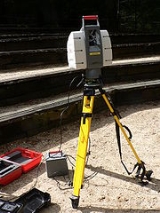
3D scanner
Encyclopedia
A 3D scanner is a device that analyzes a real-world object or environment to collect data on its shape and possibly its appearance (i.e. color). The collected data can then be used to construct digital, three dimensional models.
Many different technologies can be used to build these 3D scanning devices; each technology comes with its own limitations, advantages and costs. Many limitations in the kind of objects that can be digitized are still present: for example optical technologies encounter many difficulties with shiny, mirroring or transparent objects.
Collected 3D data is useful for a wide variety of applications. These devices are used extensively by the entertainment industry in the production of movies and video games. Other common applications of this technology include industrial design
, orthotics
and prosthetics, reverse engineering
and prototyping, quality control
/inspection and documentation of cultural artifacts.
of geometric samples on the surface of the subject. These points can then be used to extrapolate the shape of the subject (a process called reconstruction
). If color information is collected at each point, then the colors on the surface of the subject can also be determined.
3D scanners are very analogous to cameras. Like cameras, they have a cone-like field of view
, and like cameras, they can only collect information about surfaces that are not obscured. While a camera collects color information about surfaces within its field of view, a 3D scanner collects distance information about surfaces within its field of view. The "picture" produced by a 3D scanner describes the distance to a surface at each point in the picture. This allows the three dimensional position of each point in the picture to be identified.
For most situations, a single scan will not produce a complete model of the subject. Multiple scans, even hundreds, from many different directions are usually required to obtain information about all sides of the subject. These scans have to be brought in a common reference system
, a process that is usually called alignment or registration
, and then merged to create a complete model. This whole process, going from the single range map to the whole model, is usually known as the 3D scanning pipeline.
surface plate
, ground and polished to a specific maximum of surface roughness. Where the object to be scanned is not flat or can not rest stably on a flat surface, it is supported and held firmly in place by a fixture
.
The scanner mechanism may have three different forms:
A CMM (coordinate measuring machine) is an example of a contact 3D scanner. It is used mostly in manufacturing and can be very precise. The disadvantage of CMMs though, is that it requires contact with the object being scanned. Thus, the act of scanning the object might modify or damage it. This fact is very significant when scanning delicate or valuable objects such as historical artifacts. The other disadvantage of CMMs is that they are relatively slow compared to the other scanning methods. Physically moving the arm that the probe is mounted on can be very slow and the fastest CMMs can only operate on a few hundred hertz. In contrast, an optical system like a laser scanner can operate from 10 to 500 kHz.
Other examples are the hand driven touch probes used to digitize clay models in computer animation industry.
or x-ray.
The time-of-flight 3D laser scanner is an active scanner that uses laser light to probe the subject. At the heart of this type of scanner is a time-of-flight laser rangefinder. The laser rangefinder finds the distance of a surface by timing the round-trip time of a pulse of light. A laser is used to emit a pulse of light and the amount of time before the reflected light is seen by a detector is timed. Since the speed of light
is known, the round-trip time determines the travel distance of the light, which is twice the distance between the scanner and the surface. If
is the round-trip time, then distance is equal to
. The accuracy of a time-of-flight 3D laser scanner depends on how precisely we can measure the
time: 3.3 picosecond
s (approx.) is the time taken for light to travel 1 millimeter.
The laser rangefinder only detects the distance of one point in its direction of view. Thus, the scanner scans its entire field of view one point at a time by changing the range finder's direction of view to scan different points. The view direction of the laser rangefinder can be changed either by rotating the range finder itself, or by using a system of rotating mirrors. The latter method is commonly used because mirrors are much lighter and can thus be rotated much faster and with greater accuracy. Typical time-of-flight 3D laser scanners can measure the distance of 10,000~100,000 points every second.
Time-of-flight devices are also available in a 2D configuration. This is referred to as a Time-of-flight camera
.
The triangulation 3D laser scanners are also active scanner that use laser light to probe the environment. With respect to time-of-flight 3D laser scanner the triangulation laser shines a laser on the subject and exploits a camera to look for the location of the laser dot. Depending on how far away the laser strikes a surface, the laser dot appears at different places in the camera's field of view. This technique is called triangulation because the laser dot, the camera and the laser emitter form a triangle. The length of one side of the triangle, the distance between the camera and the laser emitter is known. The angle of the laser emitter corner is also known. The angle of the camera corner can be determined by looking at the location of the laser dot in the camera's field of view. These three pieces of information fully determine the shape and size of the triangle and gives the location of the laser dot corner of the triangle. In most cases a laser stripe, instead of a single laser dot, is swept across the object to speed up the acquisition process. The National Research Council of Canada
was among the first institutes to develop the triangulation based laser scanning technology in 1978.
Time of flight scanners accuracy can be lost when the laser hits the edge of an object because the information that is sent back to the scanner is from two different locations for one laser pulse. The coordinate relative to the scanners position for a point that has hit the edge of an object will be calculated based on an average and therefore will put the point in the wrong place. When using a high resolution scan on an object the chances of the beam hitting an edge are increased and the resulting data will show noise just behind the edges of the object. Scanners with a smaller beam width will help to solve this problem but will be limited by range as the beam width will increase over distance. Software can also help by determining that the first object to be hit by the laser beam should cancel out the second.
At a rate of 10,000 sample points per second, low resolution scans can take less than a second, but high resolution scans, requiring millions of samples, can take minutes for some time-of-flight scanners. The problem this creates is distortion from motion. Since each point is sampled at a different time, any motion in the subject or the scanner will distort the collected data. Thus, it is usually necessary to mount both the subject and the scanner on stable platforms and minimize vibration. Using these scanners to scan objects in motion is very difficult.
Recently, there has been research on compensating for distortion from small amounts of vibration.
When scanning in one position for any length of time slight movement can occur in the scanner position due to changes in temperature. If the scanner is set on a tripod and there is strong sunlight on one side of the scanner then that side of the tripod will expand and slowly distort the scan data from one side to another. Some laser scanners have level compensators built into them to counteract any movement of the scanner during the scan process.
system, a laser beam is projected onto the surface and then the immediate reflection along the same ray-path are put through a conoscopic crystal and projected onto a CCD. The result is a diffraction pattern, that can be frequency analyzed
to determine the distance to the measured surface. The main advantage with Conoscopic Holography is that only a single ray-path is needed for measuring, thus giving an opportunity to measure for instance the depth of a finely drilled hole.
or position sensitive device
) measures the distance to the surface. Data is collected in relation to an internal coordinate system and therefore to collect data where the scanner is in motion the position of the scanner must be determined. The position can be determined by the scanner using reference features on the surface being scanned (typically adhesive reflective tabs) or by using an external tracking method. External tracking often takes the form of a laser tracker (to provide the sensor position) with integrated camera (to determine the orientation of the scanner) or a photogrammetric solution using 3 or more cameras providing the complete Six degrees of freedom
of the scanner. Both techniques tend to use infrared
Light-emitting diode
s attached to the scanner which are seen by the camera(s) through filters providing resilience to ambient lighting.
