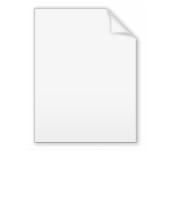
Surface plate
Encyclopedia
A surface plate is a solid, flat
plate used as the main horizontal reference plane
for precision inspection, marking out
(layout), and tooling setup. The surface plate is often used as the baseline for all measurements to the workpiece, therefore one primary surface is finished extremely flat with accuracy up to .00001"/.00025 mm for a grade AA or AAA plate. Surface plates are a very common tool in the manufacturing industry and are often permanently attached to robotic type inspection devices such as a coordinate-measuring machine
.
Unlike most instruments of mechanical precision, surface plates do not derive their precision from more-precise standards. Instead they originate precision by application of the principle of "automatic generation of gages". In this process, three approximately flat surfaces are progressively refined to precise flatness by manual rubbing against each other in pairs with a fine abrasive. Any errors of flatness tend to wear off with this abrasion, since the only stable, mutually conjugate surface shape is a plane. Joseph Whitworth
described this process to the British Association in 1840 in his paper The Mode of Producing a True Plane as he related during his chairman's address in 1856 at the inaugural meeting of the British Institute of Mechanical Engineers in Glasgow.
Surface plates must be calibrated on a regular basis to ensure that chipping, warping or wear has not occurred. A common problem with surface plates are specific areas or a section that is frequently used by another tool (such as a height gauge
) that will cause wear to a specific point resulting in an uneven surface and reduced overall accuracy to the plate. Tools and workpieces may also cause damage when dropped on the surface plate or when material chips have not been removed. This will result in erroneous measurements and can only be fixed by resurfacing the plate.
, metal was the standard material used for surface plates, however, after the war efforts of various countries put a strain on the availability of metal, a monument and metal shop owner (Wallace Herman) in Dayton, Ohio started using granite in place of metal for his surface plates. Today most surface plates continue to be made of black granite
with less common surface plates being made of pink granite or diabase
. The quartz content of surface plate determines the wear ability of the granite surface plate with higher quartz content being more resistant to wear. Pink granite contains much higher levels of quartz and is often thinner than black granite, which reduces the load-bearing capabilities of the surface plate.
Damage to a granite surface plate will usually result in a chip but does not affect the accuracy of the overall plane. Even though chipped, another flat surface can still make contact with the undamaged portion of a chipped surface plate where as damage to a cast iron plate often raises the surrounding material above the working plane causing inspected objects to no longer sit parallel to the surface plate.
Granite is also inherently stable, non-magnetic, and will not rust.
with the ribbing used to increase strength while reducing the weight. The cast iron was aged to reduce stress
in the metal in an effort to decrease the likelihood of the plate twisting or warping over time.
Cast iron surface plates are now frequently used on production floors as a tool for lapping granite surface plates to achieve certain grades of accuracy. The metal allows itself to be impregnated with the lapping media over a large flat surface.
Despite a fallout in popularity among machine shops, cast iron remains the most popular material for surface masters (different usage from a surface plate) among laboratory metrologist
s, machine builders, gage makers, and other high-accuracy industries that have a requirement for gauging flatness. Cast iron that has been properly cast is more dimensionally and geometrically stable over time than granite or ceramics, is more easily worked to a higher grade of flatness, and provides a better bearing surface to assist the creation of other master standards. These specialized surface plates are produced in sets of three, by the company that will be using them, so the plates may be regularly verified and refined without the need to send the plates out for external rework. Despite the very stable structure, cast iron remains unsuitable even in high tolerance production applications for use as a normal surface plate due to thermal expansion encountered with regular use as an inspection tool. The nature and use of a surface master, by contrast, already necessitates expensive measures to control temperature regardless of material choice, and cast iron becomes preferable.
Cast iron unlike granite has also very uniform optical properties, and unlike glass or ceramic material very small light penetration depth which makes it a favorable material for certain optical applications .
is an alternative material and was used during World War II when material and manufacturing capacity were in short supply. Glass can be suitably ground and has the benefit that it chips rather than raising a burr which is a problem when using cast iron.
, straight edge
, gage blocks, sine bar
, sine plate, dial indicator
, parallels
, angle plate
, height gage, etc.
