error is a measure of accuracy. Accuracy can be improved with external sensing for example a vision system or Infra-Red. See robot calibrationRobot calibrationRobot calibration is the process of determining the actual values of kinematic and dynamic parameters of an industrial robot . Kinematic parameters describe the relative position and orientation of links and joints in the robot while the dynamic parameters describe arm and joint masses and...
. Accuracy can vary with speed and position within the working envelope and with payload (see compliance). - Repeatability - how well the robot will return to a programmed position. This is not the same as accuracy. It may be that when told to go to a certain X-Y-Z position that it gets only to within 1 mm of that position. This would be its accuracy which may be improved by calibration. But if that position is taught into controller memory and each time it is sent there it returns to within 0.1mm of the taught position then the repeatability will be within 0.1mm.
Accuracy and repeatability are different measures. Repeatability is usually the most important criterion for a robot. ISO 9283 sets out a method whereby both accuracy and repeatability can be measured. Typically a robot is sent to a taught position a number of times and the error is measured at each return to the position after visiting 4 other positions. Repeatability is then quantified using the standard deviation
Standard deviation
Standard deviation is a widely used measure of variability or diversity used in statistics and probability theory. It shows how much variation or "dispersion" there is from the average...
of those samples in all three dimensions. A typical robot can, of course make a positional error exceeding that and that could be a problem for the process. Moreover the repeatability is different in different parts of the working envelope and also changes with speed and payload. ISO 9283 specifies that accuracy and repeatability should be measured at maximum speed and at maximum payload. But this results in pessimistic values whereas the robot could be much more accurate and repeatable at light loads and speeds.
Repeatability in an industrial process is also subject to the accuracy of the end effector, for example a gripper, and even to the design of the 'fingers' that match the gripper to the object being grasped. For example if a robot picks a screw by its head the screw could be at a random angle. A subsequent attempt to insert the screw into a hole could easily fail. These and similar scenarios can be improved with 'lead-ins' e.g. by making the entrance to the hole tapered.
- Motion control – for some applications, such as simple pick-and-place assembly, the robot need merely return repeatably to a limited number of pre-taught positions. For more sophisticated applications, such as welding and finishing (spray paintingSpray paintingSpray painting is a painting technique where a device sprays a coating through the air onto a surface. The most common types employ compressed gas—usually air—to atomize and direct the paint particles. Spray guns evolved from airbrushes, and the two are usually distinguished by their size and the...
), motion must be continuously controlled to follow a path in space, with controlled orientation and velocity. - Power source – some robots use electric motorElectric motorAn electric motor converts electrical energy into mechanical energy.Most electric motors operate through the interaction of magnetic fields and current-carrying conductors to generate force...
s, others use hydraulicHydraulicsHydraulics is a topic in applied science and engineering dealing with the mechanical properties of liquids. Fluid mechanics provides the theoretical foundation for hydraulics, which focuses on the engineering uses of fluid properties. In fluid power, hydraulics is used for the generation, control,...
actuators. The former are faster, the latter are stronger and advantageous in applications such as spray painting, where a spark could set off an explosionExplosionAn explosion is a rapid increase in volume and release of energy in an extreme manner, usually with the generation of high temperatures and the release of gases. An explosion creates a shock wave. If the shock wave is a supersonic detonation, then the source of the blast is called a "high explosive"...
; however, low internal air-pressurisation of the arm can prevent ingress of flammable vapours as well as other contaminants. - Drive – some robots connect electric motors to the joints via gearGearA gear is a rotating machine part having cut teeth, or cogs, which mesh with another toothed part in order to transmit torque. Two or more gears working in tandem are called a transmission and can produce a mechanical advantage through a gear ratio and thus may be considered a simple machine....
s; others connect the motor to the joint directly (direct drive). Using gears results in measurable 'backlash' which is free movement in an axis. Smaller robot arms frequently employ high speed, low torque DC motors, which generally require high gearing ratios; this has the disadvantage of backlash. In such cases the harmonic driveHarmonic DriveA Harmonic Drive is a special type of mechanical gear system that can improve certain characteristics compared to traditional gearing systems . It was invented in 1957 and is now produced by Harmonic Drive LLC...
is often used. - Compliance - this is a measure of the amount in angle or distance that a robot axis will move when a force is applied to it. Because of compliance when a robot goes to a position carrying its maximum payload it will be at a position slightly lower than when it is carrying no payload. Compliance can also be responsible for overshoot when carrying high payloads in which case acceleration would need to be reduced.
