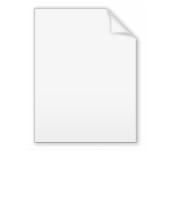
Ferritic nitrocarburizing
Encyclopedia
Ferritic nitrocarburizing is a range of case hardening
processes that diffuse
nitrogen
and carbon
into ferrous
metal
s at sub-critical temperatures. The processing temperature ranges from 525 °C (977 °F) to 625 °C (1,157 °F), but usually occurs at 565 °C (1,049 °F). At this temperature steels and other ferrous alloys are still in a ferritic phase, which is advantageous compared to other case hardening processes that occur in the austentic phase. There are four main classes of ferritic nitrocarburizing: gaseous, salt bath, ion or plasma, and fluidized-bed.
The process is used to improve three main surface integrity
aspects:
It has the added advantage of inducing little shape distortion
during the hardening process. This is because of the low processing temperature, which reduces thermal shocks and avoids phase transitions in steel.
. They called their process a "Sulfinuz" treatment because it had sulfur in the salt bath. While the process was very successful with high-speed spindles and cutting tool
s, there were issues with cleaning the solution off because it was not very water soluble.
Because of the cleaning issues the Joseph Lucas Limited company began experimenting with gaseous forms of ferritic nitrocarburizing in the late 1950s. The company applied for a patent by 1961. It produced a similar surface finish as the Sulfinuz process with the exception of the formation of sulfides. The atmosphere consisted of ammonia
, hydrocarbon
gases, and a small amount of other carbon-containing gases.
This spurred the development of a more environmentally friendly salt bath process by the German company Degussa. Their process is the widely known Tufftride process. Following this the ion nitriding process was invented in the early 1980s. This process had faster cycle times, required less cleaning and preparation, formed deeper cases, and allowed for better control of the process.
The most simple form of this process is encompassed by the trademarked Melonite process, also known as Meli 1. It is most commonly used on steels, sintered
irons, and cast iron
s to lower friction
and improve wear and corrosion resistance.
The process uses a salt bath of alkali
cyanate
. This is contained in a steel pot that has an aeration
system. The cyanate thermally reacts with the surface of the workpiece to form alkali carbonate
. The bath is then treated to convert the carbonate back to a cyanate. The surface formed from the reaction has a compound layer and a diffusion layer. The compound layer consists of iron, nitrogen, and oxygen, is abrasion resistant, and stable at elevated temperatures. The diffusion layer contains nitride
s and carbide
s. The surface hardness ranges from 800 to 1500 HV depending on the steel grade
. This also inversely affects the depth of the case; i.e. a high carbon steel will form a hard, but shallow case.
A similar process is the trademarked Nu-Tride process, also known incorrectly as the Kolene process (which is actually the company's name), which includes a preheat and an intermediate quench cycle. The intermediate quench is an oxidizing salt bath at 400 °C (752 °F). This quench is held for 5 to 20 minutes before final quenching to room temperature. This is done to minimize distortion and to destroy any lingering cyanates or cyanides left on the workpiece.
Other trademarked processes are Sursulf and Tenoplus. Sursulf has a sulfur compound in the salt bath to create surface sulfides which creates porosity
in the workpiece surface. This porosity is used to contain lubrication. Tenoplus is a two-stage high-temperature process. The first stage occurs at 625 °C (1,157 °F), while the second stage occurs at 580 °C (1,076 °F).
The parts are first cleaned, usually with a vapor degreasing
process, and then nitrocarburized around 570 °C (1,058 °F), with a process time that ranges from one to four hours. The actual gas mixtures are proprietary, but they usually contain ammonia and an endothermic
gas.
, naming the technique. The gas used for plasma nitriding is usually pure nitrogen, since no spontaneous decomposition is needed (as is the case of gaseous ferritic nitrocarburizing with ammonia). Due to the relatively low temperature range (420 °C (788 °F) to 580 °C (1,076 °F)) generally applied during plasma-assisted ferritic nitrocarburizing and gentle cooling in the furnace, the distortion of workpieces can be minimized. Stainless steel workpieces can be processed at moderate temperatures (like 420 °C (788 °F)) without the formation of chromium nitride precipitates and hence maintaining their corrosion resistance properties.
, cam
s, gear
s, dies
, hydraulic piston rods, and powdered metal
components.
