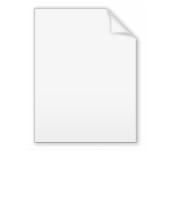
Fusible core injection molding
Encyclopedia
Fusible core injection molding, also known as lost core injection molding, is a specialized plastic
injection molding
process used to mold internal cavities or undercuts
that are not possible to mold with demoldable cores. Strictly speaking the term "fusible core injection molding refers to the use of a fusible alloy
as the core material; when the core material is made from a soluble plastic the process is known as soluble core injection molding. This process is often used for automotive parts, such as intake manifolds and brake housings
, however it is also used for aerospace
parts, plumbing
parts, bicycle wheel
s, and footwear
.
The most common molding materials are glass-filled nylon 6
and nylon 66. Other materials include unfilled nylons, polyphenylene sulfide, glass-filled polyaryletherketone
(PAEK), glass-filled polypropylene
(PP), rigid thermoplastic urethane
, and elastomeric thermoplastic polyurethane
.
took interest in it to develop intake manifolds.
in the shape of the cavity specified for the molded component. It can be made from a low melting point metal, such as a tin
-bismuth
alloy
, or a polymer
, such as a soluble acrylate
. The polymer has approximately the same melting temperature as the alloy, 275 °F (135 °C), however the alloy ratios can be modified to alter the melting point. Another advantage to using a metal core is that multiple smaller cores can be cast with mating plugs and holes so they can be assembled into a final large core.
One key in casting metal cores is to make sure they do not contain any porosity
as it will induce flaws into the molded part. In order to minimize porosity the metal may be gravity cast or the molding cavity may be pressurized. Another system slowly rocks the casting dies as the molding cavity fills to "shake" the air bubbles out.
The metal cores can be made from a number of low melting point alloys, with the most common being a mixture of 58% bismuth and 42% tin, which is used for molding nylon 66. One of the main reasons its used is because it expands as it cools which packs the mold well. Other alloys include tin-lead-silver alloys and tin-lead-antimony alloys. Between these three alloy groups a melting point between 98 and 800 °F (37–425 °C) can be achieved.
Polymer cores are not as common as metal cores and are usually only used for moldings that require simple internal surface details. They are usually 0.125 to 0.25 in (3.2 to 6.4 mm) thick hollow cross-sections that are molded in two halves and are ultrasonically welded
together. Their greatest advantage is that they can be molded in traditional injection molding machines that the company already has instead of investing into new die casting equipment and learning how to use it. Because of this polymer core materials are most adventitious for small production runs that cannot justify the added expense of metal cores. Unfortunately it is not as recyclable as the metal alloys used in cores, because 10% new material must be added with the recycled material.
, or through a combination of the two. Hot baths usually use a tub filled with glycol or Lutron
, which is a phenol
-based liquid. The bath temperature is slightly higher than that of the core alloy’s melting point, but not so high that it damages the molding. In typical commercial applications the parts are dipped into the hot bath via an overhead conveyor. The advantage to using a hot bath is that it is simpler than induction heating and it helps cure thermoset moldings. The disadvantage is that it is uneconomically slow at a cycle time of 60 to 90 minutes and it poses environmental cleanup issues. Typically a the hot bath solution needs cleaning or replacement every year or every half year when used in combination with induction heating.
For thermoplastic moldings induction heating of the core metal is required, otherwise the prolonged heat from a hot bath can warp it. Induction heating reduces the melt-out time to one to three minutes. The disadvantage is that induction heating does not remove all of the core material so it must then be finished off in a hot bath or be brushed out. Another disadvantage is that the induction coils must be custom built for each molding because the coils must be 1 to 4 in (25.4 to 101.6 mm) from the part. Finally, induction heating systems cannot be used with moldings that have brass
or steel inserts because the induction heating process can destroy or oxidize the insert.
For complex parts it can be difficult to get all of the core liquid to drain out in either melt-out process. In order to overcome this the parts may be rotated for up to an hour. Liquid core metal collects on the bottom of the heated bath and is usable for a new core.
s have been used since the mid-1980s, however loading and unloading 100 to 200 lb (45.4 to 90.7 kg) cores are difficult so two robot
s are required. Moreover, the cycle time is quite long, approximately 28 seconds. These problem are overcome by using rotary or shuttle action injection molding machines. These types of machines only require one robot to load and unload cores and have a 30% shorter cycle time. However, these types of machines cost approximately 35% more than horizontal machines, require more space, and require two bottom molds (because one is in the machine during the cycle and the other is being unloaded and loaded with a new core), which adds approximately 40% to the tooling cost. For small parts, horizontal injection molding machines are still used, because the core does not weigh enough to justify the use of a rotary machine.
