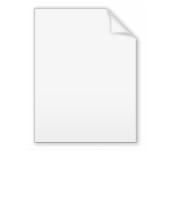
Surface integrity
Encyclopedia
Surface integrity is the surface condition of a workpiece after being modified by a manufacturing
process. The term was coined by Michael Field and John F. Kahles in 1964.
The surface integrity of a workpiece or item changes the material's properties. The consequences of changes to surface integrity are a mechanical engineering
design problem, but the preservation of those properties are a manufacturing consideration.
Surface integrity can have a great impact on a parts function; for example, Inconel
718 can have a fatigue limit
as high as 540 MPa (78,320.4 psi) after a gentle grinding
or as low as 150 MPa (21,755.7 psi) after electrical discharge machining
(EDM).
, errors of form, and flaws. The surface layer characteristics that can change through processing are: plastic deformation, residual stress
es, cracks, hardness, overaging, phase changes, recrystallization
, intergranular attack, and hydrogen embrittlement
. When a traditional manufacturing process is used, such as machining
, the surface layer sustains local plastic deformation.
The processes that affect surface integrity can be conveniently broken up into three classes: traditional processes, non-traditional processes, and finishing treatments. Traditional processes are defined as processes where the tool contacts the workpiece surface; for example: grinding
, turning
, and machining. These processes will only damage the surface integrity if the improper parameters are used, such as dull tools, too high feed speeds, improper coolant or lubrication, or incorrect grinding wheel hardness. Nontraditional processes are defined as processes where the tool does not contact the workpiece; examples of this type of process include EDM, electrochemical machining, and chemical milling. These processes will always change the surface integrity no matter how well controlled; for instance, they can leave a stress-free surface, a remelted surface, or excessive surface roughness. Finishing treatments are defined as processes that negate surface finishes imparted by traditional and non-traditional processes or improve the surface integrity. For example, residual stress can be removed via peening
or roller burnishing
or the recast layer left by EDMing can be removed via chemical milling.
Finishing treatments can affect the workpiece surface in a wide variety of manners. Some clean and/or remove defects, such as scratches, pores, burrs, flash, or blemishes. Other processes improve or modify the surface appearance by improving smoothness, texture, or color. They can also improve corrosion resistance, wear
resistance, and/or reduce friction
. Coating
s are another type of finishing treatment that may be used to plate
an expensive or scarce material onto a less expensive base material.
, the machine tool
, the environment, and process variables. All of these variables can affect the surface integrity of the workpiece by producing:
Manufacturing
Manufacturing is the use of machines, tools and labor to produce goods for use or sale. The term may refer to a range of human activity, from handicraft to high tech, but is most commonly applied to industrial production, in which raw materials are transformed into finished goods on a large scale...
process. The term was coined by Michael Field and John F. Kahles in 1964.
The surface integrity of a workpiece or item changes the material's properties. The consequences of changes to surface integrity are a mechanical engineering
Mechanical engineering
Mechanical engineering is a discipline of engineering that applies the principles of physics and materials science for analysis, design, manufacturing, and maintenance of mechanical systems. It is the branch of engineering that involves the production and usage of heat and mechanical power for the...
design problem, but the preservation of those properties are a manufacturing consideration.
Surface integrity can have a great impact on a parts function; for example, Inconel
Inconel
Inconel is a registered trademark of Special Metals Corporation that refers to a family of austenitic nickel-chromium-based superalloys. Inconel alloys are typically used in high temperature applications. It is often referred to in English as "Inco"...
718 can have a fatigue limit
Fatigue limit
Fatigue limit, endurance limit, and fatigue strength are all expressions used to describe a property of materials: the amplitude of cyclic stress that can be applied to the material without causing fatigue failure. Ferrous alloys and titanium alloys have a distinct limit, an amplitude below which...
as high as 540 MPa (78,320.4 psi) after a gentle grinding
Grinding (abrasive cutting)
Grinding is an abrasive machining process that uses a grinding wheel as the cutting tool.A wide variety of machines are used for grinding:* Hand-cranked knife-sharpening stones * Handheld power tools such as angle grinders and die grinders...
or as low as 150 MPa (21,755.7 psi) after electrical discharge machining
Electrical discharge machining
Electric discharge machining , sometimes colloquially also referred to as spark machining, spark eroding, burning, die sinking or wire erosion, is a manufacturing process whereby a desired shape is obtained using electrical discharges...
(EDM).
Definition
There are two aspects to surface integrity: topography characteristics and surface layer characteristics. The topography is made up of surface roughness, wavinessWaviness
Waviness is the measure of the more widely spaced component of surface texture. It is a broader view of roughness because it is more strictly defined as "the irregularities whose spacing is greater than the roughness sampling length"...
