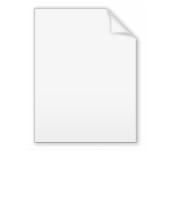
Failure mode and effects analysis
Encyclopedia
A failure modes and effects analysis (FMEA) is a procedure
in product development and operations management
for analysis of potential failure modes within a system for classification by the severity and likelihood of the failures. A successful FMEA activity helps a team to identify potential failure modes based on past experience with similar products or processes, enabling the team to design those failures out of the system with the minimum of effort and resource expenditure, thereby reducing development time and costs. It is widely used in manufacturing industries in various phases of the product life cycle and is now increasingly finding use in the service industry. Failure modes are any errors or defects in a process, design, or item, especially those that affect the customer, and can be potential or actual. Effects analysis refers to studying the consequences of those failures.
Failure mode
Failure effect
Indenture levels
Local effect
Next higher level effect
End effect
Failure cause
Severity
(1949; revised in 1980 as MIL-STD-1629A). By the early 1960s, contractors for the U.S. National Aeronautics and Space Administration (NASA) were using variations of FMECA or FMEA under a variety of names. NASA programs using FMEA variants included Apollo, Viking
, Voyager
, Magellan
, Galileo, and Skylab
. The civil aviation industry was an early adopter of FMEA, with the Society for Automotive Engineers
publishing ARP926 in 1967.
During the 1970's, use of FMEA and related techniques spread to other industries. In 1971 NASA prepared a report for the U.S. Geological Survey
recommending the use of FMEA in assessment of offshore petroleum exploration. FMEA as application for HACCP on the Apollo Space Program moved into the food
industry in general. In the late 1970s the Ford Motor Company
introduced FMEA to the automotive industry for safety and regulatory consideration after the Pinto
affair. They applied the same approach to processes (PFMEA) to consider potential process induced failures prior to launching production.
Although initially developed by the military, FMEA methodology is now extensively used in a variety of industries including semiconductor processing, food service, plastics, software, and healthcare. It is integrated into the Automotive Industry Action Group
's (AIAG) Advanced Product Quality Planning (APQP) process to provide risk mitigation, in both product and process development phases. Each potential cause must be considered for its effect on the product or process and, based on the risk, actions are determined and risks revisited after actions are complete. Toyota has taken this one step further with its Design Review Based on Failure Mode
(DRBFM) approach. The method is now supported by the American Society for Quality
which provides detailed guides on applying the method.
The outcomes of an FMEA development are actions to prevent or reduce the severity or likelihood of failures, starting with the highest-priority ones. It may be used to evaluate risk management
priorities for mitigating known threat vulnerabilities. FMEA helps select remedial actions that reduce cumulative impacts of life-cycle consequences (risks) from a systems failure (fault).
It is used in many formal quality system
s such as QS-9000 or ISO/TS 16949.
.
A robustness analysis can be obtained from interface matrices, boundary diagrams, and parameter diagrams. Failures are often found from external 'noise factors' and from shared interfaces with other parts and/or systems.
Typically, a description of the system and its function is developed, considering both intentional and unintentional uses.
A block diagram of the system is often created for inclusion with the FMEA, giving an overview of the major components or process steps and how they are related. These are called logical relations around which the FMEA can be developed.
The primary FME document or 'worksheet' lists all of the items or functions of the system in a logical manner, typically based on the block diagram.
NOTE: Above shown example format is not in line with mil.std 1629 or Civil Aerospace practise. The basic terms as given in first paragraph of this page are not available in this template!
A failure mode is given an occurrence ranking (O), again 1–10. Actions need to be determined if the occurrence is high (meaning > 4 for non-safety failure modes and > 1 when the severity-number from step 1 is 1 or 0). This step is called the detailed development section of the FMEA process. Occurrence also can be defined as %. If a non-safety issue happened less than 1%, we can give 1 to it. It is based on your product and customer specification.
A failure mode in one component can lead to a failure mode in another component, therefore each failure mode should be listed in technical terms and for function.
