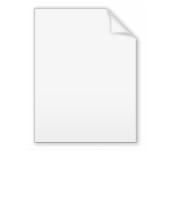
Finery forge
Encyclopedia
Iron
tapped from the blast furnace
is pig iron
, and contains significant amounts of carbon
and silicon
. To produce malleable wrought iron
, it needs to undergo a further process
. In the early modern period, this was carried out in a finery forge.
There were several types of finery forges. The dominant type in Sweden
was the German forge, which had a single hearth
that was used for all processes. In Uppland
north of Stockholm
and certain adjacent provinces, another kind known as the Walloon forge was used, mainly for the production of a particularly pure kind of iron known as oregrounds iron
, which was exported to England to make blister steel
. Its purity depended on the use of ore from the Dannemora
mine. The Walloon forge was virtually the only kind used in Great Britain
.
The forge had two kinds of hearth, the finery and the chafery
or string-furnace. In the finery, the finer remelted pig iron
so as to oxidise the carbon (and silicon). This produced a lump of iron (with some slag
) known as a bloom
. This was consolidated using a water-powered hammer (see trip hammer
) and returned to the finery. The next stages were undertaken by the hammerman, who in some iron-making areas such as South Yorkshire
was also known as the stringsmith, heating his iron in a string-furnace. Because the bloom is highly porous, and its open spaces are full of slag, the hammerman's or stringfellow's tasks were to beat the heated bloom with a hammer, to drive the molten slag out of it, and then to draw
the bloom out into a bar to produce what was known as bar iron. In the course of doing so, he had to reheat the iron, for which he used the chafery. The fuel in the finery had to be charcoal
, because impurities in any mineral fuel would affect the quality of the iron.
This is an obsolete process of making iron
. The finery forge process began to be replaced from the late 18th century by others, of which puddling
was the most successful. These used mineral fuel (coal
or coke
), and freed the iron industry from its dependence on the speed of growth of trees. That transition is the industrial revolution
for the iron industry.
Iron
Iron is a chemical element with the symbol Fe and atomic number 26. It is a metal in the first transition series. It is the most common element forming the planet Earth as a whole, forming much of Earth's outer and inner core. It is the fourth most common element in the Earth's crust...
tapped from the blast furnace
Blast furnace
A blast furnace is a type of metallurgical furnace used for smelting to produce industrial metals, generally iron.In a blast furnace, fuel and ore and flux are continuously supplied through the top of the furnace, while air is blown into the bottom of the chamber, so that the chemical reactions...
is pig iron
Pig iron
Pig iron is the intermediate product of smelting iron ore with a high-carbon fuel such as coke, usually with limestone as a flux. Charcoal and anthracite have also been used as fuel...
, and contains significant amounts of carbon
Carbon
Carbon is the chemical element with symbol C and atomic number 6. As a member of group 14 on the periodic table, it is nonmetallic and tetravalent—making four electrons available to form covalent chemical bonds...
and silicon
Silicon
Silicon is a chemical element with the symbol Si and atomic number 14. A tetravalent metalloid, it is less reactive than its chemical analog carbon, the nonmetal directly above it in the periodic table, but more reactive than germanium, the metalloid directly below it in the table...
. To produce malleable wrought iron
Wrought iron
thumb|The [[Eiffel tower]] is constructed from [[puddle iron]], a form of wrought ironWrought iron is an iron alloy with a very low carbon...
, it needs to undergo a further process
Decarburization
Decarburization is the process opposite to carburization, namely aimed at decreasing the content of carbon in metals . Decarburization occurs when Carbon in the metal reacts with gasses present in the atmosphere...
. In the early modern period, this was carried out in a finery forge.
There were several types of finery forges. The dominant type in Sweden
Sweden
Sweden , officially the Kingdom of Sweden , is a Nordic country on the Scandinavian Peninsula in Northern Europe. Sweden borders with Norway and Finland and is connected to Denmark by a bridge-tunnel across the Öresund....
was the German forge, which had a single hearth
Hearth
In common historic and modern usage, a hearth is a brick- or stone-lined fireplace or oven often used for cooking and/or heating. For centuries, the hearth was considered an integral part of a home, often its central or most important feature...
that was used for all processes. In Uppland
Uppland
Uppland is a historical province or landskap on the eastern coast of Sweden, just north of Stockholm, the capital. It borders Södermanland, Västmanland and Gästrikland. It is also bounded by lake Mälaren and the Baltic sea...
north of Stockholm
Stockholm
Stockholm is the capital and the largest city of Sweden and constitutes the most populated urban area in Scandinavia. Stockholm is the most populous city in Sweden, with a population of 851,155 in the municipality , 1.37 million in the urban area , and around 2.1 million in the metropolitan area...
and certain adjacent provinces, another kind known as the Walloon forge was used, mainly for the production of a particularly pure kind of iron known as oregrounds iron
Oregrounds iron
Oregrounds iron was a grade of iron that was regarded as the best grade available in 18th century England. The term was derived from the small Swedish city of Öregrund. The process to create it is known as the Walloon method....
