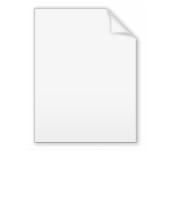
History of manufactured gas
Encyclopedia
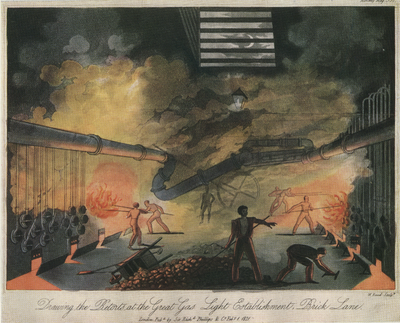
Analytical chemistry
Analytical chemistry is the study of the separation, identification, and quantification of the chemical components of natural and artificial materials. Qualitative analysis gives an indication of the identity of the chemical species in the sample and quantitative analysis determines the amount of...
and pneumatic chemistry
Pneumatic chemistry
Pneumatic chemistry is a term most-closely identified with an area of scientific research of the seventeenth, eighteenth, and early nineteenth centuries. Important goals of this work were an understanding of the physical properties of gases and how they relate to chemical reactions and,...
in the eighteenth century. The manufacturing process typically consisted of the gasification
Gasification
Gasification is a process that converts organic or fossil based carbonaceous materials into carbon monoxide, hydrogen, carbon dioxide and methane. This is achieved by reacting the material at high temperatures , without combustion, with a controlled amount of oxygen and/or steam...
of combustible materials, almost always coal, but also wood and oil. The coal was gasified by heating the coal in enclosed ovens. Coal heated in an oxygen-poor atmosphere gives off gases, including hydrogen
Hydrogen
Hydrogen is the chemical element with atomic number 1. It is represented by the symbol H. With an average atomic weight of , hydrogen is the lightest and most abundant chemical element, constituting roughly 75% of the Universe's chemical elemental mass. Stars in the main sequence are mainly...
, methane
Methane
Methane is a chemical compound with the chemical formula . It is the simplest alkane, the principal component of natural gas, and probably the most abundant organic compound on earth. The relative abundance of methane makes it an attractive fuel...
, and ethylene
Ethylene
Ethylene is a gaseous organic compound with the formula . It is the simplest alkene . Because it contains a carbon-carbon double bond, ethylene is classified as an unsaturated hydrocarbon. Ethylene is widely used in industry and is also a plant hormone...
, all of which can be burnt for heating and lighting purposes. Coal gas
Coal gas
Coal gas is a flammable gaseous fuel made by the destructive distillation of coal containing a variety of calorific gases including hydrogen, carbon monoxide, methane and volatile hydrocarbons together with small quantities of non-calorific gases such as carbon dioxide and nitrogen...
, however, also contains significant quantities of sulfur
Sulfur
Sulfur or sulphur is the chemical element with atomic number 16. In the periodic table it is represented by the symbol S. It is an abundant, multivalent non-metal. Under normal conditions, sulfur atoms form cyclic octatomic molecules with chemical formula S8. Elemental sulfur is a bright yellow...
and ammonia
Ammonia
Ammonia is a compound of nitrogen and hydrogen with the formula . It is a colourless gas with a characteristic pungent odour. Ammonia contributes significantly to the nutritional needs of terrestrial organisms by serving as a precursor to food and fertilizers. Ammonia, either directly or...
compounds, as well as heavy hydrocarbons, and so the gas needed to be purified before it could be used in most contexts.
As eighteenth century natural philosophers and practical chemists understood the nature and properties of gases better during the Chemical Revolution
Chemical Revolution
The chemical revolution, also called the first chemical revolution, denotes the reformulation of chemistry based on the Law of Conservation of Matter and the oxygen theory of combustion. It was centered on the work of French chemist Antoine Lavoisier...
, they also realized that gas could be produced, purified, and stored, used in a variety of ways. The pioneering attempts at manufacturing gas occurred in this context.
The first attempts to manufacture gas in a commercial way were made in the period 1795–1805 in France by Philippe Lebon, and in England by William Murdoch
William Murdoch
William Murdoch was a Scottish engineer and long-term inventor.Murdoch was employed by the firm of Boulton and Watt and worked for them in Cornwall, as a steam engine erector for ten years, spending most of the rest of his life in Birmingham, England.He was the inventor of the oscillating steam...
. Although precursors can be found, it was these two engineers who elaborated the technology with commercial applications in mind. Frederick Winsor was the key player behind the creation of the first gas utility, the London-based Gas Light and Coke Company
Gas Light and Coke Company
The Gas Light and Coke Company , was a company that made and supplied coal gas and coke. The Company was located on Horseferry Road in Westminster, London...
, incorporated by royal charter in April 1812.
Many other manufactured gas utilities were founded first in England, and then in the rest of Europe and North America in the 1820s. The technology increased in scale. After a period of competition, the business model of the gas industry matured in monopolies, where a single company provided gas in a given zone. The ownership of the companies varied from outright municipal ownership, such as in Manchester, to completely private corporations, such as in London and most North American cities. Gas companies thrived during most of the nineteenth century, usually returning good profits to their shareholders, but were also the subject of many complaints over price.
In the second half of the 19th century, the gas industry diversified out of lighting and into heat and cooking. The threat from electrical light in the later 1870s and 1880s drove this trend strongly. The gas industry did not cede the lighting market to electricity immediately, as the invention of the Welsbach mantle in the late 1880s dramatically increased the luminosity of gas flames, and gas remained competitive with electricity. Other technological developments in the late nineteenth century include the use of water gas and power stoking, although these were not universally adopted.
In the 1890s, pipelines
Pipeline transport
Pipeline transport is the transportation of goods through a pipe. Most commonly, liquids and gases are sent, but pneumatic tubes that transport solid capsules using compressed air are also used....
from natural gas field in Texas and Oklahoma were built to Chicago and other cities, and natural gas was used to supplement manufactured gas supplies, eventually completely displacing it. Gas ceased to be manufactured in North America by 1966(with the exception of Indianapolis and Honolulu), while it continued in Europe until the 1980s. Manufactured gas is experiencing a resurgence as energy utilities look towards coal gasification once again as a potentially cleaner way of generating power from coal.
Precursors
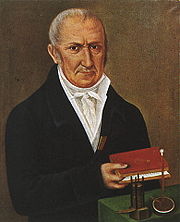
Stephen Hales
Stephen Hales, FRS was an English physiologist, chemist and inventor.Hales studied the role of air and water in the maintenance of both plant and animal life. He gave accurate accounts of the movements of water in plants, and demonstrated that plants absorb air...
, Joseph Black
Joseph Black
Joseph Black FRSE FRCPE FPSG was a Scottish physician and chemist, known for his discoveries of latent heat, specific heat, and carbon dioxide. He was professor of Medicine at University of Glasgow . James Watt, who was appointed as philosophical instrument maker at the same university...
, Joseph Priestley
Joseph Priestley
Joseph Priestley, FRS was an 18th-century English theologian, Dissenting clergyman, natural philosopher, chemist, educator, and political theorist who published over 150 works...
, and Antoine-Laurent Lavoisier, and others. Until the eighteenth century, gas was not recognized as a separated state of matter. Rather, while some of the mechanical properties of gases were understood, as typified by Robert Boyle
Robert Boyle
Robert Boyle FRS was a 17th century natural philosopher, chemist, physicist, and inventor, also noted for his writings in theology. He has been variously described as English, Irish, or Anglo-Irish, his father having come to Ireland from England during the time of the English plantations of...
's experiments and the development of the air pump
Air pump
An air pump is a device for pushing air. Examples include a bicycle pump, pumps that are used to aerate an aquarium or a pond via an airstone; a gas compressor used to power a pneumatic tool, air horn or pipe organ; a bellows used to encourage a fire; and a vacuum pump.The first effective air pump...