Robot programming and interfaces
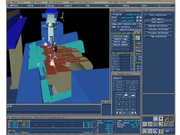
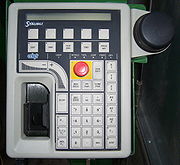
Computer programming
Computer programming is the process of designing, writing, testing, debugging, and maintaining the source code of computer programs. This source code is written in one or more programming languages. The purpose of programming is to create a program that performs specific operations or exhibits a...
of motions and sequences for an industrial robot is typically taught by linking the robot controller to a laptop
Laptop
A laptop, also called a notebook, is a personal computer for mobile use. A laptop integrates most of the typical components of a desktop computer, including a display, a keyboard, a pointing device and speakers into a single unit...
, desktop computer
Computer
A computer is a programmable machine designed to sequentially and automatically carry out a sequence of arithmetic or logical operations. The particular sequence of operations can be changed readily, allowing the computer to solve more than one kind of problem...
or (internal or Internet) network
Computer network
A computer network, often simply referred to as a network, is a collection of hardware components and computers interconnected by communication channels that allow sharing of resources and information....
.
A robot and a collection of machines or peripherals is referred to as a workcell
Workcell
A workcell is an arrangement of resources in a manufacturing environment to improve the quality, speed and cost of the process. Workcells are designed to improve these by improving process flow and eliminating waste...
, or cell. A typical cell might contain a parts feeder, a molding machine
Injection molding machine
An Injection molding machine, also known as an injection press, is a machine for manufacturing plastic products by the injection molding process. It consists of two main parts, an injection unit and a clamping unit....
and a robot. The various machines are 'integrated' and controlled by a single computer or PLC
Programmable logic controller
A programmable logic controller or programmable controller is a digital computer used for automation of electromechanical processes, such as control of machinery on factory assembly lines, amusement rides, or light fixtures. PLCs are used in many industries and machines...
. How the robot interacts with other machines in the cell must be programmed, both with regard to their positions in the cell and synchronizing with them.
Software: The computer is installed with corresponding interface
Interface (computer science)
In the field of computer science, an interface is a tool and concept that refers to a point of interaction between components, and is applicable at the level of both hardware and software...
software. The use of a computer greatly simplifies the programming process. Specialized robot software
Robot software
Robot software is the coded commands that tell a mechanical device what tasks to perform and control its actions. Robot software is used to perform tasks and automate tasks to be performed. Programming robots is a non-trivial task...
is run either in the robot controller or in the computer or both depending on the system design.
There are two basic entities that need to be taught (or programmed): positional data and procedure. For example in a task to move a screw from a feeder to a hole the positions of the feeder and the hole must first be taught or programmed. Secondly the procedure to get the screw from the feeder to the hole must be programmed along with any I/O involved, for example a signal to indicate when the screw is in the feeder ready to be picked up. The purpose of the robot software is to facilitate both these programming tasks.
Teaching the robot positions may be achieved a number of ways:
Positional commands The robot can be directed to the required position using a GUI
Gui
Gui or guee is a generic term to refer to grilled dishes in Korean cuisine. These most commonly have meat or fish as their primary ingredient, but may in some cases also comprise grilled vegetables or other vegetarian ingredients. The term derives from the verb, "gupda" in Korean, which literally...
or text based commands in which the required X-Y-Z position may be specified and edited.
Teach pendant: Robot positions can be taught via a teach pendant. This is a handheld control and programming unit. The common features of such units are the ability to manually send the robot to a desired position, or "inch" or "jog" to adjust a position. They also have a means to change the speed since a low speed is usually required for careful positioning, or while test-running through a new or modified routine. A large emergency stop
Emergency stop
-United Kingdom driving test:For the practical section of the driving test, an examiner will often request the candidate to perform an emergency stop. This is done in order to evaluate how well a candidate can react to a dangerous situation and bring their motor vehicle to a safe stop. This is to...
button is usually included as well. Typically once the robot has been programmed there is no more use for the teach pendant.
