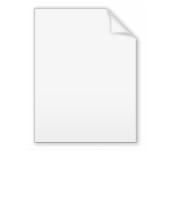
Directional solidification
Encyclopedia
Directional solidification and progressive solidification describe types of solidification within casting
s. Directional solidification describes solidification that occurs from farthest end of the casting and works its way towards the sprue. Progressive solidification, also known as parallel solidification, is solidification that starts at the walls of the casting and progresses perpendicular from that surface.
s and alloys shrink as the material changes from a liquid state to a solid state. Therefore, if liquid material is not available to compensate for this shrinkage a shrinkage defect forms. When progressive solidification dominates over directional solidification a shrinkage defect will form.
The geometrical shape of the mold cavity has direct effect on progressive and directional solidification. At the end of tunnel type geometries divergent heat flow occurs, which causes that area of the casting to cool faster than surrounding areas; this is called an end effect. Large cavities do not cool as quickly as surrounding areas because there is less heat flow; this is called a riser effect. Also note that corners can create divergent or convergent (also known as hot spots) heat flow areas.
In order to induce directional solidification chills, risers
, insulating sleeves, control of pouring rate, and pouring temperature can be utilized.
Directional solidification can be used as a purification process. Since most impurities will be more soluble in the liquid than in the solid phase during solidification, impurities will be "pushed" by the solidification front, causing much of the finished casting to have a lower concentration of impurities than the feedstock material, while the last solidified metal will be enriched with impurities. This last part of the metal can be scrapped or recycled. The suitability of directional solidification in removing a specific impurity from a certain metal depends on the partition coefficient
of the impurity in the metal in question, as described by the Scheil equation
. Directional solidification is frequently employed as a purification step in the production of multicrystalline silicon
for solar cells.
Casting
In metalworking, casting involves pouring liquid metal into a mold, which contains a hollow cavity of the desired shape, and then allowing it to cool and solidify. The solidified part is also known as a casting, which is ejected or broken out of the mold to complete the process...
s. Directional solidification describes solidification that occurs from farthest end of the casting and works its way towards the sprue. Progressive solidification, also known as parallel solidification, is solidification that starts at the walls of the casting and progresses perpendicular from that surface.
Theory
Most metalMetal
A metal , is an element, compound, or alloy that is a good conductor of both electricity and heat. Metals are usually malleable and shiny, that is they reflect most of incident light...
s and alloys shrink as the material changes from a liquid state to a solid state. Therefore, if liquid material is not available to compensate for this shrinkage a shrinkage defect forms. When progressive solidification dominates over directional solidification a shrinkage defect will form.
The geometrical shape of the mold cavity has direct effect on progressive and directional solidification. At the end of tunnel type geometries divergent heat flow occurs, which causes that area of the casting to cool faster than surrounding areas; this is called an end effect. Large cavities do not cool as quickly as surrounding areas because there is less heat flow; this is called a riser effect. Also note that corners can create divergent or convergent (also known as hot spots) heat flow areas.
In order to induce directional solidification chills, risers
Riser (casting)
A riser, also known as a feeder, is a reservoir built into a metal casting mold to prevent cavities due to shrinkage. Most metals are less dense as a liquid than as a solid so castings shrink upon cooling, which can leave a void at the last point to solidify...
, insulating sleeves, control of pouring rate, and pouring temperature can be utilized.
Directional solidification can be used as a purification process. Since most impurities will be more soluble in the liquid than in the solid phase during solidification, impurities will be "pushed" by the solidification front, causing much of the finished casting to have a lower concentration of impurities than the feedstock material, while the last solidified metal will be enriched with impurities. This last part of the metal can be scrapped or recycled. The suitability of directional solidification in removing a specific impurity from a certain metal depends on the partition coefficient
Partition coefficient
In chemistry and the pharmaceutical sciences, a partition- or distribution coefficient is the ratio of concentrations of a compound in the two phases of a mixture of two immiscible solvents at equilibrium. The terms "gas/liquid partition coefficient" and "air/water partition coefficient" are...
of the impurity in the metal in question, as described by the Scheil equation
Scheil equation
In metallurgy, the Scheil-Gulliver equation describes solute redistribution during solidification of an alloy. This approach approximates non-equilibrium solidification by assuming a local equilibrium of the advancing solidification front at the solid-liquid interface...
. Directional solidification is frequently employed as a purification step in the production of multicrystalline silicon
Silicon
Silicon is a chemical element with the symbol Si and atomic number 14. A tetravalent metalloid, it is less reactive than its chemical analog carbon, the nonmetal directly above it in the periodic table, but more reactive than germanium, the metalloid directly below it in the table...
for solar cells.