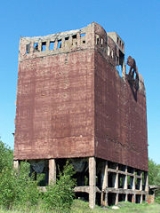
Bergius process
Encyclopedia
The Bergius Process is a method of production of liquid hydrocarbons for use as synthetic fuel
by hydrogenation
of high-volatile bituminous coal at high temperature and pressure. It was first developed by Friedrich Bergius
in 1913, in 1931 Bergius was awarded the Nobel Prize in Chemistry
for his development of high pressure chemistry.
or molybdenum
sulfide
s, tin
or nickel
oleate, and others. Alternatively, iron sulphides present in the coal may have sufficient catalytic activity for the process, which was the original Bergius process.
The mixture is pumped into a reactor
. The reaction occurs at between 400 to 500 °C and 20 to 70 MPa
hydrogen
pressure. The reaction produces heavy oils, middle oils, gasoline, and gases. The overall reaction can be summarized as follows:
(where x = Degrees of Unsaturation
)
The immediate product from the reactor must be stabilized by passing it over a conventional hydrotreating catalyst. The product stream is high in naphthenes and aromatics, low in paraffins and very low in olefins. The different fractions can be passed to further processing (cracking
, reforming)
to output synthetic fuel of desirable quality. If passed through a process such as Platforming, most of the naphthenes are converted to aromatics and the recovered hydrogen recycled to the process. The liquid product from Platforming will contain over 75% aromatics and has a RON of over 105.
Overall, about 97% of input carbon fed directly to the process can be converted into synthetic fuel. However, any carbon used in generating hydrogen will be lost as carbon dioxide, so reducing the overall carbon efficiency of the process.
There is a residue of unreactive tarry compounds mixed with ash from the coal and catalyst. To minimise the loss of carbon in the residue stream, it is necessary to have a low-ash feed. Typically the coal should be <10% ash by weight. The hydrogen required for the process can be also produced from coal or the residue by steam reforming
. A typical hydrogen demand is ~8 kg hydrogen per ton of dry, ash-free coal. Generally, this process is similar to hydrogenation. The output is at three levels: heavy oil, middle oil, gasoline. The middle oil is hydrogenated in order to get more gasoline and the heavy oil is mixed with the coal again and the process restarts. In this way, heavy oil and middle oil fractions are also reused in this process.
are produced by hydrogenation
of lignite
(brown coal). He developed the process well before the commonly-known Fischer-Tropsch process
. Karl Goldschmidt invited him to build an industrial plant at his factory the Th. Goldschmidt AG (now known as Evonik Industries
) in 1914. The production began only in 1919, after the World War I
ended, when the need for fuel was already declining. The technical problems, inflation
and the constant criticism of Franz Joseph Emil Fischer
, which changed to support after a personal demonstration of the process, made the progress slow and Bergius sold his patent to BASF
, where Carl Bosch
worked on it. Before World War II
several plants where built with an annual capacity of 4 million tons of synthetic fuel. These plants were extensively used during World War II to supply Germany with fuel and lubricants.
The Bergius process was extensively used by Nazi Germany
and targeted for bombing during the Oil Campaign of World War II
. At present there are no plants operating the Bergius Process or its derivatives commercially. The largest demonstration plant was the 200 ton per day plant at Bottrop
, Germany, operated by Ruhrkohle
, which ceased operation in 1993. There are reports of the Chinese company constructing a plant with a capacity of 4 000 ton per day. It was expected to become operational in 2007, but there has been no confirmation that this was achieved.
During WWII the United States conducted secret research in converting coal to gasoline at a facility in Louisiana, Missouri
. Located along the Mississippi river, this plant was producing gasoline in commercial quantities by 1948. The Louisiana process method produced automobile gasoline comparable in price with petroleum based gasoline but of a higher quality. The facility was shut down in 1953 by the Eisenhower administration after intense lobbying by the oil industry. Declassified documents detailing the experiments and the production process were systematically destroyed. In the 1980s 16mm microfilm of these documents were discovered in a few Federal Depository Libraries. Within three months researcher requests to view this microfilm were told the canisters were missing. In one case a physical search turned up only the rusty pattern of a 16mm film canister on a steel shelf.
