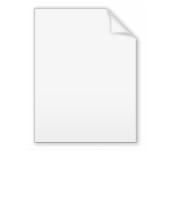
Sheet metal
Overview
Metal
A metal , is an element, compound, or alloy that is a good conductor of both electricity and heat. Metals are usually malleable and shiny, that is they reflect most of incident light...
formed into thin and flat pieces. It is one of the fundamental forms used in metalworking
Metalworking
Metalworking is the process of working with metals to create individual parts, assemblies, or large scale structures. The term covers a wide range of work from large ships and bridges to precise engine parts and delicate jewelry. It therefore includes a correspondingly wide range of skills,...
, and can be cut and bent into a variety of different shapes. Countless everyday objects are constructed of the material. Thicknesses can vary significantly, although extremely thin thicknesses are considered foil
Foil
Foil may refer to:Materials* Foil , a quite thin sheet of metal, usually manufactured with a rolling mill machine* Metal leaf, a very thin sheet of decorative metal* Aluminium foil, a type of wrapping for food...
or leaf
Metal leaf
Metal leaf, also called composition leaf or schlagmetal, is a thin foil used for decoration. Metal leaf can come in many different shades. Some metal leaf may look like gold leaf but not contain any real gold...
, and pieces thicker than 6 mm (0.25 in) are considered plate
Structural steel
Structural steel is steel construction material, a profile, formed with a specific shape or cross section and certain standards of chemical composition and mechanical properties...
.
Sheet metal is available in flat pieces or as a coiled strip.