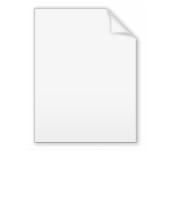
Superfinishing
Encyclopedia
Superfinishing, also known as micromachining and short-stroke honing, is a metalworking
process that improves surface finish
and workpiece geometry. This is achieved by removing just the thin amorphous surface layer left by the last process with an abrasive
stone; this layer is usually about 1 μm in magnitude. Superfinishing, unlike polishing
which produces a mirror finish, creates a cross-hatch pattern on the workpiece.
The superfinishing process was developed by the Chrysler Corporation in 1934.
piece is ground
to an initial finish, it is superfinished with a finer grit
solid abrasive
. The abrasive is oscillated or rotated while the workpiece is rotated in the opposite direction; these motions are what causes the cross-hatching. The geometry of the abrasive depends on the geometry of the workpiece surface; a stone (rectangular shape) is for cylindrical surfaces and cups and wheels are used for flat and spherical surfaces. A lubricant is used to minimize heat production, which can alter the metallurgical properties, and to carry away the swarf
; kerosene
is a common lubricant.
The abrasive cuts the surface of the workpiece in three phases. The first phase is when the abrasive first contacts the workpiece surface the dull grains of the abrasive fracture and fall away, which produces a sharp new cutting surface. In the second phase the abrasive "self dresses", where a most of the stock is removed. Finally, the abrasive grains dull, which improves the surface geometry.
The average rotational speed of abrasive wheel and/or workpiece is 1 to 15 surface m/min, with 6 to 14 m/min preferred; this is much slower compared to grinding speeds around 1800 to 3500 m/min. The pressure applied to the abrasive is very light, usually between 0.02 to 0.07 MPa (2.9 to 10.2 psi), but can be as high as 2.06 MPa (298.8 psi). Honing is usually 3.4 to 6.9 MPa (493.1 to 1,000.8 psi) and grinding is between 13.7 megapascal. When a stone is used it is oscillated at 200 to 1000 cycles with an amplitude of 1 to 5 mm (0.0393700787401575 to 0.196850393700787 in).
Superfinishing can give a surface finish of 0.01 μm.
Through-feed : This type of superfinishing is used for cylindrical workpieces. The workpiece is rotated between two drive rollers, which also move the machine as well. Four to eight progressively finer abrasive stones are used to superfinish the workpiece. The stones contact the workpiece at a 90° angle and are oscillated axially. Examples of parts that would be produced by process include tapered rolls, piston pins, shock absorber
rods, shaft
s, and needle
s.
Plunge : This type is used to finish irregularly shaped surfaces. The workpiece is rotated while the abrasive plunges onto the desired surface.
Wheels : Abrasive cups or wheels are used to superfinish flat and spherical surfaces. The wheel and workpiece are rotated in opposite directions, which creates the cross-hatching. If the two are parallel then the result if a flat finish, but if the wheel is tilted slightly a convex or concave surfaces will form.
, silicon carbide
, cubic boron nitride (CBN), and diamond
.
Aluminium oxide is used for "roughing" operations. Silicone carbide is harder than aluminium oxide, so it is used for "finishing" operations. CBN and diamond are not as commonly used, but find use with specialized materials, such as ceramic
s and M50 tool steel. Note that graphite
may be mixed with other abrasives to add lubricity and to enhance the appearance of the finish.
Abrasive grains must be very fine to be used with superfinishing; usually 5–8 μm.
, closer tolerances, higher load bearing surfaces, better sealing capabilities, and elimination of a break in period.
The main disadvantage is that superfinishing requires grinding or a hard turning operation beforehand, which increases cost. Superfinishing has a lower cutting efficiency because of smaller chips and lower material removal rate. Superfinishing stones are softer and wear more quickly, however they do not need to be dressed.
components, fuel injector components, camshaft
lobes, hydraulic cylinder rods, bearing races, needle rollers, and sharpening stones and wheels.
It has been proven that superfinishing certain parts makes them more durable. For example if the teeth in a gear are superfinished they will last up to four times as long.