Synthetic fuel
Synthetic fuel or synfuel is a liquid fuel obtained from coal, natural gas, oil shale, or biomass. It may also refer to fuels derived from other solids such as plastics or rubber waste. It may also refer to gaseous fuels produced in a similar way...
by hydrogenation
Hydrogenation
Hydrogenation, to treat with hydrogen, also a form of chemical reduction, is a chemical reaction between molecular hydrogen and another compound or element, usually in the presence of a catalyst. The process is commonly employed to reduce or saturate organic compounds. Hydrogenation typically...
of high-volatile bituminous coal at high temperature and pressure. It was first developed by Friedrich Bergius
Friedrich Bergius
Friedrich Karl Rudolf Bergius was a German chemist known for the Bergius process for producing synthetic fuel from coal, Nobel Prize in Chemistry in recognition of contributions to the invention and development of chemical high-pressure methods...
in 1913, in 1931 Bergius was awarded the Nobel Prize in Chemistry
Nobel Prize in Chemistry
The Nobel Prize in Chemistry is awarded annually by the Royal Swedish Academy of Sciences to scientists in the various fields of chemistry. It is one of the five Nobel Prizes established by the will of Alfred Nobel in 1895, awarded for outstanding contributions in chemistry, physics, literature,...
for his development of high pressure chemistry.
Process
The coal is finely ground and dried in a stream of hot gas. The dry product is mixed with heavy oil recycled from the process. Catalyst is typically added to the mixture. A number of catalysts have been developed over the years, including tungstenTungsten
Tungsten , also known as wolfram , is a chemical element with the chemical symbol W and atomic number 74.A hard, rare metal under standard conditions when uncombined, tungsten is found naturally on Earth only in chemical compounds. It was identified as a new element in 1781, and first isolated as...
or molybdenum
Molybdenum
Molybdenum , is a Group 6 chemical element with the symbol Mo and atomic number 42. The name is from Neo-Latin Molybdaenum, from Ancient Greek , meaning lead, itself proposed as a loanword from Anatolian Luvian and Lydian languages, since its ores were confused with lead ores...
sulfide
Sulfide
A sulfide is an anion of sulfur in its lowest oxidation state of 2-. Sulfide is also a slightly archaic term for thioethers, a common type of organosulfur compound that are well known for their bad odors.- Properties :...
s, tin
Tin
Tin is a chemical element with the symbol Sn and atomic number 50. It is a main group metal in group 14 of the periodic table. Tin shows chemical similarity to both neighboring group 14 elements, germanium and lead and has two possible oxidation states, +2 and the slightly more stable +4...
or nickel
Nickel
Nickel is a chemical element with the chemical symbol Ni and atomic number 28. It is a silvery-white lustrous metal with a slight golden tinge. Nickel belongs to the transition metals and is hard and ductile...
oleate, and others. Alternatively, iron sulphides present in the coal may have sufficient catalytic activity for the process, which was the original Bergius process.
The mixture is pumped into a reactor
Chemical reactor
In chemical engineering, chemical reactors are vessels designed to contain chemical reactions. The design of a chemical reactor deals with multiple aspects of chemical engineering. Chemical engineers design reactors to maximize net present value for the given reaction...
. The reaction occurs at between 400 to 500 °C and 20 to 70 MPa
Pascal (unit)
The pascal is the SI derived unit of pressure, internal pressure, stress, Young's modulus and tensile strength, named after the French mathematician, physicist, inventor, writer, and philosopher Blaise Pascal. It is a measure of force per unit area, defined as one newton per square metre...
hydrogen
Hydrogen
Hydrogen is the chemical element with atomic number 1. It is represented by the symbol H. With an average atomic weight of , hydrogen is the lightest and most abundant chemical element, constituting roughly 75% of the Universe's chemical elemental mass. Stars in the main sequence are mainly...
pressure. The reaction produces heavy oils, middle oils, gasoline, and gases. The overall reaction can be summarized as follows:

Degree of unsaturation
The degree of unsaturation formula is used in organic chemistry to help draw chemical structures. The formula lets the user determine how many rings, double bonds, and triple bonds are present in the compound to be drawn...
)
The immediate product from the reactor must be stabilized by passing it over a conventional hydrotreating catalyst. The product stream is high in naphthenes and aromatics, low in paraffins and very low in olefins. The different fractions can be passed to further processing (cracking
Cracking (chemistry)
In petroleum geology and chemistry, cracking is the process whereby complex organic molecules such as kerogens or heavy hydrocarbons are broken down into simpler molecules such as light hydrocarbons, by the breaking of carbon-carbon bonds in the precursors. The rate of cracking and the end products...
