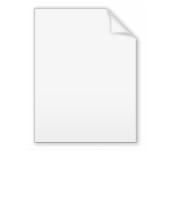
Ledglass
Encyclopedia
Ledglass is a building material which contains some functional electronics, light-emitting diode
s. The LEDGlass and its technology is described in different articles, It allows for example glass facades to be used as marketing area or windshield glasses to be used as display. This is the reason, why LEDGlass (which may also be described as LED Glass or LED embedded Glass) is a member of the so called electronic functional glasses. Historically, the vacuum sputtering
of metals and transparent conductive oxides on polymers has allowed the development of transparent conductive materials
and transparent conductive glass
. The electrical conductivity of these transparent materials has open a wide window of applications using electronic surface mounted devices
(SMD) laminated in glass. LEDs and other electronic SMD may be mounted on transparent conductive films, to produce flexible, and ready to laminate
films or directly on transparent conductive glass. While highly flexible film subtrates may be transported by fast and low weight air mail, SMD on metallized glass will result in heavy weight products.
. The resulting product called "Triplex" was most interesting in many aspects: Unlike ordinary or tempered glass, which falls apart when fractured laminated glass staid in place. However, before a satisfactory safety glass
could be marketed in commercial quantities, raw materials, including glass, plastic, and bonding agents as well as the manufacturing technique, had to be improved. Different solution were developed, like tough, clear, flexible plastic sheets made of polyvinyl butyral
(PVB), ethylene vinyl acetate (EVA) or thermoplastic polyurethane
(TPU), which could be sandwiched in between glass to create a safe and breakproof material. Today, laminated glass helps keep the building envelope intact, reduces the danger of glass shards, and helps prevent people from falling through sudden openings. Users of laminated glass soon discovered that it also helped reduce noise, block harmful UV rays
and protect against break-ins. In cars and in buildings, use of laminated glass continues to grow, increasing safety worldwide.
The first commercially used LEDs were developed in the 1960s by combining three elements: gallium
, arsenic
and phosphorus
to obtain a 655 nm (GaAsP) red light source. As LED technology progressed through the 1970s, additional wavelength
s became available. The most common materials were GaP green and red, GaAsP orange or high efficiency red and GaAsP yellow, which are still used today. Although the reliability of LEDs has always been superior to that of incandescent, neon
etc., the failure rate
of early devices was much higher than current technology now achieves. This was due in part to the actual component assembly that was primarily manual in nature. In fact, some GaAlAs LEDs may decrease by 50% after only 50,000 -70,000 hours of operation. To overcome these difficult issues, LED designers turned to laser diode technology
for solutions. This led to the development of InGaAlP (Indium
Gallium
Aluminum Phosphide
) LEDs. The use of InGaAlP allowed flexibility in the design of LED output color by adjusting the size of the energy band gap
. These developments enabled the use of ultra small LEDs with high reliability for totally new applications.
In 1877 Prof. A. W. Wright of Yale University
published a paper in the American Journal of Science and Arts on the use of an „electrical deposition apparatus“ to form mirrors and study their properties. There still is some confusion as to whether Wright was using sputtering or gaseous arcing
. But there is no doubt, that this early research anticipated later developments, including cathode shielding
, multi-layer coatings and all technologies of sputter deposition
. These applications progressed from the simple single layer coatings on plates in the 1930s and 1940s to coatings on flexible materials in the 1950s. This research anticipated the energy crises in the 1970s proving the need for energy conservation
coatings on large areas of glass and polymer webs. As published in Patents of Ford Motors (1989) and Saint Gobain
(1990)), the use of transparent high conductive layers on glass was a quite important solution for pure heating applications. But since the 1980s companies like Sharp
(1983) started to mount small electronic devices (SMDs) like LEDs on transparent conductive glass or films. The patterning of transparent conductive layers was done by laser, 7 or by wet etching
technology. While Matsushita Electric Ind would claim in 1983 the encapsulation by vacuum pressure bonding
using PVB, Fuji Electric11 Co as well as Nippon Sheet Glass would widen the technique to the use of Silicon and EVA. Beside this modern sheet type of lamination companies like Stanley Electric
Co continued the development of resin lamination
based on Epoxy
. Since 1990 Ricoh KK and Stanley Electric produced complete LED-Displays combining IC chips, liquid crystals and LEDs powered by transparent conductive layers.
Despite newer patents, the main technological questions regarding the mounting of SMD elements on patterned transparent conductive layers on glass
and its lamination was obviously well developed before 1990.
