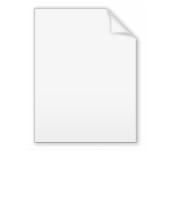
Sorption pump
Encyclopedia
The sorption pump is a vacuum pump
that creates a vacuum
by adsorbing molecules on a very porous material like molecular sieve
which is cooled by a cryogen, typically liquid nitrogen
. The ultimate pressure is about 10-2 mbar. With special techniques this can be lowered till 10-7 mbar. The main advantages are the absence of oil or other contaminants, low cost and vibration free operation because there are no moving parts
. The main disadvantages are that it cannot operate continuously and cannot effectively pump hydrogen
, helium
and neon
, all gases with lower condensation temperature than liquid nitrogen. The main application is as a roughing pump
for a sputter-ion pump
in ultra-high vacuum experiments, for example in surface physics.
, aluminium
or borosilicate glass
. It can be a simple Pyrex
flask filled with molecular sieve or an elaborate metal construction consisting of a metal flask containing perforated tubing and heat-conducting fins. A pressure relief valve can be installed. The design only influences the pumping speed and not the ultimate pressure that can be reached. The design details are a trade-off between fast cooling using heat conducting fins and high gas conductance using perforated tubing.
The typical molecular sieve used is a synthetic zeolite
with a pore diameter around 0.4 nanometer ( Type 4A ) and a surface area of about 500 m2/g. The sorption pump contains between 300 g and 1.2 kg of molecular sieve. A 15 liter system will be pumped down to about 10-2 mbar by 300 g molecular sieve.
In the sorption
phase the pump is actually used to create a vacuum. This is achieved by cooling the pump body to low temperatures, typically by immersing it in a Dewar
flask filled with liquid nitrogen. Gases will now either condense or be adsorbed by the large surface of the molecular sieve.
In the desorption
phase the pump is allowed warm up to room temperature and the gases escape through the pressure relief valve or other opening to the atmosphere. If the pump has been used to pump toxic, flammable or other dangerous gasses one has to be careful to vent safely into the atmosphere as all gases pumped during the sorption phase will be released during the desorption phase.
In the regeneration phase the pump body is heated to 300 °C to drive off water vapor that does not desorb at room temperature and accumulates in the molecular sieve. It takes typically 2 hours to fully regenerate a pump.
The pump can be used in a cycle of sorption and desorption until it loses too much efficiency and is regenerated or in a cycle where sorption and desorption are always followed by regeneration.
After filling a sorption pump with new molecular sieve it should always be regenerated as the new molecular sieve is probably saturated with water vapor
. Also when a pump is not in use it should be closed off from the atmosphere to prevent water vapor saturation.
or even a water aspirator or compressed-air venturi pump.
Sequential or multistage pumping can be used to attain lower pressures. In this case two or more pumps are connected in parallel to the vacuum vessel. Every pump has a valve to isolate it from the vacuum vessel. At the start of the pump down all valves are open. The first pump is cooled down while the others are still hot. When the first pump has reached its ultimate pressure it is closed off and the next pump is cooled down. Final pressures are in the 10-4 mbar region. What is left is mainly helium because it is almost not pumped at all. The final pressure almost equals the partial pressure of helium in air.
A sorption pump does pump all gases effectively with the exception of hydrogen, helium and neon which do not condensate at liquid nitrogen temperatures and are not efficiently adsorbed by the molecular sieves because of their small molecular size. This problem can be solved by purging the vacuum system with dry pure nitrogen before pump down. In purged system with aspirator rough pumping ultimate pressures of 10-4 mbar for a single sorption pump and 10-7 mbar for sequential pumping can be reached. A typical source of dry pure nitrogen would be a liquid nitrogen Dewar head space.
It has been suggested that by applying a dynamic pumping technique hydrogen, helium and neon can also be pumped without resorting to dry nitrogen purging. This is done by precooling the pump with the valve to the vacuum vessel closed. The valve is opened when the pump is cold and the inrush of adsorbable gases will carry all other gases into the pump. The valve is closed before hydrogen, helium or neon can back-migrate into the vacuum vessel. Sequential pumping can also be applied. No final pressures are given.
Continuous pumping may be simulated by using two pumps in parallel and letting one pump pump the system while the other pump, temporally sealed-off from the system, is in the desorption phase and venting to the atmosphere. When the pump is well desorbed it is cooled down and reconnected to the system. The other pump is sealed-off and goes into desorption. This becomes a continuous cycle.
