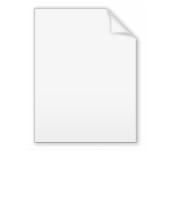
Ductile iron pipe
Encyclopedia
Ductile iron pipe is a pipe
commonly used for potable water distribution. The predominant wall material is ductile iron
, a spheroidized graphite cast iron
, although an internal cement mortar lining
usually serves to inhibit corrosion
from the fluid being distributed, and various types of external coating are used to inhibit corrosion from the environment. Ductile iron pipe is a direct development of earlier cast iron pipe
which it has superseded. Ductile iron has proven to be a better pipe material, being stronger and more fracture resistant; however, like most ferrous materials, it is susceptible to corrosion and retains some brittle characteristics. Relatively recent developments such as polyethylene
sleeving and/or zinc and polymer coatings have done much to mitigate corrosion concerns, and a typical life expectancy is in excess of 75 years.
Pipe dimensions are standardised to the mutually incompatible AWWA C151 (U.S. Customary Units
) in the USA, ISO 2531 / EN 545/598 (metric
) in Europe, and AS/NZS 2280 (metric) in Australia and New Zealand. Although both metric, European and Australian are not compatible and pipes of identical nominal diameters
have quite different dimensions.
C-151
ISO
2531 and its descendent specifications EN
545 (potable water) and EN 598 (sewage). European pipes are sized to approximately match the internal diameter of the pipe, following internal lining, to the nominal diameter. ISO 2531 maintains dimensional compatibility with older German cast iron pipes. Older British pipes, however, which used the incompatible imperial standard, BS 78, require adapter pieces when connecting to newly installed pipe. Coincidentally, the British harmonization with European pipe standards occurred at approximately the same time as its transition to ductile iron, so almost all cast iron pipe is imperial and all ductile pipe is metric.
/NZS 2280, that is not compatible with European pipes even though the same nomenclature is used. Australia adopted at an early point the imperial British cast iron pipe standard BS 78, and when this was retired on British adoption of ISO 2531, rather than similarly harmonizing with Europe, Australia opted for a 'soft' conversion from imperial units to metric, published as AS/NSZ 2280, with the physical outer diameters remaining unchanged, allowing continuity of manufacture and backwards compatibility. Therefore the inner diameters of lined pipe differ widely from the nominal diameter, and hydraulic calculations require some knowledge of the pipe standard.
s are flat rings around the end of pipes which mate with an equivalent flange from another pipe, the two being held together by bolts usually passed through holes drilled through the flanges. A deformable gasket, usually elastomeric, placed between raised faces on the mating flanges provides the seal. Flanges are designed to a large number of specifications that differ because of dimensional variations in pipes sizes and pressure requirements, and because of independent standards development. In the U.S. flanges are either threaded or welded onto the pipe. In the European market flanges are usually welded on to the pipe. In the U.S. flanges are available in a standard 125 lb. bolt pattern as well as a 250 lb (and heavier) bolt pattern (steel bolt pattern). Both are usually rated at 250 psi (1,723.7 kPa). A flanged joint is rigid and can bear both tension and compression as well as a limited degree of shear
and bending
. It also can be dismantled after assembly. Due to the rigid nature of the joint and the risk of excessive bending moment being imposed, it is advised that flanged pipework is not buried.
Current flange standards used in the water industry are ANSI B16.1 in the USA, EN 1092 in Europe, and AS/NZS 4087 in Australia and New Zealand.
A large number of different socket and seals exist. The most modern is the 'push-joint' or 'slip-joint', whereby the socket and rubber seal is designed to allow the pipe spigot to be, after lubrication, simply pushed into the socket. Push joints remain proprietary designs. Also available are locking gasket systems. These locking gasket systems allow the pipe to be pushed together but do not allow the joint to come apart without using a special tool or torch on the gasket.
