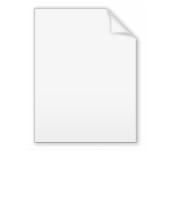
Rockwell scale
Encyclopedia
The Rockwell scale is a hardness scale based on the indentation hardness
of a material. The Rockwell test determines the hardness by measuring the depth of penetration of an indenter under a large load compared to the penetration made by a preload. There are different scales, denoted by a single letter, that use different loads or indenters. The result is a dimensionless number noted as HRX, where X is the scale letter.
When testing metals, indentation hardness correlates linearly with tensile strength
. This important relation permits economically important nondestructive testing of bulk metal deliveries with lightweight, even portable equipment, such as hand-held Rockwell hardness testers.
hardness test, invented in Sweden, was developed earlier—in 1900—but it was slow, not useful on fully hardened steel
, and left too large an impression to be considered nondestructive
.
The Rockwell hardness tester, a differential-depth machine, was co-invented by Connecticut natives Hugh M. Rockwell (1890–1957) and Stanley P. Rockwell (1886–1940). A patent was applied for on July 15, 1914. The requirement for this tester was to quickly determine the effects of heat treatment on steel bearing races. The application was subsequently approved on February 11, 1919, and holds patent number #1,294,171. At the time of invention, both Hugh and Stanley Rockwell (not direct relations) worked for the New Departure Manufacturing Co. of Bristol, CT. New Departure was a major ball bearing manufacturer that, in 1916, became part of United Motors and, shortly thereafter, General Motors Corp.
After leaving the Connecticut company, Stanley Rockwell, then in Syracuse, NY, applied for an improvement to the original invention on September 11, 1919, which was approved on November 18, 1924. The new tester holds patent #1,516,207. Rockwell moved to West Hartford, CT, and made an additional improvement in 1921. Stanley collaborated with instrument manufacturer Charles H. Wilson of the Wilson-Mauelen Company in 1920 to commercialize his invention and develop standardized testing machines. Stanley started a heat-treating firm circa 1923, the Stanley P. Rockwell Company, which still exists in Hartford, CT. The later-named Wilson Mechanical Instrument Company has changed ownership over the years, and was most recently acquired by Instron
Corp. in 1993.
It is typically used in engineering
and metallurgy
. Its commercial popularity arises from its speed, reliability, robustness, resolution and small area of indentation.
In order to get a reliable reading the thickness of the test-piece should be at least 10 times the depth of the indentation. Also, readings should be taken from a flat perpendicular surface, because convex surfaces give lower readings. A correction factor can be used if the hardness of a convex surface must be measured.
The superficial Rockwell scales use lower loads and shallower impressions on brittle and very thin materials. The 45N scale employs a 45-kgf load on a diamond cone-shaped Brale indenter, and can be used on dense ceramic
s. The 15T scale employs a 15-kgf load on a 1/16 in hardened steel ball, and can be used on sheet metal
.
Readings below HRC 20 are generally considered unreliable, as are readings much above HRB 100.
Several other scales, including the extensive A-scale, are used for specialized applications. There are special scales for measuring case-hardened
specimens.
Indentation hardness
Indentation hardness tests are used to determine the hardness of a material to deformation. Several such tests exist, wherein the examined material is indented until an impression is formed; these tests can be performed on a macroscopic or microscopic scale....
of a material. The Rockwell test determines the hardness by measuring the depth of penetration of an indenter under a large load compared to the penetration made by a preload. There are different scales, denoted by a single letter, that use different loads or indenters. The result is a dimensionless number noted as HRX, where X is the scale letter.
When testing metals, indentation hardness correlates linearly with tensile strength
Tensile strength
Ultimate tensile strength , often shortened to tensile strength or ultimate strength, is the maximum stress that a material can withstand while being stretched or pulled before necking, which is when the specimen's cross-section starts to significantly contract...
. This important relation permits economically important nondestructive testing of bulk metal deliveries with lightweight, even portable equipment, such as hand-held Rockwell hardness testers.
History
The differential depth hardness measurement was conceived in 1908 by a Viennese professor Paul Ludwik in his book Die Kegelprobe (crudely, "the cone trial"). The differential-depth method subtracted out the errors associated with the mechanical imperfections of the system, such as backlash and surface imperfections. The BrinellBrinell scale
The Brinell scale characterizes the indentation hardness of materials through the scale of penetration of an indenter, loaded on a material test-piece. It is one of several definitions of hardness in materials science....
hardness test, invented in Sweden, was developed earlier—in 1900—but it was slow, not useful on fully hardened steel
Hardened steel
The term hardened steel is often used for a medium or high carbon steel that has been given the heat treatments of quenching followed by tempering. The quenching results in the formation of metastable martensite, the fraction of which is reduced to the desired amount during tempering. This is the...