Vacuum pump
A vacuum pump is a device that removes gas molecules from a sealed volume in order to leave behind a partial vacuum. The first vacuum pump was invented in 1650 by Otto von Guericke.- Types :Pumps can be broadly categorized according to three techniques:...
that creates a vacuum
Vacuum
In everyday usage, vacuum is a volume of space that is essentially empty of matter, such that its gaseous pressure is much less than atmospheric pressure. The word comes from the Latin term for "empty". A perfect vacuum would be one with no particles in it at all, which is impossible to achieve in...
by adsorbing molecules on a very porous material like molecular sieve
Molecular sieve
A molecular sieve is a material containing tiny pores of a precise and uniform size that is used as an adsorbent for gases and liquids.Molecules small enough to pass through the pores are adsorbed while larger molecules are not. It is different from a common filter in that it operates on a...
which is cooled by a cryogen, typically liquid nitrogen
Liquid nitrogen
Liquid nitrogen is nitrogen in a liquid state at a very low temperature. It is produced industrially by fractional distillation of liquid air. Liquid nitrogen is a colourless clear liquid with density of 0.807 g/mL at its boiling point and a dielectric constant of 1.4...
. The ultimate pressure is about 10-2 mbar. With special techniques this can be lowered till 10-7 mbar. The main advantages are the absence of oil or other contaminants, low cost and vibration free operation because there are no moving parts
Moving parts
The moving parts of a machine are those parts of it that move. Machines comprise both moving and fixed parts. The moving parts have controlled and constrained motions....
. The main disadvantages are that it cannot operate continuously and cannot effectively pump hydrogen
Hydrogen
Hydrogen is the chemical element with atomic number 1. It is represented by the symbol H. With an average atomic weight of , hydrogen is the lightest and most abundant chemical element, constituting roughly 75% of the Universe's chemical elemental mass. Stars in the main sequence are mainly...
, helium
Helium
Helium is the chemical element with atomic number 2 and an atomic weight of 4.002602, which is represented by the symbol He. It is a colorless, odorless, tasteless, non-toxic, inert, monatomic gas that heads the noble gas group in the periodic table...
and neon
Neon
Neon is the chemical element that has the symbol Ne and an atomic number of 10. Although a very common element in the universe, it is rare on Earth. A colorless, inert noble gas under standard conditions, neon gives a distinct reddish-orange glow when used in either low-voltage neon glow lamps or...
, all gases with lower condensation temperature than liquid nitrogen. The main application is as a roughing pump
Roughing pump
A roughing pump is any vacuum pump used to initially evacuate a vacuum system, as a first stage towards achieving high vacuum or ultra high vacuum. The term "roughing pump" derives from the vacuum range it works in, "rough vacuum", above 1x10-3 torr...
for a sputter-ion pump
Ion pump (physics)
An ion pump is a type of vacuum pump capable of reaching up to 10−11 mbar under ideal conditions. An ion pump ionizes gases and employs a strong electrical potential, typically 3kV to 7kV, to accelerate them into a solid electrode...
in ultra-high vacuum experiments, for example in surface physics.
Construction
A sorption pump is usually constructed in stainless steelStainless steel
In metallurgy, stainless steel, also known as inox steel or inox from French "inoxydable", is defined as a steel alloy with a minimum of 10.5 or 11% chromium content by mass....
, aluminium
Aluminium
Aluminium or aluminum is a silvery white member of the boron group of chemical elements. It has the symbol Al, and its atomic number is 13. It is not soluble in water under normal circumstances....
or borosilicate glass
Borosilicate glass
Borosilicate glass is a type of glass with the main glass-forming constituents silica and boron oxide. Borosilicate glasses are known for having very low coefficients of thermal expansion , making them resistant to thermal shock, more so than any other common glass...
. It can be a simple Pyrex
Pyrex
Pyrex is a brand name for glassware, introduced by Corning Incorporated in 1915.Originally, Pyrex was made from borosilicate glass. In the 1940s the composition was changed for some products to tempered soda-lime glass, which is the most common form of glass used in glass bakeware in the US and has...
flask filled with molecular sieve or an elaborate metal construction consisting of a metal flask containing perforated tubing and heat-conducting fins. A pressure relief valve can be installed. The design only influences the pumping speed and not the ultimate pressure that can be reached. The design details are a trade-off between fast cooling using heat conducting fins and high gas conductance using perforated tubing.