Glock Ges.m.b.H., an Austria
n firearms manufacturer, utilizes the Tenifer process to protect the barrels and slides of the pistols they manufacture. The finish on a Glock pistol
is the third and final hardening process. It is 0.05 mm (0.00196850393700787 in) thick and produces a 64 Rockwell C hardness rating
via a 500 °C (932 °F) nitride bath. The final matte, non-glare finish meets or exceeds stainless steel
specifications, is 85% more corrosion resistant than a hard chrome
finish, and is 99.9% salt-water corrosion resistant. After the Tenifer process, a black Parkerized
finish is applied and the slide is protected even if the finish were to wear off. Besides Glock several other pistol manufacturers like Smith & Wesson
and Springfield Armory, Inc. also use ferritic nitrocarburizing for finishing parts like barrels and slides but they call it Melonite finish. Pistol manufacturer Caracal International L.L.C.
uses ferritic nitrocarburizing for finishing parts like barrels and slides with the plasma-based Plasox process.
Grandpower
, a Slovakian firearms producer, also uses a quench polish quench
(QPQ) treatment to harden metal parts on its K100 pistols.
Case hardening
Case hardening or surface hardening is the process of hardening the surface of a metal, often a low carbon steel, by infusing elements into the material's surface, forming a thin layer of a harder alloy...
processes that diffuse
Diffusion
Molecular diffusion, often called simply diffusion, is the thermal motion of all particles at temperatures above absolute zero. The rate of this movement is a function of temperature, viscosity of the fluid and the size of the particles...
nitrogen
Nitrogen
Nitrogen is a chemical element that has the symbol N, atomic number of 7 and atomic mass 14.00674 u. Elemental nitrogen is a colorless, odorless, tasteless, and mostly inert diatomic gas at standard conditions, constituting 78.08% by volume of Earth's atmosphere...
and carbon
Carbon
Carbon is the chemical element with symbol C and atomic number 6. As a member of group 14 on the periodic table, it is nonmetallic and tetravalent—making four electrons available to form covalent chemical bonds...
into ferrous
Ferrous
Ferrous , in chemistry, indicates a divalent iron compound , as opposed to ferric, which indicates a trivalent iron compound ....
metal
Metal
A metal , is an element, compound, or alloy that is a good conductor of both electricity and heat. Metals are usually malleable and shiny, that is they reflect most of incident light...
s at sub-critical temperatures. The processing temperature ranges from 525 °C (977 °F) to 625 °C (1,157 °F), but usually occurs at 565 °C (1,049 °F). At this temperature steels and other ferrous alloys are still in a ferritic phase, which is advantageous compared to other case hardening processes that occur in the austentic phase. There are four main classes of ferritic nitrocarburizing: gaseous, salt bath, ion or plasma, and fluidized-bed.
The process is used to improve three main surface integrity
Surface integrity
Surface integrity is the surface condition of a workpiece after being modified by a manufacturing process. The term was coined by Michael Field and John F. Kahles in 1964.The surface integrity of a workpiece or item changes the material's properties...
aspects:
- scuffing resistance
- fatigueFatigue (material)'In materials science, fatigue is the progressive and localized structural damage that occurs when a material is subjected to cyclic loading. The nominal maximum stress values are less than the ultimate tensile stress limit, and may be below the yield stress limit of the material.Fatigue occurs...
properties - corrosion resistance
It has the added advantage of inducing little shape distortion
Distortion
A distortion is the alteration of the original shape of an object, image, sound, waveform or other form of information or representation. Distortion is usually unwanted, and often many methods are employed to minimize it in practice...
during the hardening process. This is because of the low processing temperature, which reduces thermal shocks and avoids phase transitions in steel.
History
The first ferritic nitrocarburizing methods were done at low temperatures, around 550 °C (1,022 °F), in a liquid salt bath. The first company to successfully commercialize was the Imperial Chemical Industries in EnglandEngland
England is a country that is part of the United Kingdom. It shares land borders with Scotland to the north and Wales to the west; the Irish Sea is to the north west, the Celtic Sea to the south west, with the North Sea to the east and the English Channel to the south separating it from continental...
. They called their process a "Sulfinuz" treatment because it had sulfur in the salt bath. While the process was very successful with high-speed spindles and cutting tool
Cutting tool
In the context of machining, a cutting tool is any tool that is used to remove material from the workpiece by means of shear deformation. Cutting may be accomplished by single-point or multipoint tools. Single-point tools are used in turning, shaping, plaining and similar operations, and remove...
s, there were issues with cleaning the solution off because it was not very water soluble.
