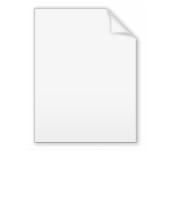
Controller (control theory)
Encyclopedia
In control theory
, a controller is a device which monitors and affects the operational conditions of a given dynamical system
. The operational conditions are typically referred to as output variables of the system which can be affected by adjusting certain input variables. For example, the heating system of a house can be equipped with a thermostat (controller) for sensing air temperature (output variable) which can turn on or off a furnace or heater when the air temperature becomes too low or too high.
In this example, the thermostat is the controller and directs the activities of the heater. The heater is the processor that warms the air inside the house to the desired temperature (setpoint). The air temperature reading inside the house is the feedback
. And finally, the house is the environment
in which the heating system operates.
The notion of controllers can be extended to more complex systems. In the natural world, individual organisms also appear to be equipped with controllers that assure the homeostasis
necessary for survival of each individual. Both human-made and natural systems exhibit collective behaviors amongst individuals in which the controllers seek some form of equilibrium.
there are two basic types of control. These are feedback
and feed-forward
. The input to a feedback controller is the same as what it is trying to control - the controlled variable is "fed back" into the controller. The thermostat of a house is an example of a feedback controller. This controller relies on measuring the controlled variable, in this case the temperature of the house, and then adjusting the output, whether or not the heater is on. However, feedback control usually results in intermediate periods where the controlled variable is not at the desired set-point. With the thermostat example, if the door of the house were opened on a cold day, the house would cool down. After it fell below the desired temperature (set-point), the heater would kick on, but there would be a period when the house was colder than desired.
Feed-forward control can avoid the slowness of feedback control. With feed-forward control, the disturbances are measured and accounted for before they have time to affect the system. In the house example, a feed-forward system may measure the fact that the door is opened and automatically turn on the heater before the house can get too cold. The difficulty with feed-forward control is that the effect of the disturbances on the system must be accurately predicted, and there must not be any unmeasured disturbances. For instance, if a window were opened that was not being measured, the feed-forward-controlled thermostat might still let the house cool down.
To achieve the benefits of feedback control (controlling unknown disturbances and not having to know exactly how a system will respond to disturbances) and the benefits of feed-forward control (responding to disturbances before they can affect the system), there are combination's of feedback and feed-forward that can be used.
Some examples of where feedback and feed-forward control can be used together are dead-time compensation, and inverse response compensation. Dead-time compensation is used to control devices that take a long time to show any change to a change in input, for example, change in composition of flow through a long pipe. A dead-time compensation control uses an element (also called a Smith predictor) to predict how changes made now by the controller will affect the controlled variable in the future. The controlled variable is also measured and used in feedback control. Inverse response compensation involves controlling systems where a change at first affects the measured variable one way but later affects it in the opposite way. An example would be eating candy. At first it will give you lots of energy, but later you will be very tired. As can be imagined, it is difficult to control this system with feedback alone, therefore a predictive feed-forward element is necessary to predict the reverse effect that a change will have in the future.
For feedback controllers there are a few simple types. The most simple is like the thermostat that just turns the heat on if the temperature falls below a certain value and off it exceeds a certain value (on-off control).
Another simple type of controller is a proportional controller
. With this type of controller, the controller output (control action) is proportional to the error in the measured variable.
In feedback control, it is standard to define the error as the difference between the desired value (setpoint)
and the current value (measured)
. If the error is large, then the control action is large. Mathematically:

where
represents the control action (controller output),
represents the error,
represents the controller's gain, and
represents the steady state control action (bias) necessary to maintain the variable at the steady state when there is no error.
It is important that the control action
counteracts the change in the controlled variable
(negative feedback). There are then two cases depending on the sign of the process gain.
In the first case the process gain is positive, so an increase in the controlled variable (measurement)
requires a decrease in the control action
(reverse-acting control). In this case the controller gain
is positive, because the standard definition of the error already contains a negative sign for
.
In the second case the process gain is negative, so an increase in the controlled variable (measurement)
requires an increase in the control action
(direct-acting control). In this case the controller gain
is negative.
A typical example of a reverse-acting system is control of temperature (
) by use of steam (
). In this case the process gain is positive, so if the temperature increases, the steam flow must be decreased to maintain the desired temperature. Conversely, a typical example of a direct-acting system is control of temperature using cooling water. In this case the process gain is negative, so if the temperature increases, the cooling water flow must be increased to maintain the desired temperature.
Although proportional control is simple to understand, it has drawbacks. The largest problem is that for most systems it will never entirely remove error. This is because when error is 0 the controller only provides the steady state control action so the system will settle back to the original steady state (which is probably not the new set point that we want the system to be at). To get the system to operate near the new steady state, the controller gain, Kc, must be very large so the controller will produce the required output when only a very small error is present. Having large gains can lead to system instability or can require physical impossibilities like infinitely large valves.
Alternates to proportional control are proportional-integral (PI) control and proportional-integral-derivative (PID) control
. PID control is commonly used to implement closed-loop control.
Open-loop control
can be used in systems sufficiently well-characterized as to predict what outputs will necessarily achieve the desired states. For example, the rotational velocity of an electric motor
may be well enough characterized for the supplied voltage
to make feedback unnecessary.
The drawback of open-loop control
is that it requires perfect knowledge of the system (i.e. one knows exactly what inputs to give in order to get the desired output), and it assumes there are no disturbances to the system.
Control theory
Control theory is an interdisciplinary branch of engineering and mathematics that deals with the behavior of dynamical systems. The desired output of a system is called the reference...
, a controller is a device which monitors and affects the operational conditions of a given dynamical system
Dynamical system
A dynamical system is a concept in mathematics where a fixed rule describes the time dependence of a point in a geometrical space. Examples include the mathematical models that describe the swinging of a clock pendulum, the flow of water in a pipe, and the number of fish each springtime in a...
. The operational conditions are typically referred to as output variables of the system which can be affected by adjusting certain input variables. For example, the heating system of a house can be equipped with a thermostat (controller) for sensing air temperature (output variable) which can turn on or off a furnace or heater when the air temperature becomes too low or too high.
In this example, the thermostat is the controller and directs the activities of the heater. The heater is the processor that warms the air inside the house to the desired temperature (setpoint). The air temperature reading inside the house is the feedback
Feedback
Feedback describes the situation when output from an event or phenomenon in the past will influence an occurrence or occurrences of the same Feedback describes the situation when output from (or information about the result of) an event or phenomenon in the past will influence an occurrence or...
. And finally, the house is the environment
Built environment
The term built environment refers to the human-made surroundings that provide the setting for human activity, ranging in scale from personal shelter and buildings to neighborhoods and cities that can often include their supporting infrastructure, such as water supply or energy networks.The built...
in which the heating system operates.
The notion of controllers can be extended to more complex systems. In the natural world, individual organisms also appear to be equipped with controllers that assure the homeostasis
Homeostasis
Homeostasis is the property of a system that regulates its internal environment and tends to maintain a stable, constant condition of properties like temperature or pH...
necessary for survival of each individual. Both human-made and natural systems exhibit collective behaviors amongst individuals in which the controllers seek some form of equilibrium.
Types of Controlling System
In control theoryControl theory
Control theory is an interdisciplinary branch of engineering and mathematics that deals with the behavior of dynamical systems. The desired output of a system is called the reference...
there are two basic types of control. These are feedback
Feedback
Feedback describes the situation when output from an event or phenomenon in the past will influence an occurrence or occurrences of the same Feedback describes the situation when output from (or information about the result of) an event or phenomenon in the past will influence an occurrence or...
and feed-forward
Feed-forward
Feed-forward is a term describing an element or pathway within a control system which passes a controlling signal from a source in the control system's external environment, often a command signal from an external operator, to a load elsewhere in its external environment...
. The input to a feedback controller is the same as what it is trying to control - the controlled variable is "fed back" into the controller. The thermostat of a house is an example of a feedback controller. This controller relies on measuring the controlled variable, in this case the temperature of the house, and then adjusting the output, whether or not the heater is on. However, feedback control usually results in intermediate periods where the controlled variable is not at the desired set-point. With the thermostat example, if the door of the house were opened on a cold day, the house would cool down. After it fell below the desired temperature (set-point), the heater would kick on, but there would be a period when the house was colder than desired.
Feed-forward control can avoid the slowness of feedback control. With feed-forward control, the disturbances are measured and accounted for before they have time to affect the system. In the house example, a feed-forward system may measure the fact that the door is opened and automatically turn on the heater before the house can get too cold. The difficulty with feed-forward control is that the effect of the disturbances on the system must be accurately predicted, and there must not be any unmeasured disturbances. For instance, if a window were opened that was not being measured, the feed-forward-controlled thermostat might still let the house cool down.
To achieve the benefits of feedback control (controlling unknown disturbances and not having to know exactly how a system will respond to disturbances) and the benefits of feed-forward control (responding to disturbances before they can affect the system), there are combination's of feedback and feed-forward that can be used.
Some examples of where feedback and feed-forward control can be used together are dead-time compensation, and inverse response compensation. Dead-time compensation is used to control devices that take a long time to show any change to a change in input, for example, change in composition of flow through a long pipe. A dead-time compensation control uses an element (also called a Smith predictor) to predict how changes made now by the controller will affect the controlled variable in the future. The controlled variable is also measured and used in feedback control. Inverse response compensation involves controlling systems where a change at first affects the measured variable one way but later affects it in the opposite way. An example would be eating candy. At first it will give you lots of energy, but later you will be very tired. As can be imagined, it is difficult to control this system with feedback alone, therefore a predictive feed-forward element is necessary to predict the reverse effect that a change will have in the future.
Types of controllers
Most control valve systems in the past were implemented using mechanical systems or solid state electronics. Pneumatics were often utilized to transmit information and control using pressure. However, most modern control systems in industrial settings now rely on computers for the controller. Obviously it is much easier to implement complex control algorithms on a computer than using a mechanical system.For feedback controllers there are a few simple types. The most simple is like the thermostat that just turns the heat on if the temperature falls below a certain value and off it exceeds a certain value (on-off control).
Another simple type of controller is a proportional controller
Proportional control
A proportional control system is a type of linear feedback control system. Two classic mechanical examples are the toilet bowl float proportioning valve and the fly-ball governor....
. With this type of controller, the controller output (control action) is proportional to the error in the measured variable.
In feedback control, it is standard to define the error as the difference between the desired value (setpoint)