Lead-by-the-nose is a technique offered by many robot manufacturers. In this method, one user holds the robot's manipulator, while another person enters a command which de-energizes the robot causing it to go limp. The user then moves the robot by hand to the required positions and/or along a required path while the software logs these positions into memory. The program can later run the robot to these positions or along the taught path. This technique is popular for tasks such as paint spraying
Spray painting
Spray painting is a painting technique where a device sprays a coating through the air onto a surface. The most common types employ compressed gas—usually air—to atomize and direct the paint particles. Spray guns evolved from airbrushes, and the two are usually distinguished by their size and the...
.
Offline programming is where the entire cell, the robot and all the machines or instruments in the workspace are mapped graphically. The robot can then be moved on screen and the process simulated. The technique has limited value because it relies on accurate measurement of the positions of the associated equipment and also relies on the positional accuracy the robot which may or may not conform to what is programmed (see accuracy and repeatability, above).
Others In addition, machine operators often use user interface
User interface
The user interface, in the industrial design field of human–machine interaction, is the space where interaction between humans and machines occurs. The goal of interaction between a human and a machine at the user interface is effective operation and control of the machine, and feedback from the...
devices, typically touchscreen
Touchscreen
A touchscreen is an electronic visual display that can detect the presence and location of a touch within the display area. The term generally refers to touching the display of the device with a finger or hand. Touchscreens can also sense other passive objects, such as a stylus...
units, which serve as the operator control panel. The operator can switch from program to program, make adjustments within a program and also operate a host of peripheral
Peripheral
A peripheral is a device attached to a host computer, but not part of it, and is more or less dependent on the host. It expands the host's capabilities, but does not form part of the core computer architecture....
devices that may be integrated within the same robotic system. These include end effectors, feeders that supply components to the robot, conveyor belt
Conveyor belt
A conveyor belt consists of two or more pulleys, with a continuous loop of material - the conveyor belt - that rotates about them. One or both of the pulleys are powered, moving the belt and the material on the belt forward. The powered pulley is called the drive pulley while the unpowered pulley...
s, emergency stop controls, machine vision systems, safety interlock
Interlock (engineering)
Interlocking is a method of preventing undesired states in a state machine, which in a general sense can include any electrical, electronic, or mechanical device or system....
systems, bar code
Barcode
A barcode is an optical machine-readable representation of data, which shows data about the object to which it attaches. Originally barcodes represented data by varying the widths and spacings of parallel lines, and may be referred to as linear or 1 dimensional . Later they evolved into rectangles,...
printers and an almost infinite array of other industrial devices which are accessed and controlled via the operator control panel.
The teach pendant or PC is usually disconnected after programming and the robot then runs on the program that has been installed in its controller
Controller (computing)
In computing and especially in computer hardware, controller is a chip, an expansion card, or a stand-alone device that interfaces with a peripheral device...
. However a computer is often used to 'supervise' the robot and any peripherals, or to provide additional storage for access to numerous complex paths and routines.
End-of-arm Tooling
The most essential robot peripheral is the end effectorRobot end effector
In robotics, an end effector is the device at the end of a robotic arm, designed to interact with the environment. The exact nature of this device depends on the application of the robot....
, or end-of-arm-tooling (EOT). Common examples of end effectors include welding devices (such as MIG-welding guns, spot-welders, etc.), spray guns and also grinding and deburring devices (such as pneumatic disk or belt grinders, burrs, etc.), and grippers (devices that can grasp an object, usually electromechanical
Electromechanics
In engineering, electromechanics combines the sciences of electromagnetism, of electrical engineering and mechanics. Mechanical engineering in this context refers to the larger discipline which includes chemical engineering, and other related disciplines. Electrical engineering in this context...
or pneumatic
Pneumatics
Pneumatics is a branch of technology, which deals with the study and application of use of pressurized gas to effect mechanical motion.Pneumatic systems are extensively used in industry, where factories are commonly plumbed with compressed air or compressed inert gases...