Because of the cleaning issues the Joseph Lucas Limited company began experimenting with gaseous forms of ferritic nitrocarburizing in the late 1950s. The company applied for a patent by 1961. It produced a similar surface finish as the Sulfinuz process with the exception of the formation of sulfides. The atmosphere consisted of ammonia
Ammonia
Ammonia is a compound of nitrogen and hydrogen with the formula . It is a colourless gas with a characteristic pungent odour. Ammonia contributes significantly to the nutritional needs of terrestrial organisms by serving as a precursor to food and fertilizers. Ammonia, either directly or...
, hydrocarbon
Hydrocarbon
In organic chemistry, a hydrocarbon is an organic compound consisting entirely of hydrogen and carbon. Hydrocarbons from which one hydrogen atom has been removed are functional groups, called hydrocarbyls....
gases, and a small amount of other carbon-containing gases.
This spurred the development of a more environmentally friendly salt bath process by the German company Degussa. Their process is the widely known Tufftride process. Following this the ion nitriding process was invented in the early 1980s. This process had faster cycle times, required less cleaning and preparation, formed deeper cases, and allowed for better control of the process.
Processes
Despite the naming the process is a modified form of nitriding and not carburizing. The shared attributes of this class of this process is the introduction of nitrogen and carbon in the ferritic state of the material. The processes are broken up into four main classes: gaseous, salt bath, ion or plasma, or fluidized-bed. The trade name and patented processes may vary slightly from the general description, but they are all a form of ferritic nitrocarburizing.Salt bath ferritic nitrocarburizing
Salt bath ferritic nitrocarburizing is also known as liquid ferritic nitrocarburizing or liquid nitrocarburizing and is also known by the trademarked names Tufftride and Tenifer.The most simple form of this process is encompassed by the trademarked Melonite process, also known as Meli 1. It is most commonly used on steels, sintered
Sintering
Sintering is a method used to create objects from powders. It is based on atomic diffusion. Diffusion occurs in any material above absolute zero, but it occurs much faster at higher temperatures. In most sintering processes, the powdered material is held in a mold and then heated to a temperature...
irons, and cast iron
Cast iron
Cast iron is derived from pig iron, and while it usually refers to gray iron, it also identifies a large group of ferrous alloys which solidify with a eutectic. The color of a fractured surface can be used to identify an alloy. White cast iron is named after its white surface when fractured, due...
s to lower friction
Friction
Friction is the force resisting the relative motion of solid surfaces, fluid layers, and/or material elements sliding against each other. There are several types of friction:...
and improve wear and corrosion resistance.
The process uses a salt bath of alkali
Alkali
In chemistry, an alkali is a basic, ionic salt of an alkali metal or alkaline earth metal element. Some authors also define an alkali as a base that dissolves in water. A solution of a soluble base has a pH greater than 7. The adjective alkaline is commonly used in English as a synonym for base,...
cyanate
Cyanate
The cyanate ion is an anion with the chemical formula written as [OCN]− or [NCO]−. In aqueous solution it acts as a base, forming isocyanic acid, HNCO. The cyanate ion is an ambidentate ligand, forming complexes with a metal ion in which either the nitrogen or oxygen atom may be the electron-pair...
. This is contained in a steel pot that has an aeration
Aeration
Aeration is the process by which air is circulated through, mixed with or dissolved in a liquid or substance.-Aeration of liquids:-Methods:Aeration of liquids is achieved by:...
system. The cyanate thermally reacts with the surface of the workpiece to form alkali carbonate
Carbonate
In chemistry, a carbonate is a salt of carbonic acid, characterized by the presence of the carbonate ion, . The name may also mean an ester of carbonic acid, an organic compound containing the carbonate group C2....
. The bath is then treated to convert the carbonate back to a cyanate. The surface formed from the reaction has a compound layer and a diffusion layer. The compound layer consists of iron, nitrogen, and oxygen, is abrasion resistant, and stable at elevated temperatures. The diffusion layer contains nitride
Nitride
In chemistry, a nitride is a compound of nitrogen where nitrogen has a formal oxidation state of −3. Nitrides are a large class of compounds with a wide range of properties and applications....
s and carbide
Carbide
In chemistry, a carbide is a compound composed of carbon and a less electronegative element. Carbides can be generally classified by chemical bonding type as follows: salt-like, covalent compounds, interstitial compounds, and "intermediate" transition metal carbides...
s. The surface hardness ranges from 800 to 1500 HV depending on the steel grade
Steel grades
Steel grades to classify various steels by their composition and physical properties have been developed by a number of standards organizations.*SAE steel grades*British Standards*International Organization for Standardization ISO/TS 4949:2003...
