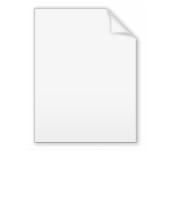
Crusher
Encyclopedia
A crusher is a machine
designed to reduce large rock
s into smaller rocks, gravel, or rock dust. Crushers may be used to reduce the size, or change the form, of waste materials so they can be more easily disposed of or recycled, or to reduce the size of a solid mix of raw materials (as in rock ore
), so that pieces of different composition can be differentiated. Crushing is the process of transferring a force amplified by mechanical advantage
through a material made of molecules that bond together more strongly, and resist deformation more, than those in the material being crushed do. Crushing devices hold material between two parallel or tangent
solid surfaces, and apply sufficient force to bring the surfaces together to generate enough energy within the material being crushed so that its molecules separate from (fracturing), or change alignment in relation to (deformation), each other. The earliest crushers were hand-held stones, where the weight of the stone provided a boost to muscle power, used against a stone anvil. Querns and mortars
are types of these crushing devices.
Mining operations use crushers, commonly classified by the degree to which they fragment the starting material, with primary and secondary crushers handling coarse materials, and tertiary and quaternary crushers reducing ore particles to finer gradations. Each crusher is designed to work with a certain maximum size of raw material, and often delivers its output to a screening machine which sorts and directs the product for further processing. Typically, crushing stages are followed by milling stages if the materials need to be further reduced. Crushers are used to reduce particle size enough so that the material can be processed into finer particles in a grinder. A typical circuit at a mine might consist of a crusher followed by a SAG mill followed by a ball mill. In this context, the SAG mill and ball mill are considered grinders rather than crushers.
In operation, the raw material (of various sizes) is usually delivered to the primary crusher's hopper by dump truck
s, excavators or wheeled front-end loaders
. A feeder device such as an apron feeder, conveyor or vibrating grid controls the rate at which this material enters the crusher, and often contains a preliminary screening device which allows smaller material to bypass the crusher itself, thus improving efficiency. Primary crushing reduces the large pieces to a size which can be handled by the downstream machinery.
Some crushers are mobile and can crush rocks (as large as 60 inches). Primarily used in-pit at the mine face these units are able to move with the large infeed machines (mainly shovels)to increase the tonnage produced. In a mobile road operation, these crushed rocks are directly combined with concrete and asphalt which are then deposited on to a road surface. This removes the need for hauling over-sized material to a stationary crusher and then back to the road surface.
The following table describes typical uses of commonly used crushers:
or pitman
mechanism. The jaws are farther apart at the top than at the bottom, forming a tapered chute so that the material is crushed progressively smaller and smaller as it travels downward until it is small enough to escape from the bottom opening. The movement of the jaw can be quite small, since complete crushing is not performed in one stroke. The inertia required to crush the material is provided by a weighted flywheel that moves a shaft creating an eccentric motion that causes the closing of the gap.
Single and double toggle jaw crushers are constructed of heavy duty fabricated plate frames with reinforcing ribs throughout. The crushers components are of high strength design to accept high power draw. Manganese steel is used for both fixed and movable jaw faces. Heavy flywheels allow crushing peaks on tough materials. Double Toggle jaw crushers may feature hydraulic toggle adjusting mechanisms.
arrangement. As with the jaw crusher, material travels downward between the two surfaces being progressively crushed until it is small enough to fall out through the gap between the two surfaces.
A gyratory crusher is one of the main types of primary crushers in a mine or ore processing plant. Gyratory crushers are designated in size either by the gape and mantle diameter or by the size of the receiving opening. Gyratory crushers can be used for primary or secondary crushing. The crushing action is caused by the closing of the gap between the mantle line (movable) mounted on the central vertical spindle and the concave liners (fixed) mounted on the main frame of the crusher. The gap is opened and closed by an eccentric on the bottom of the spindle that causes the central vertical spindle to gyrate. The vertical spindle is free to rotate around its own axis. The crusher illustrated is a short-shaft suspended spindle type, meaning that the main shaft is suspended at the top and that the eccentric is mounted above the gear. The short-shaft design has superseded the long-shaft design in which the eccentric is mounted below the gear.