Data is collected by a computer and recorded as data points within Three-dimensional space
, with processing this can be converted into a triangulated mesh and then a Computer-aided design
model, often as Nonuniform rational B-spline
surfaces. Hand-held laser scanners can combine this data with passive, visible-light sensors—which capture surface textures and colors—to build (or "reverse engineer") a full 3D model.
or a sweeping laser. A camera, offset slightly from the pattern projector, looks at the shape of the line and uses a technique similar to triangulation to calculate the distance of every point on the line. In the case of a single-line pattern, the line is swept across the field of view to gather distance information one strip at a time.
An example of a two-dimensional pattern is a grid or a line stripe pattern. A camera is used to look at the deformation of the pattern, and an algorithm is used to calculate the distance at each point in the pattern. Consider an array of parallel vertical laser stripes sweeping horizontally across a target. In the simplest case, one could analyze an image and assume that the left-to-right sequence of stripes reflects the sequence of the lasers in the array, so that the leftmost image stripe is the first laser, the next one is the second laser, and so on. In non-trivial targets having holes, occlusions, and rapid depth changes, however, this sequencing breaks down as stripes are often hidden and may even appear to change order, resulting in laser stripe ambiguity. This problem can be solved using algorithms for multistripe laser triangulation. Structured-light scanning is still a very active area of research with many research papers published each year.
The advantage of structured-light 3D scanners is speed. Instead of scanning one point at a time, structured light scanners scan multiple points or the entire field of view at once. This reduces or eliminates the problem of distortion from motion. Some existing systems are capable of scanning moving objects in real-time.
A real-time scanner a using digital fringe projection and phase-shifting technique (a various structured light method) was developed, to capture, reconstruct, and render high-density details of dynamically deformable objects (such as facial expressions) at 40 frames per second. Recently, another scanner is developed. Different patterns can be applied to this system. The frame rate for capturing and data processing achieves 120 frames per second. It can also scan isolated surfaces, for example two moving hands.
Computed tomography
(CT) is a medical imaging method which generates a three-dimensional image of the inside of an object from a large series of two-dimensional X-ray images, similarly Magnetic resonance imaging
is another a medical imaging technique that provides much greater contrast between the different soft tissues of the body than computed tomography (CT) does, making it especially useful in neurological (brain), musculoskeletal, cardiovascular, and oncological (cancer) imaging. These techniques produce a discrete 3D volumetric representation
that can be directly visualized
, manipulated or converted to traditional 3D surface by mean of isosurface extraction algorithms
.
Although most common in medicine, Computed tomography, Microtomography
and MRI are also used in other fields for acquiring a digital representation of an object and its interior, such as nondestructive materials testing, reverse engineering
, or the study biological and paleontological specimens.
.
This sort of 3D scanning is based on the principles of photogrammetry
. It is also somewhat similar in methodology to panoramic photography
, except that the photos are taken of one object on a three-dimensional space in order to replicate it instead of taking a series of photos from one point in a three-dimensional space in order to replicate the surrounding environment.
Most applications, however, use instead polygonal 3D models, NURBS surface models, or editable feature-based CAD models (aka Solid models).
These CAD models describe not simply the envelope or shape of the object, but CAD models also embody the "design intent" (i.e., critical features and their relationship to other features). An example of design intent not evident in the shape alone might be a brake drum's lug bolts, which must be concentric with the hole in the center of the drum. This knowledge would drive the sequence and method of creating the CAD model; a designer with an awareness of this relationship would not design the lug bolts referenced to the outside diameter, but instead, to the center. A modeler creating a CAD model will want to include both Shape and design intent in the complete CAD model.
Vendors offer different approaches to getting to the parametric CAD model. Some export the NURBS surfaces and leave it to the CAD designer to complete the model in CAD (e.g., Geomagic, Imageware, Rhino). Others use the scan data to create an editable and verifiable feature based model that is imported into CAD with full feature tree intact, yielding a complete, native CAD model, capturing both shape and design intent (e.g. Geomagic, Rapidform). Still other CAD applications are robust enough to manipulate limited points or polygon models within the CAD environment (e.g., Catia).
, MRI, or Micro-CT scanners do not produce point clouds but a set of 2D slices (each termed a "tomogram") which are then 'stacked together' to produce a 3D representation. There are several ways to do this depending on the output required:
describes the general method to sample or scan a surface using laser
technology. Several areas of application exist that mainly differ in the power of the lasers that are used, and in the results of the scanning process. Low laser power is used when the scanned surface doesn't have to be influenced, e.g. when it only has to be digitized. Confocal
or 3D
laser scanning are methods to get information about the scanned surface. Another low-power application are structured light projection systems that are used for solar cell flatness metrology enabling stress calculation with throughput in excess of 2000 wafers per hour.
For high laser power, the influence on a working piece depends on the power of the laser: medium power values are used for laser engraving
, where material is partially removed by the laser. With higher powers the material becomes fluid and laser welding can be realized, or if the power is high enough to remove the material completely, then laser cutting
can be performed.
of a mechanical component requires a precise digital model of the objects to be reproduced. Rather than a set of points a precise digital model can be represented by a polygon mesh
, a set of flat or curved NURBS surfaces, or ideally for mechanical components, a CAD solid model. A 3D scanner can be used to digitize free-form or gradually changing shaped components as well as prismatic geometries whereas a coordinate measuring machine is usually used only to determine simple dimensions of a highly prismatic model. These data points are then processed to create a usable digital model, usually using specialized reverse engineering software.
There have been many research projects undertaken via the scanning of historical sites and artifacts both for documentation and analysis purposes.
The combined use of 3D scanning and 3D printing
technologies allows the replication of real objects without the use of traditional plaster cast
ing techniques, that in many cases can be too invasive
for being performed on precious or delicate cultural heritage artifacts. In the side figure the gargoyle
model on the left was digitally acquired by using a 3D scanner and the produced 3D data was processed using MeshLab
. The resulting digital 3D model was used by a rapid prototyping
machine to create a real resin replica of original object.
with a group led by Marc Levoy
used a custom laser triangulation scanner built by Cyberware to scan Michelangelo's statues in Florence, notably the David
, the Prigioni and the four statues in The Medici Chapel. The scans produced a data point density of one sample per 0.25 mm, detailed enough to see Michelangelo's chisel marks. These detailed scans produced a huge amount of data (up to 32 gigabytes) and processing the data from his scans took 5 months. Approximately in the same period a research group from IBM
, led by H. Rushmeier and F. Bernardini scanned the Pietà of Florence
acquiring both geometric and color details. The digital model, result of the Stanford scanning campaign, was thoroughly used in the 2004 subsequent restoration of the statue.
3D scanning project at Uganda's historic Kasubi Tombs
, a UNESCO World Heritage Site, using a Leica HDS 4500, produced detailed architectural models of Muzibu Azaala Mpanga, the main building at the complex and tomb of the Kabaka
s (Kings) of Uganda. A fire on March 16, 2010, burned down much of the Muzibu Azaala Mpanga structure, and reconstruction work is likely to lean heavily upon the dataset produced by the 3D scan mission.
and dentistry
. It gradually supplants tedious plaster cast. CAD/CAM software are then used to design and manufacture the orthosis, prosthesis
or dental implants.