The disadvantage to transport heavy glasses from pure companies processing the sputtering mentioned above to other companies, which would mount SMD LEDs on glass, and to forward these heavy weight flat half fabricated SMD mounted glasses to glass lamination units has driven companies to develop low weight SMD embedded films, which may be transported by air-mail as rolled material.
Standard type of LEDGlass: Transparent LEDGlass:
Special type of LED Glass: Dichroic LEDGlass:
With a current maximum size of 3500 x 1250 mm the transparent metallisation as well as the connection between the films and the SMD/LED elements have to accept rolled packaging, maximum lamination temperatures of 125 °C, and following sheer stress:
a) 10 N measured at an angle of 45 ° at room temperatures
b) 3 N measured at an angle of 45 ° at 125 °C
After lamination the LEDs are fully embedded in PVB/TPU/EVA or in the resin. If at this stage, the glasses are bended, for example while mounting them, the sheer forces will be higher than 10 N and the electrical connections between the SMD / LED and the films might be destroyed. The same problem may occur if resins do shrink more than 3 % while curing.
can easily discharge
(ESD) through SMD elements like sensors or LEDs. Although high voltage (> 10´000 VDC) but micro ampere pulse ESD will not hurt humans, it will damage certain electronic devices. This damage might not appear instantly, but it can build up over time and cause the device to fail. Any time the charge reaches around 10,000 volts, it is likely to discharge to SMD/LED embedded films. As a matter of fact, ESD is the most damaging form of electrical interference associated with SMD Electronics. The following are the most common causes of ESD: Moving people, clothes rubbing together, low humidity (example: dry conditions in PVB laminating rooms), improper grounding, motors in electrical devices, unshielded cables, poor grounding connections, unrolling or moving PVB/EVA/TPU and moving rolls or plastic elements of machines. ESD generally does not occur when the humidity is above 50%. If not working with PVB, use a room humidifier to keep the humidity level above 50% in the work area. One additional low cost options for laminating units is the use of antistatic mats made of rubber or other antistatic materials they stand on while working on the equipment. Some antistatic mats have ground connections that should be connected to the safety ground of an AC power outlet. Also, grounding the working staff in this manner ensures that static charge on their bodies are removed. The use electrostatic blowers or Guns to de-ionise Glass, PVB, EVA or TPU films or even complete laminating rooms is a most efficient way to reduce ESD damages. To reduce the damaging effect of ESD, films are patterned in a way to allow a bypass flow of electricity. To reduce the effect of ESD, each SMD/LED Film or glass should have an internal bypass with an internal resistivity
of 1 – 100 kOhm.
Ongoing developments:
Light-emitting diode
A light-emitting diode is a semiconductor light source. LEDs are used as indicator lamps in many devices and are increasingly used for other lighting...
s. The LEDGlass and its technology is described in different articles, It allows for example glass facades to be used as marketing area or windshield glasses to be used as display. This is the reason, why LEDGlass (which may also be described as LED Glass or LED embedded Glass) is a member of the so called electronic functional glasses. Historically, the vacuum sputtering
Sputtering
Sputtering is a process whereby atoms are ejected from a solid target material due to bombardment of the target by energetic particles. It is commonly used for thin-film deposition, etching and analytical techniques .-Physics of sputtering:...
of metals and transparent conductive oxides on polymers has allowed the development of transparent conductive materials
Transparent conducting film
Transparent conducting films are optically transparent and electrically conductive in thin layers.TCFs for photovoltaic applications have been fabricated from both inorganic and organic materials...
and transparent conductive glass
Glass
Glass is an amorphous solid material. Glasses are typically brittle and optically transparent.The most familiar type of glass, used for centuries in windows and drinking vessels, is soda-lime glass, composed of about 75% silica plus Na2O, CaO, and several minor additives...
. The electrical conductivity of these transparent materials has open a wide window of applications using electronic surface mounted devices
Surface-mount technology
Surface mount technology is a method for constructing electronic circuits in which the components are mounted directly onto the surface of printed circuit boards . An electronic device so made is called a surface mount device...
(SMD) laminated in glass. LEDs and other electronic SMD may be mounted on transparent conductive films, to produce flexible, and ready to laminate
Laminate
A laminate is a material that can be constructed by uniting two or more layers of material together. The process of creating a laminate is lamination, which in common parlance refers to the placing of something between layers of plastic and gluing them with heat and/or pressure, usually with an...
films or directly on transparent conductive glass. While highly flexible film subtrates may be transported by fast and low weight air mail, SMD on metallized glass will result in heavy weight products.