Metalworking
Metalworking is the process of working with metals to create individual parts, assemblies, or large scale structures. The term covers a wide range of work from large ships and bridges to precise engine parts and delicate jewelry. It therefore includes a correspondingly wide range of skills,...
process that improves surface finish
Surface finish
Surface finish, also known as surface texture, is the characteristics of a surface. It has three components: lay, surface roughness, and waviness.-Lay:...
and workpiece geometry. This is achieved by removing just the thin amorphous surface layer left by the last process with an abrasive
Abrasive
An abrasive is a material, often a mineral, that is used to shape or finish a workpiece through rubbing which leads to part of the workpiece being worn away...
stone; this layer is usually about 1 μm in magnitude. Superfinishing, unlike polishing
Polishing
Polishing is the process of creating a smooth and shiny surface by rubbing it or using a chemical action, leaving a surface with a significant specular reflection In some materials polishing is also able to reduce diffuse reflection to...
which produces a mirror finish, creates a cross-hatch pattern on the workpiece.
The superfinishing process was developed by the Chrysler Corporation in 1934.
Process
After a metalMetal
A metal , is an element, compound, or alloy that is a good conductor of both electricity and heat. Metals are usually malleable and shiny, that is they reflect most of incident light...
piece is ground
Grinding (abrasive cutting)
Grinding is an abrasive machining process that uses a grinding wheel as the cutting tool.A wide variety of machines are used for grinding:* Hand-cranked knife-sharpening stones * Handheld power tools such as angle grinders and die grinders...
to an initial finish, it is superfinished with a finer grit
Grinding (abrasive cutting)
Grinding is an abrasive machining process that uses a grinding wheel as the cutting tool.A wide variety of machines are used for grinding:* Hand-cranked knife-sharpening stones * Handheld power tools such as angle grinders and die grinders...
solid abrasive
Abrasive
An abrasive is a material, often a mineral, that is used to shape or finish a workpiece through rubbing which leads to part of the workpiece being worn away...
. The abrasive is oscillated or rotated while the workpiece is rotated in the opposite direction; these motions are what causes the cross-hatching. The geometry of the abrasive depends on the geometry of the workpiece surface; a stone (rectangular shape) is for cylindrical surfaces and cups and wheels are used for flat and spherical surfaces. A lubricant is used to minimize heat production, which can alter the metallurgical properties, and to carry away the swarf
Swarf
Swarf, also known as turnings, chips, or filings, are shavings and chippings of metal — the debris or waste resulting from metalworking operations including milling and grinding. It can usually be recycled, and this is the preferred method of disposal due to the environmental concerns regarding...
; kerosene
Kerosene
Kerosene, sometimes spelled kerosine in scientific and industrial usage, also known as paraffin or paraffin oil in the United Kingdom, Hong Kong, Ireland and South Africa, is a combustible hydrocarbon liquid. The name is derived from Greek keros...
is a common lubricant.
The abrasive cuts the surface of the workpiece in three phases. The first phase is when the abrasive first contacts the workpiece surface the dull grains of the abrasive fracture and fall away, which produces a sharp new cutting surface. In the second phase the abrasive "self dresses", where a most of the stock is removed. Finally, the abrasive grains dull, which improves the surface geometry.
The average rotational speed of abrasive wheel and/or workpiece is 1 to 15 surface m/min, with 6 to 14 m/min preferred; this is much slower compared to grinding speeds around 1800 to 3500 m/min. The pressure applied to the abrasive is very light, usually between 0.02 to 0.07 MPa (2.9 to 10.2 psi), but can be as high as 2.06 MPa (298.8 psi). Honing is usually 3.4 to 6.9 MPa (493.1 to 1,000.8 psi) and grinding is between 13.7 megapascal. When a stone is used it is oscillated at 200 to 1000 cycles with an amplitude of 1 to 5 mm (0.0393700787401575 to 0.196850393700787 in).
Superfinishing can give a surface finish of 0.01 μm.