Many Chairside dental CAD/CAM systems and Dental Laboratory CAD/CAM systems use 3D Scanner technologies to capture the 3D surface of a dental preparation (either in vivo or in vitro), in order to produce a restoration digitally using CAD software and ultimately produce the final restoration using a CAM technology (such as a CNC milling machine, or 3D printer). The chairside systems are designed to facilitate the 3D scanning of a preparation in vivo and produce the restoration (such as a Crown, Onlay, Inlay or Veneer).
Within highly automated processes, the resulting geometric measures are transferred to machines that manufacture the desired objects. Due to mechanical uncertainties and abrasions, the result may differ from its digital nominal. In order to automatically capture and evaluate these deviations, the manufactured part must be digitized as well. For this purpose, 3D scanners are applied to generate point samples from the object's surface which are finally compared against the nominal data.
The process of comparing 3D data against a CAD model is referred to as CAD-Compare, and can be a useful technique for applications such as determining wear patterns on molds and tooling, determining accuracy of final build, analyzing gap and flush, or analyzing highly complex sculpted surfaces. At present, laser triangulation scanners, structured light and contact scanning are the predominant technologies employed for industrial purposes, with contact scanning remaining the slowest, but overall most accurate option.
Many different technologies can be used to build these 3D scanning devices; each technology comes with its own limitations, advantages and costs. Many limitations in the kind of objects that can be digitized are still present: for example optical technologies encounter many difficulties with shiny, mirroring or transparent objects.
Collected 3D data is useful for a wide variety of applications. These devices are used extensively by the entertainment industry in the production of movies and video games. Other common applications of this technology include industrial design
Industrial design
Industrial design is the use of a combination of applied art and applied science to improve the aesthetics, ergonomics, and usability of a product, but it may also be used to improve the product's marketability and production...
, orthotics
Orthotics
Orthotics is a specialty within the medical field concerned with the design, manufacture and application of orthoses. An orthosis is an orthopedic device that supports or corrects the function of a limb or the torso...
and prosthetics, reverse engineering
Reverse engineering
Reverse engineering is the process of discovering the technological principles of a device, object, or system through analysis of its structure, function, and operation...
and prototyping, quality control
Quality control
Quality control, or QC for short, is a process by which entities review the quality of all factors involved in production. This approach places an emphasis on three aspects:...
/inspection and documentation of cultural artifacts.
Functionality
The purpose of a 3D scanner is usually to create a point cloudPoint cloud
A point cloud is a set of vertices in a three-dimensional coordinate system. These vertices are usually defined by X, Y, and Z coordinates, and typically are intended to be representative of the external surface of an object....
of geometric samples on the surface of the subject. These points can then be used to extrapolate the shape of the subject (a process called reconstruction
3D reconstruction
See Iterative reconstruction for 3D reconstruction in Medical imaging.In computer vision and computer graphics, 3D reconstruction is the process of capturing the shape and appearance of real objects....
). If color information is collected at each point, then the colors on the surface of the subject can also be determined.
3D scanners are very analogous to cameras. Like cameras, they have a cone-like field of view
Field of view
The field of view is the extent of the observable world that is seen at any given moment....
, and like cameras, they can only collect information about surfaces that are not obscured. While a camera collects color information about surfaces within its field of view, a 3D scanner collects distance information about surfaces within its field of view. The "picture" produced by a 3D scanner describes the distance to a surface at each point in the picture. This allows the three dimensional position of each point in the picture to be identified.
For most situations, a single scan will not produce a complete model of the subject. Multiple scans, even hundreds, from many different directions are usually required to obtain information about all sides of the subject. These scans have to be brought in a common reference system
Coordinate system
In geometry, a coordinate system is a system which uses one or more numbers, or coordinates, to uniquely determine the position of a point or other geometric element. The order of the coordinates is significant and they are sometimes identified by their position in an ordered tuple and sometimes by...
, a process that is usually called alignment or registration
Image registration
Image registration is the process of transforming different sets of data into one coordinate system. Data may be multiple photographs, data from different sensors, from different times, or from different viewpoints. It is used in computer vision, medical imaging, military automatic target...
, and then merged to create a complete model. This whole process, going from the single range map to the whole model, is usually known as the 3D scanning pipeline.
Technology
There are a variety of technologies for digitally acquiring the shape of a 3D object. A well established classification divides them into two types: contact and non-contact 3D scanners. Non-contact 3D scanners can be further divided into two main categories, active scanners and passive scanners. There are a variety of technologies that fall under each of these categories.Contact
Contact 3D scanners probe the subject through physical touch, while the object is in contact with or resting on a precision flatFlatness (manufacturing)
In manufacturing and mechanical engineering, flatness is an important geometric condition for workpieces and tools.In the manufacture of precision parts and assemblies, especially where parts will be required to be connected across a surface area in an air-tight or liquid-tight manner, flatness is...
surface plate
Surface plate
A surface plate is a solid, flat plate used as the main horizontal reference plane for precision inspection, marking out , and tooling setup. The surface plate is often used as the baseline for all measurements to the workpiece, therefore one primary surface is finished extremely flat with...
, ground and polished to a specific maximum of surface roughness. Where the object to be scanned is not flat or can not rest stably on a flat surface, it is supported and held firmly in place by a fixture
Fixture (tool)
A fixture is a work-holding or support device used in the manufacturing industry. What makes a fixture unique is that each one is built to fit a particular part or shape. The main purpose of a fixture is to locate and in some cases hold a workpiece during either a machining operation or some...
.
The scanner mechanism may have three different forms:
- A carriage system with rigid arms held tightly in perpendicular relationship and each axis gliding along a track. Such systems work best with flat profile shapes or simple convex curved surfaces.
- An articulated arm with rigid bones and high precision angular sensors. The location of the end of the arm involves complex math calculating the wrist rotation angle and hinge angle of each joint. This is ideal for probing into crevasses and interior spaces with a small mouth opening.
- A combination of both methods may be used, such as an articulated arm suspended from a traveling carriage, for mapping large objects with interior cavities or overlapping surfaces.
A CMM (coordinate measuring machine) is an example of a contact 3D scanner. It is used mostly in manufacturing and can be very precise. The disadvantage of CMMs though, is that it requires contact with the object being scanned. Thus, the act of scanning the object might modify or damage it. This fact is very significant when scanning delicate or valuable objects such as historical artifacts. The other disadvantage of CMMs is that they are relatively slow compared to the other scanning methods. Physically moving the arm that the probe is mounted on can be very slow and the fastest CMMs can only operate on a few hundred hertz. In contrast, an optical system like a laser scanner can operate from 10 to 500 kHz.
Other examples are the hand driven touch probes used to digitize clay models in computer animation industry.
