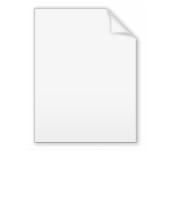
Carbonitriding
Encyclopedia
Carbonitriding is a metallurgical surface modification technique that is used to increase the surface hardness of a metal, thereby reducing wear
. During the process, atoms of carbon
and nitrogen
diffuse interstitially into the metal, creating barriers to slip
, increasing the hardness and modulus
near the surface. Carbonitriding is often applied to inexpensive, easily machined low carbon steel to impart the surface properties of more expensive and difficult to work grades of steel. Surface hardness of carbonitrided parts ranges from 55 to 62 HRC.
Certain pre-industrial case hardening
processes include not only carbon-rich materials such as charcoal, but nitrogen-rich materials such as urea
, which implies that traditional surface hardening techniques were a form of carbonitriding.
carburization with the addition of ammonia
to the carburizing atmosphere. which provides a source of nitrogen. Nitrogen is adsorbed at the surface and diffuses
into the workpiece along with carbon. Carbonitriding (around 850 °C / 1550 °F) is carried out at temperatures substantially higher than plain nitriding (around 530 °C / 990 °F) but slightly lower than those used for carburizing (around 950 °C / 1700 °F) and for shorter times. Carbonitriding tends to be more economical than carburizing, and also reduces distortion during quench
ing. The lower temperature allows oil quenching, or even gas quenching with a protective atmosphere.
Maximum case depth is typically restricted to 0.75mm; case depths greater than this take too long to diffuse to be economical. Shorter processing times are preferred to restrict the concentration of nitrogen in the case, as nitrogen addition is more difficult to control than carbon. An excess of nitrogen in the work piece can cause high levels of retained austenite and porosity, which are undesirable in producing a part of high hardness.
and increased fatigue
and impact strength. It is possible to use both carbonitriding and carburizing together to form optimum conditions of deeper case depths and therefore performance of the part in industry. This method is applied particularly to steels with low case hardenability, such as the seat of the valve. The process applied is initially carburizing to the required case depth (up to 2.5mm) at around 900-955°C, and then carbonitriding to achieve required carbonitrided case depth. The parts are then oil quenched, and the resulting part has a harder case than possibly achieved for carburization, and the addition of the carbonitrided layer increases the residual compressive stresses
in the case such that the contact fatigue resistance and strength gradient are both increased.
s, fastener
s, pin
s, automotive clutch plates, tool
s, and die
s.
Wear
In materials science, wear is erosion or sideways displacement of material from its "derivative" and original position on a solid surface performed by the action of another surface....
. During the process, atoms of carbon
Carbon
Carbon is the chemical element with symbol C and atomic number 6. As a member of group 14 on the periodic table, it is nonmetallic and tetravalent—making four electrons available to form covalent chemical bonds...
and nitrogen
Nitrogen
Nitrogen is a chemical element that has the symbol N, atomic number of 7 and atomic mass 14.00674 u. Elemental nitrogen is a colorless, odorless, tasteless, and mostly inert diatomic gas at standard conditions, constituting 78.08% by volume of Earth's atmosphere...
diffuse interstitially into the metal, creating barriers to slip
Slip (materials science)
In materials science, Slip is the process by which plastic deformation is produced by a dislocation motion. By an external force, parts of the crystal lattice glide along each other, resulting in a changed geometry of the material. Depending on the type of lattice, different slip systems are...
, increasing the hardness and modulus
Young's modulus
Young's modulus is a measure of the stiffness of an elastic material and is a quantity used to characterize materials. It is defined as the ratio of the uniaxial stress over the uniaxial strain in the range of stress in which Hooke's Law holds. In solid mechanics, the slope of the stress-strain...
near the surface. Carbonitriding is often applied to inexpensive, easily machined low carbon steel to impart the surface properties of more expensive and difficult to work grades of steel. Surface hardness of carbonitrided parts ranges from 55 to 62 HRC.
Certain pre-industrial case hardening
Case hardening
Case hardening or surface hardening is the process of hardening the surface of a metal, often a low carbon steel, by infusing elements into the material's surface, forming a thin layer of a harder alloy...
processes include not only carbon-rich materials such as charcoal, but nitrogen-rich materials such as urea
Urea
Urea or carbamide is an organic compound with the chemical formula CO2. The molecule has two —NH2 groups joined by a carbonyl functional group....
, which implies that traditional surface hardening techniques were a form of carbonitriding.