Flatness (manufacturing)
In manufacturing and mechanical engineering, flatness is an important geometric condition for workpieces and tools.In the manufacture of precision parts and assemblies, especially where parts will be required to be connected across a surface area in an air-tight or liquid-tight manner, flatness is...
plate used as the main horizontal reference plane
Datum references
Datum reference are a concept used in carpentry, metalworking, needlework, Geometric dimensioning and tolerancing and similar activities....
for precision inspection, marking out
Marking out
Marking out or layout is the process of transferring a design or pattern to a workpiece, as the first step in the manufacturing process...
(layout), and tooling setup. The surface plate is often used as the baseline for all measurements to the workpiece, therefore one primary surface is finished extremely flat with accuracy up to .00001"/.00025 mm for a grade AA or AAA plate. Surface plates are a very common tool in the manufacturing industry and are often permanently attached to robotic type inspection devices such as a coordinate-measuring machine
Coordinate-measuring machine
A coordinate measuring machine is a device for measuring the physical geometrical characteristics of an object. This machine may be manually controlled by an operator or it may be computer controlled. Measurements are defined by a probe attached to the third moving axis of this machine...
.
Accuracy and grade
There are varying grades used to describe the accuracy of some metrology equipment such as: AA, A, B and Workshop grade. While workshop grade is the least accurate, the plates are often held to a high degree of flatness.Unlike most instruments of mechanical precision, surface plates do not derive their precision from more-precise standards. Instead they originate precision by application of the principle of "automatic generation of gages". In this process, three approximately flat surfaces are progressively refined to precise flatness by manual rubbing against each other in pairs with a fine abrasive. Any errors of flatness tend to wear off with this abrasion, since the only stable, mutually conjugate surface shape is a plane. Joseph Whitworth
Joseph Whitworth
Sir Joseph Whitworth, 1st Baronet was an English engineer, entrepreneur, inventor and philanthropist. In 1841, he devised the British Standard Whitworth system, which created an accepted standard for screw threads...
described this process to the British Association in 1840 in his paper The Mode of Producing a True Plane as he related during his chairman's address in 1856 at the inaugural meeting of the British Institute of Mechanical Engineers in Glasgow.
Surface plates must be calibrated on a regular basis to ensure that chipping, warping or wear has not occurred. A common problem with surface plates are specific areas or a section that is frequently used by another tool (such as a height gauge
Height gauge
A height gauge is a measuring device used either for determining the height of something, or for repetitious marking of items to be worked on...
) that will cause wear to a specific point resulting in an uneven surface and reduced overall accuracy to the plate. Tools and workpieces may also cause damage when dropped on the surface plate or when material chips have not been removed. This will result in erroneous measurements and can only be fixed by resurfacing the plate.
Granite
Before the Second World WarWorld War II
World War II, or the Second World War , was a global conflict lasting from 1939 to 1945, involving most of the world's nations—including all of the great powers—eventually forming two opposing military alliances: the Allies and the Axis...
, metal was the standard material used for surface plates, however, after the war efforts of various countries put a strain on the availability of metal, a monument and metal shop owner (Wallace Herman) in Dayton, Ohio started using granite in place of metal for his surface plates. Today most surface plates continue to be made of black granite
Granite
Granite is a common and widely occurring type of intrusive, felsic, igneous rock. Granite usually has a medium- to coarse-grained texture. Occasionally some individual crystals are larger than the groundmass, in which case the texture is known as porphyritic. A granitic rock with a porphyritic...
with less common surface plates being made of pink granite or diabase
Diabase
Diabase or dolerite is a mafic, holocrystalline, subvolcanic rock equivalent to volcanic basalt or plutonic gabbro. In North American usage, the term diabase refers to the fresh rock, whilst elsewhere the term dolerite is used for the fresh rock and diabase refers to altered material...
. The quartz content of surface plate determines the wear ability of the granite surface plate with higher quartz content being more resistant to wear. Pink granite contains much higher levels of quartz and is often thinner than black granite, which reduces the load-bearing capabilities of the surface plate.
Damage to a granite surface plate will usually result in a chip but does not affect the accuracy of the overall plane. Even though chipped, another flat surface can still make contact with the undamaged portion of a chipped surface plate where as damage to a cast iron plate often raises the surrounding material above the working plane causing inspected objects to no longer sit parallel to the surface plate.