Non-contact active
Active scanners emit some kind of radiation or light and detect its reflection in order to probe an object or environment. Possible types of emissions used include light, ultrasoundNon-Contact Ultrasound
Non-Contact Ultrasound is a method of non-destructive testing where ultrasound is generated and used to test materials without the generating sensor making direct or indirect contact with the test material or test subject. Historically this has been difficult to do, as a typical transducer is very...
or x-ray.
Time-of-flight
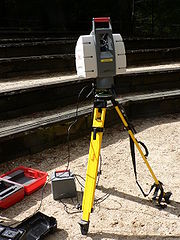
Speed of light
The speed of light in vacuum, usually denoted by c, is a physical constant important in many areas of physics. Its value is 299,792,458 metres per second, a figure that is exact since the length of the metre is defined from this constant and the international standard for time...




Picosecond
A picosecond is 10−12 of a second. That is one trillionth, or one millionth of one millionth of a second, or 0.000 000 000 001 seconds. A picosecond is to one second as one second is to 31,700 years....
s (approx.) is the time taken for light to travel 1 millimeter.
The laser rangefinder only detects the distance of one point in its direction of view. Thus, the scanner scans its entire field of view one point at a time by changing the range finder's direction of view to scan different points. The view direction of the laser rangefinder can be changed either by rotating the range finder itself, or by using a system of rotating mirrors. The latter method is commonly used because mirrors are much lighter and can thus be rotated much faster and with greater accuracy. Typical time-of-flight 3D laser scanners can measure the distance of 10,000~100,000 points every second.
Time-of-flight devices are also available in a 2D configuration. This is referred to as a Time-of-flight camera
Time-of-flight camera
A time-of-flight camera is a range imaging camera system that resolves distance based on the known speed of light, measuring the time-of-flight of a light signal between the camera and the subject...
.
Triangulation
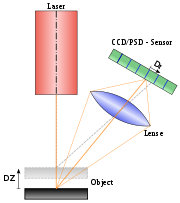
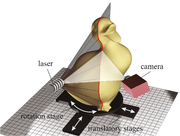
National Research Council of Canada
The National Research Council is an agency of the Government of Canada which conducts scientific research and development.- History :...
was among the first institutes to develop the triangulation based laser scanning technology in 1978.
Strengths and weaknesses
Time-of-flight and triangulation range finders each have strengths and weaknesses that make them suitable for different situations. The advantage of time-of-flight range finders is that they are capable of operating over very long distances, on the order of kilometers. These scanners are thus suitable for scanning large structures like buildings or geographic features. The disadvantage of time-of-flight range finders is their accuracy. Due to the high speed of light, timing the round-trip time is difficult and the accuracy of the distance measurement is relatively low, on the order of millimeters. Triangulation range finders are exactly the opposite. They have a limited range of some meters, but their accuracy is relatively high. The accuracy of triangulation range finders is on the order of tens of micrometers.Time of flight scanners accuracy can be lost when the laser hits the edge of an object because the information that is sent back to the scanner is from two different locations for one laser pulse. The coordinate relative to the scanners position for a point that has hit the edge of an object will be calculated based on an average and therefore will put the point in the wrong place. When using a high resolution scan on an object the chances of the beam hitting an edge are increased and the resulting data will show noise just behind the edges of the object. Scanners with a smaller beam width will help to solve this problem but will be limited by range as the beam width will increase over distance. Software can also help by determining that the first object to be hit by the laser beam should cancel out the second.
At a rate of 10,000 sample points per second, low resolution scans can take less than a second, but high resolution scans, requiring millions of samples, can take minutes for some time-of-flight scanners. The problem this creates is distortion from motion. Since each point is sampled at a different time, any motion in the subject or the scanner will distort the collected data. Thus, it is usually necessary to mount both the subject and the scanner on stable platforms and minimize vibration. Using these scanners to scan objects in motion is very difficult.
Recently, there has been research on compensating for distortion from small amounts of vibration.
When scanning in one position for any length of time slight movement can occur in the scanner position due to changes in temperature. If the scanner is set on a tripod and there is strong sunlight on one side of the scanner then that side of the tripod will expand and slowly distort the scan data from one side to another. Some laser scanners have level compensators built into them to counteract any movement of the scanner during the scan process.
Conoscopic holography
In a ConoscopicConoscopy
Conoscopy is an optical technique to make observations of a transparent specimen in a cone of converging rays of light...
system, a laser beam is projected onto the surface and then the immediate reflection along the same ray-path are put through a conoscopic crystal and projected onto a CCD. The result is a diffraction pattern, that can be frequency analyzed
Frequency analysis
In cryptanalysis, frequency analysis is the study of the frequency of letters or groups of letters in a ciphertext. The method is used as an aid to breaking classical ciphers....
to determine the distance to the measured surface. The main advantage with Conoscopic Holography is that only a single ray-path is needed for measuring, thus giving an opportunity to measure for instance the depth of a finely drilled hole.
Hand-held laser scanners
Hand-held laser scanners create a 3D image through the triangulation mechanism described above: a laser dot or line is projected onto an object from a hand-held device and a sensor (typically a charge-coupled deviceCharge-coupled device
A charge-coupled device is a device for the movement of electrical charge, usually from within the device to an area where the charge can be manipulated, for example conversion into a digital value. This is achieved by "shifting" the signals between stages within the device one at a time...
or position sensitive device
Position sensitive device
A Position Sensitive Device and/or Position Sensitive Detector is an optical position sensor , that can measure a position of a light spot in one or two-dimensions on a sensor surface.- Principles :...
) measures the distance to the surface. Data is collected in relation to an internal coordinate system and therefore to collect data where the scanner is in motion the position of the scanner must be determined. The position can be determined by the scanner using reference features on the surface being scanned (typically adhesive reflective tabs) or by using an external tracking method. External tracking often takes the form of a laser tracker (to provide the sensor position) with integrated camera (to determine the orientation of the scanner) or a photogrammetric solution using 3 or more cameras providing the complete Six degrees of freedom
Six degrees of freedom
Six degrees of freedom refers to motion of a rigid body in three-dimensional space, namely the ability to move forward/backward, up/down, left/right combined with rotation about three perpendicular axes...
of the scanner. Both techniques tend to use infrared
Infrared
Infrared light is electromagnetic radiation with a wavelength longer than that of visible light, measured from the nominal edge of visible red light at 0.74 micrometres , and extending conventionally to 300 µm...
Light-emitting diode
Light-emitting diode
A light-emitting diode is a semiconductor light source. LEDs are used as indicator lamps in many devices and are increasingly used for other lighting...
s attached to the scanner which are seen by the camera(s) through filters providing resilience to ambient lighting.
Data is collected by a computer and recorded as data points within Three-dimensional space
Three-dimensional space
Three-dimensional space is a geometric 3-parameters model of the physical universe in which we live. These three dimensions are commonly called length, width, and depth , although any three directions can be chosen, provided that they do not lie in the same plane.In physics and mathematics, a...
