.gif)
Merlin (rocket engine)
Encyclopedia
Merlin is a rocket engine
developed by SpaceX
for use on its Falcon 1
and Falcon 9
rockets. Merlin uses RP-1
and liquid oxygen
as propellants in a gas-generator
power cycle. The Merlin engine is designed for sea recovery and reuse.
The injector at the heart of Merlin is of the pintle type that was first used in the Apollo Program for the lunar module landing engine.
Propellants are fed via a single shaft, dual impeller turbo-pump. The turbo-pump also provides high pressure fluid for the hydraulic actuators, which then recycles into the low pressure inlet. This eliminates the need for a separate hydraulic power system and means that thrust vector control failure by running out of hydraulic fluid is not possible. A third use of the turbo-pump is to provide power to pivot the turbine exhaust nozzle for roll control purposes.
is used on the Falcon 9 second stage. This engine differs from the Falcon 9 first stage variant in that it uses a larger exhaust nozzle optimized for vacuum operation and can be throttled between 60 and 100 percent.
carbon fiber
composite
nozzle, and produced 340 kN (77,000 lbf) of thrust.
The Merlin 1A flew only two times: First on 24 March 2006, when it caught fire and failed due to a fuel leak shortly after launch, and the second time on 21 March 2007, where it performed successfully. Both times the Merlin 1A was mounted on a Falcon 1
first stage.
The basic design of the first engine variant was based on the abandoned FASTRAC NASA project which developed the similar Fastrac rocket engine
at the end of 1990s.
launch vehicles, capable of producing 85000 lbf (378.1 kN) of thrust.
The Merlin 1B was enhanced over the 1A with a turbine
upgrade (from 1490 kW to 1860 kW).
Initial use of the Merlin 1B was to be on the Falcon 9
launch vehicle, on whose first stage there would have been a cluster of nine of these engines. Due to experience from the Falcon 1's first flight, the 1B was never used on a flight vehicle. SpaceX moved its Merlin development to the Merlin 1C, which is regeneratively cooled. Therefore the Merlin 1B was never in use on a launch vehicle.
The Merlin 1C uses a regeneratively cooled nozzle and combustion chamber. It was fired with a full mission duty firing of 170 seconds in November, 2007,
first flew on a mission in August 2008,
powered the "first privately-developed
liquid-fueled rocket to successfully reach orbit", Falcon 1 Flight 4
, in September 2008,
and powered the Falcon 9 on its maiden flight in June 2010.
As configured for use on Falcon 1 vehicles, the Merlin 1C had a sea level thrust of 78000 lbf (347 kN), a vacuum thrust of 90000 lbf (400.3 kN) and a vacuum specific impulse
of 304 seconds. In this configuration the engine consumed 300 lb (136.1 kg) of propellant per second. Tests have been conducted with a single Merlin 1C engine successfully running a total of 27 minutes (counting together the duration of the various tests), which equals ten complete Falcon 1
flights.
As configured for use on the newer Falcon 1e and Falcon 9 vehicles, the Merlin 1C has a sea level thrust of 125000 lbf (556 kN), and an isp of 300.
A Merlin 1C was first used as part of the unsuccessful third attempt to launch a Falcon 1. In discussing the failure, Elon Musk noted, "The flight of our first stage, with the new Merlin 1C engine that will be used in Falcon 9, was picture perfect." The Merlin 1C was used in the successful fourth flight
of Falcon 1 on September 28, 2008.
The SpaceX turbopump was an entirely new, clean sheet design. Although the design has some similarities to the FASTRAC turbopump, it is clearly not the same design, and this can be seen in the external design and internal design. The flange location, housing external shape and the lack of a separate inducer piece on the LOX end pump are among the obvious differences. Both Turbopumps were designed by the same company, Barber-Nichols, and this is the only factor that makes their designs appear similar. The NASA FASTRAC engine also has less than half of the thrust capability (60,000 vs. 138,000 lbf).
alloy expansion nozzle is radiatively cooled. The engine delivers a vacuum thrust of 92500 lbf (411.5 kN) and a vacuum specific impulse
of 342 seconds. The first production Merlin Vacuum engine underwent a full duration orbital insertion firing (329 seconds) of the integrated Falcon 9 second stage on January 2, 2010. It was flown on the second stage for the inaugural Falcon 9 flight on June 4, 2010. At full power the Merlin Vacuum engine operates with the greatest efficiency ever for an American-made hydrocarbon rocket engine.