The earliest spigot and socket cast iron pipes were jointed by filling the socket with a mixture of water, sand, iron filings and sal-ammoniac (ammonium chloride
.) A gaskin ring was pushed into te socket round the spigot to contain the mixture which was pounded into the socket with a caulking tool and then pointed off. This took several weeks to set and produced a completely rigid joint. Such pipe systems are often to be seen in nineteenth century churches in the heating system.
is used; for sewage it is common to use sulfate resisting or high alumina cement.
Cement mortar linings have been found to dramatically reduce internal corrosion. A DIPRA survey has demonstrated that the Hazen-Williams factor of cement lining remains between 130 and 151 with only slight reduction with age.
. It was employed more widely in the U.S. in the late 1950s and first employed in the UK in 1965 and Australia in the mid-1960s.
Polyethylene sleeving comprises a loose sleeve of polyethylene sheet that completely wraps the pipe, including the bells of any joints. Sleeving inhibits corrosion by a number of mechanisms. It physically separates the pipe from soil particles, preventing direct galvanic corrosion. By providing an impermeable barrier to ground water, the sleeve also inhibits the diffusion of oxygen to the ductile iron surface and limits the availability of electrolytes that would accelerate corrosion. It provides a homogeneous environment along the pipe surface so that corrosion occurs evenly over the pipe. The sleeve also restricts the availability of nutrients which could support sulfate-reducing bacteria
, inhibiting microbially induced corrosion
. Sleeving is not designed to be completely water-tight but rather to greatly restrict the movement of water to and from the pipe surface. Water present beneath the sleeve and in contact with the pipe surface is rapidly deoxygenated and depleted of nutrients and forms a stable environment in which limited further corrosion occurs. An improperly installed sleeve that continues to allow the free flow of ground water is not effective in inhibiting corrosion.
Polyethylene sleeves are available in a number of materials. The most common contemporary compositions are linear low-density polyethylene film which requires an 8 mil or 200 µm thickness and high-density cross-laminated polyethylene film which requires only a 4 mil or 100 µm thickness. The latter may or may not be reinforced with a scrim layer.
Polyethylene sleeving does have limitations. In European practice, its use in the absence of additional zinc and epoxy protective coatings is discouraged where natural soil resistivity
is below 750 ohm/cm, where resistivity is below 1500 ohm/cm and where the pipe is installed at or below the water table
, where there are additional artificial soil contaminants or where there are stray currents. Because of the vulnerability of polyethylene to UV degradation, sleeving, or sleeved pipe should not be stored in sunlight, although carbon pigments included in the sleeving can provide some limited protection.
Polyethylene sleeving is standardised according to ISO 8180 internationally, AWWA C105 in the U.S., BS 6076 in the UK and AS 3680 and AS 3681 in Australia.
No current AWWA standards are available for bonded coatings (zinc, coal tar epoxy, tape-wrap systems as seen on steel pipe) for ductile iron pipe, DIPRA does not endorse bonded coatings, and AWWA M41 generally views them unfavourably, recommending they be used only in conjunction with cathodic protection
.
Pipe (material)
A pipe is a tubular section or hollow cylinder, usually but not necessarily of circular cross-section, used mainly to convey substances which can flow — liquids and gases , slurries, powders, masses of small solids...
commonly used for potable water distribution. The predominant wall material is ductile iron
Ductile iron
Ductile iron, also known as ductile cast iron, nodular cast iron, spheroidal graphite iron, spherulitic graphite cast iron and SG iron, is a type of cast iron invented in 1943 by Keith Millis...
, a spheroidized graphite cast iron
Cast iron
Cast iron is derived from pig iron, and while it usually refers to gray iron, it also identifies a large group of ferrous alloys which solidify with a eutectic. The color of a fractured surface can be used to identify an alloy. White cast iron is named after its white surface when fractured, due...