). Another common means of picking up an object is by vacuum
Vacuum
In everyday usage, vacuum is a volume of space that is essentially empty of matter, such that its gaseous pressure is much less than atmospheric pressure. The word comes from the Latin term for "empty". A perfect vacuum would be one with no particles in it at all, which is impossible to achieve in...
. End effectors are frequently highly complex, made to match the handled product and often capable of picking up an array of products at one time. They may utilize various sensors to aid the robot system in locating, handling, and positioning products.
Controlling Movement
For a given robot the only parameters necessary to completely locate the end effector (gripper, welding torch, etc.) of the robot are the angles of each of the joints or displacements of the linear axes (or combinations of the two for robot formats such as SCARA). However there are many different ways to define the points. The most common and most convenient way of defining a point is to specify a Cartesian coordinateCartesian coordinate system
A Cartesian coordinate system specifies each point uniquely in a plane by a pair of numerical coordinates, which are the signed distances from the point to two fixed perpendicular directed lines, measured in the same unit of length...
for it, i.e. the position of the 'end effector' in mm in the X, Y and Z directions relative to the robot's origin. In addition, depending on the types of joints a particular robot may have, the orientation of the end effector in yaw, pitch, and roll and the location of the tool point relative to the robot's faceplate must also be specified. For a jointed arm
Robotic arm
A mechanical arm is a robotic, usually programmable, with similar functions to a human arm. The links of such a manipulator are connected by joints allowing either rotational motion or translational displacement. The links of the manipulator can be considered to form a kinematic chain...
these coordinates must be converted to joint angles by the robot controller and such conversions are known as Cartesian Transformations which may need to be performed iteratively or recursively for a multiple axis robot. The mathematics of the relationship between joint angles and actual spatial coordinates is called kinematics. See robot control
Robot control
-See also:* Control theory* Mobile robot navigation* Robot kinematics* Simultaneous localization and mapping* Robot locomotion* Motion planning* Robot learning* Vision Based Robot Control...
Positioning by Cartesian coordinates may be done by entering the coordinates into the system or by using a teach pendant which moves the robot in X-Y-Z directions. It is much easier for a human operator to visualize motions up/down, left/right, etc. than to move each joint one at a time. When the desired position is reached it is then defined in some way particular to the robot software in use, e.g. P1 - P5 below.
Typical Programming
Most articulated robots perform by storing a series of positions in memory, and moving to them at various times in their programming sequence. For example, a robot which is moving items from one place to another might have a simple 'pick and place' program similar to the following:Define points P1–P5:
- Safely above workpiece (defined as P1)
- 10 cm Above bin A (defined as P2)
- At position to take part from bin A (defined as P3)
- 10 cm Above bin B (defined as P4)
- At position to take part from bin B. (defined as P5)
Define program:
- Move to P1
- Move to P2
- Move to P3
- Close gripper
- Move to P2
- Move to P4
- Move to P5
- Open gripper
- Move to P4
- Move to P1 and finish
For examples of how this would look in popular robot languages see industrial robot programming.
Singularities
The American National Standard for Industrial Robots and Robot Systems — Safety Requirements (ANSI/RIA R15.06-1999) defines a singularity as “a condition caused by the collinear alignment of two or more robot axes resulting in unpredictable robot motion and velocities.” It is most common in robot arms that utilize a “triple-roll wrist”. This is a wrist about which the three axes of the wrist, controlling yaw, pitch, and roll, all pass through a common point. An example of a wrist singularity is when the path through which the robot is traveling causes the first and third axes of the robot’s wrist to line up. The second wrist axis then attempts to spin 360° in zero time to maintain the orientation of the end effector. Another common term for this singularity is a “wrist flip”. The result of a singularity can be quite dramatic and can have adverse effects on the robot arm, the end effector, and the process. Some industrial robot manufacturers have attempted to side-step the situation by slightly altering the robot’s path to prevent this condition. Another method is to slow the robot’s travel speed, thus reducing the speed required for the wrist to make the transition. The ANSI/RIA has mandated that robot manufacturers shall make the user aware of singularities if they occur while the system is being manually manipulated.Recent and future developments
As of 2005, the robotic arm business is approaching a mature state, where they can provide enough speed, accuracy and ease of use for most of the applications. Vision guidance (aka machine vision) is bringing a lot of flexibility to robotic cells. However, the end effector attached to a robot is often a simple pneumatic, 2-position chuckChuck (engineering)
A chuck is a specialized type of clamp used to hold an object, usually an object with radial symmetry, especially a cylindrical object. It is most commonly used to hold a rotating tool or a rotating workpiece...