. This also inversely affects the depth of the case; i.e. a high carbon steel will form a hard, but shallow case.
A similar process is the trademarked Nu-Tride process, also known incorrectly as the Kolene process (which is actually the company's name), which includes a preheat and an intermediate quench cycle. The intermediate quench is an oxidizing salt bath at 400 °C (752 °F). This quench is held for 5 to 20 minutes before final quenching to room temperature. This is done to minimize distortion and to destroy any lingering cyanates or cyanides left on the workpiece.
Other trademarked processes are Sursulf and Tenoplus. Sursulf has a sulfur compound in the salt bath to create surface sulfides which creates porosity
Porosity
Porosity or void fraction is a measure of the void spaces in a material, and is a fraction of the volume of voids over the total volume, between 0–1, or as a percentage between 0–100%...
in the workpiece surface. This porosity is used to contain lubrication. Tenoplus is a two-stage high-temperature process. The first stage occurs at 625 °C (1,157 °F), while the second stage occurs at 580 °C (1,076 °F).
Gaseous ferritic nitrocarburizing
Gaseous ferritic nitrocarburizing is also known as controlled nitrocarburizing, soft nitriding, and vacuum nitrocarburizing or by the tradenames Nitrotec, Nitemper, Deganit, Triniding, Nitroc, and Nitrowear. The process works to achieve the same result as the salt bath process, except gaseous mixtures are used to diffuse the nitrogen and carbon into the workpiece.The parts are first cleaned, usually with a vapor degreasing
Vapor Degreasing
Vapor degreasing is a surface finishing process. It involves solvents in vapor form to cleanse the workpiece in preparation for further finishing operations.-Process:...
process, and then nitrocarburized around 570 °C (1,058 °F), with a process time that ranges from one to four hours. The actual gas mixtures are proprietary, but they usually contain ammonia and an endothermic
Endothermic
In thermodynamics, the word endothermic describes a process or reaction in which the system absorbs energy from the surroundings in the form of heat. Its etymology stems from the prefix endo- and the Greek word thermasi,...
gas.
Plasma-assisted ferritic nitrocarburizing
Plasma-assisted ferritic nitrocarburizing is also known as ion nitriding, plasma ion nitriding or glow-discharge nitriding. The process works to achieve the same result as the salt bath and gaseous process, except the reactivity of the media is not due to the temperature but to the gas ionized state. In this technique intense electric fields are used to generate ionized molecules of the gas around the surface to diffuse the nitrogen and carbon into the workpiece. Such highly active gas with ionized molecules is called plasmaPlasma (physics)
In physics and chemistry, plasma is a state of matter similar to gas in which a certain portion of the particles are ionized. Heating a gas may ionize its molecules or atoms , thus turning it into a plasma, which contains charged particles: positive ions and negative electrons or ions...
, naming the technique. The gas used for plasma nitriding is usually pure nitrogen, since no spontaneous decomposition is needed (as is the case of gaseous ferritic nitrocarburizing with ammonia). Due to the relatively low temperature range (420 °C (788 °F) to 580 °C (1,076 °F)) generally applied during plasma-assisted ferritic nitrocarburizing and gentle cooling in the furnace, the distortion of workpieces can be minimized. Stainless steel workpieces can be processed at moderate temperatures (like 420 °C (788 °F)) without the formation of chromium nitride precipitates and hence maintaining their corrosion resistance properties.
Uses
These processes are most commonly used on low-carbon, low-alloy steels, however they are also used on medium and high-carbon steels. Common applications include spindlesSpindle (tool)
In machine tools, a spindle is a rotating axis of the machine, which often has a shaft at its heart. The shaft itself is called a spindle, but also, in shop-floor practice, the word often is used metonymically to refer to the entire rotary unit, including not only the shaft itself, but its bearings...