Hereafter the ultimate effect of each failure mode needs to be considered. A failure effect is defined as the result of a failure mode on the function of the system as perceived by the user. In this way it is convenient to write these effects down in terms of what the user might see or experience. Examples of failure effects are: degraded performance, noise or even injury to a user.
Each effect is given a severity number (S) from 1 (no danger) to 10 (critical). These numbers help an engineer to prioritize the failure modes and their effects. If the sensitivity of an effect has a number 9 or 10, actions are considered to change the design by eliminating the failure mode, if possible, or protecting the user from the effect. A severity rating of 9 or 10 is generally reserved for those effects which would cause injury to a user or otherwise result in litigation.
After these three basic steps, risk priority numbers (RPN) are calculated
After ranking the severity, occurrence and detectability the RPN can be easily calculated by multiplying these three numbers:
RPN = S × O × D
This has to be done for the entire process and/or design. Once this is done it is easy to determine the areas of greatest concern. The failure modes that have the highest RPN should be given the highest priority for corrective action.
This means it is not always the failure modes with the highest severity numbers that should be treated first. There could be less severe failures, but which occur more often and are less detectable.
After these values are allocated, recommended actions with targets, responsibility and dates of implementation are noted. These actions can include specific inspection, testing or quality procedures, redesign (such as selection of new components), adding more redundancy and limiting environmental stresses or operating range.
Once the actions have been implemented in the design/process, the new RPN should be checked, to confirm the improvements. These tests are often put in graphs, for easy visualization. Whenever a design or a process changes, an FMEA should be updated.
A few logical but important thoughts come in mind:
, where documentation is vital to implementation. General texts and detailed publications are available in forensic engineering
and failure analysis
. It is a general requirement of many specific national and international standards that FMEA is used in evaluating product integrity.
If used as a top-down
tool, FMEA may only identify major failure modes in a system. Fault tree analysis
(FTA) is better suited for "top-down" analysis. When used as a "bottom-up" tool FMEA can augment or complement FTA and identify many more causes and failure modes resulting in top-level symptoms. It is not able to discover complex failure modes involving multiple failures within a subsystem, or to report expected failure intervals of particular failure modes up to the upper level subsystem or system.
Additionally, the multiplication of the severity, occurrence and detection rankings may result in rank reversals, where a less serious failure mode receives a higher RPN than a more serious failure mode. The reason for this is that the rankings are ordinal scale numbers, and multiplication is not defined for ordinal numbers. The ordinal rankings only say that one ranking is better or worse than another, but not by how much. For instance, a ranking of "2" may not be twice as bad as a ranking of "1," or an "8" may not be twice as bad as a "4," but multiplication treats them as though they are. See Level of measurement
for further discussion.
Procedure
Procedure may refer to:* Procedure * Medical procedure* Algorithm, in mathematics and computing, a set of operations or calculations that accomplish some goal* Instructions or recipes, a set of commands that show how to prepare or make something...
in product development and operations management
Operations management
Operations management is an area of management concerned with overseeing, designing, and redesigning business operations in the production of goods and/or services. It involves the responsibility of ensuring that business operations are efficient in terms of using as little resources as needed, and...
for analysis of potential failure modes within a system for classification by the severity and likelihood of the failures. A successful FMEA activity helps a team to identify potential failure modes based on past experience with similar products or processes, enabling the team to design those failures out of the system with the minimum of effort and resource expenditure, thereby reducing development time and costs. It is widely used in manufacturing industries in various phases of the product life cycle and is now increasingly finding use in the service industry. Failure modes are any errors or defects in a process, design, or item, especially those that affect the customer, and can be potential or actual. Effects analysis refers to studying the consequences of those failures.
Basic terms
Failure- The loss of an intended function of a device under stated conditions.
Failure mode
- The manner by which a failure is observed; it generally describes the way the failure occurs.
Failure effect
- Immediate consequences of a failure on operation, function or functionality, or status of some item
Indenture levels
- An identifier for item complexity. Complexity increases as levels are closer to one.
Local effect
- The failure effect as it applies to the item under analysis.