, with processing this can be converted into a triangulated mesh and then a Computer-aided design
Computer-aided design
Computer-aided design , also known as computer-aided design and drafting , is the use of computer technology for the process of design and design-documentation. Computer Aided Drafting describes the process of drafting with a computer...
model, often as Nonuniform rational B-spline
Nonuniform rational B-spline
Non-uniform rational basis spline is a mathematical model commonly used in computer graphics for generating and representing curves and surfaces which offers great flexibility and precision for handling both analytic and freeform shapes.- History :Development of NURBS began in the 1950s by...
surfaces. Hand-held laser scanners can combine this data with passive, visible-light sensors—which capture surface textures and colors—to build (or "reverse engineer") a full 3D model.
Structured light
Structured-light 3D scanners project a pattern of light on the subject and look at the deformation of the pattern on the subject. The pattern may be one dimensional or two dimensional. An example of a one dimensional pattern is a line. The line is projected onto the subject using either an LCD projectorLCD projector
An LCD projector is a type of video projector for displaying video, images or computer data on a screen or other flat surface. It is a modern equivalent of the slide projector or overhead projector...
or a sweeping laser. A camera, offset slightly from the pattern projector, looks at the shape of the line and uses a technique similar to triangulation to calculate the distance of every point on the line. In the case of a single-line pattern, the line is swept across the field of view to gather distance information one strip at a time.
An example of a two-dimensional pattern is a grid or a line stripe pattern. A camera is used to look at the deformation of the pattern, and an algorithm is used to calculate the distance at each point in the pattern. Consider an array of parallel vertical laser stripes sweeping horizontally across a target. In the simplest case, one could analyze an image and assume that the left-to-right sequence of stripes reflects the sequence of the lasers in the array, so that the leftmost image stripe is the first laser, the next one is the second laser, and so on. In non-trivial targets having holes, occlusions, and rapid depth changes, however, this sequencing breaks down as stripes are often hidden and may even appear to change order, resulting in laser stripe ambiguity. This problem can be solved using algorithms for multistripe laser triangulation. Structured-light scanning is still a very active area of research with many research papers published each year.
The advantage of structured-light 3D scanners is speed. Instead of scanning one point at a time, structured light scanners scan multiple points or the entire field of view at once. This reduces or eliminates the problem of distortion from motion. Some existing systems are capable of scanning moving objects in real-time.
A real-time scanner a using digital fringe projection and phase-shifting technique (a various structured light method) was developed, to capture, reconstruct, and render high-density details of dynamically deformable objects (such as facial expressions) at 40 frames per second. Recently, another scanner is developed. Different patterns can be applied to this system. The frame rate for capturing and data processing achieves 120 frames per second. It can also scan isolated surfaces, for example two moving hands.
Modulated light
Modulated light 3D scanners shine a continually changing light at the subject. Usually the light source simply cycles its amplitude in a sinusoidal pattern. A camera detects the reflected light and the amount the pattern is shifted by determines the distance the light traveled. Modulated light also allows the scanner to ignore light from sources other than a laser, so there is no interference.Medical
Computed tomography
Computed tomography
X-ray computed tomography or Computer tomography , is a medical imaging method employing tomography created by computer processing...
(CT) is a medical imaging method which generates a three-dimensional image of the inside of an object from a large series of two-dimensional X-ray images, similarly Magnetic resonance imaging
Magnetic resonance imaging
Magnetic resonance imaging , nuclear magnetic resonance imaging , or magnetic resonance tomography is a medical imaging technique used in radiology to visualize detailed internal structures...
is another a medical imaging technique that provides much greater contrast between the different soft tissues of the body than computed tomography (CT) does, making it especially useful in neurological (brain), musculoskeletal, cardiovascular, and oncological (cancer) imaging. These techniques produce a discrete 3D volumetric representation
Voxel
A voxel is a volume element, representing a value on a regular grid in three dimensional space. This is analogous to a pixel, which represents 2D image data in a bitmap...
that can be directly visualized
Volume rendering
In scientific visualization and computer graphics, volume rendering is a set of techniques used to display a 2D projection of a 3D discretely sampled data set.A typical 3D data set is a group of 2D slice images acquired by aCT, MRI, or MicroCT scanner....
, manipulated or converted to traditional 3D surface by mean of isosurface extraction algorithms
Marching cubes
Marching cubes is a computer graphics algorithm, published in the 1987 SIGGRAPH proceedings by Lorensen and Cline, for extracting a polygonal mesh of an isosurface from a three-dimensional scalar field...
.
Industrial
Although most common in medicine, Computed tomography, Microtomography
Industrial CT Scanning
Industrial CT scanning is a process which uses X-ray equipment to produce three-dimensional representations of components both externally and internally. Industrial CT scanning has been used in many areas of industry for internal inspection of components...
and MRI are also used in other fields for acquiring a digital representation of an object and its interior, such as nondestructive materials testing, reverse engineering
Reverse engineering
Reverse engineering is the process of discovering the technological principles of a device, object, or system through analysis of its structure, function, and operation...
, or the study biological and paleontological specimens.
Non-contact passive
Passive scanners do not emit any kind of radiation themselves, but instead rely on detecting reflected ambient radiation. Most scanners of this type detect visible light because it is a readily available ambient radiation. Other types of radiation, such as infrared could also be used. Passive methods can be very cheap, because in most cases they do not need particular hardware but simple digital cameras.- Stereoscopic systems usually employ two video cameras, slightly apart, looking at the same scene. By analyzing the slight differences between the images seen by each camera, it is possible to determine the distance at each point in the images. This method is based on the same principles driving human stereoscopic visionhttp://www.cogs.susx.ac.uk/users/davidy/teachvision/vision5.html.
- PhotometricPhotometric StereoPhotometric stereo is a technique in computer vision for estimating the surface normals of objects by observing that object under different lighting conditions....
systems usually use a single camera, but take multiple images under varying lighting conditions. These techniques attempt to invert the image formation model in order to recover the surface orientation at each pixel. - Silhouette techniques use outlines created from a sequence of photographs around a three-dimensional object against a well contrasted background. These silhouetteSilhouetteA silhouette is the image of a person, an object or scene consisting of the outline and a basically featureless interior, with the silhouetted object usually being black. Although the art form has been popular since the mid-18th century, the term “silhouette” was seldom used until the early decades...
s are extruded and intersected to form the visual hullVisual hullThe Visual hull is a geometric entity created by shape-from-silhouette 3D reconstruction technique introduced by Laurentini.This technique assumes the foreground object in an image can be separated fromthe background...
approximation of the object. With these approaches some concavities of an object (like the interior of a bowl) cannot be detected.
User assisted (image-based modeling)
There are other methods that, based on the user assisted detection and identification of some features and shapes on a set of different pictures of an object are able to build an approximation of the object itself. This kind of techniques are useful to build fast approximation of simple shaped objects like buildings. Various commercial packages are available like D-Sculptor, iModeller, Autodesk ImageModeler or PhotoModelerPhotoModeler
PhotoModeler is a software application that performs image-based modeling and close range photogrammetry – producing 3D models and measurements from photography....