A cone crusher is suitable for crushing a variety of mid-hard and above mid-hard ores and rocks. It has the advantage of reliable construction, high productivity, easy adjustment and lower operational costs. The spring release system of a cone crusher acts an overload protection that allows tramp to pass through the crushing chamber without damage to the crusher.
to crush material. The material is contained within a cage, with openings on the bottom, end, or side of the desired size to allow pulverized material to escape. This type of crusher is usually used with soft and non-abrasive material such as coal
, seeds, limestone, gypsum or soft metallic ores. There are two types of impact crushers: horizontal shaft impactor and vertical shaft impactor.
, phosphate
, gypsum
, weathered shale
s.
rather than surface force as the predominant force to break rock. In its natural state, rock has a jagged and uneven surface. Applying surface force (pressure
) results in unpredictable and typically non-cubicle resulting particles. Utilizing velocity
rather than surface force allows the breaking force to be applied evenly both across the surface of the rock as well as through the mass of the rock. Rock, regardless of size, has natural fissures (faults) throughout its structure. As rock is 'thrown' by a VSI Rotor against a solid anvil, it fractures and breaks along these fissures. Final particle size can be controlled by 1) the velocity
at which the rock is thrown against the anvil and 2) the distance between the end of the rotor and the impact point on the anvil. The product resulting from VSI Crushing is generally of a consistent cubicle shape such as that required by modern SUPERPAVE highway
asphalt
applications. Using this method also allows materials with much higher abrasiveness to be crushed than is capable with an HSI and most other crushing methods.
VSI crushers generally utilize a high speed spinning rotor at the center of the crushing chamber and an outer impact surface of either abrasive resistant metal anvils or crushed rock. Utilizing cast metal surfaces 'anvils' is traditionally referred to as a "Shoe and Anvil VSI". Utilizing crushed rock on the outer walls of the crusher for new rock to be crushed against is traditionally referred to as "rock on rock VSI". VSI crushers can be used in static plant set-up or in mobile tracked equipment.
The Three-Stage Breaking Action: Initially, the material is gripped by the leading faces of opposed rotor teeth. These subject the rock to multiple point loading, inducing stress into the material to exploit any natural weaknesses. At the second stage, material is broken in tension by being subjected to a three point loading, applied between the front tooth faces on one rotor, and rear tooth faces on the other rotor. Any lumps of material that still remain oversize, are broken as the rotors chop through the fixed teeth of the breaker bar, thereby achieving a three dimensional controlled product size.
The Rotating Screen Effect: The interlaced toothed rotor design allows free flowing undersize material to pass through the continuously changing gaps generated by the relatively slow moving shafts.
The Deep Scroll Tooth Pattern: The deep scroll conveys the larger material to one end of the machine and helps to spread the feed across the full length of the rotors. This feature can also be used to reject oversize material from the machine.
The largest advance in cone crusher reliability has been seen in the use of hydraulics to protect crushers from being damaged when uncrushable objects enter the crushing chamber. Foreign objects, such as steel
, can cause extensive damage to a cone crusher, and additional costs in lost production. The advance of hydraulic relief systems has greatly reduced downtime and improved the life of these machines.
Machine
A machine manages power to accomplish a task, examples include, a mechanical system, a computing system, an electronic system, and a molecular machine. In common usage, the meaning is that of a device having parts that perform or assist in performing any type of work...
designed to reduce large rock
Rock (geology)
In geology, rock or stone is a naturally occurring solid aggregate of minerals and/or mineraloids.The Earth's outer solid layer, the lithosphere, is made of rock. In general rocks are of three types, namely, igneous, sedimentary, and metamorphic...
s into smaller rocks, gravel, or rock dust. Crushers may be used to reduce the size, or change the form, of waste materials so they can be more easily disposed of or recycled, or to reduce the size of a solid mix of raw materials (as in rock ore
Ore
An ore is a type of rock that contains minerals with important elements including metals. The ores are extracted through mining; these are then refined to extract the valuable element....