An interesting unplanned test of a modified Merlin Vacuum engine was made in December 2010. Shortly before the scheduled second flight of the Falcon 9
, two cracks were discovered in the 9 feet (2.7 m)-long Merlin Vacuum niobium alloy sheet nozzle. The engineering solution was to cut off the lower 4 feet (1.2 m) of the nozzle, and launch two days later, as the extra performance that would have been gained from the longer nozzle was not necessary to meet the objectives of the mission. Even with the shortened nozzle, the engine placed the second-stage into an orbit of 11000 kilometres (6,835.1 mi) altitude.
At the 2011 AIAA Propulsion Conference SpaceX's Tom Mueller
revealed that the engine would have a vacuum thrust of 155000 lbf (689.5 kN), a vacuum specific impulse (Isp) of 310s, an increased expansion ratio of 16, vs. the previous 14.5 of the Merlin 1C, and chamber pressure in the "sweet spot" of 1410 psi (9.7 MPa). A new feature to the engine would be the ability to throttle from 100% to 70%.
second stage.
/rocket propellant-fueled engine, capable of a projected 1700000 lbf (7,562 kN) of thrust at sea level and 1920000 lbf (8,540.6 kN) in a vacuum and would provide the power for conceptual super-heavy-lift launch vehicles from SpaceX, which Markusic dubbed Falcon X and Falcon XX. Such a capability would result in an engine with more thrust than the F-1 engine
s used on the Saturn V
.
Slated to be introduced on more capable variants of the Falcon 9 Heavy, the Merlin 2 “could be qualified in three years for $1 billion,” Markusic says. By mid-August, the SpaceX CEO Elon Musk
clarified that while the Merlin 2 engine architecture was a key element of any effort SpaceX would make toward their objective of "super-heavy lift" launch vehicles—and that SpaceX did indeed want to "move toward super heavy lift"—the specific potential design configurations of the particular launch vehicles shown by Markusic at the propulsion conference were merely conceptual "brainstorming ideas", just a "bunch of ideas for discussion."
was a SpaceX rocket engine design concept for a higher performance upper stage for the Falcon 9
launch vehicle. The engine would be powered by liquid hydrogen
and liquid oxygen
,
rather than the RP-1
kerosene and liquid oxygen used in the Block 1 Falcon 9 upper stage, enabling much greater mass to be boosted into orbit. If implemented, Raptor would replace the Merlin Vacuum engine in the current Falcon 9 on high performance launches.
Rocket engine
A rocket engine, or simply "rocket", is a jet engineRocket Propulsion Elements; 7th edition- chapter 1 that uses only propellant mass for forming its high speed propulsive jet. Rocket engines are reaction engines and obtain thrust in accordance with Newton's third law...
developed by SpaceX
SpaceX
Space Exploration Technologies Corporation, or more popularly and informally known as SpaceX, is an American space transport company that operates out of Hawthorne, California...
for use on its Falcon 1
Falcon 1
The Falcon 1 is a partially reusable launch system designed and manufactured by SpaceX, a space transportation company in Hawthorne, California. The two-stage-to-orbit rocket uses LOX/RP-1 for both stages, the first powered by a single Merlin engine and the second powered by a single Kestrel engine...
and Falcon 9
Falcon 9
Falcon 9 is a rocket-powered spaceflight launch system designed and manufactured by SpaceX. Both stages of its two-stage-to-orbit vehicle use liquid oxygen and rocket-grade kerosene propellants...