For four-cylinder manifolds a 500-ton press is required; for a six- to eight-cylinder manifold a 600- to 800-ton press is required.
and wear. Other advantages include:
Two of the major disadvantages of this process are the high cost and long development time. An automotive part can take four years to develop; two years in the prototype stage and two years to reach production. Not all products take this long, for instance a two-way valve produced by Johnson Controls
only took 18 months. The initial cost can be as much as US$8 million to produce a four-cylinder engine manifold. However, computer flow analysis has helped reduce lead time and costs.
One of the difficulties that result from these long development times and high costs is making accurate cores repeatably. This is extremely important because the core is an integral part of the mold, so essentially each shot is into a new mold cavity. Another difficulty is keeping the core from melting when the plastic is shot into the mold, because the plastic is approximately twice the melting temperature of the core material. A third difficulty is the low strength of the core. Hollow plastic cores can collapse if too much pressure is used in the shot plastic. Metal cores are solid so they cannot collapse, but are only 10% as strong as steel cores so they can distort. This is especially a problem when molding manifolds, because the waviness
of the core can be detrimental to the airflow within the runners.
Another disadvantage is the need for a large space to house the injection molding machines, casting machines, melt-out equipment, and robots.
Because of these disadvantages, some moldings that would be made via this process are instead made by injection molding two or more parts in a traditional injection molding machine and then vibration welding them together. This process is less expensive and requires much less capital, however it imparts more design constraints. Because of the design constraints, sometimes parts are made with both processes to gain the advantages of both.
s, but with corresponding core alloys also to thermosetting plastic
molding materials (duroplast
). The fusible core process finds application, for example, for injection molded passenger car engine intake manifolds. By modifying the equipment, small molded parts like valve
s or pump
housings can be manufactured, as the manufacture of the fusible cores and the injected parts can be carried out on an injection molding machine.
Plastic
A plastic material is any of a wide range of synthetic or semi-synthetic organic solids used in the manufacture of industrial products. Plastics are typically polymers of high molecular mass, and may contain other substances to improve performance and/or reduce production costs...
injection molding
Injection molding
Injection molding is a manufacturing process for producing parts from both thermoplastic and thermosetting plastic materials. Material is fed into a heated barrel, mixed, and forced into a mold cavity where it cools and hardens to the configuration of the cavity...
process used to mold internal cavities or undercuts
Undercut (manufacturing)
In manufacturing, an undercut is a special type of recessed surface. In turning it refers to a recess in a diameter. In machining it refers to a recess in a corner. In molding it refers to a feature that cannot be molded using only a single pull mold...
that are not possible to mold with demoldable cores. Strictly speaking the term "fusible core injection molding refers to the use of a fusible alloy
Fusible alloy
A fusible alloy is a metal alloy capable of being easily fused, i.e. easily meltable, at relatively low temperatures. Fusible alloys are commonly, but not necessarily, eutectic alloys....
as the core material; when the core material is made from a soluble plastic the process is known as soluble core injection molding. This process is often used for automotive parts, such as intake manifolds and brake housings
Brake
A brake is a mechanical device which inhibits motion. Its opposite component is a clutch. The rest of this article is dedicated to various types of vehicular brakes....
, however it is also used for aerospace
Aerospace
Aerospace comprises the atmosphere of Earth and surrounding space. Typically the term is used to refer to the industry that researches, designs, manufactures, operates, and maintains vehicles moving through air and space...
parts, plumbing
Plumbing
Plumbing is the system of pipes and drains installed in a building for the distribution of potable drinking water and the removal of waterborne wastes, and the skilled trade of working with pipes, tubing and plumbing fixtures in such systems. A plumber is someone who installs or repairs piping...
parts, bicycle wheel
Bicycle wheel
A bicycle wheel is a wheel, most commonly a wire wheel, designed for bicycle. A pair is often called a wheelset, especially in the context of ready built "off the shelf" performance-oriented wheels....
s, and footwear
Footwear
Footwear consists of garments worn on the feet, for fashion, protection against the environment, and adornment. Being barefoot is commonly associated with poverty, but some cultures chose not to wear footwear at least in some situations....