, its chemical properties were not. Gases were regarded in keeping the Aristotelean tradition of four elements as being air, one of the four fundamental elements. The different sorts of airs, such as putrid airs or inflammable air, were looked upon as atmospheric air
Earth's atmosphere
The atmosphere of Earth is a layer of gases surrounding the planet Earth that is retained by Earth's gravity. The atmosphere protects life on Earth by absorbing ultraviolet solar radiation, warming the surface through heat retention , and reducing temperature extremes between day and night...
with some impurities, much like muddied water.
After Joseph Black realized that carbon dioxide
Carbon dioxide
Carbon dioxide is a naturally occurring chemical compound composed of two oxygen atoms covalently bonded to a single carbon atom...
was in fact a different sort of gas altogether from atmospheric air, other gases were identified, including hydrogen
Hydrogen
Hydrogen is the chemical element with atomic number 1. It is represented by the symbol H. With an average atomic weight of , hydrogen is the lightest and most abundant chemical element, constituting roughly 75% of the Universe's chemical elemental mass. Stars in the main sequence are mainly...
by Henry Cavendish
Henry Cavendish
Henry Cavendish FRS was a British scientist noted for his discovery of hydrogen or what he called "inflammable air". He described the density of inflammable air, which formed water on combustion, in a 1766 paper "On Factitious Airs". Antoine Lavoisier later reproduced Cavendish's experiment and...
in 1766. Alessandro Volta
Alessandro Volta
Count Alessandro Giuseppe Antonio Anastasio Gerolamo Umberto Volta was a Lombard physicist known especially for the invention of the battery in 1800.-Early life and works:...
expanded the list with his discovery of methane in 1776. It had also been known for a long time that inflammable gases could be produced from most combustible materials, such as coal and wood, through the process of distillation
Distillation
Distillation is a method of separating mixtures based on differences in volatilities of components in a boiling liquid mixture. Distillation is a unit operation, or a physical separation process, and not a chemical reaction....
. Stephen Hales, for example, had written about the phenomenon in the Vegetable Staticks in 1722. In the last two decades of the eighteenth century, as more gases were being discovered and the techniques and instruments of pneumatic chemistry became more sophisticated, and number of natural philosophers and engineers thought about using gases in medical and industrial applications. One of first such uses was ballooning
Balloon (aircraft)
A balloon is a type of aircraft that remains aloft due to its buoyancy. A balloon travels by moving with the wind. It is distinct from an airship, which is a buoyant aircraft that can be propelled through the air in a controlled manner....
beginning in 1783, but other uses soon followed.
One of the results of the ballooning craze of 1783–1784 was the first implementation of lighting by manufactured gas. A professor of natural philosophy at the University of Louvain
Catholic University of Leuven
The Catholic University of Leuven, or of Louvain, was the largest, oldest and most prominent university in Belgium. The university was founded in 1425 as the University of Leuven by John IV, Duke of Brabant and approved by a Papal bull by Pope Martin V.During France's occupation of Belgium in the...
Jan Pieter Minckeleers and two of his colleagues were asked by their patron, the Duke of Arenberg
Arenberg
Arenberg, also spelled as Aremberg or Ahremberg, is a historic county, principality and finally duchy located in modern Germany. The Dukes of Arenberg remain a prominent Belgian aristocratic family.- History :...
, to investigate ballooning. They did so, building apparatus to generate lighter than air inflammable gases from coal and other inflammable substances. In 1785 Minckeleers used some of this apparatus to gasify coal to light his lecture hall at the university. He did not extend gas lighting much beyond this, and when he was forced to flee Leuven during the Brabant Revolution
Brabant Revolution
The Brabant Revolution took place between January 1789 and December 1790, when a popular revolt broke in the Austrian Netherlands against the unpopular reforms of the Emperor Joseph II...
, he abandoned the project altogether.
Philippe Lebon and the Thermolamp
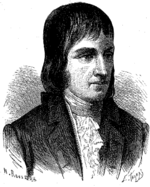
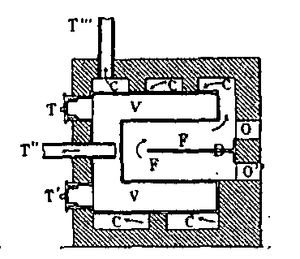
Although the themolamp received some interest in France, it was in Germany that the interest was the greatest. A number of books and articles were written on the subject in the period 1802–1812. There were also thermolamps designed and built in Germany, the most important of which were by Zachaus Winzler, a Moravian chemist who ran a salpetre factory in Blansko. Under the patronage of the aristocratic zu Salm family, he built a large one in Bruno. He later moved to Vienna to further his work there. The thermolamp, however, was used primarily for making charcoal and not for the production of gases.
William Murdock and Boulton & Watt
.jpg)
William Murdoch
William Murdoch was a Scottish engineer and long-term inventor.Murdoch was employed by the firm of Boulton and Watt and worked for them in Cornwall, as a steam engine erector for ten years, spending most of the rest of his life in Birmingham, England.He was the inventor of the oscillating steam...
(sometimes Murdock) (1754–1839) was an engineer working for the firm of Boulton & Watt, when, while investigating distillation processes sometime in 1792–1794, he also started to use coal gas for illumination. He was living in Redruth
Redruth
Redruth is a town and civil parish traditionally in the Penwith Hundred in Cornwall, United Kingdom. It has a population of 12,352. Redruth lies approximately at the junction of the A393 and A3047 roads, on the route of the old London to Land's End trunk road , and is approximately west of...
in Cornwall at the time, and made some small scale experiments with lighting his own house with coal gas. He soon thereafter dropped the subject until 1798, when he moved to Birmingham
Birmingham
Birmingham is a city and metropolitan borough in the West Midlands of England. It is the most populous British city outside the capital London, with a population of 1,036,900 , and lies at the heart of the West Midlands conurbation, the second most populous urban area in the United Kingdom with a...
to work at Boulton & Watt's home base of Soho
Soho, Birmingham
Soho is an area in north west Birmingham, approximately 2 miles from the City Centre on the A41, which until 1911 formed part of Handsworth District. Soho is also a ward within the council constituency of Ladywood...
. Boulton & Watt then instigate another small scale series of experiments, but with ongoing patent litigation and their main line of business, steam engines, to attend to, the subject was dropped once again. Gregory Watt, James Watt's second son, while traveling in Europe saw Lebon's demonstrations and wrote a letter to his brother, James Watt junior, informing him of this potential competitor. This prompted James Watt junior to begin a gaslight development program at Boulton & Watt that would scale up the technology and lead to the first commercial applications of gaslight.
After an initial installation at the Soho Foundry in 1803–1804, Boulton & Watt prepared an apparatus for the textile firm of Philips & Lee in Salford near Manchester in 1805–1806. This was to be their only major sale until late 1808. George Augustus Lee was a major motivating force behind the development of the apparatus. He had an avid interest in technology, and had introduced a series of technological innovations at the Salford Mill, such as iron frame construction and steam heating. The continued to encourage the development of gaslight technology at Boulton & Watt.
Winsor and the Gas Light and Coke Company
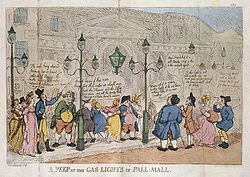
Gas Light and Coke Company
The Gas Light and Coke Company , was a company that made and supplied coal gas and coke. The Company was located on Horseferry Road in Westminster, London...
. It was founded through the efforts of a German émigré, Frederick Winsor, who had witnessed Lebon's demonstrations in Paris. He had tried unsuccessfully to purchase a thermolamp from Lebon, but remained taken with the technology, and decided to try his luck, first in his hometown of Brunswick
Braunschweig
Braunschweig , is a city of 247,400 people, located in the federal-state of Lower Saxony, Germany. It is located north of the Harz mountains at the farthest navigable point of the Oker river, which connects to the North Sea via the rivers Aller and Weser....