rockets. Merlin uses RP-1
RP-1
RP-1 is a highly refined form of kerosene outwardly similar to jet fuel, used as a rocket fuel. Although having a lower specific impulse than liquid hydrogen , RP-1 is cheaper, can be stored at room temperature, is far less of an explosive hazard and is far denser...
and liquid oxygen
Liquid oxygen
Liquid oxygen — abbreviated LOx, LOX or Lox in the aerospace, submarine and gas industries — is one of the physical forms of elemental oxygen.-Physical properties:...
as propellants in a gas-generator
Gas-generator cycle (rocket)
The gas generator cycle is a power cycle of a bipropellant rocket engine. Some of the propellant is burned in a gas-generator and the resulting hot gas is used to power the engine's pumps. The gas is then exhausted...
power cycle. The Merlin engine is designed for sea recovery and reuse.
The injector at the heart of Merlin is of the pintle type that was first used in the Apollo Program for the lunar module landing engine.
Propellants are fed via a single shaft, dual impeller turbo-pump. The turbo-pump also provides high pressure fluid for the hydraulic actuators, which then recycles into the low pressure inlet. This eliminates the need for a separate hydraulic power system and means that thrust vector control failure by running out of hydraulic fluid is not possible. A third use of the turbo-pump is to provide power to pivot the turbine exhaust nozzle for roll control purposes.
Variants
Three versions of the Merlin 1C engine are in production. The Merlin engine for Falcon 1 has a movable turbo-pump exhaust assembly which is used to provide roll control by vectoring the exhaust. The Merlin engine for the Falcon 9 first stage is nearly identical to the variant used for the Falcon 1 except that the turbo-pump exhaust assembly is not movable. Finally, the Merlin vacuumVacuum
In everyday usage, vacuum is a volume of space that is essentially empty of matter, such that its gaseous pressure is much less than atmospheric pressure. The word comes from the Latin term for "empty". A perfect vacuum would be one with no particles in it at all, which is impossible to achieve in...
is used on the Falcon 9 second stage. This engine differs from the Falcon 9 first stage variant in that it uses a larger exhaust nozzle optimized for vacuum operation and can be throttled between 60 and 100 percent.
Merlin 1A
The initial version, the Merlin 1A, used an inexpensive, expendable, ablatively cooledAblation
Ablation is removal of material from the surface of an object by vaporization, chipping, or other erosive processes. This occurs in spaceflight during ascent and atmospheric reentry, glaciology, medicine, and passive fire protection.-Spaceflight:...
carbon fiber
Carbon fiber
Carbon fiber, alternatively graphite fiber, carbon graphite or CF, is a material consisting of fibers about 5–10 μm in diameter and composed mostly of carbon atoms. The carbon atoms are bonded together in crystals that are more or less aligned parallel to the long axis of the fiber...
composite
Composite material
Composite materials, often shortened to composites or called composition materials, are engineered or naturally occurring materials made from two or more constituent materials with significantly different physical or chemical properties which remain separate and distinct at the macroscopic or...
nozzle, and produced 340 kN (77,000 lbf) of thrust.
The Merlin 1A flew only two times: First on 24 March 2006, when it caught fire and failed due to a fuel leak shortly after launch, and the second time on 21 March 2007, where it performed successfully. Both times the Merlin 1A was mounted on a Falcon 1
Falcon 1
The Falcon 1 is a partially reusable launch system designed and manufactured by SpaceX, a space transportation company in Hawthorne, California. The two-stage-to-orbit rocket uses LOX/RP-1 for both stages, the first powered by a single Merlin engine and the second powered by a single Kestrel engine...
first stage.
The basic design of the first engine variant was based on the abandoned FASTRAC NASA project which developed the similar Fastrac rocket engine
Fastrac (engine)
Fastrac or alternatively MC-1 engine was a pump-fed liquid rocket engine developed by NASA for use on small inexpensive, expendable rockets...
at the end of 1990s.