.
This sort of 3D scanning is based on the principles of photogrammetry
Photogrammetry
Photogrammetry is the practice of determining the geometric properties of objects from photographic images. Photogrammetry is as old as modern photography and can be dated to the mid-nineteenth century....
. It is also somewhat similar in methodology to panoramic photography
Panoramic photography
Panoramic photography is a technique of photography, using specialized equipment or software, that captures images with elongated fields of view. It is sometimes known as wide format photography. The term has also been applied to a photograph that is cropped to a relatively wide aspect ratio...
, except that the photos are taken of one object on a three-dimensional space in order to replicate it instead of taking a series of photos from one point in a three-dimensional space in order to replicate the surrounding environment.
From point clouds
The point clouds produced by 3D scanners can be used directly for measurement and visualization in the architecture and construction world.Most applications, however, use instead polygonal 3D models, NURBS surface models, or editable feature-based CAD models (aka Solid models).
- Polygon mesh models: In a polygonal representation of a shape, a curved surface is modeled as many small faceted flat surfaces (think of a sphere modeled as a disco ball). Polygon models—also called Mesh models, are useful for visualization, for some CAM (i.e., machining), but are generally "heavy" ( i.e., very large data sets), and are relatively un-editable in this form. Reconstruction to polygonal model involves finding and connecting adjacent points with straight lines in order to create a continuous surface. Many applications, both free and non free, are available for this purpose (e.g. MeshLabMeshLabMeshLab, is a free 3D mesh processing software program; MeshLab, started in late 2005, is an open-source general-purpose system aimed to help the processing of the typical not-so-small unstructured 3D models that arise in the pipeline of processing of the data coming from 3D scanning...
, kubit PointCloud for AutoCAD, JRC 3D Reconstructor, imagemodel, PolyWorks, Rapidform, Geomagic, Imageware, Rhino etc.). - Surface models: The next level of sophistication in modeling involves using a quilt of curved surface patches to model our shape. These might be NURBS, TSplines or other curved representations of curved topology. Using NURBS, our sphere is a true mathematical sphere. Some applications offer patch layout by hand but the best in class offer both automated patch layout and manual layout. These patches have the advantage of being lighter and more manipulable when exported to CAD. Surface models are somewhat editable, but only in a sculptural sense of pushing and pulling to deform the surface. This representation lends itself well to modeling organic and artistic shapes. Providers of surface modelers include Rapidform, Geomagic, Rhino, Maya, T Splines etc.
- Solid CAD models: From an engineering/manufacturing perspective, the ultimate representation of a digitized shape is the editable, parametric CAD model. After all, CAD is the common "language" of industry to describe, edit and maintain the shape of the enterprise's assets. In CAD, our sphere is described by parametric features which are easily edited by changing a value (e.g., centerpoint and radius).
These CAD models describe not simply the envelope or shape of the object, but CAD models also embody the "design intent" (i.e., critical features and their relationship to other features). An example of design intent not evident in the shape alone might be a brake drum's lug bolts, which must be concentric with the hole in the center of the drum. This knowledge would drive the sequence and method of creating the CAD model; a designer with an awareness of this relationship would not design the lug bolts referenced to the outside diameter, but instead, to the center. A modeler creating a CAD model will want to include both Shape and design intent in the complete CAD model.
Vendors offer different approaches to getting to the parametric CAD model. Some export the NURBS surfaces and leave it to the CAD designer to complete the model in CAD (e.g., Geomagic, Imageware, Rhino). Others use the scan data to create an editable and verifiable feature based model that is imported into CAD with full feature tree intact, yielding a complete, native CAD model, capturing both shape and design intent (e.g. Geomagic, Rapidform). Still other CAD applications are robust enough to manipulate limited points or polygon models within the CAD environment (e.g., Catia).
From a set of 2D slices
CT, industrial CTIndustrial CT Scanning
Industrial CT scanning is a process which uses X-ray equipment to produce three-dimensional representations of components both externally and internally. Industrial CT scanning has been used in many areas of industry for internal inspection of components...
, MRI, or Micro-CT scanners do not produce point clouds but a set of 2D slices (each termed a "tomogram") which are then 'stacked together' to produce a 3D representation. There are several ways to do this depending on the output required:
- Volume renderingVolume renderingIn scientific visualization and computer graphics, volume rendering is a set of techniques used to display a 2D projection of a 3D discretely sampled data set.A typical 3D data set is a group of 2D slice images acquired by aCT, MRI, or MicroCT scanner....
: Different parts of an object usually have different threshold values or greyscale densities. From this, a 3-dimensional model can be constructed and displayed on screen. Multiple models can be constructed from various thresholds, allowing different colors to represent each component of the object. Volume rendering is usually only used for visualisation of the scanned object. - Image segmentationSegmentation (image processing)In computer vision, segmentation refers to the process of partitioning a digital image into multiple segments . The goal of segmentation is to simplify and/or change the representation of an image into something that is more meaningful and easier to analyze...
: Where different structures have similar threshold/greyscale values, it can become impossible to separate them simply by adjusting volume rendering parameters. The solution is called segmentation, a manual or automatic procedure that can remove the unwanted structures from the image. Image segmentation software usually allows export of the segmented structures in CAD or STL format for further manipulation. - Image-based meshingImage-based meshingImage-based meshing is the automated process of creating computer models for computational fluid dynamics and finite element analysis from 3D image data...
: When using 3D image data for computational analysis (e.g. CFD and FEA), simply segmenting the data and meshing from CAD can become time consuming, and virtually intractable for the complex topologies typical of image data. The solution is called image-based meshing, an automated process of generating an accurate and realistic geometrical description of the scan data.
Material processing and production
Laser scanningLaser scanning
In modern engineering, the term `laser scanning' is used to described two related, but separate meanings. The first, more general, meaning is the controlled deflection of laser beams, visible or invisible...
describes the general method to sample or scan a surface using laser
Laser
A laser is a device that emits light through a process of optical amplification based on the stimulated emission of photons. The term "laser" originated as an acronym for Light Amplification by Stimulated Emission of Radiation...
technology. Several areas of application exist that mainly differ in the power of the lasers that are used, and in the results of the scanning process. Low laser power is used when the scanned surface doesn't have to be influenced, e.g. when it only has to be digitized. Confocal
Confocal
In geometry, confocal means having the same foci.* For an optical cavity consisting of two mirrors, confocal means that they share their foci...
or 3D
Three-dimensional space
Three-dimensional space is a geometric 3-parameters model of the physical universe in which we live. These three dimensions are commonly called length, width, and depth , although any three directions can be chosen, provided that they do not lie in the same plane.In physics and mathematics, a...
laser scanning are methods to get information about the scanned surface. Another low-power application are structured light projection systems that are used for solar cell flatness metrology enabling stress calculation with throughput in excess of 2000 wafers per hour.
For high laser power, the influence on a working piece depends on the power of the laser: medium power values are used for laser engraving
Laser engraving
Laser engraving, or laser marking, is the practice of using lasers to engrave or mark an object. The technique does not involve the use of inks, nor does it involve tool bits which contact the engraving surface and wear out...
