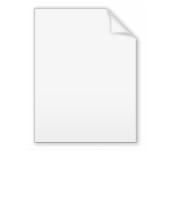
Ultrasonic impact treatment
Encyclopedia
Ultrasonic impact treatment (UIT) is a method of metal
improvement that utilizes ultrasonic energy. The physical characteristics: controlled residual compressive stress
, grain refinement and grain
size reduction. Low and high cycle fatigue
are enhanced and have been documented to provide increases up to ten times greater than non-UIT specimens.
pins. These transfer pins are free to move axially between the resonant body and the treated surface.
When the tool, made up of the ultrasonic transducer, pins and other components, comes into contact with the work piece it acoustically couples with the work piece, creating harmonic resonance. This harmonic resonance is performed at a carefully calibrated frequency, to which metals respond very favorably, resulting in compressive residual stress, stress relief and grain structure improvements.
Depending on the desired effects of treatment a combination of different frequencies and displacement amplitude is applied. These frequencies range between 25 and 55 kHz, with the displacement amplitude of the resonant body of between 22 um.
(PLC), the frequency and amplitude of UIT are easily set and maintained, thus removing a significant portion of operator dependency. UIT can also be mechanically controlled, thus providing repeatability of results from one application to the next. Examples of mechanical control employed with UIT include:
With these types of controlled applications, the surface finish of the work piece is highly controllable.
For many applications, UIT is most effectively employed by hand. The high portability of the UIT system enables travel to austere locations and hard to reach places. The flexibility that is facilitated by variations in the tool configuration ensures that access to very tight locations is possible.
UIT's effectiveness has been illustrated on the following metals, among others:
n scientists under the leadership of Dr. Efim Statnikov. Originally developed and utilized to enhance the fatigue and corrosion attributes of ship and submarine structures, UIT has been utilized in aerospace, mining, offshore drilling, shipbuilding, infrastructure, automotive, energy production and other industries.
The use of UIT on draglines and other heavy equipment in the mining industry has resulted in increased production and has decreased downtime and maintenance costs.
UIT is employed on drive shafts and crank shafts in a number of industries. Results show that UIT increases shaft life by over 3X.
The US Navy uses UIT to address cracked areas in certain aluminum decks. Without UIT, crack repairs resulted in almost immediate re-cracking. With UIT, repairs have shown to last over eight months without cracks.
IIW PUBLICATIONS:
Metal
A metal , is an element, compound, or alloy that is a good conductor of both electricity and heat. Metals are usually malleable and shiny, that is they reflect most of incident light...
improvement that utilizes ultrasonic energy. The physical characteristics: controlled residual compressive stress
Residual stress
Residual stresses are stresses that remain after the original cause of the stresses has been removed. They remain along a cross section of the component, even without the external cause. Residual stresses occur for a variety of reasons, including inelastic deformations and heat treatment...
, grain refinement and grain
Crystallite
Crystallites are small, often microscopic crystals that, held together through highly defective boundaries, constitute a polycrystalline solid. Metallurgists often refer to crystallites as grains.- Details :...
size reduction. Low and high cycle fatigue
Fatigue (material)
'In materials science, fatigue is the progressive and localized structural damage that occurs when a material is subjected to cyclic loading. The nominal maximum stress values are less than the ultimate tensile stress limit, and may be below the yield stress limit of the material.Fatigue occurs...
are enhanced and have been documented to provide increases up to ten times greater than non-UIT specimens.
Theory
UIT is based on producing ultrasonic waves via an electro-mechanical transducer, and delivering those waves into the workpiece. An acoustically tuned body is brought to resonance by energizing an ultrasonic transducer. The energy generated from these high frequency impulses is imparted to the treated surface through the contact of specially designed steelSteel
Steel is an alloy that consists mostly of iron and has a carbon content between 0.2% and 2.1% by weight, depending on the grade. Carbon is the most common alloying material for iron, but various other alloying elements are used, such as manganese, chromium, vanadium, and tungsten...
pins. These transfer pins are free to move axially between the resonant body and the treated surface.
When the tool, made up of the ultrasonic transducer, pins and other components, comes into contact with the work piece it acoustically couples with the work piece, creating harmonic resonance. This harmonic resonance is performed at a carefully calibrated frequency, to which metals respond very favorably, resulting in compressive residual stress, stress relief and grain structure improvements.
Depending on the desired effects of treatment a combination of different frequencies and displacement amplitude is applied. These frequencies range between 25 and 55 kHz, with the displacement amplitude of the resonant body of between 22 um.
Application
UIT is highly controllable. Incorporating a programmable logic controllerProgrammable logic controller
A programmable logic controller or programmable controller is a digital computer used for automation of electromechanical processes, such as control of machinery on factory assembly lines, amusement rides, or light fixtures. PLCs are used in many industries and machines...