.
The most common molding materials are glass-filled nylon 6
Nylon 6
Nylon 6 or polycaprolactam is a polymer developed by Paul Schlack at IG Farben to reproduce the properties of nylon 6,6 without violating the patent on its production. Unlike most other nylons, nylon 6 is not a condensation polymer, but instead is formed by ring-opening polymerization. This makes...
and nylon 66. Other materials include unfilled nylons, polyphenylene sulfide, glass-filled polyaryletherketone
Polyaryletherketone
Polyaryletherketone is a family of semi-crystalline thermoplastics with high-temperature stability and high mechanical strength.-Properties:...
(PAEK), glass-filled polypropylene
Polypropylene
Polypropylene , also known as polypropene, is a thermoplastic polymer used in a wide variety of applications including packaging, textiles , stationery, plastic parts and reusable containers of various types, laboratory equipment, loudspeakers, automotive components, and polymer banknotes...
(PP), rigid thermoplastic urethane
Polyurethane
A polyurethane is any polymer composed of a chain of organic units joined by carbamate links. Polyurethane polymers are formed through step-growth polymerization, by reacting a monomer with another monomer in the presence of a catalyst.Polyurethanes are...
, and elastomeric thermoplastic polyurethane
Polyurethane
A polyurethane is any polymer composed of a chain of organic units joined by carbamate links. Polyurethane polymers are formed through step-growth polymerization, by reacting a monomer with another monomer in the presence of a catalyst.Polyurethanes are...
.
History
The first patent for this type of molding process was taken out in 1968, however it was rarely used until the 1980s. That is when the automotive industryAutomotive industry
The automotive industry designs, develops, manufactures, markets, and sells motor vehicles, and is one of the world's most important economic sectors by revenue....
took interest in it to develop intake manifolds.
Process
The process consists of three major steps: casting or molding a core, inserting the core into the mold and shooting the mold, and finally removing the molding and melting out the core.Core
First, a core is molded or die castDie casting
Die casting is a metal casting process that is characterized by forcing molten metal under high pressure into a mold cavity. The mold cavity is created using two hardened tool steel dies which have been machined into shape and work similarly to an injection mold during the process...
in the shape of the cavity specified for the molded component. It can be made from a low melting point metal, such as a tin
Tin
Tin is a chemical element with the symbol Sn and atomic number 50. It is a main group metal in group 14 of the periodic table. Tin shows chemical similarity to both neighboring group 14 elements, germanium and lead and has two possible oxidation states, +2 and the slightly more stable +4...
-bismuth
Bismuth
Bismuth is a chemical element with symbol Bi and atomic number 83. Bismuth, a trivalent poor metal, chemically resembles arsenic and antimony. Elemental bismuth may occur naturally uncombined, although its sulfide and oxide form important commercial ores. The free element is 86% as dense as lead...
alloy
Alloy
An alloy is a mixture or metallic solid solution composed of two or more elements. Complete solid solution alloys give single solid phase microstructure, while partial solutions give two or more phases that may or may not be homogeneous in distribution, depending on thermal history...
, or a polymer
Polymer
A polymer is a large molecule composed of repeating structural units. These subunits are typically connected by covalent chemical bonds...
, such as a soluble acrylate
Acrylate
The acrylate ion is the ion of acrylic acid.Acrylates are the salts and esters of acrylic acid. They are also known as propenoates ....
. The polymer has approximately the same melting temperature as the alloy, 275 °F (135 °C), however the alloy ratios can be modified to alter the melting point. Another advantage to using a metal core is that multiple smaller cores can be cast with mating plugs and holes so they can be assembled into a final large core.
One key in casting metal cores is to make sure they do not contain any porosity
Porosity
Porosity or void fraction is a measure of the void spaces in a material, and is a fraction of the volume of voids over the total volume, between 0–1, or as a percentage between 0–100%...
as it will induce flaws into the molded part. In order to minimize porosity the metal may be gravity cast or the molding cavity may be pressurized. Another system slowly rocks the casting dies as the molding cavity fills to "shake" the air bubbles out.
The metal cores can be made from a number of low melting point alloys, with the most common being a mixture of 58% bismuth and 42% tin, which is used for molding nylon 66. One of the main reasons its used is because it expands as it cools which packs the mold well. Other alloys include tin-lead-silver alloys and tin-lead-antimony alloys. Between these three alloy groups a melting point between 98 and 800 °F (37–425 °C) can be achieved.
