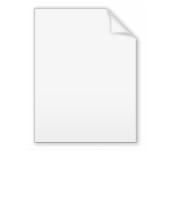
Indentation hardness
Encyclopedia
Indentation hardness tests are used to determine the hardness of a material to deformation. Several such tests exist, wherein the examined material is indented until an impression is formed; these tests can be performed on a macroscopic or microscopic scale.
When testing metals, indentation hardness correlates linearly with tensile strength. This important relation permits economically important nondestructive testing of bulk metal deliveries with lightweight, even portable equipment, such as hand-held Rockwell hardness testers.
continues towards studying the basis of properties on smaller and smaller scales, different techniques are used to quantify material characteristics and tendencies. Measuring mechanical properties for materials on smaller scales, like thin films, can not be done using conventional uniaxial tensile
testing. As a result, techniques testing material "hardness" by indenting a material with an impression have been developed to determine such properties.
Hardness measurements quantify the resistance of a material to plastic deformation. Indentation hardness tests compose the majority of processes used to determine material hardness, and can be divided into two classes: microindentation and macroindentation tests. Microindentation tests typically have forces less than 2 N. Hardness, however, cannot be considered to be a fundamental material property. Instead, it represents an arbitrary quantity used to provide a relative idea of material properties. As such, hardness can only offer a comparative idea of the material's resistance to plastic deformation since different hardness techniques have different scales.
The main source of error with indentation tests is the strain hardening effect of the process. However, it has been experimentally determined through "strainless hardness tests" that the effect is minimal with smaller indentations.
Surface finish of the part and the indenter do not have an effect on the hardness measurement, as long as the indentation is large compared to the surface roughness. This proves to be useful when measuring the hardness of practical surfaces. It also is helpful when leaving a shallow indentation, because a finely etched indenter leaves a much easier to read indentation than a smooth indenter.
The indentation that is left after the indenter and load are removed is known to "recover", or spring back slightly. This effect is properly known as shallowing. For spherical indenters the indentation is known to stay symmetrical and spherical, but with a larger radius. For very hard materials the radius can be three times as large as the indenter's radius. This effect is attributed to the release of elastic stresses. Because of this effect the diameter and depth of the indentation do contain errors. The error from the change in diameter is known to be only a few percent, with the error for the depth being greater.
Another effect the load has on the indentation is the piling-up or sinking-in of the surrounding material. If the metal is work hardened it has a tendency to pile up and form a "crater". If the metal is annealed it will sink in around the indentation. Both of these effects add to the error of the hardness measurement.
The equation based definition of hardness is the pressure applied over the contact area between the indenter and the material being tested. As a result hardness values are typically reported in units of pressure, although this is only a "true" pressure if the indenter and surface interface is perfectly flat.
or more. There are various macroindentation tests, including:
There is, in general, no simple relationship between the results of different hardness tests. Though there are practical conversion tables
for hard steels, for example, some materials show qualitatively different behaviors under the various measurement methods. The Vickers and Brinell hardness scales correlate well over a wide range, however, with Brinell only producing overestimated values at high loads.
In microindentation testing, the hardness number is based on measurements made of the indent formed in the surface of the test specimen. The hardness number is based on the surface area of the indent itself divided by the applied force, giving hardness units in kgf/mm². Microindentation hardness testing can be done using Vickers as well as Knoop indenters. For the Vickers test, both the diagonals are measured and the average value is used to compute the Vickers pyramid number. In the Knoop test, only the longer diagonal is measured, and the Knoop hardness is calculated based on the projected area of the indent divided by the applied force, also giving test units in kgf/mm².
The Vickers microindentation test is carried out in a similar manner to the Vickers macroindentation tests, using the same pyramid. The Knoop test uses an elongated pyramid to indent material samples. This elongated pyramid creates a shallow impression, which is beneficial for measuring the hardness of brittle materials or thin components. Both the Knoop and Vickers indenters require prepolishing of the surface to achieve accurate results.
Scratch tests at low loads, such as the Bierbaum microcharacter test, performed with either 3 gf or 9 gf loads, preceded the development of microhardness testers using traditional indenters. In 1925, Smith and Sandland of the UK developed an indentation test that employed a square-based pyramidal indenter made from diamond. They chose the pyramidal shape with an angle of 136° between opposite faces in order to obtain hardness numbers that would be as close as possible to Brinell hardness numbers for the specimen. The Vickers test has a great advantage of using one hardness scale to test all materials.The first reference to the Vickers indenter with low loads was made in the annual report of the National Physical Laboratory
in 1932. Lips and Sack describes the first Vickers tester using low loads in 1936.