, and left too large an impression to be considered nondestructive
Nondestructive testing
Nondestructive testing or Non-destructive testing is a wide group of analysis techniques used in science and industry to evaluate the properties of a material, component or system without causing damage....
.
The Rockwell hardness tester, a differential-depth machine, was co-invented by Connecticut natives Hugh M. Rockwell (1890–1957) and Stanley P. Rockwell (1886–1940). A patent was applied for on July 15, 1914. The requirement for this tester was to quickly determine the effects of heat treatment on steel bearing races. The application was subsequently approved on February 11, 1919, and holds patent number #1,294,171. At the time of invention, both Hugh and Stanley Rockwell (not direct relations) worked for the New Departure Manufacturing Co. of Bristol, CT. New Departure was a major ball bearing manufacturer that, in 1916, became part of United Motors and, shortly thereafter, General Motors Corp.
After leaving the Connecticut company, Stanley Rockwell, then in Syracuse, NY, applied for an improvement to the original invention on September 11, 1919, which was approved on November 18, 1924. The new tester holds patent #1,516,207. Rockwell moved to West Hartford, CT, and made an additional improvement in 1921. Stanley collaborated with instrument manufacturer Charles H. Wilson of the Wilson-Mauelen Company in 1920 to commercialize his invention and develop standardized testing machines. Stanley started a heat-treating firm circa 1923, the Stanley P. Rockwell Company, which still exists in Hartford, CT. The later-named Wilson Mechanical Instrument Company has changed ownership over the years, and was most recently acquired by Instron
Instron
Instron is a manufacturer of test equipment designed to evaluate the mechanical properties of materials and components.In 1946, Harold Hindman and George Burr, who worked together at Massachusetts Institute of Technology , teamed up to determine the properties of new materials to be used in...
Corp. in 1993.
Operation
The determination of the Rockwell hardness of a material involves the application of a minor load followed by a major load, and then noting the depth of penetration, vis a vis, hardness value directly from a dial, in which a harder material gives a higher number. The chief advantage of Rockwell hardness is its ability to display hardness values directly, thus obviating tedious calculations involved in other hardness measurement techniques.It is typically used in engineering
Engineering
Engineering is the discipline, art, skill and profession of acquiring and applying scientific, mathematical, economic, social, and practical knowledge, in order to design and build structures, machines, devices, systems, materials and processes that safely realize improvements to the lives of...
and metallurgy
Metallurgy
Metallurgy is a domain of materials science that studies the physical and chemical behavior of metallic elements, their intermetallic compounds, and their mixtures, which are called alloys. It is also the technology of metals: the way in which science is applied to their practical use...
. Its commercial popularity arises from its speed, reliability, robustness, resolution and small area of indentation.
In order to get a reliable reading the thickness of the test-piece should be at least 10 times the depth of the indentation. Also, readings should be taken from a flat perpendicular surface, because convex surfaces give lower readings. A correction factor can be used if the hardness of a convex surface must be measured.
Scales and values
There are several alternative scales, the most commonly used being the "B" and "C" scales. Both express hardness as an arbitrary dimensionless number.Scale | Abbreviation | Load | Indenter | Use |
---|---|---|---|---|
A | HRA | 60 kgf Kilogram-force A kilogram-force , or kilopond , is a gravitational metric unit of force. It is equal to the magnitude of the force exerted by one kilogram of mass in a gravitational field... |
120° diamond cone† | Tungsten carbide Tungsten carbide Tungsten carbide is an inorganic chemical compound containing equal parts of tungsten and carbon atoms. Colloquially, tungsten carbide is often simply called carbide. In its most basic form, it is a fine gray powder, but it can be pressed and formed into shapes for use in industrial machinery,... |
B | HRB | 100 kgf | 1/16 in steel sphere | Aluminium, brass, and soft steels |
C | HRC | 150 kgf | 120° diamond cone | Harder steels |
D | HRD | 100 kgf | 120° diamond cone | |
E | HRE | 100 kgf | 1/8 in steel sphere | |
F | HRF | 60 kgf | 1/16 in steel sphere | |
G | HRG | 150 kgf | 1/16 in steel sphere | |
†Also called a brale indenter |
- Except for one very limited exception, the steel indenter balls have been replaced by tungsten carbide balls of the varying diameters. Scales using the ball indenter have a "W" suffix added to the scale name to indicate usage of the carbide ball, for example "HR30T" is now "HR30TW".