Next higher level effect
- The failure effect as it applies at the next higher indenture level.
End effect
- The failure effect at the highest indenture level or total system.
Failure cause
- Defects in design, process, quality, or part application, which are the underlying cause of the failure or which initiate a process which leads to failure.
Severity
- The consequences of a failure mode. Severity considers the worst potential consequence of a failure, determined by the degree of injury, property damage, or system damage that could ultimately occur.
History
Procedures for conducting FMECA were described in US Armed Forces Military Procedures document MIL-P-1629(1949; revised in 1980 as MIL-STD-1629A). By the early 1960s, contractors for the U.S. National Aeronautics and Space Administration (NASA) were using variations of FMECA or FMEA under a variety of names. NASA programs using FMEA variants included Apollo, Viking
Viking program
The Viking program consisted of a pair of American space probes sent to Mars, Viking 1 and Viking 2. Each spacecraft was composed of two main parts, an orbiter designed to photograph the surface of Mars from orbit, and a lander designed to study the planet from the surface...
, Voyager
Voyager program
The Voyager program is a U.S program that launched two unmanned space missions, scientific probes Voyager 1 and Voyager 2. They were launched in 1977 to take advantage of a favorable planetary alignment of the late 1970s...
, Magellan
Magellan probe
The Magellan spacecraft, also referred to as the Venus Radar Mapper, was a 1,035-kilogram robotic space probe launched by NASA on May 4, 1989, to map the surface of Venus using Synthetic Aperture Radar and measure the planetary gravity...
, Galileo, and Skylab
Skylab
Skylab was a space station launched and operated by NASA, the space agency of the United States. Skylab orbited the Earth from 1973 to 1979, and included a workshop, a solar observatory, and other systems. It was launched unmanned by a modified Saturn V rocket, with a mass of...
. The civil aviation industry was an early adopter of FMEA, with the Society for Automotive Engineers
SAE International
SAE International is an organization for engineering professionals in the aerospace, automotive, and commercial vehicle industries. The Society is a standards development organization for the engineering of powered vehicles of all kinds, including cars, trucks, boats, aircraft, and others.SAE...
publishing ARP926 in 1967.
During the 1970's, use of FMEA and related techniques spread to other industries. In 1971 NASA prepared a report for the U.S. Geological Survey
United States Geological Survey
The United States Geological Survey is a scientific agency of the United States government. The scientists of the USGS study the landscape of the United States, its natural resources, and the natural hazards that threaten it. The organization has four major science disciplines, concerning biology,...
recommending the use of FMEA in assessment of offshore petroleum exploration. FMEA as application for HACCP on the Apollo Space Program moved into the food
Food
Food is any substance consumed to provide nutritional support for the body. It is usually of plant or animal origin, and contains essential nutrients, such as carbohydrates, fats, proteins, vitamins, or minerals...
industry in general. In the late 1970s the Ford Motor Company
Ford Motor Company
Ford Motor Company is an American multinational automaker based in Dearborn, Michigan, a suburb of Detroit. The automaker was founded by Henry Ford and incorporated on June 16, 1903. In addition to the Ford and Lincoln brands, Ford also owns a small stake in Mazda in Japan and Aston Martin in the UK...
introduced FMEA to the automotive industry for safety and regulatory consideration after the Pinto
Ford Pinto
The Ford Pinto is a subcompact car produced by the Ford Motor Company for the model years 1971–1980. The car's name derives from the Pinto horse. Initially offered as a two-door sedan, Ford offered "Runabout" hatchback and wagon models the following year, competing in the U.S. market with the AMC...
affair. They applied the same approach to processes (PFMEA) to consider potential process induced failures prior to launching production.
Although initially developed by the military, FMEA methodology is now extensively used in a variety of industries including semiconductor processing, food service, plastics, software, and healthcare. It is integrated into the Automotive Industry Action Group
Automotive Industry Action Group
Automotive Industry Action Group, also known as AIAG, is a not-for profit association based in Southfield, Michigan originally created to develop recommendations and a framework for the improvement of quality in the North American Automotive Industry....