History
In 1910 the French researcher Edouard Benedictus patented the gluing of two glasses by using a polymer based on cellulose acetateCellulose acetate
Cellulose acetate , first prepared in 1865, is the acetate ester of cellulose. Cellulose acetate is used as a film base in photography, as a component in some adhesives, and as a frame material for eyeglasses; it is also used as a synthetic fiber and in the manufacture of cigarette filters and...
. The resulting product called "Triplex" was most interesting in many aspects: Unlike ordinary or tempered glass, which falls apart when fractured laminated glass staid in place. However, before a satisfactory safety glass
Safety glass
Safety glass is glass with additional safety features. Designs include:* Toughened glass * Laminated glass* Wire mesh glass...
could be marketed in commercial quantities, raw materials, including glass, plastic, and bonding agents as well as the manufacturing technique, had to be improved. Different solution were developed, like tough, clear, flexible plastic sheets made of polyvinyl butyral
Polyvinyl butyral
Polyvinyl butyral is a resin usually used for applications that require strong binding, optical clarity, adhesion to many surfaces, toughness and flexibility. It is prepared from polyvinyl alcohol by reaction with butyraldehyde. The major application is laminated safety glass for automobile...
(PVB), ethylene vinyl acetate (EVA) or thermoplastic polyurethane
Thermoplastic polyurethanes
Thermoplastic polyurethanes are a class of polyurethane plastics with many useful properties, including elasticity, transparency, and resistance to oil, grease and abrasion...
(TPU), which could be sandwiched in between glass to create a safe and breakproof material. Today, laminated glass helps keep the building envelope intact, reduces the danger of glass shards, and helps prevent people from falling through sudden openings. Users of laminated glass soon discovered that it also helped reduce noise, block harmful UV rays
Ultraviolet
Ultraviolet light is electromagnetic radiation with a wavelength shorter than that of visible light, but longer than X-rays, in the range 10 nm to 400 nm, and energies from 3 eV to 124 eV...
and protect against break-ins. In cars and in buildings, use of laminated glass continues to grow, increasing safety worldwide.
The first commercially used LEDs were developed in the 1960s by combining three elements: gallium
Gallium
Gallium is a chemical element that has the symbol Ga and atomic number 31. Elemental gallium does not occur in nature, but as the gallium salt in trace amounts in bauxite and zinc ores. A soft silvery metallic poor metal, elemental gallium is a brittle solid at low temperatures. As it liquefies...
, arsenic
Arsenic
Arsenic is a chemical element with the symbol As, atomic number 33 and relative atomic mass 74.92. Arsenic occurs in many minerals, usually in conjunction with sulfur and metals, and also as a pure elemental crystal. It was first documented by Albertus Magnus in 1250.Arsenic is a metalloid...
and phosphorus
Phosphorus
Phosphorus is the chemical element that has the symbol P and atomic number 15. A multivalent nonmetal of the nitrogen group, phosphorus as a mineral is almost always present in its maximally oxidized state, as inorganic phosphate rocks...
to obtain a 655 nm (GaAsP) red light source. As LED technology progressed through the 1970s, additional wavelength
Wavelength
In physics, the wavelength of a sinusoidal wave is the spatial period of the wave—the distance over which the wave's shape repeats.It is usually determined by considering the distance between consecutive corresponding points of the same phase, such as crests, troughs, or zero crossings, and is a...
s became available. The most common materials were GaP green and red, GaAsP orange or high efficiency red and GaAsP yellow, which are still used today. Although the reliability of LEDs has always been superior to that of incandescent, neon
Neon
Neon is the chemical element that has the symbol Ne and an atomic number of 10. Although a very common element in the universe, it is rare on Earth. A colorless, inert noble gas under standard conditions, neon gives a distinct reddish-orange glow when used in either low-voltage neon glow lamps or...
etc., the failure rate
Failure rate
Failure rate is the frequency with which an engineered system or component fails, expressed for example in failures per hour. It is often denoted by the Greek letter λ and is important in reliability engineering....
of early devices was much higher than current technology now achieves. This was due in part to the actual component assembly that was primarily manual in nature. In fact, some GaAlAs LEDs may decrease by 50% after only 50,000 -70,000 hours of operation. To overcome these difficult issues, LED designers turned to laser diode technology
Laser diode
The laser diode is a laser where the active medium is a semiconductor similar to that found in a light-emitting diode. The most common type of laser diode is formed from a p-n junction and powered by injected electric current...
for solutions. This led to the development of InGaAlP (Indium
Indium
Indium is a chemical element with the symbol In and atomic number 49. This rare, very soft, malleable and easily fusible post-transition metal is chemically similar to gallium and thallium, and shows the intermediate properties between these two...