. This does not allow the robotic cell to easily handle different parts, in different orientations.
Hand-in-hand with increasing off-line programmed applications, robot calibration
Robot calibration
Robot calibration is the process of determining the actual values of kinematic and dynamic parameters of an industrial robot . Kinematic parameters describe the relative position and orientation of links and joints in the robot while the dynamic parameters describe arm and joint masses and...
is becoming more and more important in order to guarantee a good positioning accuracy.
Other developments include downsizing industrial arms for light industrial use such as production of small products, sealing and dispensing, quality control, handling samples in the laboratory. Such robots are usually classified as "bench top" robots. Robots are used in pharmaceutical research in a technique called High-throughput screening
High-throughput screening
High-throughput screening is a method for scientific experimentation especially used in drug discovery and relevant to the fields of biology and chemistry. Using robotics, data processing and control software, liquid handling devices, and sensitive detectors, High-Throughput Screening allows a...
. Bench top robots are also used in consumer applications (micro-robotic arms). Industrial arms may be used in combination with or even mounted on automated guided vehicle
Automated Guided Vehicle
An automated guided vehicle or automatic guided vehicle is a mobile robot that follows markers or wires in the floor, or uses vision or lasers. They are most often used in industrial applications to move materials around a manufacturing facility or a warehouse...
s (AGVs) to make the automation chain
Logistics automation
Logistics automation is the application of computer software and/or automated machinery to improve the efficiency of logistics operations. Typically this refers to operations within a warehouse or distribution center, with broader tasks undertaken by supply chain management systems and enterprise...
more flexible between pick-up and drop-off.
Market structure
The 2010 report from the International Federation of Robotics shows that Japanese companies lead the world in both stock and sales of multi-purpose industrial robots. About 60 per cent of the installations were articulated robotArticulated robot
An articulated robot is a robot with rotary joints . Articulated robots can range from simple two-jointed structures to systems with 10 or more interacting joints....
s, 22 per cent were gantry robot
Cartesian coordinate robot
A cartesian coordinate robot is an industrial robot whose three principal axes of control are linear and are at right angles to each other. Among other advantages, this mechanical arrangement simplifies the Robot control arm solution...
s, and 13 per cent were SCARA
SCARA
The SCARA acronym stands for Selective Compliant Assembly Robot Arm or Selective Compliant Articulated Robot Arm.In 1981, Sankyo Seiki, Pentel and NEC presented a completely new concept for assembly robots. The robot was developed under the guidance of Hiroshi Makino, a professor at the University...
robots and 4 per cent were cylindrical robots. The majority of installations are in the automobile sector. There are increasing sales into non automotive sectors such as metals and plastics.
In 2007 the world market grew by 3% with approximately 114,000 new installed industrial robots. At the end of 2007 there were around one million industrial robots in use, compared with an estimated 50,000 service robot
Service robot
Service robots assist human beings, typically by performing a job that is dirty, dull, distant, dangerous or repetitive, including household chores. They typically are autonomous and/or operated by a build in control system, with manual override options....
s for industrial use.
Further reading
- Nof, Shimon Y. (editor) (1999). Handbook of Industrial Robotics, 2nd ed. John Wiley & Sons. 1378 pp. ISBN 0-471-17783-0.
- Lars Westerlund (author) (2000). The extended arm of man. ISBN 91-7736-467-8.
External links
- Industrial robots and robot system safety (by OSHAOccupational Safety and Health AdministrationThe United States Occupational Safety and Health Administration is an agency of the United States Department of Labor. It was created by Congress of the United States under the Occupational Safety and Health Act, signed by President Richard M. Nixon, on December 29, 1970...
, so in the public domain). - International Federation of Robotics IFR (worldwide)
- Robotic Industries Association RIA (North America).