, and then in London in 1804. Once in London, Winsor began an intense marketing campaign to find investors for a new company that would manufacture gas apparatus and sell gas to consumers. He was quite successful in finding willing investors, but the legal form of the company was a more difficult problem. By the Bubble Act
Bubble Act
Bubble Act 1720 was an Act of the Parliament of Great Britain that forbade all joint-stock companies not authorised by royal charter. It was passed on 9 June 1720, and was also known as the Royal Exchange and London Assurance Corporation Act 1719, because those companies were incorporated under...
of 1720, all joint-stock companies above a certain number of shareholders in England needed to receive a royal charter
Royal Charter
A royal charter is a formal document issued by a monarch as letters patent, granting a right or power to an individual or a body corporate. They were, and are still, used to establish significant organizations such as cities or universities. Charters should be distinguished from warrants and...
to be incorporate, which meant in effect that an act of Parliament was required.
Winsor waged his campaign intermittently to 1807, when the investors constituted a committee charged with obtaining an act of Parliament. They pursued this task over the next three years, running into forms various adversity along the way, the most important of which was the resistance on part of Boulton & Watt in 1809. In that year, the committee made a serious attempt to get the House of Commons to pass a bill empowering the king to grant the charter, but Boulton & Watt felt their gaslight apparatus manufacturing business was threatened and mounted an opposition through their allies in Parliament. Although a parliamentary committee recommended approval, it went down to defeat on the third reading.
The following year, the committee tried again, succeeding with the acquiescence of Boulton & Watt because they renounced all powers to manufacture apparatus for sale. The act required that the company raise £100,000 before they could request a charter, a condition it took the next two years to fill. George III granted the charter in 1812.
Manufactured gas in England
.jpg)
Manufactured gas in Europe and North America
France's first gas company was also promoted by Frederick Winsor after he had to flee England in 1814 due to unpaid debts and tried to found another gas company in Paris, but it failed in 1819. The government was also interested in promoting the industry, and in 1817 commissioned Chabrol de Volvic to study the technology and build a prototype plant, also in Paris. The plant provided gas for lighting the hôpital Saint Louis, and the experiment was judged successful. King Louis XVIII then decided to give further impulse to the development of the French industry by sending people to England to study the situation there, and to install gaslight at a number of prestigious buildings, such as the Opera building, the national library, etc. A public company was created for this purpose in 1818. Private companies soon followed, and by 1822, when the government moved to regulate the industry, there were four in operation in the capital. The regulations passed then prevented the companies from competing, and Paris was effectively divided between the various companies operating as monopolies in their own zones.Gaslight also spread to other European countries. In 1817, a company was founded in Brussels by P. J. Meeus-Van der Maelen, and began operating the following year. By 1822, there were companies in Amsterdam and Rotterdam using English technology. In Germany, gaslight was used on a small scale from 1816 onwards, but the first gaslight utility was founded by the by English engineers and capital. In 1824, the Imperial Continental Gas Association
Imperial Continental Gas Association
Imperial Continental Gas Association plc was a leading British gas utility operating in various cities in Continental Europe . It was listed on the London Stock Exchange and was a constituent of the FTSE 100 Index.-History:...
was founded in London to establish gas utilities in other countries. Sir William Congreve, one if its leaders, signed an agreement with the government in Hanover, and the gas lamps were used on streets for the first time in 1826.
Gaslight was first introduced to the US in 1816 in Baltimore by Rembrant
Rembrandt Peale
Rembrandt Peale was an American artist and museum keeper. A prolific portrait painter, he was especially acclaimed for his likenesses of presidents George Washington and Thomas Jefferson...
and Rubens Peale, who lit their museum with gaslight, which they had seen on a trip to Europe. The brothers convinced a group of wealthy people to back them in a larger enterprise, and, the local government passed a law allowing the Peales and their associates to lay mains and light the streets. A company was incorporated for this purpose in 1817. After some difficulties with the apparatus and financial problems, the company hired an English engineer with experience in gaslight. It began to flourish, and by the 1830s, the company was supplying gas to 3000 domestic customers and 100 street lamps. Companies in other cities followed, the second being New York in 1825.
Legal, regulatory, environmental, health, and safety aspects of gas manufacture
Gas lighting was one of the most debated technology of the first industrial revolution. In Paris, in particular, as soon as 1823 a public controversy forced the government to devise safety norms (Fressoz, 2007). The residues produced from distilled coal were either disposed into rivers or stocked in basins which polluted (and still pollute) the soil.Case law
Case law
In law, case law is the set of reported judicial decisions of selected appellate courts and other courts of first instance which make new interpretations of the law and, therefore, can be cited as precedents in a process known as stare decisis...
in the United Kingdom and the United States clearly held though the construction and operation of a gas-works was not the creation of a public nuisance in se, due to the reputation of gas-works as highly undesirable neighbors, and the noxious pollution known to issue from such, especially in the early days of manufactured gas, gas-works were on extremely short notice from the courts that (detectable) contamination outside of their grounds – especially in residential districts – would be severely frowned upon. Indeed, many actions for the abatement
Abatement
Abatement may refer to:*Abatement of debts and legacies, a common law doctrine of wills*Abatement in pleading, a legal defense to civil and criminal actions based purely on procedural and technical issues involving the death of parties...
of nuisance
Nuisance
Nuisance is a common law tort. It means that which causes offence, annoyance, trouble or injury. A nuisance can be either public or private. A public nuisance was defined by English scholar Sir J. F...
s brought before the courts did result in unfavorable verdicts for gas manufacturers – in one study on early environmental law, actions for nuisance involving gas-works resulted in findings for the plaintiffs 80% of the time, compared with an overall plaintiff victory rate of 28.5% in industrial nuisance cases.
Injunction
Injunction
An injunction is an equitable remedy in the form of a court order that requires a party to do or refrain from doing certain acts. A party that fails to comply with an injunction faces criminal or civil penalties and may have to pay damages or accept sanctions...
s both preliminary and permanent could and were often issued in cases involving gas-works. For example, the ill reputation of gas-works became so well known that in City of Cleveland vs. Citizens' Gas Light Co., 20 N. J. Eq. 201
Case citation
Case citation is the system used in many countries to identify the decisions in past court cases, either in special series of books called reporters or law reports, or in a 'neutral' form which will identify a decision wherever it was reported...
, a court went so far as to enjoin a future gas-works not yet even built – preventing it from causing annoying and offensive vapours and odors in the first place. The injunction not only regulated the gas manufacturing process – forbidding the use of lime purification – but also provided that if nuisances of any sort were to issue from the works – a permanent injunction forbidding the production of gas would issue from the court. Indeed, as the Master of the Rolls
Master of the Rolls
The Keeper or Master of the Rolls and Records of the Chancery of England, known as the Master of the Rolls, is the second most senior judge in England and Wales, after the Lord Chief Justice. The Master of the Rolls is the presiding officer of the Civil Division of the Court of Appeal...
, Lord Langdale
Henry Bickersteth, 1st Baron Langdale
Henry Bickersteth, 1st Baron Langdale KC, PC was an English law reformer and Master of the Rolls.He was born on 18 June 1783 at Kirkby Lonsdale, three years before his brother Edward Bickersteth...
, once remarked in his opinion in Haines v. Taylor, 10 Beavan 80
Case citation
Case citation is the system used in many countries to identify the decisions in past court cases, either in special series of books called reporters or law reports, or in a 'neutral' form which will identify a decision wherever it was reported...
