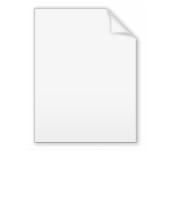
Friction stir processing
Encyclopedia
Friction stir processing is a method of changing the properties of a metal
through intense, localized plastic deformation. This deformation is produced by forcibly inserting a non-consumable tool into the workpiece, and revolving the tool in a stirring motion as it is pushed laterally through the workpiece. The precursor of this technique, friction stir welding
, is used to join multiple pieces of metal without creating the heat affected zone typical of fusion welding
.
When ideally implemented, this process mixes the material without changing the phase
(by melting
or otherwise) and creates a microstructure
with fine, equiaxed grains
. This homogeneous grain structure, separated by high-angle boundaries, allows some aluminium alloy
s to take on superplastic
properties. Friction stir processing also enhances the tensile strength
and fatigue strength of the metal. In tests with actively cooled magnesium-alloy workpieces, the microhardness was almost tripled in the area of the friction stir processed seam (to 120–130 Vickers hardness).
, AA 5083 and AA 7075 aluminum alloys, AZ61 magnesium alloy
, [nickel-aluminium bronze and 304L stainless steel
.
are comparatively inexpensive, but are often subject to metallurgical flaws like porosity
and microstructural defects. Friction stir processing can be used to introduce a wrought microstructure into a cast component and eliminate many of the defects. By vigorously stirring a cast metal part to homogenize it and reduce the grain size, the ductility and strength are increased.
objects. In particular, when dealing with aluminium powder metal alloys, the aluminium oxide
film on the surface of each granule is detrimental to the ductility
, fatigue properties and fracture toughness
of the workpiece. While conventional techniques for removing this film include forging
and extrusion
, friction stir processing is suited for situations where localized treatment is desired.
Metal
A metal , is an element, compound, or alloy that is a good conductor of both electricity and heat. Metals are usually malleable and shiny, that is they reflect most of incident light...
through intense, localized plastic deformation. This deformation is produced by forcibly inserting a non-consumable tool into the workpiece, and revolving the tool in a stirring motion as it is pushed laterally through the workpiece. The precursor of this technique, friction stir welding
Friction stir welding
Friction-stir welding is a solid-state joining process and is used for applications where the original metal characteristics must remain unchanged as far as possible...
, is used to join multiple pieces of metal without creating the heat affected zone typical of fusion welding
Fusion welding
Fusion welding is a generic term for welding processes that rely upon melting to join materials of similar compositions and melting points. Due to the high-temperature phase transitions inherent to these processes, a heat-affected zone is created in the material Fusion welding is a generic term for...
.
When ideally implemented, this process mixes the material without changing the phase
Phase transition
A phase transition is the transformation of a thermodynamic system from one phase or state of matter to another.A phase of a thermodynamic system and the states of matter have uniform physical properties....
(by melting
Melting
Melting, or fusion, is a physical process that results in the phase change of a substance from a solid to a liquid. The internal energy of a substance is increased, typically by the application of heat or pressure, resulting in a rise of its temperature to the melting point, at which the rigid...
or otherwise) and creates a microstructure
Microstructure
Microstructure is defined as the structure of a prepared surface or thin foil of material as revealed by a microscope above 25× magnification...
with fine, equiaxed grains
Crystallite
Crystallites are small, often microscopic crystals that, held together through highly defective boundaries, constitute a polycrystalline solid. Metallurgists often refer to crystallites as grains.- Details :...
. This homogeneous grain structure, separated by high-angle boundaries, allows some aluminium alloy
Aluminium alloy
Aluminium alloys are alloys in which aluminium is the predominant metal. The typical alloying elements are copper, magnesium, manganese, silicon and zinc. There are two principal classifications, namely casting alloys and wrought alloys, both of which are further subdivided into the categories...
s to take on superplastic
Superplasticity
In materials science, superplasticity is a state in which solid crystalline material is deformed well beyond its usual breaking point, usually over about 200% during tensile deformation. Such a state is usually achieved at high homologous temperature, typically half the absolute melting point. ...
properties. Friction stir processing also enhances the tensile strength
Tensile strength
Ultimate tensile strength , often shortened to tensile strength or ultimate strength, is the maximum stress that a material can withstand while being stretched or pulled before necking, which is when the specimen's cross-section starts to significantly contract...
and fatigue strength of the metal. In tests with actively cooled magnesium-alloy workpieces, the microhardness was almost tripled in the area of the friction stir processed seam (to 120–130 Vickers hardness).