, although an internal cement mortar lining
Cement-mortar lined ductile iron pipe
Cement-mortar lined ductile iron pipe is a ductile iron pipe with cement lining on the inside surface, and is commonly used for water distribution....
usually serves to inhibit corrosion
Corrosion
Corrosion is the disintegration of an engineered material into its constituent atoms due to chemical reactions with its surroundings. In the most common use of the word, this means electrochemical oxidation of metals in reaction with an oxidant such as oxygen...
from the fluid being distributed, and various types of external coating are used to inhibit corrosion from the environment. Ductile iron pipe is a direct development of earlier cast iron pipe
Cast iron pipe
Cast iron pipe is a historical pipe which found widespread use as a pressure pipe for transmission of water, gas and sewage, and as a water drainage pipe, during the 19th and 20th centuries. It comprises predominantly a gray cast iron tube and was frequently used uncoated, although later...
which it has superseded. Ductile iron has proven to be a better pipe material, being stronger and more fracture resistant; however, like most ferrous materials, it is susceptible to corrosion and retains some brittle characteristics. Relatively recent developments such as polyethylene
Polyethylene
Polyethylene or polythene is the most widely used plastic, with an annual production of approximately 80 million metric tons...
sleeving and/or zinc and polymer coatings have done much to mitigate corrosion concerns, and a typical life expectancy is in excess of 75 years.
Dimensions
Ductile iron pipe is sized according to a dimensionless term known as the Pipe Size or Nominal Diameter (known by its French abbreviation, DN). This is roughly equivalent to the pipe's internal diameter in inches or millimeters. However, it is the external diameter of the pipe that is kept constant between changes in wall thickness, in order to maintain compatibility in joints and fittings. Consequently the internal diameter varies, sometimes significantly, from its nominal size. Nominal pipe sizes vary from 3 inches up to 64 inches, in increments of at least 1 inch, in the USA.Pipe dimensions are standardised to the mutually incompatible AWWA C151 (U.S. Customary Units
United States customary units
United States customary units are a system of measurements commonly used in the United States. Many U.S. units are virtually identical to their imperial counterparts, but the U.S. customary system developed from English units used in the British Empire before the system of imperial units was...
) in the USA, ISO 2531 / EN 545/598 (metric
Metric system
The metric system is an international decimalised system of measurement. France was first to adopt a metric system, in 1799, and a metric system is now the official system of measurement, used in almost every country in the world...
) in Europe, and AS/NZS 2280 (metric) in Australia and New Zealand. Although both metric, European and Australian are not compatible and pipes of identical nominal diameters
Nominal size
In manufacturing, a nominal size or trade size is a size "in name only" used for identification. The nominal size may not match any dimension of the product, but within the domain of that product the nominal size may correspond to a large number of highly standardized dimensions and tolerances.For...
have quite different dimensions.
North America
Pipe dimensions according to the American AWWAAmerican Water Works Association
American Water Works Association was established as an international non-profit professional organization dedicated to the improvement of water quality and supply. Founded in 1881, it claims a membership of around 56,000 members worldwide as of 2010.AWWA has become the largest organization of...
C-151
Pipe Size | Outside Diameter [in (mm)] |
---|---|
3 | 3.96 (100.584 mm) |
4 | 4.8 (121.92 mm) |
6 | 6.9 (175.26 mm) |
8 | 9.05 (229.87 mm) |
10 | 11.1 (281.94 mm) |
12 | 13.2 (335.28 mm) |
Pipe Size | Outside Diameter [in (mm)] |
---|---|
14 | 15.3 (388.62 mm) |
16 | 17.4 (441.96 mm) |
18 | 19.5 (495.3 mm) |
20 | 21.6 (548.64 mm) |
24 | 25.8 (655.32 mm) |
30 | 32 (812.8 mm) |
Europe
European pipe is standardized toISO
International Organization for Standardization
The International Organization for Standardization , widely known as ISO, is an international standard-setting body composed of representatives from various national standards organizations. Founded on February 23, 1947, the organization promulgates worldwide proprietary, industrial and commercial...
2531 and its descendent specifications EN
European Committee for Standardization
The European Committee for Standardization or Comité Européen de Normalisation , is a non-profit organisation whose mission is to foster the European economy in global trading, the welfare of European citizens and the environment by providing an efficient infrastructure to interested parties for...