There is some disagreement in the literature regarding the load range applicable to microhardness testing. ASTM Specification E384, for example, states that the load range for microhardness testing is 1 to 1000 gf. For loads of 1 kgf and below, the Vickers hardness (HV) is calculated with an equation, wherein load (L) is in grams force and the mean of two diagonals (d) is in millimeters:

For any given load, the hardness increases rapidly at low diagonal lengths, with the effect becoming more pronounced as the load decreases. Thus at low loads, small measurement errors will produce large hardness deviations. Thus one should always use the highest possible load in any test. Also, in the vertical portion of the curves, small measurement errors will produce large hardness deviations.
When testing metals, indentation hardness correlates linearly with tensile strength. This important relation permits economically important nondestructive testing of bulk metal deliveries with lightweight, even portable equipment, such as hand-held Rockwell hardness testers.
Material hardness
As the direction of materials scienceMaterials science
Materials science is an interdisciplinary field applying the properties of matter to various areas of science and engineering. This scientific field investigates the relationship between the structure of materials at atomic or molecular scales and their macroscopic properties. It incorporates...
continues towards studying the basis of properties on smaller and smaller scales, different techniques are used to quantify material characteristics and tendencies. Measuring mechanical properties for materials on smaller scales, like thin films, can not be done using conventional uniaxial tensile
Tensile strength
Ultimate tensile strength , often shortened to tensile strength or ultimate strength, is the maximum stress that a material can withstand while being stretched or pulled before necking, which is when the specimen's cross-section starts to significantly contract...
testing. As a result, techniques testing material "hardness" by indenting a material with an impression have been developed to determine such properties.
Hardness measurements quantify the resistance of a material to plastic deformation. Indentation hardness tests compose the majority of processes used to determine material hardness, and can be divided into two classes: microindentation and macroindentation tests. Microindentation tests typically have forces less than 2 N. Hardness, however, cannot be considered to be a fundamental material property. Instead, it represents an arbitrary quantity used to provide a relative idea of material properties. As such, hardness can only offer a comparative idea of the material's resistance to plastic deformation since different hardness techniques have different scales.
The main source of error with indentation tests is the strain hardening effect of the process. However, it has been experimentally determined through "strainless hardness tests" that the effect is minimal with smaller indentations.
Surface finish of the part and the indenter do not have an effect on the hardness measurement, as long as the indentation is large compared to the surface roughness. This proves to be useful when measuring the hardness of practical surfaces. It also is helpful when leaving a shallow indentation, because a finely etched indenter leaves a much easier to read indentation than a smooth indenter.
The indentation that is left after the indenter and load are removed is known to "recover", or spring back slightly. This effect is properly known as shallowing. For spherical indenters the indentation is known to stay symmetrical and spherical, but with a larger radius. For very hard materials the radius can be three times as large as the indenter's radius. This effect is attributed to the release of elastic stresses. Because of this effect the diameter and depth of the indentation do contain errors. The error from the change in diameter is known to be only a few percent, with the error for the depth being greater.
Another effect the load has on the indentation is the piling-up or sinking-in of the surrounding material. If the metal is work hardened it has a tendency to pile up and form a "crater". If the metal is annealed it will sink in around the indentation. Both of these effects add to the error of the hardness measurement.
The equation based definition of hardness is the pressure applied over the contact area between the indenter and the material being tested. As a result hardness values are typically reported in units of pressure, although this is only a "true" pressure if the indenter and surface interface is perfectly flat.
Macroindentation tests
The term "macroindentation" is applied to tests with a larger test load, such as 1 kgfKGF
KGF may refer to:*Keratinocyte Growth Factor*King George's Fields A UK set of 471 memorial playing fields and recreation grounds*Kolar Gold Fields*The IATA code for Sary-Arka Airport, Karaganda, Kazakhstan...
or more. There are various macroindentation tests, including:
- Vickers hardness testVickers hardness testThe Vickers hardness test was developed in 1924 by Smith and Sandland at Vickers Ltd as an alternative to the Brinell method to measure the hardness of materials. The Vickers test is often easier to use than other hardness tests since the required calculations are independent of the size of the...
(HV), which has one of the widest scales - Brinell hardness test (HB)
- Knoop hardness testKnoop hardness testThe Knoop hardness test is a microhardness test - a test for mechanical hardness used particularly for very brittle materials or thin sheets, where only a small indentation may be made for testing purposes...
(HK), for measurement over small areas - Janka hardness test, for wood
- Meyer hardness testMeyer hardness testThe Meyer hardness test is a rarely used hardness test based upon projected area of an impression. This is a more fundamental measurement of hardness than other hardness tests which are based on the surface area of an indentation. The principle behind the test is that the mean pressure required to...
- Rockwell hardness testRockwell scaleThe Rockwell scale is a hardness scale based on the indentation hardness of a material. The Rockwell test determines the hardness by measuring the depth of penetration of an indenter under a large load compared to the penetration made by a preload. There are different scales, denoted by a single...
