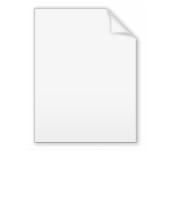
Parallels (engineering)
Encyclopedia
Parallels are rectangular blocks of metal, commonly made from tool steel
, stainless steel
or cast iron
, which have 2, 4 or 6 faces ground or lapped
to a precise surface finish. They are used when machining with a miller
, drill
or any other machining operation that requires work to be held in a vise
or with clamps
- to keep work parallel or raised evenly such as in a milling vise to give adequate height for the cutting tool/spindle to pass over.
on each side to remove any sharp edges.
Generally, workshop parallels have 4 faces that are machined and ground - the front, back and sides, although some do have the ends with a smooth surface. The surface of a parallel can often tell how it was manufactured, with a 'grain' showing that it was ground - and a smooth or mirrored finish showing it has been lapped. Parallels that have a good surface tolerance can be lightly bonded together by sliding or rotating two parallels together, and the smooth surfaces allows a temporary molecular-attraction
to take place - this is known as Wringing and is also found with gauge blocks
.
Parallels are first machined to rough dimensions, leaving a few millimeters to allow the rest to be ground. Parallels that only have 2 or 4 precision faces will often have the tool-marks from the machining on the non-ground sides. They are then paired and placed in a grinding machine, and each face is ground until the overall dimensions are correct - they are paired during this stage so that even if the dimensions are not correct, they are still parallel to each other. Then, the individual finishes are applied, from drilling to machining a chamfer
along the edges to remove any burrs or sharpened edges. They may also be lapped to achieve a mirror smooth surface. Most parallels are also hardened.
Parallels are manufactured to either imperial
or metric
dimensions, and are often sold in a set, with several pairs of different sizes.
, drill
ing, turning
or sometimes grinding. The most common use is to support work when it is in a vise or clamped to the machine bed. If a workpiece is too small to be machined in a vise without it being in contact with all three faces of the vice - parallels can be used either side to give clearance from the vise, and to give support from underneath to eliminate the workpiece being pushed down by the force of the cutting tool.
Parallels of different sizes can be used to support a workpiece that doesn't have a 'flat' surface underneath, or to give clearance when drilling in a vise to stop the drill damaging the vise. Parallels can also be used if the vise itself has a damaged face, which could cause the workpiece to be held insecurely.
Other uses include giving a raised surface when using t-slot clamps and for comparison with a surface or machined face to check the flatness
.
Tool steel
Tool steel refers to a variety of carbon and alloy steels that are particularly well-suited to be made into tools. Their suitability comes from their distinctive hardness, resistance to abrasion, their ability to hold a cutting edge, and/or their resistance to deformation at elevated temperatures...
, stainless steel
Stainless steel
In metallurgy, stainless steel, also known as inox steel or inox from French "inoxydable", is defined as a steel alloy with a minimum of 10.5 or 11% chromium content by mass....
or cast iron
Cast iron
Cast iron is derived from pig iron, and while it usually refers to gray iron, it also identifies a large group of ferrous alloys which solidify with a eutectic. The color of a fractured surface can be used to identify an alloy. White cast iron is named after its white surface when fractured, due...
, which have 2, 4 or 6 faces ground or lapped
Lapping
Lapping is a machining operation, in which two surfaces are rubbed together with an abrasive between them, by hand movement or by way of a machine.This can take two forms...
to a precise surface finish. They are used when machining with a miller
Milling machine
A milling machine is a machine tool used to machine solid materials. Milling machines are often classed in two basic forms, horizontal and vertical, which refers to the orientation of the main spindle. Both types range in size from small, bench-mounted devices to room-sized machines...
, drill
Drill
A drill or drill motor is a tool fitted with a cutting tool attachment or driving tool attachment, usually a drill bit or driver bit, used for drilling holes in various materials or fastening various materials together with the use of fasteners. The attachment is gripped by a chuck at one end of...
or any other machining operation that requires work to be held in a vise
Vise (tool)
A vise or vice is a mechanical screw apparatus used for holding or clamping a work piece to allow work to be performed on it with tools such as saws, planes, drills, mills, screwdrivers, sandpaper, etc. Vises usually have one fixed jaw and another, parallel, jaw which is moved towards or away from...
or with clamps
Clamp (tool)
A clamp is a fastening device to hold or secure objects tightly together to prevent movement or separation through the application of inward pressure...
- to keep work parallel or raised evenly such as in a milling vise to give adequate height for the cutting tool/spindle to pass over.
