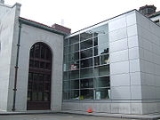
Peening
Encyclopedia

Metal
A metal , is an element, compound, or alloy that is a good conductor of both electricity and heat. Metals are usually malleable and shiny, that is they reflect most of incident light...
's surface to improve its material properties, usually by mechanical means such as hammer blows or by blasting with shot (shot peening
Shot peening
Shot peening is a cold working process used to produce a compressive residual stress layer and modify mechanical properties of metals. It entails impacting a surface with shot with force sufficient to create plastic deformation...
). Peening is normally a cold work process (laser peening
Laser peening
Laser peening, or laser shock peening , is the process of hardening or peening metal using a powerful laser. Laser peening can impart a layer of residual compressive stress on a surface that is four times deeper than that attainable from conventional shot peening treatments. A coating, usually...
being a notable exception). It tends to expand the surface of the cold metal, thereby inducing compressive stresses or relieving tensile stresses already present. Peening can also encourage strain hardening of the surface metal.
Residual stress
Plastic deformation from peening induces a residual compressive stress in a peened surface, along with tensile stress in the interior. This stress state resembles the one seen in toughened glassToughened glass
Toughened or tempered glass is a type of safety glass processed by controlled thermal or chemical treatments to increase its strength compared with normal glass. Tempering creates balanced internal stresses which cause the glass, when broken, to crumble into small granular chunks instead of...
, and is useful for similar reasons.
Surface compressive stresses confer resistance to metal fatigue
Fatigue (material)
'In materials science, fatigue is the progressive and localized structural damage that occurs when a material is subjected to cyclic loading. The nominal maximum stress values are less than the ultimate tensile stress limit, and may be below the yield stress limit of the material.Fatigue occurs...
and to some forms of corrosion
Corrosion
Corrosion is the disintegration of an engineered material into its constituent atoms due to chemical reactions with its surroundings. In the most common use of the word, this means electrochemical oxidation of metals in reaction with an oxidant such as oxygen...
, since cracks will not grow in a compressive environment. The benefit comes at the expense of higher tensile stresses deeper in the part. However, the fatigue properties of the part will be improved since the stresses are normally significantly higher at the surface in part due to surface imperfections and damage.
Work hardening
Cold work also serves to harden the material's surface. This makes cracks less likely to form at the surface and provides resistance to abrasionAbrasion (mechanical)
Abrasion is the process of scuffing, scratching, wearing down, marring, or rubbing away. It can be intentionally imposed in a controlled process using an abrasive...
. When a metal undergoes strain hardening its yield strength increases but its ductility
Ductility
In materials science, ductility is a solid material's ability to deform under tensile stress; this is often characterized by the material's ability to be stretched into a wire. Malleability, a similar property, is a material's ability to deform under compressive stress; this is often characterized...
decreases. Strain hardening actually increases the number of dislocation
Dislocation
In materials science, a dislocation is a crystallographic defect, or irregularity, within a crystal structure. The presence of dislocations strongly influences many of the properties of materials...
s in the crystal lattice of the material. When a material has a great number of dislocations, plastic deformation is hindered, and the material will continue to behave in an elastic way well beyond the elastic yield stress of the non-strain hardened material.
Copper
Copper
Copper is a chemical element with the symbol Cu and atomic number 29. It is a ductile metal with very high thermal and electrical conductivity. Pure copper is soft and malleable; an exposed surface has a reddish-orange tarnish...
and other malleable metals respond well to strain hardening. Some forms of copper, such as ductile wire, are easily deformed, yet beaten copper articles are quite stiff. Strain hardening may be reversed by annealing
Annealing (metallurgy)
Annealing, in metallurgy and materials science, is a heat treatment wherein a material is altered, causing changes in its properties such as strength and hardness. It is a process that produces conditions by heating to above the recrystallization temperature, maintaining a suitable temperature, and...
.