The superficial Rockwell scales use lower loads and shallower impressions on brittle and very thin materials. The 45N scale employs a 45-kgf load on a diamond cone-shaped Brale indenter, and can be used on dense ceramic
Ceramic
A ceramic is an inorganic, nonmetallic solid prepared by the action of heat and subsequent cooling. Ceramic materials may have a crystalline or partly crystalline structure, or may be amorphous...
s. The 15T scale employs a 15-kgf load on a 1/16 in hardened steel ball, and can be used on sheet metal
Sheet metal
Sheet metal is simply metal formed into thin and flat pieces. It is one of the fundamental forms used in metalworking, and can be cut and bent into a variety of different shapes. Countless everyday objects are constructed of the material...
.
Readings below HRC 20 are generally considered unreliable, as are readings much above HRB 100.
Typical values
- Very hard steel (e.g. a higher quality knife blade): HRC 55–66 ( Hardened High Speed Carbon and Tool Steels such as M2, W2, O1, and D2, as well as many of the newer powder metallurgy Stainless Steels such as S30V, 154CM, CPM-M4, ZDP-189 , etc. )
- Axes, chisels, etc.: HRC 40–45 (about 1045 carbon steel)
- Brass: HRB 55 (Low brass, UNS C24000, H01 Temper) to HRB 93 (Cartridge Brass, UNS C26000 (260 Brass), H10 Temper)
Several other scales, including the extensive A-scale, are used for specialized applications. There are special scales for measuring case-hardened
Case hardening
Case hardening or surface hardening is the process of hardening the surface of a metal, often a low carbon steel, by infusing elements into the material's surface, forming a thin layer of a harder alloy...
specimens.
Standards
- International (ISOInternational Organization for StandardizationThe International Organization for Standardization , widely known as ISO, is an international standard-setting body composed of representatives from various national standards organizations. Founded on February 23, 1947, the organization promulgates worldwide proprietary, industrial and commercial...
) - ISO 6508-1: Metallic materials -- Rockwell hardness test -- Part 1: Test method (scales A, B, C, D, E, F, G, H, K, N, T)
- ISO 2039-2: Plastics -- Determination of hardness -- Part 2: Rockwell hardness
- US standard (ASTM InternationalASTM InternationalASTM International, known until 2001 as the American Society for Testing and Materials , is an international standards organization that develops and publishes voluntary consensus technical standards for a wide range of materials, products, systems, and services...
) - ASTM E18 : Standard methods for Rockwell hardness and Rockwell superficial hardness of metallic materials
See also
- Brinell hardness test
- Hardness comparisonHardness comparisonThere are a large number of hardness testing methods available . Although it is impossible in many cases to give an exact conversion, it is possible to give an approximate material-specific comparison table e.g...
- Holger F. StruerHolger F. StruerHolger F. Struer was a Danish chemist and founder of "H. Struers Chemiske Laboratorium" in 1875 at Skindergade 38, the centre of Copenhagen...
- Knoop hardness testKnoop hardness testThe Knoop hardness test is a microhardness test - a test for mechanical hardness used particularly for very brittle materials or thin sheets, where only a small indentation may be made for testing purposes...
- Leeb Rebound Hardness TestLeeb rebound hardness testThe Leeb rebound hardness test is one of the four most used method for testing metal hardness. This portable method is mainly used for testing sufficiently large workpieces .-History:...
- Meyer hardness testMeyer hardness testThe Meyer hardness test is a rarely used hardness test based upon projected area of an impression. This is a more fundamental measurement of hardness than other hardness tests which are based on the surface area of an indentation. The principle behind the test is that the mean pressure required to...
- Shore durometerShore durometerDurometer is one of several measures of the hardness of a material. Hardness may be defined as a material's resistance to permanent indentation. The durometer scale was defined by Albert F. Shore, who developed a measurement device called a durometer in the 1920s. The term durometer is often used...
- Vickers hardness testVickers hardness testThe Vickers hardness test was developed in 1924 by Smith and Sandland at Vickers Ltd as an alternative to the Brinell method to measure the hardness of materials. The Vickers test is often easier to use than other hardness tests since the required calculations are independent of the size of the...