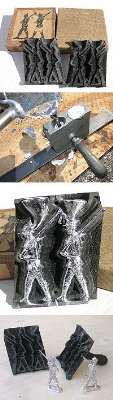
Permanent mold casting
Encyclopedia
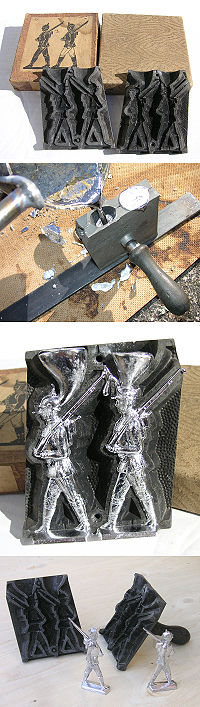
Molding (process)
Molding or moulding is the process of manufacturing by shaping pliable raw material using a rigid frame or model called a pattern....
("permanent molds"), usually made from metal
Metal
A metal , is an element, compound, or alloy that is a good conductor of both electricity and heat. Metals are usually malleable and shiny, that is they reflect most of incident light...
. The most common process uses gravity to fill the mold, however gas pressure or a vacuum
Vacuum
In everyday usage, vacuum is a volume of space that is essentially empty of matter, such that its gaseous pressure is much less than atmospheric pressure. The word comes from the Latin term for "empty". A perfect vacuum would be one with no particles in it at all, which is impossible to achieve in...
are also used. A variation on the typical gravity casting process, called slush casting, produces hollow castings. Common casting metals are aluminum, magnesium
Magnesium
Magnesium is a chemical element with the symbol Mg, atomic number 12, and common oxidation number +2. It is an alkaline earth metal and the eighth most abundant element in the Earth's crust and ninth in the known universe as a whole...
, and copper
Copper
Copper is a chemical element with the symbol Cu and atomic number 29. It is a ductile metal with very high thermal and electrical conductivity. Pure copper is soft and malleable; an exposed surface has a reddish-orange tarnish...
alloys. Other materials include tin
Tin
Tin is a chemical element with the symbol Sn and atomic number 50. It is a main group metal in group 14 of the periodic table. Tin shows chemical similarity to both neighboring group 14 elements, germanium and lead and has two possible oxidation states, +2 and the slightly more stable +4...
, zinc
Zinc
Zinc , or spelter , is a metallic chemical element; it has the symbol Zn and atomic number 30. It is the first element in group 12 of the periodic table. Zinc is, in some respects, chemically similar to magnesium, because its ion is of similar size and its only common oxidation state is +2...
, and lead
Lead
Lead is a main-group element in the carbon group with the symbol Pb and atomic number 82. Lead is a soft, malleable poor metal. It is also counted as one of the heavy metals. Metallic lead has a bluish-white color after being freshly cut, but it soon tarnishes to a dull grayish color when exposed...
alloys and iron
Iron
Iron is a chemical element with the symbol Fe and atomic number 26. It is a metal in the first transition series. It is the most common element forming the planet Earth as a whole, forming much of Earth's outer and inner core. It is the fourth most common element in the Earth's crust...
and steel are also cast in graphite
Graphite
The mineral graphite is one of the allotropes of carbon. It was named by Abraham Gottlob Werner in 1789 from the Ancient Greek γράφω , "to draw/write", for its use in pencils, where it is commonly called lead . Unlike diamond , graphite is an electrical conductor, a semimetal...
molds.
Typical parts include gear
Gear
A gear is a rotating machine part having cut teeth, or cogs, which mesh with another toothed part in order to transmit torque. Two or more gears working in tandem are called a transmission and can produce a mechanical advantage through a gear ratio and thus may be considered a simple machine....
s, spline
Spline
Spline can refer to:* Spline , a mating feature for rotating elements* Spline , a mathematical function used for interpolation or smoothing* Smoothing spline, a method of smoothing using a spline function...
s, wheel
Wheel
A wheel is a device that allows heavy objects to be moved easily through rotating on an axle through its center, facilitating movement or transportation while supporting a load, or performing labor in machines. Common examples found in transport applications. A wheel, together with an axle,...
s, gear housings, pipe fitting
Pipe fitting
Pipe fitting is the occupation of installing or repairing piping or tubing systems that convey liquid, gas, and occasionally solid materials...
s, fuel injection housings, and automotive engine piston
Piston
A piston is a component of reciprocating engines, reciprocating pumps, gas compressors and pneumatic cylinders, among other similar mechanisms. It is the moving component that is contained by a cylinder and is made gas-tight by piston rings. In an engine, its purpose is to transfer force from...
s.