, reforming)
Catalytic reforming
Catalytic reforming is a chemical process used to convert petroleum refinery naphthas, typically having low octane ratings, into high-octane liquid products called reformates which are components of high-octane gasoline...
to output synthetic fuel of desirable quality. If passed through a process such as Platforming, most of the naphthenes are converted to aromatics and the recovered hydrogen recycled to the process. The liquid product from Platforming will contain over 75% aromatics and has a RON of over 105.
Overall, about 97% of input carbon fed directly to the process can be converted into synthetic fuel. However, any carbon used in generating hydrogen will be lost as carbon dioxide, so reducing the overall carbon efficiency of the process.
There is a residue of unreactive tarry compounds mixed with ash from the coal and catalyst. To minimise the loss of carbon in the residue stream, it is necessary to have a low-ash feed. Typically the coal should be <10% ash by weight. The hydrogen required for the process can be also produced from coal or the residue by steam reforming
Steam reforming
Fossil fuel reforming is a method of producing hydrogen or other useful products from fossil fuels such as natural gas. This is achieved in a processing device called a reformer which reacts steam at high temperature with the fossil fuel. The steam methane reformer is widely used in industry to...
. A typical hydrogen demand is ~8 kg hydrogen per ton of dry, ash-free coal. Generally, this process is similar to hydrogenation. The output is at three levels: heavy oil, middle oil, gasoline. The middle oil is hydrogenated in order to get more gasoline and the heavy oil is mixed with the coal again and the process restarts. In this way, heavy oil and middle oil fractions are also reused in this process.
History
Friedrich Bergius developed the process during his habilitation. A techniques for the high-pressure and high-temperature chemistry of carbon-containing substrates yielded in a patent in 1913. In this process liquid hydrocarbons used as synthetic fuelSynthetic fuel
Synthetic fuel or synfuel is a liquid fuel obtained from coal, natural gas, oil shale, or biomass. It may also refer to fuels derived from other solids such as plastics or rubber waste. It may also refer to gaseous fuels produced in a similar way...
are produced by hydrogenation
Hydrogenation
Hydrogenation, to treat with hydrogen, also a form of chemical reduction, is a chemical reaction between molecular hydrogen and another compound or element, usually in the presence of a catalyst. The process is commonly employed to reduce or saturate organic compounds. Hydrogenation typically...
of lignite
Lignite
Lignite, often referred to as brown coal, or Rosebud coal by Northern Pacific Railroad,is a soft brown fuel with characteristics that put it somewhere between coal and peat...
(brown coal). He developed the process well before the commonly-known Fischer-Tropsch process
Fischer-Tropsch process
The Fischer–Tropsch process is a set of chemical reactions that convert a mixture of carbon monoxide and hydrogen into liquid hydrocarbons. The process, a key component of gas to liquids technology, produces a petroleum substitute, typically from coal, natural gas, or biomass for use as synthetic...
. Karl Goldschmidt invited him to build an industrial plant at his factory the Th. Goldschmidt AG (now known as Evonik Industries
Evonik Industries
Evonik Industries is an industrial corporation in Germany owned by RAG Foundation and one of the world´s leading specialty chemicals companies. It was created on 12 September 2007 as a result of restructuring of the mining and technology group RAG...
) in 1914. The production began only in 1919, after the World War I
World War I
World War I , which was predominantly called the World War or the Great War from its occurrence until 1939, and the First World War or World War I thereafter, was a major war centred in Europe that began on 28 July 1914 and lasted until 11 November 1918...
ended, when the need for fuel was already declining. The technical problems, inflation
Inflation
In economics, inflation is a rise in the general level of prices of goods and services in an economy over a period of time.When the general price level rises, each unit of currency buys fewer goods and services. Consequently, inflation also reflects an erosion in the purchasing power of money – a...
and the constant criticism of Franz Joseph Emil Fischer
Franz Joseph Emil Fischer
Franz Joseph Emil Fischer was a German chemist. He and Hans Tropsch discovered the Fischer-Tropsch process. With Hans Schrader he developed the Fischer Assay, a standardized laboratory test for determining the oil yield from oil shale to be expected from a conventional shale oil extraction...
