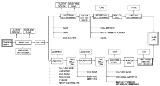
Zinc smelting
Encyclopedia
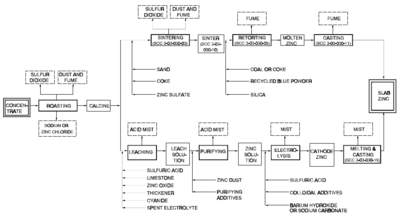
The most common zinc concentrate processed is zinc sulfide
Zinc sulfide
Zinc sulfide is a inorganic compound with the formula ZnS. ZnS is the main form of zinc in nature, where it mainly occurs as the mineral sphalerite...
, which is obtained by concentrating sphalerite
Sphalerite
Sphalerite is a mineral that is the chief ore of zinc. It consists largely of zinc sulfide in crystalline form but almost always contains variable iron. When iron content is high it is an opaque black variety, marmatite. It is usually found in association with galena, pyrite, and other sulfides...
using the froth flotation
Froth flotation
Froth flotation is a process for selectively separating hydrophobic materials from hydrophilic. This is used in several processing industries...
method. Secondary (recycled) zinc material, such as zinc oxide, is also processed with the zinc sulfide. Approximately 30% of all zinc produced is from recycled sources.
There are two methods of smelting zinc: the pyrometallurgical process and the electrolysis process. Both methods are still used. Both of these processes share the same first step: roasting.
Roasting
Roasting is a process of oxidizing zinc sulfide concentrates at high temperatures into an impure zinc oxide, called "Zinc Calcine". The chemical reactions taking place during the process are:

Approximately 90% of zinc in concentrates are oxidized to zinc oxide, but at the roasting temperatures around 10% of the zinc reacts with the iron impurities of the zinc sulfide concentrates to form zinc ferrite
Zinc ferrite
Zinc ferrites are a series of synthetic inorganic compounds of zinc and iron with the general formula of ZnxFe3-xO4. Zinc ferrite compounds can be prepared by aging solutions of Zn2, Fe3, and triethanolamine in the presence and in the absence of hydrazine, or reacting iron oxides and zinc oxide...
. A byproduct of roasting is sulfur dioxide
Sulfur dioxide
Sulfur dioxide is the chemical compound with the formula . It is released by volcanoes and in various industrial processes. Since coal and petroleum often contain sulfur compounds, their combustion generates sulfur dioxide unless the sulfur compounds are removed before burning the fuel...
, which is further processed into sulfuric acid
Sulfuric acid
Sulfuric acid is a strong mineral acid with the molecular formula . Its historical name is oil of vitriol. Pure sulfuric acid is a highly corrosive, colorless, viscous liquid. The salts of sulfuric acid are called sulfates...
, a commodity
Commodity
In economics, a commodity is the generic term for any marketable item produced to satisfy wants or needs. Economic commodities comprise goods and services....
. The linked refinery flow sheet shows a schematic of Noranda's eastern Canadian zinc roasting operation
The process of roasting varies based on the type of roaster used. There are three types of roasters: multiple-hearth, suspension, and fluidized-bed.