Types
There are three types superfinishing: Through-feed, plunge, and wheels.Through-feed : This type of superfinishing is used for cylindrical workpieces. The workpiece is rotated between two drive rollers, which also move the machine as well. Four to eight progressively finer abrasive stones are used to superfinish the workpiece. The stones contact the workpiece at a 90° angle and are oscillated axially. Examples of parts that would be produced by process include tapered rolls, piston pins, shock absorber
Shock absorber
A shock absorber is a mechanical device designed to smooth out or damp shock impulse, and dissipate kinetic energy. It is a type of dashpot.-Nomenclature:...
rods, shaft
Axle
An axle is a central shaft for a rotating wheel or gear. On wheeled vehicles, the axle may be fixed to the wheels, rotating with them, or fixed to its surroundings, with the wheels rotating around the axle. In the former case, bearings or bushings are provided at the mounting points where the axle...
s, and needle
Sewing needle
A sewing needle is a long slender tool with a pointed tip. The first needles were made of bone or wood; modern ones are manufactured from high carbon steel wire, nickel- or 18K gold plated for corrosion resistance. The highest quality embroidery needles are plated with two-thirds platinum and...
s.
Plunge : This type is used to finish irregularly shaped surfaces. The workpiece is rotated while the abrasive plunges onto the desired surface.
Wheels : Abrasive cups or wheels are used to superfinish flat and spherical surfaces. The wheel and workpiece are rotated in opposite directions, which creates the cross-hatching. If the two are parallel then the result if a flat finish, but if the wheel is tilted slightly a convex or concave surfaces will form.
Abrasives
Common abrasives used for superfinishing include: aluminium oxideAluminium oxide
Aluminium oxide is an amphoteric oxide with the chemical formula 23. It is commonly referred to as alumina, or corundum in its crystalline form, as well as many other names, reflecting its widespread occurrence in nature and industry...
, silicon carbide
Silicon carbide
Silicon carbide , also known as carborundum, is a compound of silicon and carbon with chemical formula SiC. It occurs in nature as the extremely rare mineral moissanite. Silicon carbide powder has been mass-produced since 1893 for use as an abrasive...
, cubic boron nitride (CBN), and diamond
Diamond
In mineralogy, diamond is an allotrope of carbon, where the carbon atoms are arranged in a variation of the face-centered cubic crystal structure called a diamond lattice. Diamond is less stable than graphite, but the conversion rate from diamond to graphite is negligible at ambient conditions...
.
Aluminium oxide is used for "roughing" operations. Silicone carbide is harder than aluminium oxide, so it is used for "finishing" operations. CBN and diamond are not as commonly used, but find use with specialized materials, such as ceramic
Ceramic
A ceramic is an inorganic, nonmetallic solid prepared by the action of heat and subsequent cooling. Ceramic materials may have a crystalline or partly crystalline structure, or may be amorphous...
s and M50 tool steel. Note that graphite
Graphite
The mineral graphite is one of the allotropes of carbon. It was named by Abraham Gottlob Werner in 1789 from the Ancient Greek γράφω , "to draw/write", for its use in pencils, where it is commonly called lead . Unlike diamond , graphite is an electrical conductor, a semimetal...
may be mixed with other abrasives to add lubricity and to enhance the appearance of the finish.
Abrasive grains must be very fine to be used with superfinishing; usually 5–8 μm.
Advantages and disadvantages
Advantages of superfinishing include: increasing part life, decreasing wearWear
In materials science, wear is erosion or sideways displacement of material from its "derivative" and original position on a solid surface performed by the action of another surface....
, closer tolerances, higher load bearing surfaces, better sealing capabilities, and elimination of a break in period.
The main disadvantage is that superfinishing requires grinding or a hard turning operation beforehand, which increases cost. Superfinishing has a lower cutting efficiency because of smaller chips and lower material removal rate. Superfinishing stones are softer and wear more quickly, however they do not need to be dressed.
Applications
Common applications include: steering rack components, transmissionTransmission (mechanics)
A machine consists of a power source and a power transmission system, which provides controlled application of the power. Merriam-Webster defines transmission as: an assembly of parts including the speed-changing gears and the propeller shaft by which the power is transmitted from an engine to a...
components, fuel injector components, camshaft
Camshaft
A camshaft is a shaft to which a cam is fastened or of which a cam forms an integral part.-History:An early cam was built into Hellenistic water-driven automata from the 3rd century BC. The camshaft was later described in Iraq by Al-Jazari in 1206. He employed it as part of his automata,...
lobes, hydraulic cylinder rods, bearing races, needle rollers, and sharpening stones and wheels.
It has been proven that superfinishing certain parts makes them more durable. For example if the teeth in a gear are superfinished they will last up to four times as long.