Granite is also inherently stable, non-magnetic, and will not rust.
Cast iron
Prior to World War II, almost all surface plates were made from ribbed cast ironCast iron
Cast iron is derived from pig iron, and while it usually refers to gray iron, it also identifies a large group of ferrous alloys which solidify with a eutectic. The color of a fractured surface can be used to identify an alloy. White cast iron is named after its white surface when fractured, due...
with the ribbing used to increase strength while reducing the weight. The cast iron was aged to reduce stress
Residual stress
Residual stresses are stresses that remain after the original cause of the stresses has been removed. They remain along a cross section of the component, even without the external cause. Residual stresses occur for a variety of reasons, including inelastic deformations and heat treatment...
in the metal in an effort to decrease the likelihood of the plate twisting or warping over time.
Cast iron surface plates are now frequently used on production floors as a tool for lapping granite surface plates to achieve certain grades of accuracy. The metal allows itself to be impregnated with the lapping media over a large flat surface.
Despite a fallout in popularity among machine shops, cast iron remains the most popular material for surface masters (different usage from a surface plate) among laboratory metrologist
Metrologist
Metrologists perform metrology work involving precision measurement and comparison of physical quantities such as mass, length, time, force, speed, voltage and current. They calibrate precision equipment which measures these physical units. They may also certify that outside standards of such...
s, machine builders, gage makers, and other high-accuracy industries that have a requirement for gauging flatness. Cast iron that has been properly cast is more dimensionally and geometrically stable over time than granite or ceramics, is more easily worked to a higher grade of flatness, and provides a better bearing surface to assist the creation of other master standards. These specialized surface plates are produced in sets of three, by the company that will be using them, so the plates may be regularly verified and refined without the need to send the plates out for external rework. Despite the very stable structure, cast iron remains unsuitable even in high tolerance production applications for use as a normal surface plate due to thermal expansion encountered with regular use as an inspection tool. The nature and use of a surface master, by contrast, already necessitates expensive measures to control temperature regardless of material choice, and cast iron becomes preferable.
Cast iron unlike granite has also very uniform optical properties, and unlike glass or ceramic material very small light penetration depth which makes it a favorable material for certain optical applications .
Glass
GlassGlass
Glass is an amorphous solid material. Glasses are typically brittle and optically transparent.The most familiar type of glass, used for centuries in windows and drinking vessels, is soda-lime glass, composed of about 75% silica plus Na2O, CaO, and several minor additives...
is an alternative material and was used during World War II when material and manufacturing capacity were in short supply. Glass can be suitably ground and has the benefit that it chips rather than raising a burr which is a problem when using cast iron.
Accessories
The surface plate is used in conjunction with accessories such as a squareMachinist square
A machinist square or engineer's square is the metalworkers' equivalent of a try square. It consists of a steel blade inserted and either welded or pinned into a heavier body at an angle of 90°. In the accompanying image, there is evidence of pinning at the intersection of the blade and body: the...
, straight edge
Straightedge
A straightedge is a tool with an edge free from curves, or straight, used for transcribing straight lines, or checking the straightness of lines...
, gage blocks, sine bar
Sine bar
It consists of a hardened, precision ground body with two precision ground cylinders fixed at the ends. The distance between the centers of the cylinders is precisely controlled, and the top of the bar is parallel to a line through the centers of the two rollers...
, sine plate, dial indicator
Dial indicator
Dial indicators, also known as dial gauges and probe indicators, are instruments used to accurately measure small linear distances, and are frequently used in industrial and mechanical processes...
, parallels
Parallels (engineering)
Parallels are rectangular blocks of metal, commonly made from tool steel, stainless steel or cast iron, which have 2, 4 or 6 faces ground or lapped to a precise surface finish...
, angle plate
Angle plate
An angle plate is a work holding device used as a fixture in metalworking.The angle plate is made from high quality material that has been stabilized to prevent further movement or distortion...
, height gage, etc.
Further reading
- Society of Manufacturing Engineers, (1991). Fundamentals of Tool Design. Dearborn, MichiganMichiganMichigan is a U.S. state located in the Great Lakes Region of the United States of America. The name Michigan is the French form of the Ojibwa word mishigamaa, meaning "large water" or "large lake"....
: Society of Manufacturing Engineers. ISBN 0-87263-412-4