), so that pieces of different composition can be differentiated. Crushing is the process of transferring a force amplified by mechanical advantage
Mechanical advantage
Mechanical advantage is a measure of the force amplification achieved by using a tool, mechanical device or machine system. Ideally, the device preserves the input power and simply trades off forces against movement to obtain a desired amplification in the output force...
through a material made of molecules that bond together more strongly, and resist deformation more, than those in the material being crushed do. Crushing devices hold material between two parallel or tangent
Tangent
In geometry, the tangent line to a plane curve at a given point is the straight line that "just touches" the curve at that point. More precisely, a straight line is said to be a tangent of a curve at a point on the curve if the line passes through the point on the curve and has slope where f...
solid surfaces, and apply sufficient force to bring the surfaces together to generate enough energy within the material being crushed so that its molecules separate from (fracturing), or change alignment in relation to (deformation), each other. The earliest crushers were hand-held stones, where the weight of the stone provided a boost to muscle power, used against a stone anvil. Querns and mortars
Mortar and pestle
A mortar and pestle is a tool used to crush, grind, and mix solid substances . The pestle is a heavy bat-shaped object, the end of which is used for crushing and grinding. The mortar is a bowl, typically made of hard wood, ceramic or stone...
are types of these crushing devices.
Industrial use
In industry, crushers are machines which use a metal surface to break or compress materials.Mining operations use crushers, commonly classified by the degree to which they fragment the starting material, with primary and secondary crushers handling coarse materials, and tertiary and quaternary crushers reducing ore particles to finer gradations. Each crusher is designed to work with a certain maximum size of raw material, and often delivers its output to a screening machine which sorts and directs the product for further processing. Typically, crushing stages are followed by milling stages if the materials need to be further reduced. Crushers are used to reduce particle size enough so that the material can be processed into finer particles in a grinder. A typical circuit at a mine might consist of a crusher followed by a SAG mill followed by a ball mill. In this context, the SAG mill and ball mill are considered grinders rather than crushers.
In operation, the raw material (of various sizes) is usually delivered to the primary crusher's hopper by dump truck
Dump truck
A dump truck is a truck used for transporting loose material for construction. A typical dump truck is equipped with a hydraulically operated open-box bed hinged at the rear, the front of which can be lifted up to allow the contents to be deposited on the ground behind the truck at the site of...
s, excavators or wheeled front-end loaders
Loader (equipment)
A loader is a heavy equipment machine often used in construction, primarily used to load material into or onto another type of machinery .-Heavy equipment front loaders:A loader A loader is a heavy equipment machine often used in construction, primarily used to load material (such as asphalt,...
. A feeder device such as an apron feeder, conveyor or vibrating grid controls the rate at which this material enters the crusher, and often contains a preliminary screening device which allows smaller material to bypass the crusher itself, thus improving efficiency. Primary crushing reduces the large pieces to a size which can be handled by the downstream machinery.
Some crushers are mobile and can crush rocks (as large as 60 inches). Primarily used in-pit at the mine face these units are able to move with the large infeed machines (mainly shovels)to increase the tonnage produced. In a mobile road operation, these crushed rocks are directly combined with concrete and asphalt which are then deposited on to a road surface. This removes the need for hauling over-sized material to a stationary crusher and then back to the road surface.
Types of crushers
The following table describes typical uses of commonly used crushers:
Type | Hardness | Abrasion limit | Moisture content | Reduction ratio | Main use |
---|---|---|---|---|---|
Jaw crushers | Soft to very hard | No limit | Dry to slightly wet, not sticky | 3/1 to 5/1 | Heavy mining, Quarried materials, sand & gravel, recycling |
Gyratory crushers | Soft to very hard | Abrasive | Dry to slightly wet, not sticky | 4/1 to 7/1 | Heavy mining, Quarried materials |
Cone crushers | Medium hard to very hard | Abrasive | Dry or wet, not sticky | 3/1 to 5/1 | Quarried materials, Sand & gravel |
Compound crusher | Medium hard to very hard | Abrasive | Dry or wet, not sticky | 3/1 to 5/1 | Mine, Building Materials |
Horizontal shaft impactors | Soft to medium hard | Slightly abrasive | Dry or wet, not sticky | 10/1 to 25/1 | Quarried materials, sand & gravel, recycling |
Vertical shaft impactors (shoe and anvil) | Medium hard to very hard | Slightly abrasive | Dry or wet, not sticky | 6/1 to 8/1 | Sand & gravel, recycling |
Vertical shaft impactors (autogenous) | Soft to very hard | No limit | Dry or wet, not sticky | 2/1 to 5/1 | Quarried materials, sand & gravel |
Mineral sizers | Hard to soft | Abrasive | Dry or wet and sticky | 2/1 to 5/1 | Heavy mining |
Jaw crusher
A jaw or toggle crusher consists of a set of vertical jaws, one jaw being fixed and the other being moved back and forth relative to it by a camCam
A cam is a rotating or sliding piece in a mechanical linkage used especially in transforming rotary motion into linear motion or vice-versa. It is often a part of a rotating wheel or shaft that strikes a lever at one or more points on its circular path...