Multiple-hearth roaster
In a multiple-hearth roaster, the concentrate drops through a series of 9 or more hearths stacked inside a brick-lined cylindrical column. As the feed concentrate drops through the furnace, it is first dried by the hot gases passing through the hearths and then oxidized to produce calcine. The reactions are slow and can be sustained only by the addition of fuel. Multiple hearth roasters are unpressurized and operate at about 690 °C (1,274 °F). Operating time depends upon the composition of concentrate and the amount of the sulfur removal required. Multiple hearth roasters have the capability of producing a high-purity calcine.Suspension roaster
In a suspension roaster, the concentrates are blown into a combustion chamber very similar to that of a pulverized coal furnace. The roaster consists of a refractory-lined cylindrical steel shell, with a large combustion space at the top and 2 to 4 hearths in the lower portion, similar to those of a multiple hearth furnace. Additional grinding, beyond that required for a multiple hearth furnace, is normally required to ensure that heat transfer to the material is sufficiently rapid for the desulfurization and oxidation reactions to occur in the furnace chamber. Suspension roasters are unpressurized and operate at about 980 °C (1,796 °F).Fluidized-bed roaster
In a fluidized-bed roaster, finely ground sulfide concentrates are suspended and oxidized in a feedstock bed supported on an air column. As in the suspension roaster, the reaction rates for desulfurization are more rapid than in the older multiple-hearth processes. Fluidized-bed roasters operate under a pressure slightly lower than atmospheric and at temperatures averaging 1000 °C (1,832 °F). In the fluidized-bed process, no additional fuel is required after ignition has been achieved. The major advantages of this roaster are greater throughput capacities, greater sulfur removal capabilities, and lower maintenance.Electrolysis process
The electrolysis process, also known as the hydrometallurgical process, Roast-Leach-Electrowin (RLE) process, or electrolytic process, is more widely used than the pyrometallurgical processes.The electrolysis process consists of 4 steps: leaching, purification, electrolysis, and melting and casting.
Leaching
The basic leaching chemical formula that drives this process is:
This is achieved in practice though a process called double leaching. The calcine is first leached in a neutral or slightly acidic solution (of sulfuric acid) in order to leach the zinc out of the zinc oxide. The remaining calcine is then leached in strong sulfuric acid to leach the rest of the zinc out of the zinc oxide and zinc ferrite. The result of this process is a solid and a liquid; the liquid contains the zinc and is often called leach product; the solid is called leach residue and contains precious metals (usually lead and silver) which are sold as a by-product. There is also iron in the leach product from the strong acid leach, which is removed in an intermediate step, in the form of goethite
Goethite
Goethite , named after the German polymath Johann Wolfgang von Goethe, is an iron bearing oxide mineral found in soil and other low-temperature environments. Goethite has been well known since prehistoric times for its use as a pigment. Evidence has been found of its use in paint pigment samples...
, jarosite
Jarosite
Jarosite is a basic hydrous sulfate of potassium and iron with a chemical formula of KFe3+362. This sulfate mineral is formed in ore deposits by the oxidation of iron sulfides...
, and haematite. There is still cadmium
Cadmium
Cadmium is a chemical element with the symbol Cd and atomic number 48. This soft, bluish-white metal is chemically similar to the two other stable metals in group 12, zinc and mercury. Similar to zinc, it prefers oxidation state +2 in most of its compounds and similar to mercury it shows a low...
, copper
Copper
Copper is a chemical element with the symbol Cu and atomic number 29. It is a ductile metal with very high thermal and electrical conductivity. Pure copper is soft and malleable; an exposed surface has a reddish-orange tarnish...
, arsenic
Arsenic
Arsenic is a chemical element with the symbol As, atomic number 33 and relative atomic mass 74.92. Arsenic occurs in many minerals, usually in conjunction with sulfur and metals, and also as a pure elemental crystal. It was first documented by Albertus Magnus in 1250.Arsenic is a metalloid...
, antimony
Antimony
Antimony is a toxic chemical element with the symbol Sb and an atomic number of 51. A lustrous grey metalloid, it is found in nature mainly as the sulfide mineral stibnite...
, cobalt
Cobalt
Cobalt is a chemical element with symbol Co and atomic number 27. It is found naturally only in chemically combined form. The free element, produced by reductive smelting, is a hard, lustrous, silver-gray metal....
, germanium
Germanium
Germanium is a chemical element with the symbol Ge and atomic number 32. It is a lustrous, hard, grayish-white metalloid in the carbon group, chemically similar to its group neighbors tin and silicon. The isolated element is a semiconductor, with an appearance most similar to elemental silicon....
, nickel
Nickel
Nickel is a chemical element with the chemical symbol Ni and atomic number 28. It is a silvery-white lustrous metal with a slight golden tinge. Nickel belongs to the transition metals and is hard and ductile...