Merlin 1B
The Merlin 1B rocket engine was an upgraded version of the Merlin engine developed by SpaceX for its Falcon 1Falcon 1
The Falcon 1 is a partially reusable launch system designed and manufactured by SpaceX, a space transportation company in Hawthorne, California. The two-stage-to-orbit rocket uses LOX/RP-1 for both stages, the first powered by a single Merlin engine and the second powered by a single Kestrel engine...
launch vehicles, capable of producing 85000 lbf (378.1 kN) of thrust.
The Merlin 1B was enhanced over the 1A with a turbine
Turbine
A turbine is a rotary engine that extracts energy from a fluid flow and converts it into useful work.The simplest turbines have one moving part, a rotor assembly, which is a shaft or drum with blades attached. Moving fluid acts on the blades, or the blades react to the flow, so that they move and...
upgrade (from 1490 kW to 1860 kW).
Initial use of the Merlin 1B was to be on the Falcon 9
Falcon 9
Falcon 9 is a rocket-powered spaceflight launch system designed and manufactured by SpaceX. Both stages of its two-stage-to-orbit vehicle use liquid oxygen and rocket-grade kerosene propellants...
launch vehicle, on whose first stage there would have been a cluster of nine of these engines. Due to experience from the Falcon 1's first flight, the 1B was never used on a flight vehicle. SpaceX moved its Merlin development to the Merlin 1C, which is regeneratively cooled. Therefore the Merlin 1B was never in use on a launch vehicle.
Merlin 1C
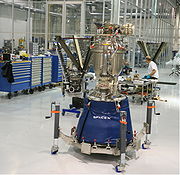
first flew on a mission in August 2008,
powered the "first privately-developed
Private spaceflight
Private spaceflight is flight above Earth altitude conducted by and paid for by an entity other than a government. In the early decades of the Space Age, the government space agencies of the Soviet Union and United States pioneered space technology augmented by collaboration with affiliated design...
liquid-fueled rocket to successfully reach orbit", Falcon 1 Flight 4
Falcon 1 Flight 4
Ratsat, was a 165-kilogram non-functional boilerplate spacecraft used as a mass simulator on the fourth flight of the Falcon 1 rocket. The non-functional payload was carried due to the Falcon 1 having failed on all of the three previous launches...
, in September 2008,
and powered the Falcon 9 on its maiden flight in June 2010.
As configured for use on Falcon 1 vehicles, the Merlin 1C had a sea level thrust of 78000 lbf (347 kN), a vacuum thrust of 90000 lbf (400.3 kN) and a vacuum specific impulse
Specific impulse
Specific impulse is a way to describe the efficiency of rocket and jet engines. It represents the derivative of the impulse with respect to amount of propellant used, i.e., the thrust divided by the amount of propellant used per unit time. If the "amount" of propellant is given in terms of mass ,...
of 304 seconds. In this configuration the engine consumed 300 lb (136.1 kg) of propellant per second. Tests have been conducted with a single Merlin 1C engine successfully running a total of 27 minutes (counting together the duration of the various tests), which equals ten complete Falcon 1
Falcon 1
The Falcon 1 is a partially reusable launch system designed and manufactured by SpaceX, a space transportation company in Hawthorne, California. The two-stage-to-orbit rocket uses LOX/RP-1 for both stages, the first powered by a single Merlin engine and the second powered by a single Kestrel engine...
flights.
As configured for use on the newer Falcon 1e and Falcon 9 vehicles, the Merlin 1C has a sea level thrust of 125000 lbf (556 kN), and an isp of 300.
A Merlin 1C was first used as part of the unsuccessful third attempt to launch a Falcon 1. In discussing the failure, Elon Musk noted, "The flight of our first stage, with the new Merlin 1C engine that will be used in Falcon 9, was picture perfect." The Merlin 1C was used in the successful fourth flight
Falcon 1 Flight 4
Ratsat, was a 165-kilogram non-functional boilerplate spacecraft used as a mass simulator on the fourth flight of the Falcon 1 rocket. The non-functional payload was carried due to the Falcon 1 having failed on all of the three previous launches...
of Falcon 1 on September 28, 2008.