Polymer cores are not as common as metal cores and are usually only used for moldings that require simple internal surface details. They are usually 0.125 to 0.25 in (3.2 to 6.4 mm) thick hollow cross-sections that are molded in two halves and are ultrasonically welded
Ultrasonic welding
Ultrasonic welding is an industrial technique whereby high-frequency ultrasonic acoustic vibrations are locally applied to workpieces being held together under pressure to create a solid-state weld. It is commonly used for plastics, and especially for joining dissimilar materials...
together. Their greatest advantage is that they can be molded in traditional injection molding machines that the company already has instead of investing into new die casting equipment and learning how to use it. Because of this polymer core materials are most adventitious for small production runs that cannot justify the added expense of metal cores. Unfortunately it is not as recyclable as the metal alloys used in cores, because 10% new material must be added with the recycled material.
Molding
In the second step, the core is then inserted into the mold. For simple molds this is as simple as inserting the core and closing the dies. However, more complex tools require multiple steps from the programmed robot. For instance, some complex tools can have multiple conventional side pulls that mate with the core to add rigidity to the core and reduce the core mass. After the core is loaded and the press closed the plastic is shot.Melt-out
In the final step, the molded component and core are both demolded and the core is melted-out from the molding. This is done in a hot bath, via induction heatingInduction heating
Induction heating is the process of heating an electrically conducting object by electromagnetic induction, where eddy currents are generated within the metal and resistance leads to Joule heating of the metal...
, or through a combination of the two. Hot baths usually use a tub filled with glycol or Lutron
Lutron
Lutron Electronics Company, Inc. is a privately held corporation that designs, manufactures, and sells lighting control systems and a variety of other related products...
, which is a phenol
Phenol
Phenol, also known as carbolic acid, phenic acid, is an organic compound with the chemical formula C6H5OH. It is a white crystalline solid. The molecule consists of a phenyl , bonded to a hydroxyl group. It is produced on a large scale as a precursor to many materials and useful compounds...
-based liquid. The bath temperature is slightly higher than that of the core alloy’s melting point, but not so high that it damages the molding. In typical commercial applications the parts are dipped into the hot bath via an overhead conveyor. The advantage to using a hot bath is that it is simpler than induction heating and it helps cure thermoset moldings. The disadvantage is that it is uneconomically slow at a cycle time of 60 to 90 minutes and it poses environmental cleanup issues. Typically a the hot bath solution needs cleaning or replacement every year or every half year when used in combination with induction heating.
For thermoplastic moldings induction heating of the core metal is required, otherwise the prolonged heat from a hot bath can warp it. Induction heating reduces the melt-out time to one to three minutes. The disadvantage is that induction heating does not remove all of the core material so it must then be finished off in a hot bath or be brushed out. Another disadvantage is that the induction coils must be custom built for each molding because the coils must be 1 to 4 in (25.4 to 101.6 mm) from the part. Finally, induction heating systems cannot be used with moldings that have brass
Brass
Brass is an alloy of copper and zinc; the proportions of zinc and copper can be varied to create a range of brasses with varying properties.In comparison, bronze is principally an alloy of copper and tin...
or steel inserts because the induction heating process can destroy or oxidize the insert.
For complex parts it can be difficult to get all of the core liquid to drain out in either melt-out process. In order to overcome this the parts may be rotated for up to an hour. Liquid core metal collects on the bottom of the heated bath and is usable for a new core.
Equipment
Traditional horizontal injection molding machineInjection molding machine
An Injection molding machine, also known as an injection press, is a machine for manufacturing plastic products by the injection molding process. It consists of two main parts, an injection unit and a clamping unit....
s have been used since the mid-1980s, however loading and unloading 100 to 200 lb (45.4 to 90.7 kg) cores are difficult so two robot
Robot
A robot is a mechanical or virtual intelligent agent that can perform tasks automatically or with guidance, typically by remote control. In practice a robot is usually an electro-mechanical machine that is guided by computer and electronic programming. Robots can be autonomous, semi-autonomous or...
s are required. Moreover, the cycle time is quite long, approximately 28 seconds. These problem are overcome by using rotary or shuttle action injection molding machines. These types of machines only require one robot to load and unload cores and have a 30% shorter cycle time. However, these types of machines cost approximately 35% more than horizontal machines, require more space, and require two bottom molds (because one is in the machine during the cycle and the other is being unloaded and loaded with a new core), which adds approximately 40% to the tooling cost. For small parts, horizontal injection molding machines are still used, because the core does not weigh enough to justify the use of a rotary machine.