Gallium
Gallium
Gallium is a chemical element that has the symbol Ga and atomic number 31. Elemental gallium does not occur in nature, but as the gallium salt in trace amounts in bauxite and zinc ores. A soft silvery metallic poor metal, elemental gallium is a brittle solid at low temperatures. As it liquefies...
Aluminum Phosphide
Phosphide
In chemistry, a phosphide is a compound of phosphorus with a less electronegative element or elements. Binary compounds are formed with the majority of less electronegative elements with the exception of Hg, Pb, Sb, Bi, Te, Po...
) LEDs. The use of InGaAlP allowed flexibility in the design of LED output color by adjusting the size of the energy band gap
Band gap
In solid state physics, a band gap, also called an energy gap or bandgap, is an energy range in a solid where no electron states can exist. In graphs of the electronic band structure of solids, the band gap generally refers to the energy difference between the top of the valence band and the...
. These developments enabled the use of ultra small LEDs with high reliability for totally new applications.
In 1877 Prof. A. W. Wright of Yale University
Yale University
Yale University is a private, Ivy League university located in New Haven, Connecticut, United States. Founded in 1701 in the Colony of Connecticut, the university is the third-oldest institution of higher education in the United States...
published a paper in the American Journal of Science and Arts on the use of an „electrical deposition apparatus“ to form mirrors and study their properties. There still is some confusion as to whether Wright was using sputtering or gaseous arcing
Corona discharge
In electricity, a corona discharge is an electrical discharge brought on by the ionization of a fluid surrounding a conductor that is electrically energized...
. But there is no doubt, that this early research anticipated later developments, including cathode shielding
Cathodic protection
Cathodic protection is a technique used to control the corrosion of a metal surface by making it the cathode of an electrochemical cell. The simplest method to apply CP is by connecting the metal to be protected with another more easily corroded "sacrificial metal" to act as the anode of the...
, multi-layer coatings and all technologies of sputter deposition
Sputter deposition
Sputter deposition is a physical vapor deposition method of depositing thin films by sputtering, that is ejecting, material from a "target," that is source, which then deposits onto a "substrate," such as a silicon wafer...
. These applications progressed from the simple single layer coatings on plates in the 1930s and 1940s to coatings on flexible materials in the 1950s. This research anticipated the energy crises in the 1970s proving the need for energy conservation
Energy conservation
Energy conservation refers to efforts made to reduce energy consumption. Energy conservation can be achieved through increased efficient energy use, in conjunction with decreased energy consumption and/or reduced consumption from conventional energy sources...
coatings on large areas of glass and polymer webs. As published in Patents of Ford Motors (1989) and Saint Gobain
Saint Gobain
Saint Gobain , also known as Goban, was an Irish Benedictine monk and spiritual student of Saint Fursey at Burgh Castle, Norfolk, England. Born in Ireland. Little else is known of Gobain except that he would have accompanied Fursey on his travel to France where they lived as hermits in the forest...
(1990)), the use of transparent high conductive layers on glass was a quite important solution for pure heating applications. But since the 1980s companies like Sharp
Sharp Corporation
is a Japanese multinational corporation that designs and manufactures electronic products. Headquartered in Abeno-ku, Osaka, Japan, Sharp employs more than 55,580 people worldwide as of June 2011. The company was founded in September 1912 and takes its name from one of its founder's first...
(1983) started to mount small electronic devices (SMDs) like LEDs on transparent conductive glass or films. The patterning of transparent conductive layers was done by laser, 7 or by wet etching
Wet etching
Wet etching may refer to:*Industrial etching*Etching...
technology. While Matsushita Electric Ind would claim in 1983 the encapsulation by vacuum pressure bonding
Laminated glass
Laminated glass is a type of safety glass that holds together when shattered. In the event of breaking, it is held in place by an interlayer, typically of polyvinyl butyral , between its two or more layers of glass. The interlayer keeps the layers of glass bonded even when broken, and its high...
using PVB, Fuji Electric11 Co as well as Nippon Sheet Glass would widen the technique to the use of Silicon and EVA. Beside this modern sheet type of lamination companies like Stanley Electric
William Stanley, Jr.
William Stanley, Jr. was an American physicist born in Brooklyn, New York. In his career, he obtained 129 patents covering a variety of electric devices.-Biography:...