or pitman
Connecting rod
In a reciprocating piston engine, the connecting rod or conrod connects the piston to the crank or crankshaft. Together with the crank, they form a simple mechanism that converts linear motion into rotating motion....
mechanism. The jaws are farther apart at the top than at the bottom, forming a tapered chute so that the material is crushed progressively smaller and smaller as it travels downward until it is small enough to escape from the bottom opening. The movement of the jaw can be quite small, since complete crushing is not performed in one stroke. The inertia required to crush the material is provided by a weighted flywheel that moves a shaft creating an eccentric motion that causes the closing of the gap.
Single and double toggle jaw crushers are constructed of heavy duty fabricated plate frames with reinforcing ribs throughout. The crushers components are of high strength design to accept high power draw. Manganese steel is used for both fixed and movable jaw faces. Heavy flywheels allow crushing peaks on tough materials. Double Toggle jaw crushers may feature hydraulic toggle adjusting mechanisms.
Gyratory crusher
A gyratory crusher is similar in basic concept to a jaw crusher, consisting of a concave surface and a conical head; both surfaces are typically lined with manganese steel surfaces. The inner cone has a slight circular movement, but does not rotate; the movement is generated by an eccentricEccentric (mechanism)
In mechanical engineering, an eccentric is a circular disk solidly fixed to a rotating axle with its centre offset from that of the axle ....
arrangement. As with the jaw crusher, material travels downward between the two surfaces being progressively crushed until it is small enough to fall out through the gap between the two surfaces.
A gyratory crusher is one of the main types of primary crushers in a mine or ore processing plant. Gyratory crushers are designated in size either by the gape and mantle diameter or by the size of the receiving opening. Gyratory crushers can be used for primary or secondary crushing. The crushing action is caused by the closing of the gap between the mantle line (movable) mounted on the central vertical spindle and the concave liners (fixed) mounted on the main frame of the crusher. The gap is opened and closed by an eccentric on the bottom of the spindle that causes the central vertical spindle to gyrate. The vertical spindle is free to rotate around its own axis. The crusher illustrated is a short-shaft suspended spindle type, meaning that the main shaft is suspended at the top and that the eccentric is mounted above the gear. The short-shaft design has superseded the long-shaft design in which the eccentric is mounted below the gear.
Cone crusher
A cone crusher is similar in operation to a gyratory crusher, with less steepness in the crushing chamber and more of a parallel zone between crushing zones. A cone crusher breaks rock by squeezing the rock between an eccentrically gyrating spindle, which is covered by a wear resistant mantle, and the enclosing concave hopper, covered by a manganese concave or a bowl liner. As rock enters the top of the cone crusher, it becomes wedged and squeezed between the mantle and the bowl liner or concave. Large pieces of ore are broken once, and then fall to a lower position (because they are now smaller) where they are broken again. This process continues until the pieces are small enough to fall through the narrow opening at the bottom of the crusher.A cone crusher is suitable for crushing a variety of mid-hard and above mid-hard ores and rocks. It has the advantage of reliable construction, high productivity, easy adjustment and lower operational costs. The spring release system of a cone crusher acts an overload protection that allows tramp to pass through the crushing chamber without damage to the crusher.