For four-cylinder manifolds a 500-ton press is required; for a six- to eight-cylinder manifold a 600- to 800-ton press is required.
Advantages and disadvantages
The greatest advantage of this process is its ability to produce single-piece injection moldings with highly complex interior geometries without secondary operations. Similarly shaped objects are usually made from aluminium castings, which can weigh 45% to 75% more than a comparable molding. The tooling also lasts longer than metal casting tooling due to the lack of chemical corrosionCorrosion
Corrosion is the disintegration of an engineered material into its constituent atoms due to chemical reactions with its surroundings. In the most common use of the word, this means electrochemical oxidation of metals in reaction with an oxidant such as oxygen...
and wear. Other advantages include:
- Very good surface quality with no weak areas due to joints or welds
- High dimensional accuracy and structural integrity
- Not labor intensive due to the few secondary operations required
- Little waste
- Inserts can be incorporated
Two of the major disadvantages of this process are the high cost and long development time. An automotive part can take four years to develop; two years in the prototype stage and two years to reach production. Not all products take this long, for instance a two-way valve produced by Johnson Controls
Johnson Controls
Johnson Controls, Inc. is a company, based in Milwaukee, Wisconsin, USA. It was founded in 1885 by professor Warren S. Johnson, inventor of the first electric room thermostat....
only took 18 months. The initial cost can be as much as US$8 million to produce a four-cylinder engine manifold. However, computer flow analysis has helped reduce lead time and costs.
One of the difficulties that result from these long development times and high costs is making accurate cores repeatably. This is extremely important because the core is an integral part of the mold, so essentially each shot is into a new mold cavity. Another difficulty is keeping the core from melting when the plastic is shot into the mold, because the plastic is approximately twice the melting temperature of the core material. A third difficulty is the low strength of the core. Hollow plastic cores can collapse if too much pressure is used in the shot plastic. Metal cores are solid so they cannot collapse, but are only 10% as strong as steel cores so they can distort. This is especially a problem when molding manifolds, because the waviness
Waviness
Waviness is the measure of the more widely spaced component of surface texture. It is a broader view of roughness because it is more strictly defined as "the irregularities whose spacing is greater than the roughness sampling length"...
of the core can be detrimental to the airflow within the runners.
Another disadvantage is the need for a large space to house the injection molding machines, casting machines, melt-out equipment, and robots.
Because of these disadvantages, some moldings that would be made via this process are instead made by injection molding two or more parts in a traditional injection molding machine and then vibration welding them together. This process is less expensive and requires much less capital, however it imparts more design constraints. Because of the design constraints, sometimes parts are made with both processes to gain the advantages of both.
Application
The application of the fusible core process is not limited just to the injection of thermoplasticThermoplastic
Thermoplastic, also known as a thermosoftening plastic, is a polymer that turns to a liquid when heated and freezes to a very glassy state when cooled sufficiently...
s, but with corresponding core alloys also to thermosetting plastic
Thermosetting plastic
A thermosetting plastic, also known as a thermoset, is polymer material that irreversibly cures. The cure may be done through heat , through a chemical reaction , or irradiation such as electron beam processing.Thermoset materials are usually liquid or malleable prior to curing and designed to be...
molding materials (duroplast
Duroplast
Duroplast is a composite thermosetting plastic, a close relative of formica and bakelite. It is a resin plastic reinforced with fibers making it a fiber-reinforced plastic similar to glass-reinforced plastic.-Uses:...
). The fusible core process finds application, for example, for injection molded passenger car engine intake manifolds. By modifying the equipment, small molded parts like valve
Valve
A valve is a device that regulates, directs or controls the flow of a fluid by opening, closing, or partially obstructing various passageways. Valves are technically pipe fittings, but are usually discussed as a separate category...
s or pump
Pump
A pump is a device used to move fluids, such as liquids, gases or slurries.A pump displaces a volume by physical or mechanical action. Pumps fall into three major groups: direct lift, displacement, and gravity pumps...
housings can be manufactured, as the manufacture of the fusible cores and the injected parts can be carried out on an injection molding machine.