, and thallium
Thallium
Thallium is a chemical element with the symbol Tl and atomic number 81. This soft gray poor metal resembles tin but discolors when exposed to air. The two chemists William Crookes and Claude-Auguste Lamy discovered thallium independently in 1861 by the newly developed method of flame spectroscopy...
in the leach product. Therefore it needs to be purified.
Purification
The purification process utilizes the cementation process to further purify the zinc. It uses zinc dust and steam to remove copper, cadmium, cobalt, and nickel, which would interfere with the electrolysis process. After purification, concentrations of these impurities are limited to less than 0.05 milligram per liter (4×10−7 pound per U.S. gallon). Purification is usually conducted in large agitated tanks. The process takes place at temperatures ranging from 40 to 85 °C (104 to 185 F), and pressures ranging from atmospheric to 2.4 atm (243.2 kPa) (absolute scale). The by-products are sold for further refining.The zinc sulfate solution must be very pure for electrowinning to be at all efficient. Impurities can change the decomposition voltage enough to where the electrolysis cell produces largely hydrogen gas rather than zinc metal.
Electrolysis
Zinc is extracted from the purified zinc sulfate solution by electrowinningElectrowinning
Electrowinning, also called electroextraction, is the electrodeposition of metals from their ores that have been put in solution or liquefied. Electrorefining uses a similar process to remove impurities from a metal. Both processes use electroplating on a large scale and are important techniques...
, which is a specialized form of electrolysis. The process works by passing an electric current through the solution in a series of cells. This causes the zinc to deposits on the cathodes (aluminium
Aluminium
Aluminium or aluminum is a silvery white member of the boron group of chemical elements. It has the symbol Al, and its atomic number is 13. It is not soluble in water under normal circumstances....
sheets) and oxygen to form at the anodes. Sulfuric acid is also formed in the process and reused in the leaching process. Every 24 to 48 hours, each cell is shut down, the zinc-coated cathodes are removed and rinsed, and the zinc is mechanically stripped from the aluminium plates.
Electrolytic zinc smelters contain as many as several hundred cells. A portion of the electrical energy is converted into heat, which increases the temperature of the electrolyte. Electrolytic cells operate at temperature ranges from 30 to 35 °C (86 to 95 F) and at atmospheric pressure. A portion of the electrolyte is continuously circulated through the cooling towers both to cool and concentrate the electrolyte through evaporation of water. The cooled and concentrated electrolyte is then recycled to the cells. This process accounts for approximately one-third of all the energy usage when smelting zinc.
There are two common processes for electrowinning the metal: the low current density process, and the Tainton high current density process. The former uses a 10% sulfuric acid solution as the electrolyte, with current density of 270–325 amperes per square meter. The latter uses 22–28% sulfuric acid solution as the electrolyte with a current density of about 1,000 amperes per square metre. The latter gives better purity and has higher production capacity per volume of electrolyte, but has the disadvantage of running hotter and being more corrosive to the vessel in which it is done. In either of the electrolytic processes, each metric ton of zinc production expends about 3900 kilowatt-hour of electric power.
Melting and casting
The final step is to melt the cathodes in an induction furnaceInduction furnace
An induction furnace is an electrical furnace in which the heat is applied by induction heating of metal. The advantage of the induction furnace is a clean, energy-efficient and well-controllable melting process compared to most other means of metal melting...
. It is then either cast into pure zinc (99.995% pure) ingots or alloyed and cast into ingots.
Pyrometallurgical processes
There are also several pyrometallurgical processes that reduce zinc oxide using carbon, then distil the metallic zinc from the resulting mix in an atmosphere of carbon monoxide. The major downfall of any of the pyrometallurgical process is that it is only 98% pure; a standard composition is 1.3% lead, 0.2% cadmium, 0.03% iron, and 98.5% zinc. This may be pure enough for galvanization, but not enough for die casting alloys, which requires special high-grade zinc (99.995% pure). In order to reach this purity the zinc must be refinedZinc refining
Zinc refining is the process of purifying zinc to super high grade zinc, which is at least 99.995% pure. This process isn't usually required when smelting zinc through electrolysis processes, but is needed when zinc is produced by pyrometallurgical processes, because it is only 98.5% pure.There...