, where material is partially removed by the laser. With higher powers the material becomes fluid and laser welding can be realized, or if the power is high enough to remove the material completely, then laser cutting
Laser cutting
Laser cutting is a technology that uses a laser to cut materials, and is typically used for industrial manufacturing applications, but is also starting to be used by schools, small businesses and hobbyists. Laser cutting works by directing the output of a high-power laser, by computer, at the...
can be performed.
Construction industry and civil engineering
- Robotic Control: e.g., a laser scanner may function as the "eye" of a robot.
- As-built drawings of Bridges, Industrial Plants, and Monuments
- Documentation of historical sites
- Site modeling and lay outing
- Quality control
- Quantity Surveys
- Freeway Redesign
- Establishing a bench mark of pre-existing shape/state in order to detect structural changes resulting from exposure to extreme loadings such as earthquake, vessel/truck impact or fire.
- Create GIS (Geographic information system) maps and GeomaticsGeomaticsGeomatics is the discipline of gathering, storing, processing, and delivering geographic information, or spatially referenced information.-Overview and etymology:...
.
Benefits of 3D scanning
3D model scanning could benefit the design process if:- Increase effectiveness working with complex parts and shapes.
- Help with design of products to accommodate someone else's part.
- If CAD models are outdated, a 3D scan will provide an updated version
- Replacement of missing or older parts
Entertainment
3D scanners are used by the entertainment industry to create digital 3D models for both movies and video games. In cases where a real-world equivalent of a model exists, it is much faster to scan the real-world object than to manually create a model using 3D modeling software. Frequently, artists sculpt physical models of what they want and scan them into digital form rather than directly creating digital models on a computer.Reverse engineering
Reverse engineeringReverse engineering
Reverse engineering is the process of discovering the technological principles of a device, object, or system through analysis of its structure, function, and operation...
of a mechanical component requires a precise digital model of the objects to be reproduced. Rather than a set of points a precise digital model can be represented by a polygon mesh
Polygon mesh
A polygon mesh or unstructured grid is a collection of vertices, edges and faces that defines the shape of a polyhedral object in 3D computer graphics and solid modeling...
, a set of flat or curved NURBS surfaces, or ideally for mechanical components, a CAD solid model. A 3D scanner can be used to digitize free-form or gradually changing shaped components as well as prismatic geometries whereas a coordinate measuring machine is usually used only to determine simple dimensions of a highly prismatic model. These data points are then processed to create a usable digital model, usually using specialized reverse engineering software.
Cultural heritage
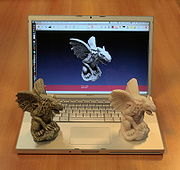
The combined use of 3D scanning and 3D printing
3D printing
3D printing is a form of additive manufacturing technology where a three dimensional object is created by laying down successive layers of material. 3D printers are generally faster, more affordable, and easier to use than other additive manufacturing technologies. However, the term 3D printing is...
technologies allows the replication of real objects without the use of traditional plaster cast
Plaster cast
A plaster cast is a copy made in plaster of another 3-dimensional form. The original from which the cast is taken may be a sculpture, building, a face, a fossil or other remains such as fresh or fossilised footprints – particularly in palaeontology .Sometimes a...
ing techniques, that in many cases can be too invasive
Invasive
Invasive may refer to:*A military invasion*An invasive species*An invasive medical procedure*The invasively progressive spread of disease from one organ in the body to another, especially in reference to cancer...
for being performed on precious or delicate cultural heritage artifacts. In the side figure the gargoyle
Gargoyle
In architecture, a gargoyle is a carved stone grotesque, usually made of granite, with a spout designed to convey water from a roof and away from the side of a building thereby preventing rainwater from running down masonry walls and eroding the mortar between...
model on the left was digitally acquired by using a 3D scanner and the produced 3D data was processed using MeshLab
MeshLab
MeshLab, is a free 3D mesh processing software program; MeshLab, started in late 2005, is an open-source general-purpose system aimed to help the processing of the typical not-so-small unstructured 3D models that arise in the pipeline of processing of the data coming from 3D scanning...
. The resulting digital 3D model was used by a rapid prototyping
Rapid prototyping
Rapid prototyping is the automatic construction of physical objects using additive manufacturing technology. The first techniques for rapid prototyping became available in the late 1980s and were used to produce models and prototype parts. Today, they are used for a much wider range of applications...
machine to create a real resin replica of original object.
Michelangelo
In 1999, two different research groups started scanning Michelangelo's statues. Stanford UniversityStanford University
The Leland Stanford Junior University, commonly referred to as Stanford University or Stanford, is a private research university on an campus located near Palo Alto, California. It is situated in the northwestern Santa Clara Valley on the San Francisco Peninsula, approximately northwest of San...
with a group led by Marc Levoy
Marc Levoy
Marc Levoy is a computer graphics researcher and Professor of Computer Science and Electrical Engineering at Stanford University. He is noted for pioneering work in volume rendering....
used a custom laser triangulation scanner built by Cyberware to scan Michelangelo's statues in Florence, notably the David
David (Michelangelo)
David is a masterpiece of Renaissance sculpture created between 1501 and 1504, by the Italian artist Michelangelo. It is a marble statue of a standing male nude. The statue represents the Biblical hero David, a favoured subject in the art of Florence...
, the Prigioni and the four statues in The Medici Chapel. The scans produced a data point density of one sample per 0.25 mm, detailed enough to see Michelangelo's chisel marks. These detailed scans produced a huge amount of data (up to 32 gigabytes) and processing the data from his scans took 5 months. Approximately in the same period a research group from IBM
IBM
International Business Machines Corporation or IBM is an American multinational technology and consulting corporation headquartered in Armonk, New York, United States. IBM manufactures and sells computer hardware and software, and it offers infrastructure, hosting and consulting services in areas...
, led by H. Rushmeier and F. Bernardini scanned the Pietà of Florence
The Deposition (Michelangelo)
The Deposition is a marble sculpture by the Italian High Renaissance master Michelangelo...
acquiring both geometric and color details. The digital model, result of the Stanford scanning campaign, was thoroughly used in the 2004 subsequent restoration of the statue.
Monticello
In 2002, David Luebke, et al. scanned Thomas Jefferson's Monticello. A commercial time of flight laser scanner, the DeltaSphere 3000, was used. The scanner data was later combined with color data from digital photographs to create the Virtual Monticello, and the Jefferson's Cabinet exhibits in the New Orleans Museum of Art in 2003. The Virtual Monticello exhibit simulated a window looking into Jefferson's Library. The exhibit consisted of a rear projection display on a wall and a pair of stereo glasses for the viewer. The glasses, combined with polarized projectors, provided a 3D effect. Position tracking hardware on the glasses allowed the display to adapt as the viewer moves around, creating the illusion that the display is actually a hole in the wall looking into Jefferson's Library. The Jefferson's Cabinet exhibit was a barrier stereogram (essentially a non-active hologram that appears different from different angles) of Jefferson's Cabinet.Cuneiform tablets
In 2003, Subodh Kumar, et al. undertook the 3D scanning of ancient cuneiform tablets. Again, a laser triangulation scanner was used. The tablets were scanned on a regular grid pattern at a resolution of 0.025 mm (0.000984251968503937 in).Kasubi Tombs
A 2009 CyArkCyArk
CyArk is a 501 nonprofit organization located in Oakland, California, United States. The company's website refers to it as a "digital archive of the world’s heritage sites for preservation and education"...