Impact crusher
Impact crushers involve the use of impact rather than pressurePressure
Pressure is the force per unit area applied in a direction perpendicular to the surface of an object. Gauge pressure is the pressure relative to the local atmospheric or ambient pressure.- Definition :...
to crush material. The material is contained within a cage, with openings on the bottom, end, or side of the desired size to allow pulverized material to escape. This type of crusher is usually used with soft and non-abrasive material such as coal
Coal
Coal is a combustible black or brownish-black sedimentary rock usually occurring in rock strata in layers or veins called coal beds or coal seams. The harder forms, such as anthracite coal, can be regarded as metamorphic rock because of later exposure to elevated temperature and pressure...
, seeds, limestone, gypsum or soft metallic ores. There are two types of impact crushers: horizontal shaft impactor and vertical shaft impactor.
Horizontal shaft impactor (HSI) / Hammer mill
The HSI crushers break rock by impacting the rock with hammers that fixed upon the outer edge of a spinning rotor. The practical use of HSI crushers is limited to soft materials and non abrasive materials, such as limestoneLimestone
Limestone is a sedimentary rock composed largely of the minerals calcite and aragonite, which are different crystal forms of calcium carbonate . Many limestones are composed from skeletal fragments of marine organisms such as coral or foraminifera....
, phosphate
Phosphate
A phosphate, an inorganic chemical, is a salt of phosphoric acid. In organic chemistry, a phosphate, or organophosphate, is an ester of phosphoric acid. Organic phosphates are important in biochemistry and biogeochemistry or ecology. Inorganic phosphates are mined to obtain phosphorus for use in...
, gypsum
Gypsum
Gypsum is a very soft sulfate mineral composed of calcium sulfate dihydrate, with the chemical formula CaSO4·2H2O. It is found in alabaster, a decorative stone used in Ancient Egypt. It is the second softest mineral on the Mohs Hardness Scale...
, weathered shale
Shale
Shale is a fine-grained, clastic sedimentary rock composed of mud that is a mix of flakes of clay minerals and tiny fragments of other minerals, especially quartz and calcite. The ratio of clay to other minerals is variable. Shale is characterized by breaks along thin laminae or parallel layering...
s.
Vertical shaft impactor (VSI)
VSI crushers use a different approach involving a high speed rotor with wear resistant tips and a crushing chamber designed to 'throw' the rock against. The VSI crushers utilize velocityVelocity
In physics, velocity is speed in a given direction. Speed describes only how fast an object is moving, whereas velocity gives both the speed and direction of the object's motion. To have a constant velocity, an object must have a constant speed and motion in a constant direction. Constant ...
rather than surface force as the predominant force to break rock. In its natural state, rock has a jagged and uneven surface. Applying surface force (pressure
Pressure
Pressure is the force per unit area applied in a direction perpendicular to the surface of an object. Gauge pressure is the pressure relative to the local atmospheric or ambient pressure.- Definition :...
) results in unpredictable and typically non-cubicle resulting particles. Utilizing velocity
Velocity
In physics, velocity is speed in a given direction. Speed describes only how fast an object is moving, whereas velocity gives both the speed and direction of the object's motion. To have a constant velocity, an object must have a constant speed and motion in a constant direction. Constant ...
rather than surface force allows the breaking force to be applied evenly both across the surface of the rock as well as through the mass of the rock. Rock, regardless of size, has natural fissures (faults) throughout its structure. As rock is 'thrown' by a VSI Rotor against a solid anvil, it fractures and breaks along these fissures. Final particle size can be controlled by 1) the velocity
Velocity
In physics, velocity is speed in a given direction. Speed describes only how fast an object is moving, whereas velocity gives both the speed and direction of the object's motion. To have a constant velocity, an object must have a constant speed and motion in a constant direction. Constant ...
at which the rock is thrown against the anvil and 2) the distance between the end of the rotor and the impact point on the anvil. The product resulting from VSI Crushing is generally of a consistent cubicle shape such as that required by modern SUPERPAVE highway
Highway
A highway is any public road. In American English, the term is common and almost always designates major roads. In British English, the term designates any road open to the public. Any interconnected set of highways can be variously referred to as a "highway system", a "highway network", or a...
asphalt
Asphalt
Asphalt or , also known as bitumen, is a sticky, black and highly viscous liquid or semi-solid that is present in most crude petroleums and in some natural deposits, it is a substance classed as a pitch...
applications. Using this method also allows materials with much higher abrasiveness to be crushed than is capable with an HSI and most other crushing methods.