's (AIAG) Advanced Product Quality Planning (APQP) process to provide risk mitigation, in both product and process development phases. Each potential cause must be considered for its effect on the product or process and, based on the risk, actions are determined and risks revisited after actions are complete. Toyota has taken this one step further with its Design Review Based on Failure Mode
Design Review Based on Failure Mode
Design Review Based on Failure Mode is a tool originally developed by the Toyota Motor Corporation. This tool was developed based on the philosophy that design problems occur when changes are made to existing engineering designs that have already been proven successful.-Methodology:DRBFM...
(DRBFM) approach. The method is now supported by the American Society for Quality
American Society for Quality
American Society for Quality , formerly known as American Society for Quality Control , is a knowledge-based global community of quality control experts, with nearly 85,000 members dedicated to the promotion and advancement of quality tools, principles, and practices in their workplaces and in...
which provides detailed guides on applying the method.
Implementation
In FMEA, failures are prioritized according to how serious their consequences are, how frequently they occur and how easily they can be detected. A FMEA also documents current knowledge and actions about the risks of failures for use in continuous improvement. FMEA is used during the design stage with an aim to avoid future failures (sometimes called DFMEA in that case). Later it is used for process control, before and during ongoing operation of the process. Ideally, FMEA begins during the earliest conceptual stages of design and continues throughout the life of the product or service.The outcomes of an FMEA development are actions to prevent or reduce the severity or likelihood of failures, starting with the highest-priority ones. It may be used to evaluate risk management
Risk management
Risk management is the identification, assessment, and prioritization of risks followed by coordinated and economical application of resources to minimize, monitor, and control the probability and/or impact of unfortunate events or to maximize the realization of opportunities...
priorities for mitigating known threat vulnerabilities. FMEA helps select remedial actions that reduce cumulative impacts of life-cycle consequences (risks) from a systems failure (fault).
It is used in many formal quality system
Quality management system
A quality management system can be expressed as the organizational structure, procedures, processes and resources needed to implement quality management.-Elements of a Quality Management System:# Organizational structure# Responsibilities# Methods...
s such as QS-9000 or ISO/TS 16949.
Using FMEA when designing
FMEA is intended to provide an analytical approach to reviewing potential failure modes and their associated causes. FMEA is a recognised tool to help to assess which risks have the greatest concern, and therefore which risks to address in order to prevent problems before they arise. The development of these specifications helps to ensure the product will meet the defined requirements and customer needsVoice of the customer
Voice of the customer is a term used in business and Information Technology to describe the in-depth process of capturing a customer's expectations, preferences and aversions...
.
The pre-work
The process for conducting an FMEA is typically developed in three main phases, in which appropriate actions need to be defined. Before starting with an FMEA, several other techniques are frequently employed to ensure that robustness and past history are included in the analysis.A robustness analysis can be obtained from interface matrices, boundary diagrams, and parameter diagrams. Failures are often found from external 'noise factors' and from shared interfaces with other parts and/or systems.
Typically, a description of the system and its function is developed, considering both intentional and unintentional uses.
A block diagram of the system is often created for inclusion with the FMEA, giving an overview of the major components or process steps and how they are related. These are called logical relations around which the FMEA can be developed.
The primary FME document or 'worksheet' lists all of the items or functions of the system in a logical manner, typically based on the block diagram.
Item / Function | Potential Failure mode | Potential Effects of Failure | S (severity rating) | Potential Cause(s) | O (occurrence rating) | Current controls | D (detection rating) | CRIT (critical characteristic | RPN (risk priority number) | Recommended actions | Responsibility and target completion date | Action taken | New S | New O | New D | New RPN |
---|---|---|---|---|---|---|---|---|---|---|---|---|---|---|---|---|
Fill tub | High level sensor never trips | Liquid spills on customer floor | 8 | level sensor failed level sensor disconnected |
2 | Fill timeout based on time to fill to low level sensor | 5 | N | 80 | Perform cost analysis of adding additional sensor halfway between low and high level sensors | Jane Doe 10-June-2011 |
NOTE: Above shown example format is not in line with mil.std 1629 or Civil Aerospace practise. The basic terms as given in first paragraph of this page are not available in this template!