.
The four types of commercial pyrometallurgical processes are the Belgian-type horizontal retort process, the New Jersey Zinc
New Jersey Zinc Company
The Horsehead Corporation , formerly the New Jersey Zinc Company, is an American producer of zinc and related materials.The New Jersey Zinc Company was for many years the largest producer of zinc and zinc products in the United States. The company thrived in the period from 1897 to 1966, at which...
continuous vertical-retort process, the blast furnace process and the St. Joseph Minerals Corporation's
St. Joe Minerals
St. Joe Minerals Corporation was the United States largest producer of lead and zinc when it merged with Fluor Corporation in 1981.St. Joe was founded at the St. Joseph Lead Company on March 25, 1864 by Lyman W. Gilbert, John E. Wylie, Edmund I. Wade, Wilmot Williams, James L. Dunham and James L....
(electrothermic) process.
St. Joseph Mineral Company (electrothermic) process
This process was developed by the St. Joseph Mineral Company in 1930, and is the only pyrometallurgical process still used in the US to smelt zinc. The advantage of this system is that it is able to smelt a wide variety of zinc-bearing materials, including electric arc furnace dust. The disadvantage of this process is that it is less efficient than the electrolysis process.The process begins with a downdraft sintering operation. The sinter, which is a mixture of roaster calcine and EAF calcine, is loaded onto a gate type conveyor and then combustions gases are pumped through the sinter. The carbon in the combustion gases react with some the impurities, such as lead, cadmium, and halides. These impurities are driven off into filtration bags. The sinter after this process, called product sinter, usually has a composition of 48% zinc, 8% iron, 5% aluminium, 4% silicon, 2.5% calcium, and smaller quantities of magnesium, lead, and other metals. The sinter product is then charged with coke into an electric retort furnace. A pair of graphite electrodes from the top and bottom furnace produce current flow through the mixture. The coke provides electrical resistance to the mixture in order to heat the mixture to 1400 °C (2,552 °F) and produce carbon monoxide. These conditions allow for the following chemical reaction to occur:

The zinc vapour and carbon dioxide pass to a vacuum condenser, where zinc is recovered by bubbling through a molten zinc bath. Over 95% of the zinc vapour leaving the retort is condensed to liquid zinc. The carbon dioxide is regenerated with carbon, and the carbon monoxide is recycled back to the retort furnace.
Blast furnace process
This process was developed by the Imperial Smelting Corporation at AvonmouthAvonmouth
Avonmouth is a port and suburb of Bristol, England, located on the Severn Estuary, at the mouth of the River Avon.The council ward of Avonmouth also includes Shirehampton and the western end of Lawrence Weston.- Geography :...
, England, in order to increase production, increase efficiency, and decrease labour and maintenance costs. L. J. Derham proposed using a spray of molten lead droplets to rapidly chill and absorb the zinc vapour, despite the high concentration of carbon dioxide. The mixture is then cooled, where the zinc separates from the lead. The first plant using this design opened up in 1950. One of the advantages of this process is that it can co-produce lead bullion and copper dross. In 1990, it accounted for 12% of the world's zinc production.
The process starts by charging solid sinter and heated coke into the top of the blast furnace. Preheated air at 190 to 1050 °C (374 to 1,922 F) is blown into the bottom of the furnace. Zinc vapour and sulfides leave through the top and enter the condenser. Slag and lead collect at the bottom of the furnace and are tapped off regularly. The zinc is scrubbed from the vapour in the condenser via liquid lead. The liquid zinc is separated from the lead in the cooling circuit. Approximately 5000 metric tons (5,511.6 ST) of lead are required each year for this process, however this process recovers 25% more lead from the starting ores than other processes.