VSI crushers generally utilize a high speed spinning rotor at the center of the crushing chamber and an outer impact surface of either abrasive resistant metal anvils or crushed rock. Utilizing cast metal surfaces 'anvils' is traditionally referred to as a "Shoe and Anvil VSI". Utilizing crushed rock on the outer walls of the crusher for new rock to be crushed against is traditionally referred to as "rock on rock VSI". VSI crushers can be used in static plant set-up or in mobile tracked equipment.
Mineral Sizers
The basic concept of the mineral Sizer, is the use of two rotors with large teeth, on small diameter shafts, driven at a low speed by a direct high torque drive system. This design produces three major principles which all interact when breaking materials using Sizer Technology. The unique principles are; The Three-Stage Breaking Action, The Rotating Screen Effect, and The Deep Scroll Tooth Pattern.The Three-Stage Breaking Action: Initially, the material is gripped by the leading faces of opposed rotor teeth. These subject the rock to multiple point loading, inducing stress into the material to exploit any natural weaknesses. At the second stage, material is broken in tension by being subjected to a three point loading, applied between the front tooth faces on one rotor, and rear tooth faces on the other rotor. Any lumps of material that still remain oversize, are broken as the rotors chop through the fixed teeth of the breaker bar, thereby achieving a three dimensional controlled product size.
The Rotating Screen Effect: The interlaced toothed rotor design allows free flowing undersize material to pass through the continuously changing gaps generated by the relatively slow moving shafts.
The Deep Scroll Tooth Pattern: The deep scroll conveys the larger material to one end of the machine and helps to spread the feed across the full length of the rotors. This feature can also be used to reject oversize material from the machine.
Technology
For the most part advances in crusher design have moved slowly. Jaw crushers have remained virtually unchanged for sixty years. More reliability and higher production have been added to basic cone crusher designs that have also remained largely unchanged. Increases in rotating speed, have provided the largest variation. For instance, a 48 inch (120 cm) cone crusher manufactured in 1960 may be able to produce 170 tons/h of crushed rock, whereas the same size cone manufactured today may produce 300 tons/h. These production improvements come from speed increases and better crushing chamber designs.The largest advance in cone crusher reliability has been seen in the use of hydraulics to protect crushers from being damaged when uncrushable objects enter the crushing chamber. Foreign objects, such as steel
Steel
Steel is an alloy that consists mostly of iron and has a carbon content between 0.2% and 2.1% by weight, depending on the grade. Carbon is the most common alloying material for iron, but various other alloying elements are used, such as manganese, chromium, vanadium, and tungsten...
, can cause extensive damage to a cone crusher, and additional costs in lost production. The advance of hydraulic relief systems has greatly reduced downtime and improved the life of these machines.
See also
- CompactorCompactorA compactor is a machine or mechanism used to reduce the size of waste material or soil through compaction. A trash compactor is often used by homes and businesses to reduce the volume of trash....
- Ball millBall millA ball mill is a type of grinder used to grind materials into extremely fine powder for use in mineral dressing processes, paints, pyrotechnics, and ceramics.-Description:...
for further reduction to powder - Mill (grinding)Mill (grinding)A grinding mill is a unit operation designed to break a solid material into smaller pieces. There are many different types of grinding mills and many types of materials processed in them. Historically mills were powered by hand , working animal , wind or water...
- Stamp millStamp millA stamp mill is a type of mill machine that crushes material by pounding rather than grinding, either for further processing or for extraction of metallic ores. Breaking material down is a type of unit operation....
- Car crusherCar crusherA car crusher is an industrial device used to reduce the dimensions of derelict cars prior to transport for recycling.Car crushers are compactors and can be of two types: "pancake", where a scrap automobile is flattened by a huge descending hydraulically-powered plate, or the baling press type,...