Process
Carbonitriding is similar to gasGas
Gas is one of the three classical states of matter . Near absolute zero, a substance exists as a solid. As heat is added to this substance it melts into a liquid at its melting point , boils into a gas at its boiling point, and if heated high enough would enter a plasma state in which the electrons...
carburization with the addition of ammonia
Ammonia
Ammonia is a compound of nitrogen and hydrogen with the formula . It is a colourless gas with a characteristic pungent odour. Ammonia contributes significantly to the nutritional needs of terrestrial organisms by serving as a precursor to food and fertilizers. Ammonia, either directly or...
to the carburizing atmosphere. which provides a source of nitrogen. Nitrogen is adsorbed at the surface and diffuses
Diffusion
Molecular diffusion, often called simply diffusion, is the thermal motion of all particles at temperatures above absolute zero. The rate of this movement is a function of temperature, viscosity of the fluid and the size of the particles...
into the workpiece along with carbon. Carbonitriding (around 850 °C / 1550 °F) is carried out at temperatures substantially higher than plain nitriding (around 530 °C / 990 °F) but slightly lower than those used for carburizing (around 950 °C / 1700 °F) and for shorter times. Carbonitriding tends to be more economical than carburizing, and also reduces distortion during quench
Quench
In materials science, quenching is the rapid cooling of a workpiece to obtain certain material properties. It prevents low-temperature processes, such as phase transformations, from occurring by only providing a narrow window of time in which the reaction is both thermodynamically favorable and...
ing. The lower temperature allows oil quenching, or even gas quenching with a protective atmosphere.
Characteristics of carbonitrided parts
Carbonitriding forms a hard, wear resistant case, typically .07mm -.5mm thick, and generally has higher hardness than a carburized case. Case depth is tailored to the application, and a thicker case, increases wear life of the part. Carbonitriding alters only the top layers of the workpiece; and does not deposit an additional layer, so the process does not significantly alter the dimensions of the part.Maximum case depth is typically restricted to 0.75mm; case depths greater than this take too long to diffuse to be economical. Shorter processing times are preferred to restrict the concentration of nitrogen in the case, as nitrogen addition is more difficult to control than carbon. An excess of nitrogen in the work piece can cause high levels of retained austenite and porosity, which are undesirable in producing a part of high hardness.
Advantages
Carbonitriding also has other advantages over carburizing; it has a greater resistance to softening during temperingTempering
Tempering is a heat treatment technique for metals, alloys and glass. In steels, tempering is done to "toughen" the metal by transforming brittle martensite or bainite into a combination of ferrite and cementite or sometimes Tempered martensite...
and increased fatigue
Fatigue (material)
'In materials science, fatigue is the progressive and localized structural damage that occurs when a material is subjected to cyclic loading. The nominal maximum stress values are less than the ultimate tensile stress limit, and may be below the yield stress limit of the material.Fatigue occurs...
and impact strength. It is possible to use both carbonitriding and carburizing together to form optimum conditions of deeper case depths and therefore performance of the part in industry. This method is applied particularly to steels with low case hardenability, such as the seat of the valve. The process applied is initially carburizing to the required case depth (up to 2.5mm) at around 900-955°C, and then carbonitriding to achieve required carbonitrided case depth. The parts are then oil quenched, and the resulting part has a harder case than possibly achieved for carburization, and the addition of the carbonitrided layer increases the residual compressive stresses
Residual stress
Residual stresses are stresses that remain after the original cause of the stresses has been removed. They remain along a cross section of the component, even without the external cause. Residual stresses occur for a variety of reasons, including inelastic deformations and heat treatment...
in the case such that the contact fatigue resistance and strength gradient are both increased.
Applications
Typical applications for case hardening are gear teeth, cams, shafts, bearingBearing (mechanical)
A bearing is a device to allow constrained relative motion between two or more parts, typically rotation or linear movement. Bearings may be classified broadly according to the motions they allow and according to their principle of operation as well as by the directions of applied loads they can...
s, fastener
Fastener
A fastener is a hardware device that mechanically joins or affixes two or more objects together.Fasteners can also be used to close a container such as a bag, a box, or an envelope; or they may involve keeping together the sides of an opening of flexible material, attaching a lid to a container,...
s, pin
Pin
A pin is a device used for fastening objects or material together.Pin may also refer to:* Award pin, a small piece of metal or plastic with a pin attached given as an award for some achievement...
s, automotive clutch plates, tool
Tool
A tool is a device that can be used to produce an item or achieve a task, but that is not consumed in the process. Informally the word is also used to describe a procedure or process with a specific purpose. Tools that are used in particular fields or activities may have different designations such...
s, and die
Die (manufacturing)
A die is a specialized tool used in manufacturing industries to cut or shape material using a press. Like molds, dies are generally customized to the item they are used to create...
s.
See also
- NitridizationNitridizationNitriding is a heat treating process that diffuses nitrogen into the surface of a metal to create a case hardened surface. It is predominantly used on steel, but also titanium, aluminum and molybdenum....
- CarburizationCarburizationCarburizing, spelled carburising in the UK, is a heat treatment process in which iron or steel is heated in the presence of another material which liberates carbon as it decomposes. Depending on the amount of time and temperature, the affected area can vary in carbon content...
- Differential hardeningDifferential hardeningDifferential hardening is a method used in forging swords and knives to increase the hardness of the edge without making the whole blade brittle. To achieve this, the edge is cooled more rapidly than the spine by adding a heat insulator to the spine before quenching. Clay or another material is...
- Quench polish quenchQuench Polish QuenchQuench polish quench is a specialized type of nitrocarburizing case hardening that increases corrosion resistance, originally developed by the Kolene Company...
- Surface engineeringSurface engineeringSurface engineering is the sub-discipline of materials science which deals with the surface of solid matter. It has applications to chemistry, mechanical engineering, and electrical engineering ....