New Jersey Zinc continuous vertical retort
The New Jersey Zinc process is no longer used to produce primary zinc in the U.S., Europe and Japan, however it still is used to treat secondary operations. This processes peaked in 1960, when 5% of the world production was done by this process. A modified version of this process is still used at Huludao, China, which produced 65,000 metric tons per year.This process begins by roasting concentrates that are mixed with coal and briquette
Briquette
A briquette is a block of flammable matter used as fuel to start and maintain a fire. Common types of briquettes are charcoal briquettes and biomass briquettes.-Constituents of charcoal briquettes:...
d in two stages. The briquettes are then heated in an autogenous coker at 700 °C (1,292 °F) and then charged into the retort. There are three reasons to briquette the calcine: to ensure free downward movement of the charge; to permit heat transfer across a practical size cross-section; to allow adequate porosity for the passage of reduced zinc vapour to the top of the retort. The reduced zinc vapour that is collected at the top of the retort is then condensed to a liquid.
Overpelt improved upon this design by using only one large condensation chamber, instead of many small ones, as it was originally designed. This allowed for the carbon monoxide to be recirculated into the furnaces for heating the retorts.
This process was licensed to the Imperial Smelting Company (ISC), in Avonmouth, England, which had a large vertical retort (VR) plant in production for many years. It was used until the mid 1970s when it was superseded by the company's Imperial Smelting Furnace (ISF) plant. The VR plant was demolished in 1975.
Belgian-type horizontal retort process
This process was the main process used in Britain from the mid-19th century until 1951. The process was very inefficient as it was designed as a small scale batch operation. Each retort only produced 40 kilograms (88.2 lb) so companies would put them together in banks and used one large gas burner to heat all of them. The Belgian process requires redistillation to remove impurities of lead, cadmium, iron, copper, and arsenic.History
Although some zinc artifacts appear to have been made during classical antiquity in EuropeEurope
Europe is, by convention, one of the world's seven continents. Comprising the westernmost peninsula of Eurasia, Europe is generally 'divided' from Asia to its east by the watershed divides of the Ural and Caucasus Mountains, the Ural River, the Caspian and Black Seas, and the waterways connecting...
, the first production of zinc in quantity seems to have been in India
India
India , officially the Republic of India , is a country in South Asia. It is the seventh-largest country by geographical area, the second-most populous country with over 1.2 billion people, and the most populous democracy in the world...
and China
China
Chinese civilization may refer to:* China for more general discussion of the country.* Chinese culture* Greater China, the transnational community of ethnic Chinese.* History of China* Sinosphere, the area historically affected by Chinese culture...
. In India, zinc was produced at Zawar from the 12th to the 18th centuries. The sphalerite ore found here was presumably converted to zinc oxide
Zinc oxide
Zinc oxide is an inorganic compound with the formula ZnO. It is a white powder that is insoluble in water. The powder is widely used as an additive into numerous materials and products including plastics, ceramics, glass, cement, rubber , lubricants, paints, ointments, adhesives, sealants,...
via roasting, although no archaeological evidence of this has been found. Smelting is thought to have been done in sealed cylindrical clay retorts which were packed with a mixture of roasted ore, dolomite
Dolomite
Dolomite is a carbonate mineral composed of calcium magnesium carbonate CaMg2. The term is also used to describe the sedimentary carbonate rock dolostone....
, and an organic material, perhaps cow dung
Cow dung
Cow dung is the waste product of bovine animal species. These species include domestic cattle , bison , yak and water buffalo. Cow dung is the undigested residue of plant matter which has passed through the animal's gut. The resultant faecal matter is rich in minerals...
, and then placed vertically in a furnace and heated to around 1100 °C. Carbon monoxide
Carbon monoxide
Carbon monoxide , also called carbonous oxide, is a colorless, odorless, and tasteless gas that is slightly lighter than air. It is highly toxic to humans and animals in higher quantities, although it is also produced in normal animal metabolism in low quantities, and is thought to have some normal...
produced by the charring of the organic material would have reduced the zinc oxide to zinc vapour, which then liquefied in a conical clay condenser at the bottom of the retort, dripping down into a collection vessel. Over the period 1400–1800, production is estimated to have been about 200 kg/day. Zinc was also smelted in China from the mid-sixteenth century on.