Process
There are four main types of permanent mold casting: gravity, slush, low-pressure, and vacuum.Gravity process
The gravity process begins by preheating the mold to 150-200 °C (300-400 °F) to ease the flow and reduce thermal damage to the casting. The mold cavity is then coated with a refractoryRefractory
A refractory material is one that retains its strength at high temperatures. ASTM C71 defines refractories as "non-metallic materials having those chemical and physical properties that make them applicable for structures, or as components of systems, that are exposed to environments above...
material or a mold wash, which prevents the casting from sticking to the mold and prolongs the mold life. Any sand or metal cores are then installed and the mold is clamped shut. Molten metal is then poured into the mold. Soon after solidification the mold is opened and the casting removed to reduce chances of hot tears. The process is then started all over again, but preheating is not required because the heat from the previous casting is adequate and the refractory coating should last several castings. Because this process is usually carried out on large production run workpieces automated equipment is used to coat the mold, pour the metal, and remove the casting.
The metal is poured at the lowest practical temperature in order to minimize cracks and porosity. The pouring temperature can range greatly depending on the casting material; for instance zinc alloys are poured at approximately 700 °F (371.1 °C), while gray iron is poured at approximately 2500 °F (1,371.1 °C).
Mold
Molds for the casting process consist of two halves. Casting molds are usually formed from gray cast iron because it has about the best thermal fatigue resistance, but other materials include steel, bronze, and graphite. These metals are chosen because of their resistance to erosion and thermal fatigue. They are usually not very complex because the mold offers no collapsibility to compensate for shrinkage. Instead the mold is opened as soon as the casting is solidified, which prevents hot tears. Cores can be used and are usually made from sand or metal.As stated above, the mold is heated prior to the first casting cycle and then used continuously in order to maintain as uniform a temperature as possible during the cycles. This decreases thermal fatigue, facilitates metal flow, and helps control the cooling rate of the casting metal.
Venting usually occurs through the slight crack between the two mold halves, but if this is not enough then very small vent holes are used. They are small enough to let the air escape but not the molten metal. A riser
Riser (casting)
A riser, also known as a feeder, is a reservoir built into a metal casting mold to prevent cavities due to shrinkage. Most metals are less dense as a liquid than as a solid so castings shrink upon cooling, which can leave a void at the last point to solidify...
must also be included to compensate for shrinkage. This usually limits the yield to less than 60%.
Mechanical ejectors in the form of pins are used when coatings are not enough to remove casts from the molds. These pins are placed throughout the mold and usually leave small round impressions on the casting.
Slush
Slush casting is a variant of permanent molding casting to create a hollow casting or hollow cast. In the process the material is poured into the mold and allowed to cool until a shell of material forms in the mold. The remaining liquid is then poured out to leave a hollow shell. The resulting casting has good surface detail but the wall thickness can vary. The process is usually used to cast ornamentalOrnamental
Ornamental may refer to:*Ornamental grass, a type of grass grown as a decoration*Ornamental iron, mild steel that has been formed into decorative shapes, similar to wrought iron work*Ornamental plant, a plant that is grown for its ornamental qualities...
products, such as candlestick
Candlestick
A candlestick, chamberstick, or candelabrum is a holder for one or more candles, used for illumination, rituals, or decorative purposes. The name 'candlestick' derives from the fact that it is usually tall and stick-shaped.Candlesticks are also called candle holders...
s, lamp bases, and statuary, from low-melting-point materials. A similar technique is used to make hollow chocolate figures for Easter
Easter
Easter is the central feast in the Christian liturgical year. According to the Canonical gospels, Jesus rose from the dead on the third day after his crucifixion. His resurrection is celebrated on Easter Day or Easter Sunday...
and Christmas
Christmas
Christmas or Christmas Day is an annual holiday generally celebrated on December 25 by billions of people around the world. It is a Christian feast that commemorates the birth of Jesus Christ, liturgically closing the Advent season and initiating the season of Christmastide, which lasts twelve days...
.
The method was developed by William Britain
W. Britain
The W. Britain brand name of toy and collectable soldiers is derived from a company founded by William Britain Jr., a British toy manufacturer, who in 1893 invented the process of hollow casting in lead, and revolutionized the production of toy soldiers. The company quickly became the industry...
in 1893 for the production of lead toy soldier
Toy soldier
A toy soldier is a miniature figurine that represents a soldier. The term applies to depictions of uniformed military personnel from all eras, and includes knights, cowboys, pirates, and other subjects that involve combat-related themes. Toy soldiers vary from simple playthings to highly realistic...
s. It uses less material than solid casting, and results in a lighter and less expensive product. Hollow cast figures generally have a small hole where the excess liquid was poured out.