Co continued the development of resin lamination
Laminate
A laminate is a material that can be constructed by uniting two or more layers of material together. The process of creating a laminate is lamination, which in common parlance refers to the placing of something between layers of plastic and gluing them with heat and/or pressure, usually with an...
based on Epoxy
Epoxy
Epoxy, also known as polyepoxide, is a thermosetting polymer formed from reaction of an epoxide "resin" with polyamine "hardener". Epoxy has a wide range of applications, including fiber-reinforced plastic materials and general purpose adhesives....
. Since 1990 Ricoh KK and Stanley Electric produced complete LED-Displays combining IC chips, liquid crystals and LEDs powered by transparent conductive layers.
Despite newer patents, the main technological questions regarding the mounting of SMD elements on patterned transparent conductive layers on glass
Sputter deposition
Sputter deposition is a physical vapor deposition method of depositing thin films by sputtering, that is ejecting, material from a "target," that is source, which then deposits onto a "substrate," such as a silicon wafer...
and its lamination was obviously well developed before 1990.
The disadvantage to transport heavy glasses from pure companies processing the sputtering mentioned above to other companies, which would mount SMD LEDs on glass, and to forward these heavy weight flat half fabricated SMD mounted glasses to glass lamination units has driven companies to develop low weight SMD embedded films, which may be transported by air-mail as rolled material.
Standard type of LEDGlass: Transparent LEDGlass:
Special type of LED Glass: Dichroic LEDGlass:
Current Materials
Current SMD embedded materials, have been optimised for being transported as rolled materials and to be used in processes like vacuum bagging or autoclaving lamination using PVB, EVA, TPU or Resin at temperatures below 125 °C.With a current maximum size of 3500 x 1250 mm the transparent metallisation as well as the connection between the films and the SMD/LED elements have to accept rolled packaging, maximum lamination temperatures of 125 °C, and following sheer stress:
a) 10 N measured at an angle of 45 ° at room temperatures
b) 3 N measured at an angle of 45 ° at 125 °C
After lamination the LEDs are fully embedded in PVB/TPU/EVA or in the resin. If at this stage, the glasses are bended, for example while mounting them, the sheer forces will be higher than 10 N and the electrical connections between the SMD / LED and the films might be destroyed. The same problem may occur if resins do shrink more than 3 % while curing.
Static electricity
Static electricityStatic electricity
Static electricity refers to the build-up of electric charge on the surface of objects. The static charges remain on an object until they either bleed off to ground or are quickly neutralized by a discharge. Static electricity can be contrasted with current electricity, which can be delivered...
can easily discharge
Electrostatic discharge
Electrostatic discharge is a serious issue in solid state electronics, such as integrated circuits. Integrated circuits are made from semiconductor materials such as silicon and insulating materials such as silicon dioxide...
(ESD) through SMD elements like sensors or LEDs. Although high voltage (> 10´000 VDC) but micro ampere pulse ESD will not hurt humans, it will damage certain electronic devices. This damage might not appear instantly, but it can build up over time and cause the device to fail. Any time the charge reaches around 10,000 volts, it is likely to discharge to SMD/LED embedded films. As a matter of fact, ESD is the most damaging form of electrical interference associated with SMD Electronics. The following are the most common causes of ESD: Moving people, clothes rubbing together, low humidity (example: dry conditions in PVB laminating rooms), improper grounding, motors in electrical devices, unshielded cables, poor grounding connections, unrolling or moving PVB/EVA/TPU and moving rolls or plastic elements of machines. ESD generally does not occur when the humidity is above 50%. If not working with PVB, use a room humidifier to keep the humidity level above 50% in the work area. One additional low cost options for laminating units is the use of antistatic mats made of rubber or other antistatic materials they stand on while working on the equipment. Some antistatic mats have ground connections that should be connected to the safety ground of an AC power outlet. Also, grounding the working staff in this manner ensures that static charge on their bodies are removed. The use electrostatic blowers or Guns to de-ionise Glass, PVB, EVA or TPU films or even complete laminating rooms is a most efficient way to reduce ESD damages. To reduce the damaging effect of ESD, films are patterned in a way to allow a bypass flow of electricity. To reduce the effect of ESD, each SMD/LED Film or glass should have an internal bypass with an internal resistivity
Resistivity
Electrical resistivity is a measure of how strongly a material opposes the flow of electric current. A low resistivity indicates a material that readily allows the movement of electric charge. The SI unit of electrical resistivity is the ohm metre...
of 1 – 100 kOhm.
Ongoing developments:
- Separately controlled full colour RGB LEDs for media walls
- Use of high power LEDs
- Use of Infra Red sensoric SMD elements in glass
- Use of film for transparent heating applications
- Use of transparent conductive films for electromagnetic induction sensoric