Large-scale zinc production in Europe began with William Champion
William Champion (metallurgist)
William Champion is credited with patenting a process in Great Britain to distill zinc from calamine using charcoal in a smelter.Champion came from a family who were already concerned in the metal trade at Bristol, his father being a leading partner in the Bristol Brass Company. As a young man he...
, who patented a zinc distillation process in 1738. In Champion's process, zinc ore (in this case, the carbonate, ZnCO3) was sealed in large reduction pots with charcoal and heated in a furnace. The zinc vapor then descended through an iron condensing pipe until reaching a water-filled vessel at the bottom. Champion set up his first zinc works in Bristol
Bristol
Bristol is a city, unitary authority area and ceremonial county in South West England, with an estimated population of 433,100 for the unitary authority in 2009, and a surrounding Larger Urban Zone with an estimated 1,070,000 residents in 2007...
, England, but soon expanded to Warmley
Warmley
Warmley is a village in South Gloucestershire, England, to the east of Kingswood on the outskirts of Bristol.In the mid 18th century it contained the Warmley Works of William Champion...
and by 1754 had built four zinc furnaces there. Although Champion succeeded in producing about 200 tons of zinc, his business plans were not successful and he was bankrupt by 1769. However, zinc smelting continued in this area until 1880.
Year | Horizontal retort |
Vertical retort |
Electrothermic | Blast furnace |
Electrolytic |
<1916 | >90 | ||||
1929 | 28 | ||||
1937 | c. 33 | ||||
1960 | 34.5 | 11 | 7.5 | 2 | 45 |
1970 | 15 | 10 | 6.5 | 12.5 | 56 |
1980 | 3 | 7 | 6 | 10 | 74 |
Early European zinc production also took place in Silesia
Silesia
Silesia is a historical region of Central Europe located mostly in Poland, with smaller parts also in the Czech Republic, and Germany.Silesia is rich in mineral and natural resources, and includes several important industrial areas. Silesia's largest city and historical capital is Wrocław...
, in Carinthia, and in Liège
Liège
Liège is a major city and municipality of Belgium located in the province of Liège, of which it is the economic capital, in Wallonia, the French-speaking region of Belgium....
, Belgium
Belgium
Belgium , officially the Kingdom of Belgium, is a federal state in Western Europe. It is a founding member of the European Union and hosts the EU's headquarters, and those of several other major international organisations such as NATO.Belgium is also a member of, or affiliated to, many...
. In the Carinthian process, used in works established in 1798 by Bergrath Dillinger, a wood-fueled furnace heated a large number of small vertical retorts, and zinc vapor then dropped through a ceramic pipe into a common condensation chamber below. This process was out of use by 1840. The Belgian and Silesian processes both used horizontal retorts. In Silesia, Johann Ruhberg built a furnace to distill zinc in 1799, at first using pots but later changing to flat-bottomed retorts called "muffles", attached to horizontal tubes bent downwards in which the zinc condensed. The Silesian process eventually merged with the Belgian process. This process, developed by Jean-Jacques Daniel Dony, was introduced 1805–1810, and used retorts with a cylindrical cross-section. Condensers were horizontal clay tubes extending from the ends of the retorts. The merged "Belgo-Silesian" horizontal retort process was widely adopted in Europe by the third quarter of the 19th century, and later in the United States.
Experimental attempts to extract zinc via electrolysis begun in the 19th century, but the only commercially successful application before 1913 was a process, used in Great Britain
Great Britain
Great Britain or Britain is an island situated to the northwest of Continental Europe. It is the ninth largest island in the world, and the largest European island, as well as the largest of the British Isles...
and Austria
Austria
Austria , officially the Republic of Austria , is a landlocked country of roughly 8.4 million people in Central Europe. It is bordered by the Czech Republic and Germany to the north, Slovakia and Hungary to the east, Slovenia and Italy to the south, and Switzerland and Liechtenstein to the...