The SpaceX turbopump was an entirely new, clean sheet design. Although the design has some similarities to the FASTRAC turbopump, it is clearly not the same design, and this can be seen in the external design and internal design. The flange location, housing external shape and the lack of a separate inducer piece on the LOX end pump are among the obvious differences. Both Turbopumps were designed by the same company, Barber-Nichols, and this is the only factor that makes their designs appear similar. The NASA FASTRAC engine also has less than half of the thrust capability (60,000 vs. 138,000 lbf).
Merlin Vacuum (1C)
On March 10, 2009 a SpaceX press release announced successful testing of the Merlin Vacuum engine. A variant of the 1C engine, Merlin Vacuum features a larger exhaust section and a significantly larger expansion nozzle to maximize the engine's efficiency in the vacuum of space. Its combustion chamber is regeneratively cooled while the 9 feet (2.7 m)-long niobiumNiobium
Niobium or columbium , is a chemical element with the symbol Nb and atomic number 41. It's a soft, grey, ductile transition metal, which is often found in the pyrochlore mineral, the main commercial source for niobium, and columbite...
alloy expansion nozzle is radiatively cooled. The engine delivers a vacuum thrust of 92500 lbf (411.5 kN) and a vacuum specific impulse
Specific impulse
Specific impulse is a way to describe the efficiency of rocket and jet engines. It represents the derivative of the impulse with respect to amount of propellant used, i.e., the thrust divided by the amount of propellant used per unit time. If the "amount" of propellant is given in terms of mass ,...
of 342 seconds. The first production Merlin Vacuum engine underwent a full duration orbital insertion firing (329 seconds) of the integrated Falcon 9 second stage on January 2, 2010. It was flown on the second stage for the inaugural Falcon 9 flight on June 4, 2010. At full power the Merlin Vacuum engine operates with the greatest efficiency ever for an American-made hydrocarbon rocket engine.
An interesting unplanned test of a modified Merlin Vacuum engine was made in December 2010. Shortly before the scheduled second flight of the Falcon 9
Falcon 9
Falcon 9 is a rocket-powered spaceflight launch system designed and manufactured by SpaceX. Both stages of its two-stage-to-orbit vehicle use liquid oxygen and rocket-grade kerosene propellants...
, two cracks were discovered in the 9 feet (2.7 m)-long Merlin Vacuum niobium alloy sheet nozzle. The engineering solution was to cut off the lower 4 feet (1.2 m) of the nozzle, and launch two days later, as the extra performance that would have been gained from the longer nozzle was not necessary to meet the objectives of the mission. Even with the shortened nozzle, the engine placed the second-stage into an orbit of 11000 kilometres (6,835.1 mi) altitude.
Merlin 1D
The Merlin 1D is currently in development, and was originally (April 2011) designed for a sea level thrust of 140000 lbf (622.8 kN).At the 2011 AIAA Propulsion Conference SpaceX's Tom Mueller
revealed that the engine would have a vacuum thrust of 155000 lbf (689.5 kN), a vacuum specific impulse (Isp) of 310s, an increased expansion ratio of 16, vs. the previous 14.5 of the Merlin 1C, and chamber pressure in the "sweet spot" of 1410 psi (9.7 MPa). A new feature to the engine would be the ability to throttle from 100% to 70%.
Merlin Vacuum (1D)
A vacuum version of the Merlin 1D engine is planned for the Falcon HeavyFalcon Heavy
Falcon Heavy, previously known as the Falcon 9 Heavy, is a spaceflight launch system that uses rocket engines currently being designed and manufactured by SpaceX. Both stages of the two-stage-to-orbit vehicles use liquid oxygen and rocket-grade kerosene propellants...
second stage.