Hand peening may be performed using a peening hammer
Ball-peen hammer
A ball-peen hammer, also known as a machinist's hammer, is a type of peening hammer used in metalworking. It is distinguished from a point-peen hammer or chisel-peen hammer by having a hemispherical head...
. It is still used today in the hand manufacture of high quality cutting blades.
Use with welding
Hand peening may also be performed after weldingWelding
Welding is a fabrication or sculptural process that joins materials, usually metals or thermoplastics, by causing coalescence. This is often done by melting the workpieces and adding a filler material to form a pool of molten material that cools to become a strong joint, with pressure sometimes...
to help relieve the tensile stresses that develop in the weld metal and surrounding base metal on cooling. The level of reduction in tensile stress is minimal and only occurs on or near to the weld surface. Other methods like heat spots if applicable help reduce residual tensile stresses. Peening will induce a higher hardness in to the weld and this is something that should be avoided. For this reason peening is not normally accepted by the majority of codes, standards or specifications (ex. ASME B31.3 para 328.5.1 (d)). Any peening that is carried out on a weld should have been carried out on the weld procedure qualification test piece.
The welding procedure qualification test piece replicates all of the essential variables that will be used in production welding. If the weld is peened during the qualification of a welding procedure the subsequent mechanical testing of the procedure qualification test piece will demonstrate the mechanical properties of the weld. These mechanical properties must as a minimum match the mechanical properties of the materials that have been welded together. If they do not the procedure has failed and the welding procedure is not acceptable for use in production welding. Peening should only be carried out on a production weld where the procedure test piece has been peened.
History
The first published article about peening was written in Germany in 1929 and was specifically about shot peening. The first patent for shot peening was also taken out in Germany in 1934, however it was never commercially implemented. In 1930, a few engineers at BuickBuick
Buick is a premium brand of General Motors . Buick models are sold in the United States, Canada, Mexico, China, Taiwan, and Israel, with China being its largest market. Buick holds the distinction as the oldest active American make...
, independent of the Germans, noticed that "shot blasted" (as it was originally termed) springs had a much better fatigue life than the springs that were not. The process was then commercially used in the automotive industry to overcome fatigue issues. Zimmerli was the first to do research on it, publishing a report in 1940, but John Almen was the one who did the most extensive research on the topic. Almen helped expand shot peening to the aircraft
Aircraft
An aircraft is a vehicle that is able to fly by gaining support from the air, or, in general, the atmosphere of a planet. An aircraft counters the force of gravity by using either static lift or by using the dynamic lift of an airfoil, or in a few cases the downward thrust from jet engines.Although...
industry during World War 2.
By 1950, peening became an accepted process and was being included in engineering literature. In the same year peen forming was invented to form the wing skin of the Super Constellation aircraft.
See also
- Almen stripAlmen stripAn Almen strip is a thin strip of SAE 1070 steel used to quantify the intensity of a shot peening process.Developed and patented by John O. Almen, the strip was originally supported by 2 knife edges; later improvements see it being supported on 4 small balls...
- Case hardeningCase hardeningCase hardening or surface hardening is the process of hardening the surface of a metal, often a low carbon steel, by infusing elements into the material's surface, forming a thin layer of a harder alloy...
- Heat treatmentHeat treatmentHeat treating is a group of industrial and metalworking processes used to alter the physical, and sometimes chemical, properties of a material. The most common application is metallurgical. Heat treatments are also used in the manufacture of many other materials, such as glass...
- Peen platingPeen platingMechanical plating, also known as peen plating, mechanical deposition, or impact plating, is a plating process that imparts the coating by cold welding fine metal particles to a workpiece. Mechanical galvanization is the same process, but applies to coatings that are thicker than . It is commonly...
- Ultrasonic impact treatmentUltrasonic impact treatmentUltrasonic impact treatment is a method of metal improvement that utilizes ultrasonic energy. The physical characteristics: controlled residual compressive stress, grain refinement and grain size reduction...