Description
Parallels come in pairs of two, which are machined to be the same dimensions their corresponding faces. They come in a variety of thicknesses and size, allowing them to be stacked up or to support a workpiece which doesn't have a flat profile. Parallels commonly have a series of holes drilled on the 'front' face - allowing them to be used to position a workpiece or secured using t-slot clamps, and a countersinkCountersink
A countersink is a conical hole cut into a manufactured object, or the cutter used to cut such a hole. A common usage is to allow the head of a countersunk bolt or screw, when placed in the hole, to sit flush with or below the surface of the surrounding material...
on each side to remove any sharp edges.
Generally, workshop parallels have 4 faces that are machined and ground - the front, back and sides, although some do have the ends with a smooth surface. The surface of a parallel can often tell how it was manufactured, with a 'grain' showing that it was ground - and a smooth or mirrored finish showing it has been lapped. Parallels that have a good surface tolerance can be lightly bonded together by sliding or rotating two parallels together, and the smooth surfaces allows a temporary molecular-attraction
Molecular attraction
Molecular attraction occurs when neutrally-charged molecules nevertheless experience the uneven distribution of electrons over their structure due to London Forces induced by random variations of electron density occurring in non-polar compounds, hydrogen bonding due to the production of what is...
to take place - this is known as Wringing and is also found with gauge blocks
Gauge blocks
A gauge block is a precision ground and lapped length measuring standard...
.
Manufacturing
There are two main grades of surface tolerance:- Grade A - Used for close-tolerance work, such as inspection or precision machining
- Grade B - Lower surface tolerances, and are used for lower-precision machining
Parallels are first machined to rough dimensions, leaving a few millimeters to allow the rest to be ground. Parallels that only have 2 or 4 precision faces will often have the tool-marks from the machining on the non-ground sides. They are then paired and placed in a grinding machine, and each face is ground until the overall dimensions are correct - they are paired during this stage so that even if the dimensions are not correct, they are still parallel to each other. Then, the individual finishes are applied, from drilling to machining a chamfer
Chamfer
A chamfer is a beveled edge connecting two surfaces. If the surfaces are at right angles, the chamfer will typically be symmetrical at 45 degrees. A fillet is the rounding off of an interior corner. A rounding of an exterior corner is called a "round" or a "radius"."Chamfer" is a term commonly...
along the edges to remove any burrs or sharpened edges. They may also be lapped to achieve a mirror smooth surface. Most parallels are also hardened.
Parallels are manufactured to either imperial
Imperial unit
The system of imperial units or the imperial system is the system of units first defined in the British Weights and Measures Act of 1824, which was later refined and reduced. The system came into official use across the British Empire...
or metric
Metric system
The metric system is an international decimalised system of measurement. France was first to adopt a metric system, in 1799, and a metric system is now the official system of measurement, used in almost every country in the world...
dimensions, and are often sold in a set, with several pairs of different sizes.
Uses
Parallels are used in machining operations, be it millingMilling machine
A milling machine is a machine tool used to machine solid materials. Milling machines are often classed in two basic forms, horizontal and vertical, which refers to the orientation of the main spindle. Both types range in size from small, bench-mounted devices to room-sized machines...
, drill
Drill
A drill or drill motor is a tool fitted with a cutting tool attachment or driving tool attachment, usually a drill bit or driver bit, used for drilling holes in various materials or fastening various materials together with the use of fasteners. The attachment is gripped by a chuck at one end of...
ing, turning
Turning
Turning is the process whereby a single point cutting tool is parallel to the surface. It can be done manually, in a traditional form of lathe, which frequently requires continuous supervision by the operator, or by using a computer controlled and automated lathe which does not. This type of...
or sometimes grinding. The most common use is to support work when it is in a vise or clamped to the machine bed. If a workpiece is too small to be machined in a vise without it being in contact with all three faces of the vice - parallels can be used either side to give clearance from the vise, and to give support from underneath to eliminate the workpiece being pushed down by the force of the cutting tool.
Parallels of different sizes can be used to support a workpiece that doesn't have a 'flat' surface underneath, or to give clearance when drilling in a vise to stop the drill damaging the vise. Parallels can also be used if the vise itself has a damaged face, which could cause the workpiece to be held insecurely.
Other uses include giving a raised surface when using t-slot clamps and for comparison with a surface or machined face to check the flatness
Flatness (manufacturing)
In manufacturing and mechanical engineering, flatness is an important geometric condition for workpieces and tools.In the manufacture of precision parts and assemblies, especially where parts will be required to be connected across a surface area in an air-tight or liquid-tight manner, flatness is...
.