The typical molecular sieve used is a synthetic zeolite
Zeolite
Zeolites are microporous, aluminosilicate minerals commonly used as commercial adsorbents. The term zeolite was originally coined in 1756 by Swedish mineralogist Axel Fredrik Cronstedt, who observed that upon rapidly heating the material stilbite, it produced large amounts of steam from water that...
with a pore diameter around 0.4 nanometer ( Type 4A ) and a surface area of about 500 m2/g. The sorption pump contains between 300 g and 1.2 kg of molecular sieve. A 15 liter system will be pumped down to about 10-2 mbar by 300 g molecular sieve.
Operation
The sorption pump is a cyclic pump and its cycle has 3 phases: sorption, desorption and regeneration.In the sorption
Sorption
Sorption refers to the action of absorption* Absorption is the incorporation of a substance in one state into another of a different state ....
phase the pump is actually used to create a vacuum. This is achieved by cooling the pump body to low temperatures, typically by immersing it in a Dewar
Dewar
Dewar may refer to:*Clan Dewar* Vacuum flask , a container with vacuum insulation; used to keep the contents hot or cold for an extended period...
flask filled with liquid nitrogen. Gases will now either condense or be adsorbed by the large surface of the molecular sieve.
In the desorption
Desorption
Desorption is a phenomenon whereby a substance is released from or through a surface. The process is the opposite of sorption . This occurs in a system being in the state of sorption equilibrium between bulk phase and an adsorbing surface...
phase the pump is allowed warm up to room temperature and the gases escape through the pressure relief valve or other opening to the atmosphere. If the pump has been used to pump toxic, flammable or other dangerous gasses one has to be careful to vent safely into the atmosphere as all gases pumped during the sorption phase will be released during the desorption phase.
In the regeneration phase the pump body is heated to 300 °C to drive off water vapor that does not desorb at room temperature and accumulates in the molecular sieve. It takes typically 2 hours to fully regenerate a pump.
The pump can be used in a cycle of sorption and desorption until it loses too much efficiency and is regenerated or in a cycle where sorption and desorption are always followed by regeneration.
After filling a sorption pump with new molecular sieve it should always be regenerated as the new molecular sieve is probably saturated with water vapor
Water vapor
Water vapor or water vapour , also aqueous vapor, is the gas phase of water. It is one state of water within the hydrosphere. Water vapor can be produced from the evaporation or boiling of liquid water or from the sublimation of ice. Under typical atmospheric conditions, water vapor is continuously...
. Also when a pump is not in use it should be closed off from the atmosphere to prevent water vapor saturation.
Performance improvement
Pumping capacity can be improved by prepumping the system by another simple and clean vacuum pump like a diaphragm pumpDiaphragm pump
A diaphragm pump is a positive displacement pump that uses a combination of the reciprocating action of a rubber, thermoplastic or teflon diaphragm and suitable non-return check valves to pump a fluid...
or even a water aspirator or compressed-air venturi pump.
Sequential or multistage pumping can be used to attain lower pressures. In this case two or more pumps are connected in parallel to the vacuum vessel. Every pump has a valve to isolate it from the vacuum vessel. At the start of the pump down all valves are open. The first pump is cooled down while the others are still hot. When the first pump has reached its ultimate pressure it is closed off and the next pump is cooled down. Final pressures are in the 10-4 mbar region. What is left is mainly helium because it is almost not pumped at all. The final pressure almost equals the partial pressure of helium in air.
A sorption pump does pump all gases effectively with the exception of hydrogen, helium and neon which do not condensate at liquid nitrogen temperatures and are not efficiently adsorbed by the molecular sieves because of their small molecular size. This problem can be solved by purging the vacuum system with dry pure nitrogen before pump down. In purged system with aspirator rough pumping ultimate pressures of 10-4 mbar for a single sorption pump and 10-7 mbar for sequential pumping can be reached. A typical source of dry pure nitrogen would be a liquid nitrogen Dewar head space.
It has been suggested that by applying a dynamic pumping technique hydrogen, helium and neon can also be pumped without resorting to dry nitrogen purging. This is done by precooling the pump with the valve to the vacuum vessel closed. The valve is opened when the pump is cold and the inrush of adsorbable gases will carry all other gases into the pump. The valve is closed before hydrogen, helium or neon can back-migrate into the vacuum vessel. Sequential pumping can also be applied. No final pressures are given.
Continuous pumping may be simulated by using two pumps in parallel and letting one pump pump the system while the other pump, temporally sealed-off from the system, is in the desorption phase and venting to the atmosphere. When the pump is well desorbed it is cooled down and reconnected to the system. The other pump is sealed-off and goes into desorption. This becomes a continuous cycle.