(PLC), the frequency and amplitude of UIT are easily set and maintained, thus removing a significant portion of operator dependency. UIT can also be mechanically controlled, thus providing repeatability of results from one application to the next. Examples of mechanical control employed with UIT include:
- CNC milling machines
- LatheLatheA lathe is a machine tool which rotates the workpiece on its axis to perform various operations such as cutting, sanding, knurling, drilling, or deformation with tools that are applied to the workpiece to create an object which has symmetry about an axis of rotation.Lathes are used in woodturning,...
s - Robotic control
- Weld tractors
With these types of controlled applications, the surface finish of the work piece is highly controllable.
For many applications, UIT is most effectively employed by hand. The high portability of the UIT system enables travel to austere locations and hard to reach places. The flexibility that is facilitated by variations in the tool configuration ensures that access to very tight locations is possible.
UIT's effectiveness has been illustrated on the following metals, among others:
- AluminiumAluminiumAluminium or aluminum is a silvery white member of the boron group of chemical elements. It has the symbol Al, and its atomic number is 13. It is not soluble in water under normal circumstances....
- BronzeBronzeBronze is a metal alloy consisting primarily of copper, usually with tin as the main additive. It is hard and brittle, and it was particularly significant in antiquity, so much so that the Bronze Age was named after the metal...
- CobaltCobaltCobalt is a chemical element with symbol Co and atomic number 27. It is found naturally only in chemically combined form. The free element, produced by reductive smelting, is a hard, lustrous, silver-gray metal....
alloys - NickelNickelNickel is a chemical element with the chemical symbol Ni and atomic number 28. It is a silvery-white lustrous metal with a slight golden tinge. Nickel belongs to the transition metals and is hard and ductile...
alloys - Steels
- Carbon steel
- Stainless steelStainless steelIn metallurgy, stainless steel, also known as inox steel or inox from French "inoxydable", is defined as a steel alloy with a minimum of 10.5 or 11% chromium content by mass....
- High-strength low-alloy steel
- Manganese steel
- TitaniumTitaniumTitanium is a chemical element with the symbol Ti and atomic number 22. It has a low density and is a strong, lustrous, corrosion-resistant transition metal with a silver color....
History
UIT was originally developed in 1972 and has since been perfected by a team of RussiaRussia
Russia or , officially known as both Russia and the Russian Federation , is a country in northern Eurasia. It is a federal semi-presidential republic, comprising 83 federal subjects...
n scientists under the leadership of Dr. Efim Statnikov. Originally developed and utilized to enhance the fatigue and corrosion attributes of ship and submarine structures, UIT has been utilized in aerospace, mining, offshore drilling, shipbuilding, infrastructure, automotive, energy production and other industries.
Practical applications
UIT enables life extension of steel bridges. This technique has been employed in numerous US states as well as other nations. The result is a greatly reduced cost of infrastructure. UIT has been certified for this use by AASHTO.The use of UIT on draglines and other heavy equipment in the mining industry has resulted in increased production and has decreased downtime and maintenance costs.
UIT is employed on drive shafts and crank shafts in a number of industries. Results show that UIT increases shaft life by over 3X.
The US Navy uses UIT to address cracked areas in certain aluminum decks. Without UIT, crack repairs resulted in almost immediate re-cracking. With UIT, repairs have shown to last over eight months without cracks.
Further reading
- Fisher, J.W., E.Sh. Statnikov, L. Tehini, Fatigue Strength Enhancement by Means of Weld Design Change and the Application of Ultrasonic Impact treatment, Proc. of Intl. Symp. On Steel Bridges, Chicago (2001).
- Haagensen, P.J., Weld Improvement Methods – Applications and Implementations in Design Codes, invited paper at the Conference on Fatigue of Welded Structures, Senlis, Paris, France, 12–14 June 1996.
- Prokopenko, G.I., T.A. Lyatun, Study of Surface Hardening Conditions by Means of Ultrasound, in: Physics and Chemistry of Material Processing, No. 3, p 91, 1977.
- Blaha, F., B.Langenecker.“Dehnung von Zink-Kristallen unter Ultraschalleinwirkung”, Zeitschrift die Naturwissenschaften, 20, 556, 1955.
- Konovalov, E.G., V.M. Drozdov, M.D. Tyavlovski, Dynamic Strength of Metals (in Russian), Nauka i Tekhnika, Minsk, 1969.
- Kazantsev, V.F., Basic Physics of Ultrasonic Action on Solid Body Processing (in Russian). Doctoral thesis, AKIN, Moscow, 1980, pp. 12–44.