, which was exported to England to make blister steel
Cementation process
The cementation process is an obsolete technique for making steel by carburization of iron. Unlike modern steelmaking, it increased the amount of carbon in the iron. It was apparently developed before the 17th century. Derwentcote Steel Furnace, built in 1720, is the earliest surviving example...
. Its purity depended on the use of ore from the Dannemora
Dannemora, Sweden
Dannemora is an old mining town and a locality situated in Östhammar Municipality, Uppsala County, Sweden with 238 inhabitants in 2005.-Dannemora mine:...
mine. The Walloon forge was virtually the only kind used in Great Britain
Great Britain
Great Britain or Britain is an island situated to the northwest of Continental Europe. It is the ninth largest island in the world, and the largest European island, as well as the largest of the British Isles...
.
The forge had two kinds of hearth, the finery and the chafery
Chafery
A chafery is a variety of hearth used in ironmaking for reheating a bloom of iron, in the course of its being drawn out into a bar of wrought iron....
or string-furnace. In the finery, the finer remelted pig iron
Pig iron
Pig iron is the intermediate product of smelting iron ore with a high-carbon fuel such as coke, usually with limestone as a flux. Charcoal and anthracite have also been used as fuel...
so as to oxidise the carbon (and silicon). This produced a lump of iron (with some slag
Slag
Slag is a partially vitreous by-product of smelting ore to separate the metal fraction from the unwanted fraction. It can usually be considered to be a mixture of metal oxides and silicon dioxide. However, slags can contain metal sulfides and metal atoms in the elemental form...
) known as a bloom
Bloomery
A bloomery is a type of furnace once widely used for smelting iron from its oxides. The bloomery was the earliest form of smelter capable of smelting iron. A bloomery's product is a porous mass of iron and slag called a bloom. This mix of slag and iron in the bloom is termed sponge iron, which...
. This was consolidated using a water-powered hammer (see trip hammer
Trip hammer
A trip hammer, also known as a helve hammer, is a massive powered hammer used in:* agriculture to facilitate the labor of pounding, decorticating and polishing of grain;...
) and returned to the finery. The next stages were undertaken by the hammerman, who in some iron-making areas such as South Yorkshire
South Yorkshire
South Yorkshire is a metropolitan county in the Yorkshire and the Humber region of England. It has a population of 1.29 million. It consists of four metropolitan boroughs: Barnsley, Doncaster, Rotherham, and City of Sheffield...
was also known as the stringsmith, heating his iron in a string-furnace. Because the bloom is highly porous, and its open spaces are full of slag, the hammerman's or stringfellow's tasks were to beat the heated bloom with a hammer, to drive the molten slag out of it, and then to draw
Shingling (metallurgy)
Shingling was a stage in the production of bar iron or steel, in the finery and puddling processes. As with many ironmaking terms, this is derived from the French - cinglage....
the bloom out into a bar to produce what was known as bar iron. In the course of doing so, he had to reheat the iron, for which he used the chafery. The fuel in the finery had to be charcoal
Charcoal
Charcoal is the dark grey residue consisting of carbon, and any remaining ash, obtained by removing water and other volatile constituents from animal and vegetation substances. Charcoal is usually produced by slow pyrolysis, the heating of wood or other substances in the absence of oxygen...
, because impurities in any mineral fuel would affect the quality of the iron.
This is an obsolete process of making iron
Wrought iron
thumb|The [[Eiffel tower]] is constructed from [[puddle iron]], a form of wrought ironWrought iron is an iron alloy with a very low carbon...
. The finery forge process began to be replaced from the late 18th century by others, of which puddling
Puddling (metallurgy)
Puddling was an Industrial Revolution means of making iron and steel. In the original puddling technique, molten iron in a reverberatory furnace was stirred with rods, which were consumed in the process...
was the most successful. These used mineral fuel (coal
Coal
Coal is a combustible black or brownish-black sedimentary rock usually occurring in rock strata in layers or veins called coal beds or coal seams. The harder forms, such as anthracite coal, can be regarded as metamorphic rock because of later exposure to elevated temperature and pressure...
or coke
Coke (fuel)
Coke is the solid carbonaceous material derived from destructive distillation of low-ash, low-sulfur bituminous coal. Cokes from coal are grey, hard, and porous. While coke can be formed naturally, the commonly used form is man-made.- History :...
), and freed the iron industry from its dependence on the speed of growth of trees. That transition is the industrial revolution
Industrial Revolution
The Industrial Revolution was a period from the 18th to the 19th century where major changes in agriculture, manufacturing, mining, transportation, and technology had a profound effect on the social, economic and cultural conditions of the times...
for the iron industry.