, which changed to support after a personal demonstration of the process, made the progress slow and Bergius sold his patent to BASF
BASF
BASF SE is the largest chemical company in the world and is headquartered in Germany. BASF originally stood for Badische Anilin- und Soda-Fabrik . Today, the four letters are a registered trademark and the company is listed on the Frankfurt Stock Exchange, London Stock Exchange, and Zurich Stock...
, where Carl Bosch
Carl Bosch
Carl Bosch was a German chemist and engineer and Nobel laureate in chemistry. He was a pioneer in the field of high-pressure industrial chemistry and founder of IG Farben, at one point the world's largest chemical company....
worked on it. Before World War II
World War II
World War II, or the Second World War , was a global conflict lasting from 1939 to 1945, involving most of the world's nations—including all of the great powers—eventually forming two opposing military alliances: the Allies and the Axis...
several plants where built with an annual capacity of 4 million tons of synthetic fuel. These plants were extensively used during World War II to supply Germany with fuel and lubricants.
Use
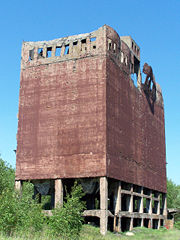
Nazi Germany
Nazi Germany , also known as the Third Reich , but officially called German Reich from 1933 to 1943 and Greater German Reich from 26 June 1943 onward, is the name commonly used to refer to the state of Germany from 1933 to 1945, when it was a totalitarian dictatorship ruled by...
and targeted for bombing during the Oil Campaign of World War II
Oil Campaign of World War II
The Allied Oil Campaign of World War II was directed at facilities supplying Nazi Germany with petroleum, oil, and lubrication products...
. At present there are no plants operating the Bergius Process or its derivatives commercially. The largest demonstration plant was the 200 ton per day plant at Bottrop
Bottrop
Bottrop is a city in west central Germany, on the Rhine-Herne Canal, in North Rhine-Westphalia. Located in the Ruhr industrial area, Bottrop adjoins Essen, Oberhausen, Gladbeck and Dorsten. The city had been a coal-mining and rail center and contains factories producing coal-tar derivatives,...
, Germany, operated by Ruhrkohle
RAG Aktiengesellschaft
RAG AG, formerly Ruhrkohle AG, is the largest German coal mining corporation. The company headquarters are in Herne in the Ruhr area. The company was founded on 27 November 1968, consolidating several coalmining corporations into the Ruhrkohle AG....
, which ceased operation in 1993. There are reports of the Chinese company constructing a plant with a capacity of 4 000 ton per day. It was expected to become operational in 2007, but there has been no confirmation that this was achieved.
During WWII the United States conducted secret research in converting coal to gasoline at a facility in Louisiana, Missouri
Louisiana, Missouri
Louisiana is a city in Pike County, Missouri, United States. The population was 3,863 at the 2000 census, making it the largest city in Pike Couunty. Louisiana is located in northeast Missouri, on the Mississippi River south of Hannibal....
. Located along the Mississippi river, this plant was producing gasoline in commercial quantities by 1948. The Louisiana process method produced automobile gasoline comparable in price with petroleum based gasoline but of a higher quality. The facility was shut down in 1953 by the Eisenhower administration after intense lobbying by the oil industry. Declassified documents detailing the experiments and the production process were systematically destroyed. In the 1980s 16mm microfilm of these documents were discovered in a few Federal Depository Libraries. Within three months researcher requests to view this microfilm were told the canisters were missing. In one case a physical search turned up only the rusty pattern of a 16mm film canister on a steel shelf.
See also
- Synthetic Liquid Fuels ProgramSynthetic Liquid Fuels ProgramThe Synthetic Liquid Fuels Program was a program run by the United States Bureau of Mines to create the technology to produce synthetic fuel from coal. It was initiated in 1944 during World War II...
- Fischer-Tropsch processFischer-Tropsch processThe Fischer–Tropsch process is a set of chemical reactions that convert a mixture of carbon monoxide and hydrogen into liquid hydrocarbons. The process, a key component of gas to liquids technology, produces a petroleum substitute, typically from coal, natural gas, or biomass for use as synthetic...
- Karrick processKarrick processThe Karrick process is a low-temperature carbonization and pyrolysis process of carbonaceous materials. Although primarily meant for coal carbonization, it also could be used for processing of oil shale, lignite or any carbonaceous materials. These are heated at to in the absence of air to...
External links
- The Early Days of Coal Research, U.S. Department of Energy webpage