- Statnikov, E.S., Development and Study of Ultrasonic Specific-purpose Devices, Thesis, Academician N.N. Andreyev Acoustic Institute, Academy of Sciences of the USSR, 1982.
- Severdenko, V.P., E.G. Konovalov, E.Sh. Statnikov et al., Study of Mechanical Properties of New Materials under Ultrasonic Oscillations, Report # 21-971, FTI Acad. Nauk of BSSR,Minsk (1966).
- Statnikov, E.Sh., Activation of Deformation Process under Ultrasonic Effect,. Scientific andTechnical Conference “XXX Lomonosov Readings”, Sevmashvtuz, Severodvinsk (2001).
IIW PUBLICATIONS:
- Increasing the Fatigue Strength of Welded Joints in Cyclic Compression. 47th Annual Assembly of the International Institute of Welding. IIW Doc. XIII-1569-94, Peking, 1994. Y. Kudryavtzev, V.I. Tryufyakov, P.P. Mikheev, E. S. Statnikov.
- Improvement of Fatigue Strength of Welded Joint (in High Strength Steels and Aluminium Alloys) by Means of Ultrasonic Hammer Peening. 48th Annual Assembly of the International Institute of Welding. IIW Doc. XIII-1594-95, Stockholm, 1995. J.J. Janosch, H. Koneczny, S. Debiez, E. S. Statnikov, V.I. Tryufyakov, P.P. Mikheev.
- Ultrasonic Impact Treatment of Welded Joints. 48th Annual Assembly of the International Institute of Welding. IIW Doc. XIII-1609-95, Stockholm, 1995. V.I. Trufyakov, P.P. Mikheev, Yu. Kudryavtzev, E. S. Statnikov.
- Specification for Weld Toe Improvement by Means of Ultrasonic Impact Treatment. 49th Annual Assembly of the International Institute of Welding. IIW Doc. XIII-1617-96, Budapest, 1996. E. S. Statnikov, V.I. Trufyakov, P.P. Mikheev Yu. Kudryavtzev.
- Ultrasonic Impact Treatment (UIT) of Welded Joints. 49th Annual Assembly of the International Institute of Welding, Budapest, 1996., E. S. Statnikov.
- Applications of Operational Ultrasonic Impact Treatment (UIT) Technology in Production of Welded Joints. 50th Annual Assembly of the International Institute of Welding. IIW Doc. XIII-1667-97, San-Francisco, 1997. E.S. Statnikov.
- Comparison of Efficiency and Processibility of Post-Weld Deformation Methods for Increase in Fatigue Strength of Welded Joints. 50th Annual Assembly of the International Institute of Welding. IIW Doc. XIII-1668-97, San-Francisco, 1997. E. S. Statnikov.
- The Efficiency of Ultrasonic Impact Treatment (UIT) for Improving the Fatigue Strength of Welded Joints. 51stAnnual Assembly of the International Institute of Welding. IIW Doc. XIII-1745-98, Hamburg, 1998. V.I. Troufyakov, E.S. Statnikov, P.P. Mikheev, A.Z. Kuzmenko.
- Introductory Fatigue Tests on Welded Joints in High Strength Steel and Aluminium Treated by Various Improvement Methods Including Ultrasonic Impact Treatment (UIT). 51st Annual Assembly of the International Institute of Welding. IIW Doc. XIII-1748-98, Hamburg, 1998. P.J. Haagensen, E.S. Statnikov, L. Lopez-Martinez.
- Repair of Fatigue Cracks. Working Group 5. 51st Annual Assembly of the International Institute of Welding. IIW Doc. XIII-WG5-18-98, Hamburg, 1998. E.S. Statnikov, L. Kelner, , J. Baker, H. Croft, V.I. Dvoretsky, V.O. Muktepavel.
- Guide for Application of Ultrasonic Impact Treatment Improving Fatigue Life of Welded Structures. 52nd Annual Assembly of the International Institute of Welding. IIW Doc. XIII-1757-99, Lisbon, 1999. E.S. Statnikov.
- Comparison of Ultrasonic Impact Treatment (UIT) and other Fatigue Life Improvement Methods. 53rd Annual Assembly of the International Institute of Welding. IIW-Doc. XIII-1817-00, Florence, 2000. E.S. Statnikov, V.O. Muktepavel, A. Blomqvist.
- Repair of Fatigue Welded Structures Repair Case Study. Working Group 5. 54th Annual Assembly of the International Institute of Welding. IIW Doc. XIII-WG5-1873-01, Slovenia, 2001. E.S. Statnikov, L. Tehini.
- Fatigue Strength Improvement of Bridge Girders by Ultrasonic Impact Treatment (UIT). 55th Annual Assembly of the International Institute of Welding. IIW Doc.XIII-1916-02, Copenhagen, 2002. J.W. Fisher, E.S. Statnikov, L. Tehini.