, cam
Cam
A cam is a rotating or sliding piece in a mechanical linkage used especially in transforming rotary motion into linear motion or vice-versa. It is often a part of a rotating wheel or shaft that strikes a lever at one or more points on its circular path...
s, gear
Gear
A gear is a rotating machine part having cut teeth, or cogs, which mesh with another toothed part in order to transmit torque. Two or more gears working in tandem are called a transmission and can produce a mechanical advantage through a gear ratio and thus may be considered a simple machine....
s, dies
Die (manufacturing)
A die is a specialized tool used in manufacturing industries to cut or shape material using a press. Like molds, dies are generally customized to the item they are used to create...
, hydraulic piston rods, and powdered metal
Powder metallurgy
Powder metallurgy is the process of blending fine powdered materials, pressing them into a desired shape , and then heating the compressed material in a controlled atmosphere to bond the material . The powder metallurgy process generally consists of four basic steps: powder manufacture, powder...
components.
Glock Ges.m.b.H., an Austria
Austria
Austria , officially the Republic of Austria , is a landlocked country of roughly 8.4 million people in Central Europe. It is bordered by the Czech Republic and Germany to the north, Slovakia and Hungary to the east, Slovenia and Italy to the south, and Switzerland and Liechtenstein to the...
n firearms manufacturer, utilizes the Tenifer process to protect the barrels and slides of the pistols they manufacture. The finish on a Glock pistol
Glock pistol
The Glock pistol, sometimes referred to by the manufacturer as Glock "Safe Action" Pistol, is a series of semi-automatic pistols designed and produced by Glock Ges.m.b.H., located in Deutsch-Wagram, Austria. The company's founder, engineer Gaston Glock, had no experience with firearm design or...
is the third and final hardening process. It is 0.05 mm (0.00196850393700787 in) thick and produces a 64 Rockwell C hardness rating
Rockwell scale
The Rockwell scale is a hardness scale based on the indentation hardness of a material. The Rockwell test determines the hardness by measuring the depth of penetration of an indenter under a large load compared to the penetration made by a preload. There are different scales, denoted by a single...
via a 500 °C (932 °F) nitride bath. The final matte, non-glare finish meets or exceeds stainless steel
Stainless steel
In metallurgy, stainless steel, also known as inox steel or inox from French "inoxydable", is defined as a steel alloy with a minimum of 10.5 or 11% chromium content by mass....
specifications, is 85% more corrosion resistant than a hard chrome
Chrome plating
Chrome plating, often referred to simply as chrome, is a technique of electroplating a thin layer of chromium onto a metal object. The chromed layer can be decorative, provide corrosion resistance, ease cleaning procedures, or increase surface hardness.-Process:A component to be chrome plated will...
finish, and is 99.9% salt-water corrosion resistant. After the Tenifer process, a black Parkerized
Parkerizing
Parkerizing is a method of protecting a steel surface from corrosion and increasing its resistance to wear through the application of an electrochemical phosphate conversion coating...
finish is applied and the slide is protected even if the finish were to wear off. Besides Glock several other pistol manufacturers like Smith & Wesson
Smith & Wesson
Smith & Wesson is the largest manufacturer of handguns in the United States. The corporate headquarters is in Springfield, Massachusetts. Founded in 1852, Smith & Wesson's pistols and revolvers have become standard issue to police and armed forces throughout the world...
and Springfield Armory, Inc. also use ferritic nitrocarburizing for finishing parts like barrels and slides but they call it Melonite finish. Pistol manufacturer Caracal International L.L.C.
Caracal pistol
The Caracal pistol is a series of semi-automatic pistols manufactured by Caracal International L.L.C. a subsidiary of Tawazun Holding from the United Arab Emirates. Newly arrived on a competitive market, the Caracal pistol series are the first pistols made in the United Arab Emirates.In 2007,...
uses ferritic nitrocarburizing for finishing parts like barrels and slides with the plasma-based Plasox process.
Grandpower
Grandpower K100
The K100 is a 9 mm semi-automatic pistol designed and built by Grand Power s.r.o. in Banská Bystrica, Slovakia.-Development:The K100 was developed by Jaroslav Kuracina, a former weapons officer in the Slovak Army. Kuracina sketched drawings of the K100 as early as 1992, but manufacturing activities...
, a Slovakian firearms producer, also uses a quench polish quench
Quench Polish Quench
Quench polish quench is a specialized type of nitrocarburizing case hardening that increases corrosion resistance, originally developed by the Kolene Company...
(QPQ) treatment to harden metal parts on its K100 pistols.