Step 1: Occurrence
In this step it is necessary to look at the cause of a failure mode and the number of times it occurs. This can be done by looking at similar products or processes and the failure modes that have been documented for them in the past. A failure cause is looked upon as a design weakness. All the potential causes for a failure mode should be identified and documented. Again this should be in technical terms. Examples of causes are: erroneous algorithms, excessive voltage or improper operating conditions.A failure mode is given an occurrence ranking (O), again 1–10. Actions need to be determined if the occurrence is high (meaning > 4 for non-safety failure modes and > 1 when the severity-number from step 1 is 1 or 0). This step is called the detailed development section of the FMEA process. Occurrence also can be defined as %. If a non-safety issue happened less than 1%, we can give 1 to it. It is based on your product and customer specification.
Rating | Meaning |
---|---|
1 | No known occurrences on similar products or processes |
2/3 | Low (relatively few failures) |
4/5/6 | Moderate (occasional failures) |
7/8 | High (repeated failures) |
9/10 | Very high (failure is almost inevitable) |
Step 2: Severity
Determine all failure modes based on the functional requirements and their effects. Examples of failure modes are: Electrical short-circuiting, corrosion or deformation.A failure mode in one component can lead to a failure mode in another component, therefore each failure mode should be listed in technical terms and for function.
Hereafter the ultimate effect of each failure mode needs to be considered. A failure effect is defined as the result of a failure mode on the function of the system as perceived by the user. In this way it is convenient to write these effects down in terms of what the user might see or experience. Examples of failure effects are: degraded performance, noise or even injury to a user.
Each effect is given a severity number (S) from 1 (no danger) to 10 (critical). These numbers help an engineer to prioritize the failure modes and their effects. If the sensitivity of an effect has a number 9 or 10, actions are considered to change the design by eliminating the failure mode, if possible, or protecting the user from the effect. A severity rating of 9 or 10 is generally reserved for those effects which would cause injury to a user or otherwise result in litigation.
Rating | Meaning |
---|---|
1 | No effect |
2 | Very minor (only noticed by discriminating customers) |
3 | Minor (affects very little of the system, noticed by average customer) |
4/5/6 | Moderate (most customers are annoyed) |
7/8 | High (causes a loss of primary function; customers are dissatisfied) |
9/10 | Very high and hazardous (product becomes inoperative; customers angered; the failure may result unsafe operation and possible injury) |
Step 3: Detection
When appropriate actions are determined, it is necessary to test their efficiency. In addition, design verification is needed. The proper inspection methods need to be chosen. First, an engineer should look at the current controls of the system, that prevent failure modes from occurring or which detect the failure before it reaches the customer. Hereafter one should identify testing, analysis, monitoring and other techniques that can be or have been used on similar systems to detect failures. From these controls an engineer can learn how likely it is for a failure to be identified or detected. Each combination from the previous 2 steps receives a detection number (D). This ranks the ability of planned tests and inspections to remove defects or detect failure modes in time. The assigned detection number measures the risk that the failure will escape detection. A high detection number indicates that the chances are high that the failure will escape detection, or in other words, that the chances of detection are low.Rating | Meaning |
---|---|
1 | Certain - fault will be caught on test |
2 | Almost Certain |
3 | High |
4/5/6 | Moderate |
7/8 | Low |
9/10 | Fault will be passed to customer undetected |
After these three basic steps, risk priority numbers (RPN) are calculated
Risk priority number (RPN)
RPN play an important part in the choice of an action against failure modes. They are threshold values in the evaluation of these actions.After ranking the severity, occurrence and detectability the RPN can be easily calculated by multiplying these three numbers:
RPN = S × O × D
This has to be done for the entire process and/or design. Once this is done it is easy to determine the areas of greatest concern. The failure modes that have the highest RPN should be given the highest priority for corrective action.
This means it is not always the failure modes with the highest severity numbers that should be treated first. There could be less severe failures, but which occur more often and are less detectable.