, that I have been rather astonished to hear the effects of gas works treated as nothing...every man, in these days, must have sufficient experience, to enable him to come to the conclusion, that, whether a nuisance or not, a gas manufactory is a very disagreeable thing. Nobody can doubt that the volatile products which arise from the distillation of coal are extremely offensive. It is quite contrary to common experience to say they are not so...every man knows it.
However, as time went by, gas-works began to be seen as more as a double-edged sword – and eventually as a positive good, as former nuisances were abated by technological improvements, and the full benefits of gas became clear. There were several major impetuses that drove this phenomenon:
- regulation of pollution from gas-works (in the case of the United Kingdom, with the passage of the Gas-works Clauses Act 1847), which increased the cost of pollution, previously being near zero, leading to the development of technologies that abated the ongoing pollution nuisances (in many cases, turning discarded former pollutants into profitable by-products);
- the rise of the "smoke nuisance" in the 1850s, brought about by the domestic and commercial use of coal, in many cities and metropolises; direct combustion of coal being a particularly notorious source of pollution; which the widespread use of gas could abate, especially with the commencement of using gas for purposes other than illuminating during the 1870s; for cooking, for the heating of dwelling-houses, for making domestic hot water, for raising steam, for industrial and chemical purposes, and for stationary internal combustion engine-driving purposes – which were previously met by employing coal;
- the development of high-pressure gas mains, and compressors (1900s); these were capable of efficiently transporting gas over long distances, allowing one manufactured gas plant to supply a relatively large area – leading to the concentration of gas-manufacturing operations, instead of their geographic distribution; this resulted in gas-works being able to be located away from residential and commercial districts, where their presence could result in discomfort and concern for the inhabitants thereof;
Both the era of consolidation of gas-works through high-pressure distribution systems (1900s–1930s) and the end of the era of manufactured gas (1955–1975) saw gas-works being shut down due to redundancies. What brought about the end of manufactured gas was that pipelines began to be built to bring natural gas directly from the well to gas distribution systems. Natural gas was superior to the manufactured gas of that time, being cheaper – extracted from wells rather than manufactured in a gas-works – more user friendly – coming from the well requiring little, if any, purification – and safer – due to the lack of carbon monoxide in the distributed product. Upon being shut down, few former manufactured gas plant sites were brought to an acceptable level of environmental cleanliness to allow for their re-use, at least by contemporary standards. In fact, many were literally abandoned in place, with process wastes left in situ, and never adequately disposed of.
As the wastes produced by former manufactured gas plants were persistent in nature, they often (as of 2009) still contaminate the site of former manufactured gas plants: the waste causing the most concern today is primarily coal tar (mixed long-chain aromatic and aliphatic hydrocarbons, a byproduct of coal carbonization), while "blue billy" (a noxious byproduct of lime purification contaminated with cyanides) as well as other lime and coal tar residues are regarded as lesser, though significant environmental hazards. Some former manufactured gas plants are sometimes still are owned by the gas utilities of today, often in an effort to prevent contaminated land from falling into public use, and inadvertently causing the release of the wastes therein contained. Others have fallen into public use, and without proper reclamation, have caused – often severe – health hazards for their users. When and where necessary, former manufactured gas plants are subject to environmental remediation laws, and can be subject to legally mandated cleanups.
Appliances and machinery of the historic gas-works
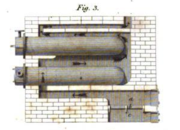
Samuel Clegg
Samuel Clegg was a British civil engineer.Clegg was born at Manchester on 2 March 1781, received a scientific education under the care of Dr. Dalton. He was then apprenticed to Boulton and Watt, and at the Soho Manufactory witnessed many of William Murdoch's earlier experiments in the use of coal...
in the period 1805–1812. Further improvements were made at the Gas Light and Coke Company, as well as by the growing number of gas engineers such as John Malam and Thomas Peckston after 1812. Boulton & Watt contributed the basic design of the retort, condenser, and gasometer, while Clegg improved the gasometer and introduced lime purification and the hydraulic main, another purifier.
Retort bench
The retort bench was the construction in which the retorts were located for the carbonization (synonymous with pyrolysis) of the coal feedstock and the evolution of coal gas. Over the many years of manufactured gas production, advances were made that turned the retort-bench from little more than coal-containing iron vessels over an open fire to a massive, highly efficient, partially automated, industrial-scale, capital-intensive plant for the carbonization of large amounts of coal. Several retort benches were usually located in a single "retort house", which there was at least one of in every gas-works.Initially, retort benches were of many different configurations due to the lack of long use and scientific and practical understanding of the carbonization of coal. Some early retorts were little more than iron vessels filled with coal and thrust upon a coal fire with pipes attached to their top ends. Though practical for the earliest of gas-workings, this quickly changed once the very early gas-works served more than a relatively few customers. As the size of such vessels grew – the need became apparent for efficiency in refilling retorts – and it became known that though while filling one-ended vertical retorts may be easy – removing the coke and residues from them after the carbonization of coal was far more difficult than filling them was. So gas retorts were transitioned from vertical vessels to horizontal tubular vessels.
Retorts were usually made of cast iron during the early days of manufactured gas. Early gas engineers experimented extensively with the best shape, size, and setting to adopt. No one form of retort initially came to dominate, and many different cross-sections remained in use; however, after the 1850s, retorts generally became made of fire-clay due to greater heat retention, greater durability under heat, longer life with proper care, and other positive qualities. Cast-iron retorts were still used in the small gas-works, due to their compatibility with the demands of such, with the cast-iron retort's lower cost, ability to heat up quickly to meet transient demand, and "plug and play" replacement capabilities outweighing the disadvantages of shorter life-time, lower temperature margins, and lack of ability to be manufactured in non-cylindrical shapes. Also, general gas-works practice following the switch to fire-clay retorts favored retorts that were shaped like a "D" turned 90 degrees to the left, sometimes with a slightly pitched bottom section.
With the introduction of the fire-clay retort, higher heats could be held in the retort benches, leading to faster and more complete carbonization of the coal within. As higher heats became possible, advanced methods of retort bench firing were introduced, catalyzed by the development of the open hearth furnace
Open hearth furnace
Open hearth furnaces are one of a number of kinds of furnace where excess carbon and other impurities are burnt out of the pig iron to produce steel. Since steel is difficult to manufacture due to its high melting point, normal fuels and furnaces were insufficient and the open hearth furnace was...
by Siemens
Carl Wilhelm Siemens
Carl Wilhelm Siemens was a German born engineer who for most of his life worked in Britain and later became a British subject.-Biography:...
, during a period from around 1855 – 1870, leading to a revolution in gas-works efficiency.
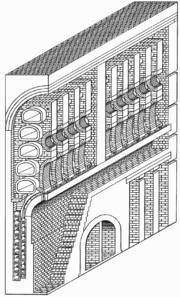
- The introduction of the "indirectly fired" retort bench. The early "directly fired" retort bench consisted of retorts suspended over a coke fire, which heated the retorts and drove the carbonization of coal within to coke, and the evolution of gas. The introduction of indirect firing changed this – instead of the retorts being heated directly by the fire – the fire was placed a ways below and to one side of the retorts, brought to a very high heat, while the air supply was reduced and a small amount of steam introduced. Instead of evolving large quantities of heat to directly heat the retorts, the fire now evolved heated gasses – specifically carbon monoxide and – due to the steam – a small amount of hydrogen gas as well, which are both highly combustible. These gasses rise from the fire into a channel which soon brings them to the "tuyereTuyereA tuyere, also can be spelled as tuyère, is a tube, nozzle or pipe through which air is blown into a furnace or hearth.Air or oxygen is injected into a hearth under pressure from bellows or a blast engine or other devices...
s" – small holes similar to "nostrils", located adjacent to the retorts, which shoot the "furnace-gasses" out of them. Adjacent "tuyeres" emit a large amount of "secondary air", which is preheated air, that, upon mixing with the furnace gasses, causes them to ignite and burst into flame and bathe the exterior of the retorts in heat. - The introduction of heat recuperation for the preheating of the air of primary and secondary combustion. By causing the exhaust of the retort-bench to pass through a labyrinthine maze of refractory brickwork, substantial quantities of heat can be extracted from it. On the other side of the exhaust channels are channels for the passage of the air of combustion. The bricks thus transfer the heat of the exhaust to the air of combustion, preheating it. This provides for a much greater degree of thermal efficiency in the retort-bench, causing it to be able to use far less coke – as air that is preheated by waste heat is already hot when it enters the fire to be burnt, or the "tuyere" to fuel secondary combustion.