Hollow casting is also used extensively for vitreous china products, such as sinks, urinals, and toilets.
Low-pressure
Low-pressure permanent mold (LPPM) casting uses a gas at low pressure, usually between 3 and 15 psig (20 to 100 kPag) to push the molten metal into the mold cavity. The pressure is applied to the top of the pool of liquid, which forces the molten metal up a refractory pouring tube and finally into the bottom of the mold. The pouring tube extends to the bottom of the ladle so that the material being pushed into the mold is exceptionally clean. No risers are required because the applied pressure forces molten metal in to compensate for shrinkage. Yields are usually greater than 85% because there is no riser and any metal in the pouring tube just falls back into the ladle for reuse.The vast majority of LPPM casting are from aluminum and magnesium, but some are copper alloys. Advantages include very little turbulence when filling the mold because of the constant pressure, which minimizes gas porosity and dross
Dross
Dross is a mass of solid impurities floating on a molten metal. It appears usually on the melting of low-melting-point metals or alloys such as tin, lead, zinc or aluminium, or by oxidation of the metal. It can also consist of impurities such as paint leftovers...
formation. Mechanical properties are about 5% better than gravity permanent mold castings. The disadvantage is that cycles times are longer than gravity permanent mold castings.
Vacuum
Vacuum permanent mold casting retains all of the advantages of LPPM casting, plus the dissolved gases in the molten metal are minimized and molten metal cleanliness is even better. The process can handle thin-walled profiles and gives an excellent surface finishSurface finish
Surface finish, also known as surface texture, is the characteristics of a surface. It has three components: lay, surface roughness, and waviness.-Lay:...
. Mechanical properties are usually 10 to 15% better than gravity permanent mold castings. The process is limited in weight to 0.2 kilogram.
Advantages and disadvantages
The main advantages are the reusable mold, good surface finish, and good dimensional accuracy. Typical tolerances are 0.4 mm for the first 25 mm (0.015 in for the first inch) and 0.02 mm for each additional centimeter (0.002 in per in); if the dimension crosses the parting lineParting line
A parting line in moldmaking is the place where two or more parts of the mold meet. At times, either because the mold halves do not meet with enough precision or because injection pressure is high, material will creep into the space between the molds. This material is generally called molding...
add an additional 0.25 mm (0.00984251968503937 in). Typical surface finishes are 2.5 to 7.5 μm (100–250 μin) RMS
RMS
-Science and technology:* Root mean square, a concept encapsulating the "average", in some sense, of a quantity. Frequently encountered in statistics, the physical sciences and electronics...
. A draft of 2 to 3° is required. Wall thicknesses are limited to 3 millimetre. Typical part sizes range from 100 g to 75 kg (several ounces to 150 lb). Other advantages include the ease of inducing directional solidification
Directional solidification
Directional solidification and progressive solidification describe types of solidification within castings. Directional solidification describes solidification that occurs from farthest end of the casting and works its way towards the sprue...
by changing the mold wall thickness or by heating or cooling portions of the mold. The fast cooling rates created by using a metal mold results in a finer grain
Crystallite
Crystallites are small, often microscopic crystals that, held together through highly defective boundaries, constitute a polycrystalline solid. Metallurgists often refer to crystallites as grains.- Details :...
structure than sand casting. Retractable metal cores can be used to create undercuts
Undercut (manufacturing)
In manufacturing, an undercut is a special type of recessed surface. In turning it refers to a recess in a diameter. In machining it refers to a recess in a corner. In molding it refers to a feature that cannot be molded using only a single pull mold...
while maintaining a quick action mold.
There are three main disadvantages: high tooling cost, limited to low-melting-point metals, and short mold life. The high tooling costs make this process uneconomical for small production runs. When the process is used to cast steel or iron the mold life is extremely short. For lower melting point metals the mold life is longer but thermal fatigue and erosion usually limit the life to 10,000 to 120,000 cycles. The mold life is dependent on four factors: the mold material, the pouring temperature, the mold temperature, and the mold configuration. The pouring temperature is dependent on the casting metal, but the higher the pouring temperature the shorter the mold life. A high pouring temperature can also induce shrinkage problems and create longer cycle times. If the mold temperature is too low misruns are produced, but if the mold temperature is too high then the cycle time is prolonged and mold erosion is increased. Large differences in section thickness in the mold or casting can decrease mold life as well.