Production
, SpaceX is producing Merlin engines at the rate of eight per month, with the "eventual plan" to raise production to 400 engines per year.Merlin 2
At the AIAA Joint Propulsion conference on July 30, 2010 SpaceX McGregor rocket development facility director Tom Markusic shared some information from the initial stages of planning for a new engine. SpaceX’s Merlin 2 LOXLox
Lox is salmon fillet that has been cured. In its most popular form, it is thinly sliced—less than in thickness—and, typically, served on a bagel, often with cream cheese, onion, tomato, cucumber and capers...
/rocket propellant-fueled engine, capable of a projected 1700000 lbf (7,562 kN) of thrust at sea level and 1920000 lbf (8,540.6 kN) in a vacuum and would provide the power for conceptual super-heavy-lift launch vehicles from SpaceX, which Markusic dubbed Falcon X and Falcon XX. Such a capability would result in an engine with more thrust than the F-1 engine
F-1 (rocket engine)
The F-1 is a rocket engine developed by Rocketdyne and used in the Saturn V. Five F-1 engines were used in the S-IC first stage of each Saturn V, which served as the main launch vehicle in the Apollo program. The F-1 is still the most powerful single-chamber liquid-fueled rocket engine ever...
s used on the Saturn V
Saturn V
The Saturn V was an American human-rated expendable rocket used by NASA's Apollo and Skylab programs from 1967 until 1973. A multistage liquid-fueled launch vehicle, NASA launched 13 Saturn Vs from the Kennedy Space Center, Florida with no loss of crew or payload...
.
Slated to be introduced on more capable variants of the Falcon 9 Heavy, the Merlin 2 “could be qualified in three years for $1 billion,” Markusic says. By mid-August, the SpaceX CEO Elon Musk
Elon Musk
Elon Musk is an American engineer and entrepreneur heritage best known for co-founding PayPal, SpaceX and Tesla Motors. He is currently the CEO and CTO of SpaceX, CEO and Product Architect of Tesla Motors and Chairman of SolarCity...
clarified that while the Merlin 2 engine architecture was a key element of any effort SpaceX would make toward their objective of "super-heavy lift" launch vehicles—and that SpaceX did indeed want to "move toward super heavy lift"—the specific potential design configurations of the particular launch vehicles shown by Markusic at the propulsion conference were merely conceptual "brainstorming ideas", just a "bunch of ideas for discussion."
Raptor
, RaptorRaptor (rocket stage)
,Raptor is a rocket engine design concept by SpaceX for a higher performance upper stage for the Falcon 9 launch vehicle. The engine would be powered by liquid hydrogen and liquid oxygen,...
was a SpaceX rocket engine design concept for a higher performance upper stage for the Falcon 9
Falcon 9
Falcon 9 is a rocket-powered spaceflight launch system designed and manufactured by SpaceX. Both stages of its two-stage-to-orbit vehicle use liquid oxygen and rocket-grade kerosene propellants...
launch vehicle. The engine would be powered by liquid hydrogen
Liquid hydrogen
Liquid hydrogen is the liquid state of the element hydrogen. Hydrogen is found naturally in the molecular H2 form.To exist as a liquid, H2 must be pressurized above and cooled below hydrogen's Critical point. However, for hydrogen to be in a full liquid state without boiling off, it needs to be...
and liquid oxygen
Liquid oxygen
Liquid oxygen — abbreviated LOx, LOX or Lox in the aerospace, submarine and gas industries — is one of the physical forms of elemental oxygen.-Physical properties:...
,
rather than the RP-1
RP-1
RP-1 is a highly refined form of kerosene outwardly similar to jet fuel, used as a rocket fuel. Although having a lower specific impulse than liquid hydrogen , RP-1 is cheaper, can be stored at room temperature, is far less of an explosive hazard and is far denser...
kerosene and liquid oxygen used in the Block 1 Falcon 9 upper stage, enabling much greater mass to be boosted into orbit. If implemented, Raptor would replace the Merlin Vacuum engine in the current Falcon 9 on high performance launches.