(HR), principally used in the USA - Shore hardness testShore durometerDurometer is one of several measures of the hardness of a material. Hardness may be defined as a material's resistance to permanent indentation. The durometer scale was defined by Albert F. Shore, who developed a measurement device called a durometer in the 1920s. The term durometer is often used...
, for polymers - Barcol hardness testBarcol hardness testThe Barcol hardness test characterizes the indentation hardness of materials through the depth of penetration of an indentor, loaded on a material sample and compared to the penetration in a reference material. The method is most often used for composite materials such as reinforced thermosetting...
, for composite materials.
There is, in general, no simple relationship between the results of different hardness tests. Though there are practical conversion tables
Hardness comparison
There are a large number of hardness testing methods available . Although it is impossible in many cases to give an exact conversion, it is possible to give an approximate material-specific comparison table e.g...
for hard steels, for example, some materials show qualitatively different behaviors under the various measurement methods. The Vickers and Brinell hardness scales correlate well over a wide range, however, with Brinell only producing overestimated values at high loads.
Microindentation tests
The term "microhardness" has been widely employed in the literature to describe the hardness testing of materials with low applied loads. A more precise term is "microindentation hardness testing." In microindentation hardness testing, a diamond indenter of specific geometry is impressed into the surface of the test specimen using a known applied force (commonly called a "load" or "test load") of 1 to 1000 gf. Microindentation tests typically have forces of 2 N (roughly 200 gf) and produce indentations of about 50 μm. Due to their specificity, microhardness testing can be used to observe changes in hardness on the microscopic scale. Unfortunately, it is difficult to standardize microhardness measurements; it has been found that the microhardness of almost any material is higher than its macrohardness. Additionally, microhardness values vary with load and work-hardening effects of materials. The two most commonly used microhardness tests are tests that also can be applied with heavier loads as macroindentation tests:- Vickers hardness testVickers hardness testThe Vickers hardness test was developed in 1924 by Smith and Sandland at Vickers Ltd as an alternative to the Brinell method to measure the hardness of materials. The Vickers test is often easier to use than other hardness tests since the required calculations are independent of the size of the...
(HV) - Knoop hardness testKnoop hardness testThe Knoop hardness test is a microhardness test - a test for mechanical hardness used particularly for very brittle materials or thin sheets, where only a small indentation may be made for testing purposes...
(HK)
In microindentation testing, the hardness number is based on measurements made of the indent formed in the surface of the test specimen. The hardness number is based on the surface area of the indent itself divided by the applied force, giving hardness units in kgf/mm². Microindentation hardness testing can be done using Vickers as well as Knoop indenters. For the Vickers test, both the diagonals are measured and the average value is used to compute the Vickers pyramid number. In the Knoop test, only the longer diagonal is measured, and the Knoop hardness is calculated based on the projected area of the indent divided by the applied force, also giving test units in kgf/mm².
The Vickers microindentation test is carried out in a similar manner to the Vickers macroindentation tests, using the same pyramid. The Knoop test uses an elongated pyramid to indent material samples. This elongated pyramid creates a shallow impression, which is beneficial for measuring the hardness of brittle materials or thin components. Both the Knoop and Vickers indenters require prepolishing of the surface to achieve accurate results.
Scratch tests at low loads, such as the Bierbaum microcharacter test, performed with either 3 gf or 9 gf loads, preceded the development of microhardness testers using traditional indenters. In 1925, Smith and Sandland of the UK developed an indentation test that employed a square-based pyramidal indenter made from diamond. They chose the pyramidal shape with an angle of 136° between opposite faces in order to obtain hardness numbers that would be as close as possible to Brinell hardness numbers for the specimen. The Vickers test has a great advantage of using one hardness scale to test all materials.The first reference to the Vickers indenter with low loads was made in the annual report of the National Physical Laboratory
National Physical Laboratory, UK
The National Physical Laboratory is the national measurement standards laboratory for the United Kingdom, based at Bushy Park in Teddington, London, England. It is the largest applied physics organisation in the UK.-Description:...
in 1932. Lips and Sack describes the first Vickers tester using low loads in 1936.
There is some disagreement in the literature regarding the load range applicable to microhardness testing. ASTM Specification E384, for example, states that the load range for microhardness testing is 1 to 1000 gf. For loads of 1 kgf and below, the Vickers hardness (HV) is calculated with an equation, wherein load (L) is in grams force and the mean of two diagonals (d) is in millimeters:

For any given load, the hardness increases rapidly at low diagonal lengths, with the effect becoming more pronounced as the load decreases. Thus at low loads, small measurement errors will produce large hardness deviations. Thus one should always use the highest possible load in any test. Also, in the vertical portion of the curves, small measurement errors will produce large hardness deviations.