where




It is important that the control action


In the first case the process gain is positive, so an increase in the controlled variable (measurement)




In the second case the process gain is negative, so an increase in the controlled variable (measurement)



A typical example of a reverse-acting system is control of temperature (


Although proportional control is simple to understand, it has drawbacks. The largest problem is that for most systems it will never entirely remove error. This is because when error is 0 the controller only provides the steady state control action so the system will settle back to the original steady state (which is probably not the new set point that we want the system to be at). To get the system to operate near the new steady state, the controller gain, Kc, must be very large so the controller will produce the required output when only a very small error is present. Having large gains can lead to system instability or can require physical impossibilities like infinitely large valves.
Alternates to proportional control are proportional-integral (PI) control and proportional-integral-derivative (PID) control
PID controller
A proportional–integral–derivative controller is a generic control loop feedback mechanism widely used in industrial control systems – a PID is the most commonly used feedback controller. A PID controller calculates an "error" value as the difference between a measured process variable and a...
. PID control is commonly used to implement closed-loop control.
Open-loop control
Open-loop controller
An open-loop controller, also called a non-feedback controller, is a type of controller that computes its input into a system using only the current state and its model of the system....
can be used in systems sufficiently well-characterized as to predict what outputs will necessarily achieve the desired states. For example, the rotational velocity of an electric motor
Electric motor
An electric motor converts electrical energy into mechanical energy.Most electric motors operate through the interaction of magnetic fields and current-carrying conductors to generate force...
may be well enough characterized for the supplied voltage
Voltage
Voltage, otherwise known as electrical potential difference or electric tension is the difference in electric potential between two points — or the difference in electric potential energy per unit charge between two points...
to make feedback unnecessary.
The drawback of open-loop control
Open-loop controller
An open-loop controller, also called a non-feedback controller, is a type of controller that computes its input into a system using only the current state and its model of the system....
is that it requires perfect knowledge of the system (i.e. one knows exactly what inputs to give in order to get the desired output), and it assumes there are no disturbances to the system.
See also
- AutomationAutomationAutomation is the use of control systems and information technologies to reduce the need for human work in the production of goods and services. In the scope of industrialization, automation is a step beyond mechanization...
- BELBICBELBICIn recent years, the use of biologically inspired methods such as the evolutionary algorithm have been increasingly employed to solve and analyze complex computational problems...
- CoDeSysCoDeSysCoDeSys is a development environment for programming controller applications according to the international industrial standard IEC 61131-3. The term CoDeSys is an acronym and stands for Controller Development System....
- Control theoryControl theoryControl theory is an interdisciplinary branch of engineering and mathematics that deals with the behavior of dynamical systems. The desired output of a system is called the reference...
- PID controllerPID controllerA proportional–integral–derivative controller is a generic control loop feedback mechanism widely used in industrial control systems – a PID is the most commonly used feedback controller. A PID controller calculates an "error" value as the difference between a measured process variable and a...
- Process controlProcess controlProcess control is a statistics and engineering discipline that deals with architectures, mechanisms and algorithms for maintaining the output of a specific process within a desired range...
- EICASLABEICASLABEICASLAB is a software suite providing a laboratory for automatic control design and time-series forecasting developed as final output of the European ACODUASIS Project IPS-2001-42068 funded by the European Community within the Innovation Programme...