, errors of form, and flaws. The surface layer characteristics that can change through processing are: plastic deformation, residual stress
Residual stress
Residual stresses are stresses that remain after the original cause of the stresses has been removed. They remain along a cross section of the component, even without the external cause. Residual stresses occur for a variety of reasons, including inelastic deformations and heat treatment...
es, cracks, hardness, overaging, phase changes, recrystallization
Recrystallization (metallurgy)
Recrystallization is a process by which deformed grains are replaced by a new set of undeformed grains that nucleate and grow until the original grains have been entirely consumed. Recrystallization is usually accompanied by a reduction in the strength and hardness of a material and a simultaneous...
, intergranular attack, and hydrogen embrittlement
Hydrogen embrittlement
Hydrogen embrittlement is the process by which various metals, most importantly high-strength steel, become brittle and fracture following exposure to hydrogen...
. When a traditional manufacturing process is used, such as machining
Machining
Conventional machining is a form of subtractive manufacturing, in which a collection of material-working processes utilizing power-driven machine tools, such as saws, lathes, milling machines, and drill presses, are used with a sharp cutting tool to physical remove material to achieve a desired...
, the surface layer sustains local plastic deformation.
The processes that affect surface integrity can be conveniently broken up into three classes: traditional processes, non-traditional processes, and finishing treatments. Traditional processes are defined as processes where the tool contacts the workpiece surface; for example: grinding
Grinding (abrasive cutting)
Grinding is an abrasive machining process that uses a grinding wheel as the cutting tool.A wide variety of machines are used for grinding:* Hand-cranked knife-sharpening stones * Handheld power tools such as angle grinders and die grinders...
, turning
Turning
Turning is the process whereby a single point cutting tool is parallel to the surface. It can be done manually, in a traditional form of lathe, which frequently requires continuous supervision by the operator, or by using a computer controlled and automated lathe which does not. This type of...
, and machining. These processes will only damage the surface integrity if the improper parameters are used, such as dull tools, too high feed speeds, improper coolant or lubrication, or incorrect grinding wheel hardness. Nontraditional processes are defined as processes where the tool does not contact the workpiece; examples of this type of process include EDM, electrochemical machining, and chemical milling. These processes will always change the surface integrity no matter how well controlled; for instance, they can leave a stress-free surface, a remelted surface, or excessive surface roughness. Finishing treatments are defined as processes that negate surface finishes imparted by traditional and non-traditional processes or improve the surface integrity. For example, residual stress can be removed via peening
Peening
Peening is the process of working a metal's surface to improve its material properties, usually by mechanical means such as hammer blows or by blasting with shot . Peening is normally a cold work process...
or roller burnishing
Roller burnishing
Roller burnishing is a method of cold working metal surfaces to induce compressive residual stresses and enhance surface roughness qualities. The tooling typically consists of a hardened sphere or cylindrical roller. These tools are pressed onto/across the part being processed...
or the recast layer left by EDMing can be removed via chemical milling.
Finishing treatments can affect the workpiece surface in a wide variety of manners. Some clean and/or remove defects, such as scratches, pores, burrs, flash, or blemishes. Other processes improve or modify the surface appearance by improving smoothness, texture, or color. They can also improve corrosion resistance, wear
Wear
In materials science, wear is erosion or sideways displacement of material from its "derivative" and original position on a solid surface performed by the action of another surface....
resistance, and/or reduce friction
Friction
Friction is the force resisting the relative motion of solid surfaces, fluid layers, and/or material elements sliding against each other. There are several types of friction:...
. Coating
Coating
Coating is a covering that is applied to the surface of an object, usually referred to as the substrate. In many cases coatings are applied to improve surface properties of the substrate, such as appearance, adhesion, wetability, corrosion resistance, wear resistance, and scratch resistance...
s are another type of finishing treatment that may be used to plate
Plating
Plating is a surface covering in which a metal is deposited on a conductive surface. Plating has been done for hundreds of years, but it is also critical for modern technology...
an expensive or scarce material onto a less expensive base material.
Variables
Manufacturing processes have five main variables: the workpiece, the toolTool
A tool is a device that can be used to produce an item or achieve a task, but that is not consumed in the process. Informally the word is also used to describe a procedure or process with a specific purpose. Tools that are used in particular fields or activities may have different designations such...
, the machine tool
Machine tool
A machine tool is a machine, typically powered other than by human muscle , used to make manufactured parts in various ways that include cutting or certain other kinds of deformation...
, the environment, and process variables. All of these variables can affect the surface integrity of the workpiece by producing:
- High temperatures involved in various machining processes
- Plastic deformation in the workpiece (residual stresses)
- Surface geometry (roughness, cracks, distortion)
- Chemical reactionChemical reactionA chemical reaction is a process that leads to the transformation of one set of chemical substances to another. Chemical reactions can be either spontaneous, requiring no input of energy, or non-spontaneous, typically following the input of some type of energy, such as heat, light or electricity...
s, especially between the tool and the workpiece