These two advances turned the old, "directly fired" retort bench into the advanced, "indirectly fired", "regenerative" or "generative" retort bench, and lead coke usage within the retort benches – at least in the larger works – to drop from upwards of 40% of the coke made by the retorts to factors as low as 15% of the coke made by the retorts, leading to an improvement in efficiency of an order of magnitude. However, these improvements imparted an additional capital cost to the retort bench to incorporate them, which caused them to be only slowly incorporated in the smaller gas-works, if they were incorporated at all.
Further increases in efficiency and safety were seen with the introduction of the "through" retort, which had a door at both its front and its rear. This provided for greater efficiency and safety in loading and unloading the retorts, which was a labor-intensive and often dangerous process. Coal could now be pushed out of the retort – rather than pulled out of the retort. One interesting modification of the "through" retort was the "inclined" retort – coming into its heyday in the 1880s – a retort set on a moderate incline, where coal was poured in at one end, and the retort sealed; following pyrolysis, the bottom was opened and the coke poured out through means of gravity. This was adopted in some gas-works, but the savings in labor were often offset by the uneven distribution and pyrolysis of the coal as well as clumping problems leading to failure of the coal to pour out of the bottom following pyrolysis that were exacerbated in certain coal types. As such, inclined retorts were rendered obsolescent by later advances, including the retort-handling machine and the vertical retort system.
Several advanced retort-house appliances were introduced for improved efficiency and convenience. The compressed-air or steam-driven clinkering pick was found to be especially useful in removing clinker from the primary combustion area of the indirectly fired benches – previously clinkering was an arduous and time-consuming process that used large amounts of retort house labor. Another class of appliances introduced were apparatuses – and ultimately, machines – for retort loading and unloading. Retorts were generally loaded by using an elongated scoop, into which the coal was loaded – a gang of men would then lift the scoop and ram it into the retort. The coal would then be raked by the men into a layer of even thickness and the retort sealed. Gas production would then ensue – and from 8 – 12 hours later, the retort would be opened, and the coal would be either pulled (in the case of "stop-ended" retorts) or pushed (in the case of "through" retorts) out of the retort. Thus, the retort house had heavy manpower requirements – as many men were often required to bear the coal-containing scoop and load the retort.
(TBD: Brief description of advanced retort loading apparatus; more detailed description of retort-handling machine.)
Coming soon: The introduction of the coke-oven system, and, finally, the vertical retort system.
Other Gas-Works facilities
From the retort, the gas would first pass through a tar/water "trap" (similar to a trap in plumbing) called a hydraulic main, where a considerable fraction of coal tar was given up and the gas was significantly cooled. Then, it would pass through the main out of the retort house into an atmospheric or water-cooled condenser, where it would be cooled to the temperature of the atmosphere or the water used. At this point, it enters the exhauster house and passes through an "exhauster", an air pump which maintains the hydraulic mains and, consequently, the retorts at a negative pressure (with a zero pressure being atmospheric). It would then be washed in a "washer" by bubbling it through water, to extract any remaining tars. After this, it would enter a purifier. The gas would then be ready for distribution, and pass into a gasholder for storage.Hydraulic main

The hydraulic main had a level of a liquid mixture of (initially) water, but, following use, also coal tar, and ammoniacal liquor. Each retort ascension pipe dropped under the water level by at least a small amount, perhaps by an inch, but often considerably more in the earlier days of gas manufacture. The gas evolved from each retort would thus bubble through the liquid and emerge from it into the void above the liquid, where it would mix with the gas evolved from the other retorts and be drawn off through the foul main to the condenser.
There were two purposes to the liquid seal: first, to draw off some of the tar and liquor, as the gas from the retort was laden with tar, and the hydraulic main could rid the gas of it, to a certain degree; further tar removal would take place in the condenser, washer/scrubber, and the tar extractor. Still, there would be less tar to deal with later. Second, the liquid seal also provided defense against air being drawn into the hydraulic main: if the main had no liquid within, and a retort was left open with the pipe not shut off, and air were to combine with the gas, the main could explode, along with nearby benches.
However, after the early years of gas, research proved that a very deep, excessive seal on the hydraulic main threw a backpressure upon all the retorts as the coal within was gasifying, and this had deleterious consequences; carbon would likely deposit onto the insides of retorts and ascension pipes; and the bottom layer of tar with which the gas would have to travel through in a deeply sealed main robbed the gas of some of its illuminating value. As such, after the 1860s, hydraulic mains were run at around 1 inch of seal, and no more.
Later retort systems (many types of vertical retorts, especially ones in continuous operation) which had other anti-oxygen safeguards, such as check valves, etc., as well as larger retorts, often omitted the hydraulic main entirely and went straight to the condensers – as other apparatus and buildings could be used for tar extraction, the main was unnecessary for these systems.
Condenser
Cooled evolved gas to temperature of atmosphere (or water), so that gas would give up a good portion of its remaining volatiles at this point. Most tar (except for very light tar) would be given up.Exhauster
Maintained hydraulic main and condenser at negative pressure.There were several types of exhausters.
- The steam ejector/aspirator type exhauster used a substantial steam jet/venturi to maintain the negative pressure in the hydraulic main and condenser. This type of exhauster was mechanically simple, had no moving parts, and thus, had virtually no potential to fail. However, it consumed a comparatively large amount of steam. Often used as a backup exhauster; in this role it continued as a reliable backup until the end of the age of manufactured gas.
- Reciprocating exhausters of various types. Steam engine-driven exhauster used cylinder pump to pump gas. Relatively reliable, but inefficient, using large quantities of steam, but less than the ejector type exhauster. Used in the early days of exhausters, but quickly obsoleted.
- Blower-type exhauster.
- Turboexhauster.
Purifier
Coal gas coming directly from the bench was a noxious soup of chemicals, and removal of the most deleterious fractions was important, for improving the quality of the gas, for preventing damage to equipment or premises, and for recovering revenues from the sale of the extracted chemicals. Several offensive fractions being present in a distributed gas might lead to problems – TarCoal tar
Coal tar is a brown or black liquid of extremely high viscosity, which smells of naphthalene and aromatic hydrocarbons. Coal tar is among the by-products when coal iscarbonized to make coke or gasified to make coal gas...
in the distributed gas might gum up the pipes (and could be sold for a good price), ammoniacal vapours
Ammonia
Ammonia is a compound of nitrogen and hydrogen with the formula . It is a colourless gas with a characteristic pungent odour. Ammonia contributes significantly to the nutritional needs of terrestrial organisms by serving as a precursor to food and fertilizers. Ammonia, either directly or...
in the gas might lead to corrosion problems (and the extracted ammonium sulfate was a decent fertilizer), naphthalene vapours
Naphthalene
Naphthalene is an organic compound with formula . It is a white crystalline solid with a characteristic odor that is detectable at concentrations as low as 0.08 ppm by mass. As an aromatic hydrocarbon, naphthalene's structure consists of a fused pair of benzene rings...
in the gas might stop up the gas-mains, and even carbon dioxide
Carbon dioxide
Carbon dioxide is a naturally occurring chemical compound composed of two oxygen atoms covalently bonded to a single carbon atom...
in the gas was known to decrease illumination; thus various facilities within the gas-works were tasked with the removal of these deleterious effluents. But these do not compare to the most hazardous contaminant in the raw coal gas: the sulfuret of hydrogen (hydrogen sulfide
Hydrogen sulfide
Hydrogen sulfide is the chemical compound with the formula . It is a colorless, very poisonous, flammable gas with the characteristic foul odor of expired eggs perceptible at concentrations as low as 0.00047 parts per million...