After these values are allocated, recommended actions with targets, responsibility and dates of implementation are noted. These actions can include specific inspection, testing or quality procedures, redesign (such as selection of new components), adding more redundancy and limiting environmental stresses or operating range.
Once the actions have been implemented in the design/process, the new RPN should be checked, to confirm the improvements. These tests are often put in graphs, for easy visualization. Whenever a design or a process changes, an FMEA should be updated.
A few logical but important thoughts come in mind:
- Try to eliminate the failure mode (some failures are more preventable than others)
- Minimize the severity of the failure (severity of a failure cannot be changed)
- Reduce the occurrence of the failure mode
- Improve the detection
Timing of FMEA
The FMEA should be updated whenever:- A new cycle begins (new product/process)
- Changes are made to the operating conditions
- A change is made in the design
- New regulations are instituted
- Customer feedback indicates a problem
Uses of FMEA
- Development of system requirements that minimize the likelihood of failures.
- Development of methods to design and test systems to ensure that the failures have been eliminated.
- Evaluation of the requirements of the customer to ensure that those do not give rise to potential failures.
- Identification of certain design characteristics that contribute to failures, and minimize or eliminate those effects.
- Tracking and managing potential risks in the design. This helps avoid the same failures in future projects.
- Ensuring that any failure that could occur will not injure the customer or seriously impact a system.
- To produce world class quality products
Advantages
- Improve the quality, reliability and safety of a product/process
- Improve company image and competitiveness
- Increase user satisfaction
- Reduce system development timing and cost
- Collect information to reduce future failures, capture engineering knowledge
- Reduce the potential for warranty concerns
- Early identification and elimination of potential failure modes
- Emphasize problem prevention
- Minimize late changes and associated cost
- Catalyst for teamwork and idea exchange between functions
- Reduce the possibility of same kind of failure in future
- Reduce impact of profit margin company
- Reduce possible scrap in production
Limitations
Since FMEA is effectively dependent on the members of the committee which examines product failures, it is limited by their experience of previous failures. If a failure mode cannot be identified, then external help is needed from consultants who are aware of the many different types of product failure. FMEA is thus part of a larger system of quality controlQuality control
Quality control, or QC for short, is a process by which entities review the quality of all factors involved in production. This approach places an emphasis on three aspects:...
, where documentation is vital to implementation. General texts and detailed publications are available in forensic engineering
Forensic engineering
Forensic engineering is the investigation of materials, products, structures or components that fail or do not operate or function as intended, causing personal injury or damage to property. The consequences of failure are dealt with by the law of product liability. The field also deals with...
and failure analysis
Failure analysis
Failure analysis is the process of collecting and analyzing data to determine the cause of a failure. It is an important discipline in many branches of manufacturing industry, such as the electronics industry, where it is a vital tool used in the development of new products and for the improvement...
. It is a general requirement of many specific national and international standards that FMEA is used in evaluating product integrity.
If used as a top-down
Top-down and bottom-up design
Top–down and bottom–up are strategies of information processing and knowledge ordering, mostly involving software, but also other humanistic and scientific theories . In practice, they can be seen as a style of thinking and teaching...
tool, FMEA may only identify major failure modes in a system. Fault tree analysis
Fault tree analysis
Fault tree analysis is a top down, deductive failure analysis in which an undesired state of a system is analyzed using boolean logic to combine a series of lower-level events...
(FTA) is better suited for "top-down" analysis. When used as a "bottom-up" tool FMEA can augment or complement FTA and identify many more causes and failure modes resulting in top-level symptoms. It is not able to discover complex failure modes involving multiple failures within a subsystem, or to report expected failure intervals of particular failure modes up to the upper level subsystem or system.