Merlin 1C Engine specifications
Current published ratings for Merlin 1C variant:- Sea level thrust: 556 kN (125,000 lbf)
- Vacuum thrust: 616 kN (138,400 lbf)
- Chamber pressure: 6.77 MPaMPA-Academic degrees:* Master of Professional Accountancy* Master of Public Administration* Master of Public Affairs* Master of Physician's Assistant-Chemicals:* Medroxyprogesterone acetate, also known by the brand name Depo-Provera* Morpholide of pelargonic acid...
(890 psi) - Sea level specific impulse: 275 s (2.6 kN·s/kg)
- Vacuum specific impulse: 304 s (3.0 kN·s/kg)
- Thrust-to-weight ratio (fully accounted): 96
- Fuel: RP-1 (rocket grade kerosene)
- Oxidizer: Liquid oxygen
See also
- Rocket engineRocket engineA rocket engine, or simply "rocket", is a jet engineRocket Propulsion Elements; 7th edition- chapter 1 that uses only propellant mass for forming its high speed propulsive jet. Rocket engines are reaction engines and obtain thrust in accordance with Newton's third law...
- Draco (rocket engine)Draco (rocket engine)Draco is a small hypergolic rocket engine designed by SpaceX for use on their Dragon spacecraftand the upper stage of their Falcon 9 rocket.-Performance and use:...
– SpaceX orbital thruster - Kestrel (rocket engine)Kestrel (rocket engine)The Kestrel engine is an LOX/RP-1 pressure-fed rocket engine. The Kestrel engine was developed by SpaceX for upper stage use on the Falcon 1 rocket....
– SpaceX small upper stage engine for Falcon-1 - RS-27A (rocket engine)RS-27A (rocket engine)The RS-27A is a liquid-fuel rocket engine developed by Rocketdyne for use on the first stage of the Delta II and Delta III launch vehicles. It provides 1.05 meganewtons of thrust burning RP-1 and LOX in a gas-generator cycle...
– RP-1 engine currently used in the US Delta IIDelta IIDelta II was an American space launch system, originally designed and built by McDonnell Douglas. Delta II is part of the Delta rocket family and was in service from 1989 until November 1, 2011...
launcher - RD-180 – RP-1 engine currently used in the first-stage of the US Atlas VAtlas VAtlas V is an active expendable launch system in the Atlas rocket family. Atlas V was formerly operated by Lockheed Martin, and is now operated by the Lockheed Martin-Boeing joint venture United Launch Alliance...
launcher - RD-191RD-191The RD-191 is a high performance single-combustion chamber rocket engine, developed in Russia. It is derived from the RD-170 originally used in the Energia launcher....
– contemporary Russian RP-1 engine - NK-33NK-33The NK-33 and NK-43 are rocket engines designed and built in the late 1960s and early 1970s by the Kuznetsov Design Bureau. They were intended for the ill-fated Soviet N-1 rocket moon shot. The NK-33 engine achieves the highest thrust-to-weight ratio of any Earth-launchable rocket engine, whilst...
– RP-1 engine used on Soviet N1, currently slated for use by Orbital Sciences in Taurus IITaurus IITaurus II is an expendable launch system being developed by Orbital Sciences Corporation. It is a two stage vehicle designed to launch payloads weighing up to into low-Earth orbit...
launcher - F-1 (rocket engine)F-1 (rocket engine)The F-1 is a rocket engine developed by Rocketdyne and used in the Saturn V. Five F-1 engines were used in the S-IC first stage of each Saturn V, which served as the main launch vehicle in the Apollo program. The F-1 is still the most powerful single-chamber liquid-fueled rocket engine ever...
– main engine of the Saturn VSaturn VThe Saturn V was an American human-rated expendable rocket used by NASA's Apollo and Skylab programs from 1967 until 1973. A multistage liquid-fueled launch vehicle, NASA launched 13 Saturn Vs from the Kennedy Space Center, Florida with no loss of crew or payload...
moon rocket