, H2S). This was regarded as utterly unacceptable for several reasons:
- The gas would smell rankly of rotten eggs when burnt;
- The gas-works and adjacent district would smell of rotten eggs when the gas-works was producing gas;
- The gas, upon burning, would form sulfur dioxideSulfur dioxideSulfur dioxide is the chemical compound with the formula . It is released by volcanoes and in various industrial processes. Since coal and petroleum often contain sulfur compounds, their combustion generates sulfur dioxide unless the sulfur compounds are removed before burning the fuel...
, which would be quickly oxidized to sulfur trioxideSulfur trioxideSulfur trioxide is the chemical compound with the formula SO3. In the gaseous form, this species is a significant pollutant, being the primary agent in acid rain. It is prepared on massive scales as a precursor to sulfuric acid.-Structure and bonding:Gaseous SO3 is a trigonal planar molecule of...
, and subsequently would react with the water vapor produced by combustion to form sulfuric acidSulfuric acidSulfuric acid is a strong mineral acid with the molecular formula . Its historical name is oil of vitriol. Pure sulfuric acid is a highly corrosive, colorless, viscous liquid. The salts of sulfuric acid are called sulfates...
vapour. In a dwelling-house, this could lead to the formation of irritating, poisonous and corrosive atmospheres where and when burnt. - Manufactured gas was originally distributed in the well-to-do districts, as such were low-hanging fruit for the gas utility. Such persons were of a class known to possess silver goods of varying sorts. If exposed to a sulfurous atmosphere, silver tarnishes – and a sulfurous atmosphere would undoubtedly be present in any house lit with sulfuretted gas.
As such, the removal of the sulfuret of hydrogen was given the highest level of priority in the gas-works. A special facility existed to extract the sulfuret of hydrogen – known as the purifier. The purifier was arguably the most important facility in the gas-works, if the retort-bench itself is not included.
Originally, purifiers were simple tanks of lime-water where the raw gas from the retort bench was bubbled through to remove the sulfuret of hydrogen. This original process of purification was known as the "wet lime" process. But this process created noxious waste, as the combination of the sulfuret and calcium was also accompanied by the combination of the nitrogen of ammonia and the carbon of carbonate (lime being calcium carbonate), mediated by the aqueous environment, forming poisonous cyanide
Cyanide
A cyanide is a chemical compound that contains the cyano group, -C≡N, which consists of a carbon atom triple-bonded to a nitrogen atom. Cyanides most commonly refer to salts of the anion CN−. Most cyanides are highly toxic....
ions. Originally, the waste of the purifier house was flushed into a nearby body of water, such as a river or a canal. However, after fish kills, the nauseating way it made the rivers stink, and the truly horrendous stench caused by exposure of residuals if the river was running low, the public clamoured for better means of disposal. Thus it was piled into heaps for disposal. The lime residue left over from the "wet lime" process was one of the first true "toxic wastes", a material called "blue billy". Some enterprising gas entrepreneurs tried to sell it as a weed-killer, but most people wanted nothing to do with it, and generally, it was regarded as waste which was both smelly and poisonous, and gas-works could do little with, except bury. But this was not the end of the "blue billy", for after burying it, rain would often fall upon its burial site, and leach the poison and stench from the buried waste, which could drain into fields or streams. Following countless fiascoes with "blue billy" contaminating the environment, a furious public, aided by courts, juries, judges, and masters in chancery, were often very willing to demand that the gas-works seek other methods of purification – and even pay for the damages caused by their old methods of purification.
This led to the development of the "dry lime" purification process, which was less effective than the "wet lime" process, but had less toxic consequences. Still, it was quite noxious. Slaked lime (calcium hydroxide) was placed in thick layers on trays which were then inserted into a square or cylinder-shaped purifier tower which gas was then passed through, from the bottom to the top. After the charge of slaked lime had lost most of its absorption effectiveness, the purifier was then shut off from the flow of gas, and either was opened, or air was piped in. Immediately, the sulfur-impregnated slaked lime would react with the air to liberate large concentrations of sulfuretted hydrogen, which would then billow out of the purifier house, and make the gas-works, and the district, stink of sulfuretted hydrogen. Though toxic in sufficient concentrations or long exposures, the sulfuret was generally just nauseating for short exposures at moderate concentrations, and was merely a health hazard (as compared to the outright danger of "blue billy") for the gas-works employees and the neighbors of the gas-works. The sulfuretted lime was not toxic, but not greatly wanted, slightly stinking of the odor of the sulfuret, and was spread as a low grade fertilizer, being impregnated with ammonia to some degree. The outrageous stinks from many gas-works led many citizens to regard them as public nuisances, and attracted the eye of regulators, neighbors, and courts.
The "gas nuisance" was finally solved by the "iron ore" process. Enterprising gas-works engineers discovered that bog iron ore could be used to remove the sulfuretted hydrogen from the gas, and not only could it be used for such, but it could be used in the purifier, exposed to the air, whence it would be rejuvenated, without emitting noxious sulfuretted hydrogen gas, the sulfur being retained in the iron ore. Then it could be reinserted into the purifier, and reused and rejuvenated multiple times, until it was thoroughly embedded with sulfur. It could then be sold to the sulfuric acid works for a small profit. Lime was sometimes still used after the iron ore had thoroughly removed the sulfuret of hydrogen, to remove carbonic acid (carbon dioxide, CO2), the bisulfuret of carbon (carbon disulfide
Carbon disulfide
Carbon disulfide is a colorless volatile liquid with the formula CS2. The compound is used frequently as a building block in organic chemistry as well as an industrial and chemical non-polar solvent...
, CS2), and any ammonia still aeroform after its travels through the works. But it was not made noxious as before, and usually could fetch a decent rate as fertilizer when impregnated with ammonia. This finally solved the greatest pollution nuisances of the gas-works, but still lesser problems remained – not any that the purifier house could solve, though.
Purifier designs also went through different stages throughout the years.
Minor and incidental coal gas-works facilities
The gasworks had numerous small appertunances and facilities to aid with divers gas management tasks or auxiliary services.Boilers
As the years went by, boilers (for the raising of steam) became extremely common in most gas-works above those small in size; the smaller works often used gas-powered internal combustion engines to do some of the tasks that steam performed in larger workings.
Steam was in use in many areas of the gasworks, including:
For the operation of the exhauster;
For scurfing of pyrolysis char and slag from the retorts and for clinkering the producer of the bench;
For the operation of engines used for conveying, compressing air, charging hydraulics, or the driving of dynamos or generators producing electric current;
To be injected under the grate of the producer in the indirectly fired bench, so as to prevent the formation of clinker, and to aid in the water-gas shift reaction, ensuring high-quality secondary combustion;
As a reactant in the (carburetted) water gas plant, as well as driving the equipment thereof, such as the numerous blowers used in that process, as well as the oil spray for the carburettor;
For the operation of fire, water, liquid, liquor, and tar pumps;
For the operation of engines driving coal and coke conveyor-belts;
For clearing of chemical obstructions in pipes, including naphthalene & tar as well as general cleaning of equipment;
For heating cold buildings in the works, for maintaining the temperature of process piping, and preventing freezing of the water of the gasholder, or congealment of various chemical tanks and wells.