Additionally, the multiplication of the severity, occurrence and detection rankings may result in rank reversals, where a less serious failure mode receives a higher RPN than a more serious failure mode. The reason for this is that the rankings are ordinal scale numbers, and multiplication is not defined for ordinal numbers. The ordinal rankings only say that one ranking is better or worse than another, but not by how much. For instance, a ranking of "2" may not be twice as bad as a ranking of "1," or an "8" may not be twice as bad as a "4," but multiplication treats them as though they are. See Level of measurement
Level of measurement
The "levels of measurement", or scales of measure are expressions that typically refer to the theory of scale types developed by the psychologist Stanley Smith Stevens. Stevens proposed his theory in a 1946 Science article titled "On the theory of scales of measurement"...
for further discussion.
Software
Most FMEAs are created as a spreadsheet. Specialized FMEA software packages exist that offer some advantages over spreadsheets.Types of FMEA
- Process: analysis of manufacturing and assembly processes
- Design: analysis of products prior to production
- Concept: analysis of systems or subsystems in the early design concept stages
- Equipment: analysis of machinery and equipment design before purchase
- Service: analysis of service industry processes before they are released to impact the customer
- System: analysis of the global system functions
- Software: analysis of the software functions
See also
- Failure mode, effects, and criticality analysis (FMECA)
- Causal layered analysisCausal layered analysisCausal layered analysis is one of several futures techniques used as a means to inquire into the causes of social phenomena and to generate a set of forecasts as to the future course of the phenomena....
- Futures techniquesFutures techniquesIn the multi-disciplinary field of futurology, futurologists use a diverse range of forecasting methods, including:- Delphi method :The Delphi method is a very popular technique used in Futures Studies. It was developed by Gordon and Helmer in 1953 at RAND...
- Failure modeFailure modeFailure causes are defects in design, process, quality, or part application, which are the underlying cause of a failure or which initiate a process which leads to failure. Where failure depends on the user of the product or process, then human error must be considered.-Component failure:A part...
- Failure rateFailure rateFailure rate is the frequency with which an engineered system or component fails, expressed for example in failures per hour. It is often denoted by the Greek letter λ and is important in reliability engineering....
- Forensic engineeringForensic engineeringForensic engineering is the investigation of materials, products, structures or components that fail or do not operate or function as intended, causing personal injury or damage to property. The consequences of failure are dealt with by the law of product liability. The field also deals with...
- High availabilityHigh availabilityHigh availability is a system design approach and associated service implementation that ensures a prearranged level of operational performance will be met during a contractual measurement period....
- Process decision program chartProcess decision program chartProcess Decision Program Chart is a technique designed to help prepare contingency plans. The emphasis of the PDPC is to identify the consequential impact of failure on activity plans, and create appropriate contingency plans to limit risks...
- Hazard Analysis and Critical Control Points
- Quality controlQuality controlQuality control, or QC for short, is a process by which entities review the quality of all factors involved in production. This approach places an emphasis on three aspects:...
- Reliability engineeringReliability engineeringReliability engineering is an engineering field, that deals with the study, evaluation, and life-cycle management of reliability: the ability of a system or component to perform its required functions under stated conditions for a specified period of time. It is often measured as a probability of...
- Risk assessmentRisk assessmentRisk assessment is a step in a risk management procedure. Risk assessment is the determination of quantitative or qualitative value of risk related to a concrete situation and a recognized threat...
- Safety engineeringSafety engineeringSafety engineering is an applied science strongly related to systems engineering / industrial engineering and the subset System Safety Engineering...
- Six sigmaSix SigmaSix Sigma is a business management strategy originally developed by Motorola, USA in 1986. , it is widely used in many sectors of industry.Six Sigma seeks to improve the quality of process outputs by identifying and removing the causes of defects and minimizing variability in manufacturing and...
- DRBFM
- Fault tree analysisFault tree analysisFault tree analysis is a top down, deductive failure analysis in which an undesired state of a system is analyzed using boolean logic to combine a series of lower-level events...
External links
- FMEA and FMECA Information
- FMEA Info Centre
- Failure Analysis of FMEA Article
- Expanded FMEA (EFMEA) Article
- Scenario-Based FMEA presentation (PDF)
- Difference between FMEA and Hazard Analysis
- FMEA - Failure Modes and Effects Analysis Presentation
- Institut pour la Maîtrise des Risques, method sheets, english version