- Comparison of the Improvement in Corrosion Fatigue Strength of Weld Repaired Marine Cu 3-grade Bronze Propellers by Ultrasonic Impact Treatment (UIT) or Heat Treatment. 56th Annual Assembly of the International Institute of Welding. IIW. Doc. XIII-1964-03, Bucharest, 2003. E.S. Statnikov, V.O. Muktepavel, V.N. Vityazev, V.I. Trufyakov, V.S. Kovalchuk, P. Haagensen.
- The influence of ultrasonic impact treatment on fatigue behaviour of welded joints in high strength steel. 56th Annual Assembly of the International Institute of Welding, IIW-Doc. XIII-1976-03, Bucharest, 2003. André Galtier, E.S. Statnikov.
- Fatigue strength of a longitudinal attachment improved by ultrasonic impact treatment. 56th Annual Assembly of the International Institute of Welding. IIW. Doc.XIII-1990-03, Bucharest, 2003. Veli-Matti Lihavainen, Gary Marquis, E.S. Statnikov.
- Physics and Mechanism of Ultrasonic Impact Treatment. 57th Annual Assembly of the International Institute of Welding. IIW Doc. XIII-2004-04, Osaka, 2004, E. S. Statnikov.
- Comparison of the Efficiency of 27, 36 and 44 kHz UIT Tools. 57th Annual Assembly of the International Institute of Welding. IIW Doc. XIII-2005, Osaka, 2004. E.S. Statnikov, V.N. Vityazev, O.V. Korolkov.
- Improvement in Quality and Reliability of Structures by Means of UIT Esonix. 58th Annual Assembly of the International Institute of Welding. IIW Doc. XIII-2049-05, Prague, 2005. E. S. Statnikov.
- Ultrasonic Impact Treatment versus Ultrasonic Peening. 58th Annual Assembly of the International Institute of Welding. IIW Doc. XIII-2050-05. Prague, 2005. E. S. Statnikov.
- Physics and Mechanism of Ultrasonic Impact. 59th Annual Assembly of the International Institute of Welding. IIW Doc. XIII-2096-06, Quebec, 2006. E .S. Statnikov, O.V. Korolkov, V.N.Vityazev.
- On the Assessment of Ultrasonic Impact Treatment Effect on Fatigue (Discussion of some experimental results). 59th Annual Assembly of the International Institute of Welding. IIW Doc. XIII-2097-06, Quebec, 2006. E. S. Statnikov, V.Y. Korostel.
- Development of Esonix Ultrasonic Impact Treatment Techniques. 59th Annual Assembly of the International Institute of Welding. IIW Doc. XIII-2098-06, Quebec, 2006. E.S. Statnikov, V.Y. Korostel, N.Vekshin, G. Marquis.
- Fatigue Strength Improvement of Thin Stainless Steel Specimens by UIT. 59th Annual Assembly of the International Institute of Welding. IIW Doc. XIII-2104-06, Quebec, 2006. L Huhtala, V-M Lihavainen, G Marquis, E. S. Statnikov, V.Y. Korostel, S.J. Maddox.
- On the Use of Ultrasound to Accelerate Fatigue Testing. 59th Annual Assembly of the International Institute of Welding. IIW Doc. XIII-2106-06, Quebec, 2006. E.S. Statnikov, V.Y. Korostel.
- UIT Application for Angular Distortion Compensation in Welded T-joints. 59th Annual Assembly of the International Institute of Welding. IIW Doc. XIII-2107-06, Quebec, 2006. E.S. Statnikov, V.Y. Korostel, W. Fricke.
- On Identify in UIT Preparation for Comparative Testing and Field Application. 60th Annual Assembly of the International Institute of Welding. IIW Doc. XIII-2180-07, Dubrovnik, 2007. E.S. Statnikov, V.Y. Korostel, A.D. Manelik.
- The use of ultrasound to accelerate fatigue testing during assessment of the UIT effectiveness. 60th Annual Assembly of the International Institute of Welding. IIW Doc. XIII-2182-07, Dubrovnik, 2007. E.S. Statnikov, V.Y. Korostel.
- UIT application for angular distortion compensation in welded T-joints. 60th Annual Assembly of the International Institute of Welding. IIW Doc. X-1603-07, Dubrovnik, 2007. E.S. Statnikov, Wolfgang Fricke.
- Inventing Ultrasonic Impact Technology and its Industry Impact. 63rd Annual Assembly of the International Institute of Welding, IIW Doc. XIII-2320-10, Istanbul, 2010. L. Kelner, D. Sharman.
External links
- http://www.appliedultrasonics.com/pdf/pdf8.pdf
- http://www.appliedultrasonics.com/pdf/pdf2.pdf