Heat recovery appliances could also be classed with boilers. As the gas industry applied scientific and rational design principles to its equipment, the importance of thermal management and capture from processes became common. Even the small gasworks began to use heat-recovery generators, as a fair amount of steam could be generated for "free" simply by capturing process thermal waste using water-filled metal tubing inserted into a strategic flue.
Dynamos/generators
As the electric age came into being, the gas-works began to use electricity – generated on site – for many of the smaller plant functions previously performed by steam or gas-powered engines, which were impractical and inefficient for small, sub-horsepower uses without complex and failure-prone mechanical linkages. As the benefits of electric illumination became known, sometimes the progressive gasworks diversified into electric generation as well, as coke for steam-raising could be had on-site at low prices, and boilers were already in the works.
Coal storage
According to Meade, the gasworks of the early 20th century generally kept on hand several weeks of coal. This amount of coal could cause major problems, because coal was liable to spontaneous combustion when in large piles, especially if they were rained upon, due to the protective dust coating of the coal being washed off, exposing the full porous surface area of the coal of slightly to highly activated carbon below; in a heavy pile with poor heat transfer characteristics, the heat generated could lead to ignition. But storage in air-entrained confined spaces was not highly looked upon either, as residual heat removal would be difficult, and fighting a fire if it was started could result in the formation of highly toxic carbon monoxide through the water-gas reaction, caused by allowing water to pass over extremely hot carbon (H2O + C = H2 + CO), which would be dangerous outside, but deadly in a confined space.
Coal storage was designed to alleviate this problem. Two methods of storage were generally used; underwater, or outdoor covered facilities. To the outdoor covered pile, sometimes cooling appurtenances were applied as well; for example, means to allow the circulation of air through the depths of the pile and the carrying off of heat. Amounts of storage varied, often due to local conditions. Works in areas with industrial strife often stored more coal, while nations whose proletariat was under "control" stored less. Other variables included national security; for instance, the gasworks of Tegel
Tegel
Tegel is a locality in the Berlin borough of Reinickendorf on the shore of Lake Tegel. The Tegel locality, the second largest in area of the 95 Berlin districts, also includes the neighbourhood of Saatwinkel.-History:...
in Berlin had some 1 million tons of coal (6 months of supply) in gigantic underwater bunker facilities half a mile long (Meade 2e, p. 379); as Berlin is on the North German Plain
North German plain
The North German Plain or Northern Lowland is one of the major geographical regions of Germany. It is the German part of the North European Plain...
, perhaps this was due to what happened to Paris in the Franco-Prussian War
Franco-Prussian War
The Franco-Prussian War or Franco-German War, often referred to in France as the 1870 War was a conflict between the Second French Empire and the Kingdom of Prussia. Prussia was aided by the North German Confederation, of which it was a member, and the South German states of Baden, Württemberg and...
of 1870–1871.
Tar/liquor storage
The chemical industries demanded coal tar
Coal tar
Coal tar is a brown or black liquid of extremely high viscosity, which smells of naphthalene and aromatic hydrocarbons. Coal tar is among the by-products when coal iscarbonized to make coke or gasified to make coal gas...
, and the gas-works could provide it for them; as such, the coal tar was stored on site in large underground tanks. As a rule, these were single wall metal tanks – that is, if they were not porous masonry. In those days, underground tar leaks were seen as merely a waste of tar; out of sight was truly out of mind; and such leaks were generally addressed only when the loss of revenue from leaking tar "wells", as these were sometimes called, exceeded the cost of repairing the leak. This practice of bygone days has caused representatives of present-day gas utilities to dive under tables and utter minced oaths when terms like "purportedly responsible party", "BTEX
BTEX
BTEX is an acronym that stands for benzene, toluene, ethylbenzene, and xylenes. These compounds are some of the volatile organic compounds found in petroleum derivatives such as petrol . Toluene, ethylbenzene, and xylenes have harmful effects on the central nervous system.BTEX compounds are...
", "aquifer plume", or "Superfund
Superfund
Superfund is the common name for the Comprehensive Environmental Response, Compensation, and Liability Act of 1980 , a United States federal law designed to clean up sites contaminated with hazardous substances...
" are mentioned.
Ammoniacal liquor was stored on site as well, in similar tanks. Sometimes the more progressive gasworks would have an ammonium sulfate
Ammonium sulfate
Ammonium sulfate , 2SO4, is an inorganic salt with a number of commercial uses. The most common use is as a soil fertilizer. It contains 21% nitrogen as ammonium cations, and 24% sulfur as sulfate anions...
plant, to convert the liquor into fertilizer, which was sold to farmers.
Station meter
This large-scale gas meter precisely measured gas as it issued from the works into the mains. It was of the utmost importance, as the gasworks balanced the account of issued gas versus the amount of paid for gas, and strived to detect why and how they varied from one another. Often it was coupled with a dynamic regulator to keep pressure constant, or even to modulate the pressure at specified times (a series of rapid pressure spikes was sometimes used with appropriately equipped street-lamps to automatically ignite or extinguish such remotely).
Anti-naphthalene minor carburettor
This device injected a fine mist of naphtha into the outgoing gas so as to avoid the crystallization of naphthalene in the mains, and their consequent blockage. Naphtha was found to be a rather effective solvent for these purposes, even in small concentrations. Where troubles with naphthalene developed, as it occasionally did even after the introduction of this minor carburettor, a team of workers was sent out to blow steam into the main and dissolve the blockage; still, prior to its introduction, naphthalene was a very major annoyance for the gasworks.
High-pressure distribution booster pump
This steam or gas engine powered device compressed the gas for injection into the high-pressure mains, which in the early 1900s began to be used to convey gas over greater distances to the individual low pressure mains, which served the end-users. This allowed the works to serve a larger area and achieve economies of scale.