, where zinc and chlorine
Chlorine
Chlorine is the chemical element with atomic number 17 and symbol Cl. It is the second lightest halogen, found in the periodic table in group 17. The element forms diatomic molecules under standard conditions, called dichlorine...
were co-produced by electrolysis of an aqueous zinc chloride
Zinc chloride
Zinc chloride is the name of chemical compound with the formula ZnCl2 and its hydrates. Zinc chlorides, of which nine crystalline forms are known, are colorless or white, and are highly soluble in water. ZnCl2 itself is hygroscopic and even deliquescent. Samples should therefore be protected from...
solution. The Anaconda Copper Company, at Anaconda
Anaconda, Montana
Anaconda, county seat of Anaconda City/Deer Lodge County, is located in mountainous southwestern Montana. The Continental Divide passes within 8 miles of the community with the local Pintler Mountain range reaching 10,379 feet...
, Montana
Montana
Montana is a state in the Western United States. The western third of Montana contains numerous mountain ranges. Smaller, "island ranges" are found in the central third of the state, for a total of 77 named ranges of the Rocky Mountains. This geographical fact is reflected in the state's name,...
, and the Consolidated Mining and Smelting Company, at Trail
Trail, British Columbia
Trail is a city in the West Kootenay region of the Interior of British Columbia, Canada.-Geography:Trail has an area of . The city is located on both banks of the Columbia River, approximately 10 km north of the United States border. This section of the Columbia River valley is located between the...
, British Columbia
British Columbia
British Columbia is the westernmost of Canada's provinces and is known for its natural beauty, as reflected in its Latin motto, Splendor sine occasu . Its name was chosen by Queen Victoria in 1858...
, both built successful electrolytic plants in 1915 using the currently used zinc sulfate process. This method has continued to grow in importance and in 1975 accounted for 68% of world zinc production.
The continuous vertical retort process was introduced in 1929 by the New Jersey Zinc Company. This process used a retort with silicon carbide walls, around 9 meters high and with a cross section of 2 by 0.3 meters. The walls of the retort were heated to 1300 °C and briquettes consisting of sintered zinc ore, coke, coal, and recycled material were fed into the top of the retort. Gaseous zinc was drawn off from the top of the column and, after a 20-hour journey through the retort, spent briquettes were removed from the bottom. To condense the gaseous zinc, the company first used a simple brick chamber with carborundum baffles, but efficiency was poor. During the 1940s a condenser was developed which condensed the zinc vapor on a spray of liquid zinc droplets, thrown up by an electrical impeller.
The electrothermic process, developed by the St. Joseph's Lead Company
St. Joe Minerals
St. Joe Minerals Corporation was the United States largest producer of lead and zinc when it merged with Fluor Corporation in 1981.St. Joe was founded at the St. Joseph Lead Company on March 25, 1864 by Lyman W. Gilbert, John E. Wylie, Edmund I. Wade, Wilmot Williams, James L. Dunham and James L....
, was somewhat similar. The first commercial plant using this process was built in 1930 at the present site of Josephtown, Pennsylvania
Pennsylvania
The Commonwealth of Pennsylvania is a U.S. state that is located in the Northeastern and Mid-Atlantic regions of the United States. The state borders Delaware and Maryland to the south, West Virginia to the southwest, Ohio to the west, New York and Ontario, Canada, to the north, and New Jersey to...
. The electrothermic furnace was a steel cylinder around 15 meters high and 2 meters in diameter, lined with firebrick. A mixture of sintered ore and coke was fed into the top of the furnace, and a current of 10,000–20,000 amperes, at a potential difference of 240 volts, was applied between carbon electrodes in the furnace, raising the temperature to 1200–1400 °C. An efficient condenser was devised for this process from 1931–1936; it consisted of a bath of liquid zinc which the exhaust gases were drawn through by suction. The zinc content of the gas stream was absorbed into the liquid bath.
The blast-furnace process was developed starting in 1943 at Avonmouth, England by the Imperial Smelting Corporation. It uses a spray of molten lead droplets to condense the zinc vapor.