3D scanning project at Uganda's historic Kasubi Tombs
Kasubi Tombs
The Kasubi Tombs in Kampala, Uganda, is the site of the burial grounds for four kabakas , and a UNESCO World Heritage Site.On 16 March 2010, some of the major buildings there were almost completely destroyed by a fire, the cause of which is under investigation...
, a UNESCO World Heritage Site, using a Leica HDS 4500, produced detailed architectural models of Muzibu Azaala Mpanga, the main building at the complex and tomb of the Kabaka
Kabaka
Kabaka may refer to:*Kabaka of Buganda, the title of the king of Buganda*Kabaka Puttur, a village in the state of Karnataka, India...
s (Kings) of Uganda. A fire on March 16, 2010, burned down much of the Muzibu Azaala Mpanga structure, and reconstruction work is likely to lean heavily upon the dataset produced by the 3D scan mission.
"Plastico di Roma antica"
In 2005, Gabriele Guidi, et al. scanned the "Plastico di Roma antica", a model of Rome created in the last century. Neither the triangulation method, nor the time of flight method satisfied the requirements of this project because the item to be scanned was both large and contained small details. They found though, that a modulated light scanner was able to provide both the ability to scan an object the size of the model and the accuracy that was needed. The modulated light scanner was supplemented by a triangulation scanner which was used to scan some parts of the model.Medical CAD/CAM
3D scanners are used in order to capture the 3D shape of a patient in orthoticsOrthotics
Orthotics is a specialty within the medical field concerned with the design, manufacture and application of orthoses. An orthosis is an orthopedic device that supports or corrects the function of a limb or the torso...
and dentistry
Dentistry
Dentistry is the branch of medicine that is involved in the study, diagnosis, prevention, and treatment of diseases, disorders and conditions of the oral cavity, maxillofacial area and the adjacent and associated structures and their impact on the human body. Dentistry is widely considered...
. It gradually supplants tedious plaster cast. CAD/CAM software are then used to design and manufacture the orthosis, prosthesis
Prosthesis
In medicine, a prosthesis, prosthetic, or prosthetic limb is an artificial device extension that replaces a missing body part. It is part of the field of biomechatronics, the science of using mechanical devices with human muscle, skeleton, and nervous systems to assist or enhance motor control...
or dental implants.
Many Chairside dental CAD/CAM systems and Dental Laboratory CAD/CAM systems use 3D Scanner technologies to capture the 3D surface of a dental preparation (either in vivo or in vitro), in order to produce a restoration digitally using CAD software and ultimately produce the final restoration using a CAM technology (such as a CNC milling machine, or 3D printer). The chairside systems are designed to facilitate the 3D scanning of a preparation in vivo and produce the restoration (such as a Crown, Onlay, Inlay or Veneer).
Quality assurance and industrial metrology
The digitalization of real-world objects is of vital importance in various application domains. This method is especially applied in industrial quality assurance to measure the geometric dimension accuracy. Industrial processes such as assembly are complex, highly automated and typically based on CAD (Computer Aided Design) data. The problem is that the same degree of automation is also required for quality assurance. It is, for example, a very complex task to assemble a modern car, since it consists of many parts that must fit together at the very end of the production line. The optimal performance of this process is guaranteed by quality assurance systems. Especially the geometry of the metal parts must be checked in order to assure that they have the correct dimensions, fit together and finally work reliably.Within highly automated processes, the resulting geometric measures are transferred to machines that manufacture the desired objects. Due to mechanical uncertainties and abrasions, the result may differ from its digital nominal. In order to automatically capture and evaluate these deviations, the manufactured part must be digitized as well. For this purpose, 3D scanners are applied to generate point samples from the object's surface which are finally compared against the nominal data.
The process of comparing 3D data against a CAD model is referred to as CAD-Compare, and can be a useful technique for applications such as determining wear patterns on molds and tooling, determining accuracy of final build, analyzing gap and flush, or analyzing highly complex sculpted surfaces. At present, laser triangulation scanners, structured light and contact scanning are the predominant technologies employed for industrial purposes, with contact scanning remaining the slowest, but overall most accurate option.
See also
- 3D computer graphics3D computer graphics3D computer graphics are graphics that use a three-dimensional representation of geometric data that is stored in the computer for the purposes of performing calculations and rendering 2D images...
- 3D modeling3D modelingIn 3D computer graphics, 3D modeling is the process of developing a mathematical representation of any three-dimensional surface of object via specialized software. The product is called a 3D model...
- Additive Manufacturing File FormatAdditive Manufacturing File FormatAdditive Manufacturing File Format is an open standard for describing objects for additive manufacturing processes such as 3D printing. The official ASTM F2915standard is an XML-based format designed to allow any computer-aided design software to describe the shape and composition of any 3D object...
- Computer visionComputer visionComputer vision is a field that includes methods for acquiring, processing, analysing, and understanding images and, in general, high-dimensional data from the real world in order to produce numerical or symbolic information, e.g., in the forms of decisions...
- Confocal microscopyConfocal microscopyConfocal microscopy is an optical imaging technique used to increase optical resolution and contrast of a micrograph by using point illumination and a spatial pinhole to eliminate out-of-focus light in specimens that are thicker than the focal plane. It enables the reconstruction of...
- Confocal laser scanning microscopyConfocal laser scanning microscopyConfocal laser scanning microscopy is a technique for obtaining high-resolution optical images with depth selectivity. The key feature of confocal microscopy is its ability to acquire in-focus images from selected depths, a process known as optical sectioning...
- Industrial CT scanningIndustrial CT ScanningIndustrial CT scanning is a process which uses X-ray equipment to produce three-dimensional representations of components both externally and internally. Industrial CT scanning has been used in many areas of industry for internal inspection of components...
- InterferometryInterferometryInterferometry refers to a family of techniques in which electromagnetic waves are superimposed in order to extract information about the waves. An instrument used to interfere waves is called an interferometer. Interferometry is an important investigative technique in the fields of astronomy,...
- Laser rangefinder
- Laser scanningLaser scanningIn modern engineering, the term `laser scanning' is used to described two related, but separate meanings. The first, more general, meaning is the controlled deflection of laser beams, visible or invisible...
- Time-of-flight cameraTime-of-flight cameraA time-of-flight camera is a range imaging camera system that resolves distance based on the known speed of light, measuring the time-of-flight of a light signal between the camera and the subject...
External links
- 3D Photography Course Notes
- 3D Photography on your desk: development of a simple and inexpensive method for extracting the three-dimensional shape of objects