Types of historically manufactured gasses
Manufactured Gas | Feedstock | Manufacture | Composition | Heat Yield at STP (BTU/ft3) | Light Yield at STP (std candle/ft3) | Notes |
---|---|---|---|---|---|---|
Coal gas. | Primarily bituminous or cannel coal. Lignite occasionally used. | Carbonization (pyrolysis Pyrolysis Pyrolysis is a thermochemical decomposition of organic material at elevated temperatures without the participation of oxygen. It involves the simultaneous change of chemical composition and physical phase, and is irreversible... ) of the coal feedstock (the heating of the coal feedstock in the absence of oxygen.) The gas produced by the hot coal is the gas distributed. |
As distributed, contains a moderate proportion of marsh gas (methane Methane Methane is a chemical compound with the chemical formula . It is the simplest alkane, the principal component of natural gas, and probably the most abundant organic compound on earth. The relative abundance of methane makes it an attractive fuel... , CH4), hydrogen (H2), carbonic oxide (carbon monoxide Carbon monoxide Carbon monoxide , also called carbonous oxide, is a colorless, odorless, and tasteless gas that is slightly lighter than air. It is highly toxic to humans and animals in higher quantities, although it is also produced in normal animal metabolism in low quantities, and is thought to have some normal... , CO), and simple hydrocarbon "illuminants", including oliefant gas (ethylene Ethylene Ethylene is a gaseous organic compound with the formula . It is the simplest alkene . Because it contains a carbon-carbon double bond, ethylene is classified as an unsaturated hydrocarbon. Ethylene is widely used in industry and is also a plant hormone... , C2H4) and acetylene gas (C2H2). In addition, prior to treatment, contains coal tars (complex aliphatic and aromatic hydrocarbons), ammoniacal liquor (gaseous ammonia, NH3, and aqueous ammonia, NH4OH), the sulfuret of hydrogen (H2S), and the sulfuret of carbon (CS2). |
500–650 | 10–18 | The oldest type, introduced in 1798 by Murdoch, et al.; when the term "manufactured gas" or "town gas" is used without qualifiers, it generally refers to coal gas. Substantially greater illuminant yield with use of special "cannel coal Cannel coal Cannel coal, also known as candle coal, is a type of coal, also classified as terrestrial type oil shale, with a large amount of hydrogen, which burns easily with a bright light and leaves little ash.... ", which may be modern oil shale Oil shale Oil shale, an organic-rich fine-grained sedimentary rock, contains significant amounts of kerogen from which liquid hydrocarbons called shale oil can be produced... , richer in hydrocarbons than most regular gas coal (bituminous coal). |
Wood gas | Timber resources. | Carbonization (pyrolysis) of the timber feedstock (the heating of the timber feedstock in the absence of oxygen.) The volatiles evolved from the heated wood is the gas distributed. | Resulting products unknown. Probably marsh gas, hydrogen, and carbonic oxide, along with some hydrocarbons and organics, like turpentine. | ? | < 10 | Wood was used as a feedstock during the early days (1820s - 1850s) of manufactured gas in certain areas of the United States, due to lack of development of coal resources. Wood was carbonized in a manner similar to coal; however, the gas evolved was markedly inferior to that of coal in lighting and heating qualities. Still very useful for lighting. This wood gas produced solely through pyrolysis should not be confused with wood gas Wood gas Wood gas is a syngas fuel which can be used as a fuel for furnaces, stoves and vehicles in place of petrol, diesel or other fuels. During the production process biomass or other carbon-containing materials is gasified within the oxygen-limited environment of a wood gas generator to produce hydrogen... as used today; the modern wood gas generator Wood gas generator A wood gas generator is a gasification unit which converts timber or charcoal into wood gas, a syngas consisting of atmospheric nitrogen, carbon monoxide, hydrogen, traces of methane, and other gases, which - after cooling and filtering - can then be used to power an internal combustion engine or... produces its synthesis gas through the complete gasification process, as described below. |
Oil pyrolytic gas. | Petroleum oil. | Carbonization (pyrolysis) of petroleum (the heating of the petroleum feedstock in the absence of oxygen.) The gas produced by the heated & decomposed oil is the gas distributed. | As distributed, contains an extremely high proportion of simple hydrocarbon "illuminants", including oliefant gas (ethylene, C2H4) and acetylene gas (C2H2), as well as propane gas (C3H8), marsh gas (methane, CH4), hydrogen (H2), and a small amount of carbonic oxide (carbon monoxide, CO). | 1000–1500 | 40–60 | Initial experiments in 1817–1825, which were failures; began to be used widely in 1860s. Simpler, much less labor intensive manufacturing process. Oil very expensive feedstock compared to coal; prices (and illuminous efficacy per ft3) double to triple that of regular coal gas. |
Oil catalytic semi-water gas. (Improved Jones Process) | Petroleum oil. | Staged partial reaction of petroleum oil using steam at high temperature in catalytic environment. The gas produced by the partially reacted and partially cracked oil is the gas distributed. | As distributed, contains 35 – 40% hydrogen (H2), 45% – 50% marsh gas (methane, CH4), and the balance of higher hydrocarbons and carbonic oxide (carbon monoxide, CO). | 500–700 | 10–18 | E.C. Jones, chief gas engineer of the San Francisco Gas Light Company (later the PG&E) developed this ingenious process to turn oil into a gas very similar to that produced by the pyrolysis of coal using a catalytic backflush of already produced gas and steam to provide a hydrogen atmosphere to stimulate disassociation of the oil with the minimal production of lampblack. Singlehandedly revolutionized gasmaking on the Pacific Coast, as oil was plentiful compared to coal, and could be turned into a gas capable of drop-in replacement for coal gas, eliminating the need for coal to be shipped by water transport from Australia and the Far East to Pacific ports at high expense. The Improved Jones Process and evolutions of that process continued to be used on the Pacific Coast until the end of the manufactured gas age. |
Producer gas. | Anthracite coal, coke, bituminous coal dust and waste, lignite, or biomass. | Manufactured by the incomplete combustion of varying carboniferous feedstocks in a extremely hot (>= 1100oC), limited-oxygen atmosphere aided by the injection of a small, stochiometric flow of steam. | Contains a high proportion of nitrogen (N2) & carbonic oxide (carbon monoxide, CO), limited amounts of hydrogen (H2), and a very small quantity of swamp gas (methane, CH4). | 100–170 | nil | Produced in early days of coal gasification; however, only became common after invention of Otto cycle internal combustion engine for which it was an ideal fuel, as well as small sized, reliable gas producers, which allowed the easy generation of producer gas nearly anywhere a supply of anthracite or coke was available. Gas generally not distributed past the walls of the production site, but used on location, due to low energy content and that it was mostly composed of deadly carbonic oxide. Used for standard domestic gas needs within institutions large enough to justify a hired man for the upkeep of the producer; these institutions often included work-houses, alms-houses, reformatories, orphanages, houses of correction, lunatic asylums, lyceums, industrial schools, and penitentiaries. Bulk heating, electric generation, and engine-running uses; also for welding purposes, as it possesses a "reducing flame" and a high temperature. N.B. One variant of producer gas was Mond gas, known for both its consistent yield and that ammonia could be obtained as a byproduct. Slight modifications of producer necessary. |
Water gas. | Coke or anthracite coal and steam. | Manufactured by the reaction of extremely hot feedstock and steam in an superheated non-oxygen atmosphere. | Contains high proportions of carbonic oxide (carbon monoxide, CO) and hydrogen (H2), and very low proportions of other gasses. | ~ 300 | nil | Manufacture known since late 1830s. However, not optimized for profitable generation until approximately 1865–70. Produced using an intermittent process; first, the exothermic "blow", where the feedstock was heated by blowing air through it, followed by an endothermic "run", where the air was cut off, and steam passed through the now superhot feedstock, leading to the decomposition of the steam and scavenging of carbon from the feedstock. Generally mixed with coal gas, valued for being able to be produced "just in time" with 1 hour's notice, unlike coal gas, which would require 4+ days to bring online from idle. Low labor and capital costs, however, high, inefficient use of anthracite/coke feedstock. |
Carburetted water gas. | Water gas & petroleum or coal tar. | Manufactured by passing just-produced, super-hot water gas through a superheated "carburettor" in to which petroleum or coal tar oil is sprayed, accomplishing the "cracking" of the oil into the gas. | Contains high proportions of carbonic oxide (carbon monoxide, CO) and hydrogen (H2), and moderate proportions of marsh gas (methane, CH4) and mixed hydrocarbon illuminant gasses. | 400–700 | 10–25 | Introduced in 1876. Became a common process during the heady days of gas-lighting from the 1870s to the first decade of the 20th century, especially useful for mixing with coal gas. Process had similar positives and negatives as straight water gas, but also had illuminant value, as well as higher cost, due to oil/tar use. Variable illuminant yield, depending on amount/quality of oil spray. As gas steadily lost ground as an illuminant, extensive carburetting reduced to low values or carburetting omitted entirely, representing a return to water gas. |
Complete Gasification Gas | Gas-evolving coal or other organics. | Manufactured by a complex, staged process where as coal travelled down the vertical axis of a upright, semicylindrical reaction chamber, it would be subject to different chemical reactions based on what was being fed into that area of the reaction chamber. | Mix of carbonic oxide (carbon monoxide, CO), marsh gas (methane, CH4), hydrogen (H2), a small quantity of simple hydrocarbon illuminants, along with small quantities of nitrogen and carbon dioxide. | 330–400 | > 8 | Earliest processes from 1895, came into industrial-scale use by 1918 (Meade, p. 766 – 769). Numerous processes developed, many in Germany, Austria, and other Continental nations. Potential of retaining over 75% energy of feedstock in gas with heat recovery from raw gas (Meade, p. 762), as compared to ~55% feedstock energy retention of other gasification processes. |