Applications
Examples of materials successfully processed using the friction stir technique include AA 25192519 aluminium alloy
AA 2519 is an aluminium alloy principally containing copper as an alloying element. It also contains 0.25% silicon, 0.30% iron, 0.10–0.50% manganese, 0.05–0.40% magnesium, 0.10% zinc, 0.02–0.10% titanium, 0.05–0.15% vanadium, 0.10–0.25% zirconium, 0.40% silicon-iron compounds, and up to 0.15%...
, AA 5083 and AA 7075 aluminum alloys, AZ61 magnesium alloy
Magnesium alloy
Magnesium alloys are mixtures of magnesium with other metals , often aluminium, zinc, manganese, silicon, copper, rare earths and zirconium. Magnesium is the lightest structural metal. Magnesium alloys have a hexagonal lattice structure, which affects the fundamental properties of these alloys...
, [nickel-aluminium bronze and 304L stainless steel
Stainless steel
In metallurgy, stainless steel, also known as inox steel or inox from French "inoxydable", is defined as a steel alloy with a minimum of 10.5 or 11% chromium content by mass....
.
Casting
Metallic parts produced by castingCasting
In metalworking, casting involves pouring liquid metal into a mold, which contains a hollow cavity of the desired shape, and then allowing it to cool and solidify. The solidified part is also known as a casting, which is ejected or broken out of the mold to complete the process...
are comparatively inexpensive, but are often subject to metallurgical flaws like porosity
Porosity
Porosity or void fraction is a measure of the void spaces in a material, and is a fraction of the volume of voids over the total volume, between 0–1, or as a percentage between 0–100%...
and microstructural defects. Friction stir processing can be used to introduce a wrought microstructure into a cast component and eliminate many of the defects. By vigorously stirring a cast metal part to homogenize it and reduce the grain size, the ductility and strength are increased.
Powder metallurgy
Friction stir processing can also be used to improve the microstructural properties of powder metalPowder metallurgy
Powder metallurgy is the process of blending fine powdered materials, pressing them into a desired shape , and then heating the compressed material in a controlled atmosphere to bond the material . The powder metallurgy process generally consists of four basic steps: powder manufacture, powder...
objects. In particular, when dealing with aluminium powder metal alloys, the aluminium oxide
Aluminium oxide
Aluminium oxide is an amphoteric oxide with the chemical formula 23. It is commonly referred to as alumina, or corundum in its crystalline form, as well as many other names, reflecting its widespread occurrence in nature and industry...
film on the surface of each granule is detrimental to the ductility
Ductility
In materials science, ductility is a solid material's ability to deform under tensile stress; this is often characterized by the material's ability to be stretched into a wire. Malleability, a similar property, is a material's ability to deform under compressive stress; this is often characterized...
, fatigue properties and fracture toughness
Fracture toughness
In materials science, fracture toughness is a property which describes the ability of a material containing a crack to resist fracture, and is one of the most important properties of any material for virtually all design applications. The fracture toughness of a material is determined from the...
of the workpiece. While conventional techniques for removing this film include forging
Forging
Forging is a manufacturing process involving the shaping of metal using localized compressive forces. Forging is often classified according to the temperature at which it is performed: '"cold," "warm," or "hot" forging. Forged parts can range in weight from less than a kilogram to 580 metric tons...
and extrusion
Extrusion
Extrusion is a process used to create objects of a fixed cross-sectional profile. A material is pushed or drawn through a die of the desired cross-section...
, friction stir processing is suited for situations where localized treatment is desired.