545 (potable water) and EN 598 (sewage). European pipes are sized to approximately match the internal diameter of the pipe, following internal lining, to the nominal diameter. ISO 2531 maintains dimensional compatibility with older German cast iron pipes. Older British pipes, however, which used the incompatible imperial standard, BS 78, require adapter pieces when connecting to newly installed pipe. Coincidentally, the British harmonization with European pipe standards occurred at approximately the same time as its transition to ductile iron, so almost all cast iron pipe is imperial and all ductile pipe is metric.
DN | Outside Diameter [mm (in)] |
Wall thickness [mm (in)] |
||
---|---|---|---|---|
Class 40 | K9 | K10 | ||
40 | 56 (2.205 in) | 4.8 (0.188976377952756 in) | 6 (0.236220472440945 in) | 6 (0.236220472440945 in) |
50 | 66 (2.598 in) | 4.8 (0.188976377952756 in) | 6 (0.236220472440945 in) | 6 (0.236220472440945 in) |
60 | 77 (3.031 in) | 4.8 (0.188976377952756 in) | 6 (0.236220472440945 in) | 6 (0.236220472440945 in) |
65 | 82 (3.228 in) | 4.8 (0.188976377952756 in) | 6 (0.236220472440945 in) | 6 (0.236220472440945 in) |
80 | 98 (3.858 in) | 4.8 (0.188976377952756 in) | 6 (0.236220472440945 in) | 6 (0.236220472440945 in) |
100 | 118 (4.646 in) | 4.8 (0.188976377952756 in) | 6 (0.236220472440945 in) | 6 (0.236220472440945 in) |
125 | 144 (5.669 in) | 4.8 (0.188976377952756 in) | 6 (0.236220472440945 in) | 6 (0.236220472440945 in) |
150 | 170 (6.693 in) | 5 (0.196850393700787 in) | 6 (0.236220472440945 in) | 6.5 (0.255905511811024 in) |
200 | 222 (8.74 in) | 8.4 (0.330708661417323 in) | 6.3 (0.248031496062992 in) | 7 (0.275590551181102 in) |
250 | 274 (10.787 in) | 5.8 (0.228346456692913 in) | 6.8 (0.267716535433071 in) | 7.5 (0.295275590551181 in) |
300 | 326 (12.835 in) | 6.2 (0.244094488188976 in) | 7.2 (0.283464566929134 in) | 8 (0.31496062992126 in) |
350 | 378 (14.882 in) | 7 (0.275590551181102 in) | 7.7 (0.303149606299213 in) | 8.5 (0.334645669291339 in) |
400 | 429 (16.89 in) | 7.8 (0.307086614173228 in) | 8.1 (0.318897637795276 in) | 9 (0.354330708661417 in) |
450 | 480 (18.898 in) | - | 8.6 (0.338582677165354 in) | 9.5 (0.374015748031496 in) |
DN | Outside Diameter [mm (in)] |
Wall thickness [mm (in)] |
||
---|---|---|---|---|
Class 40 | K9 | K10 | ||
500 | 532 (20.945 in) | - | 9 (0.354330708661417 in) | 10 (0.393700787401575 in) |
600 | 635 (25 in) | - | 9.9 (0.389763779527559 in) | 11.1 (0.437007874015748 in) |
700 | 738 (29.055 in) | - | 10.9 (0.429133858267717 in) | 12 (0.47244094488189 in) |
800 | 842 (33.15 in) | - | 11.7 (0.460629921259843 in) | 13 (0.511811023622047 in) |
900 | 945 (37.205 in) | - | 12.9 (0.507874015748031 in) | 14.1 (0.55511811023622 in) |
1000 | 1048 (41.26 in) | - | 13.5 (0.531496062992126 in) | 15 (0.590551181102362 in) |
1100 | 1152 (45.354 in) | - | 14.4 (0.566929133858268 in) | 16 (0.62992125984252 in) |
1200 | 1255 (49.409 in) | - | 15.3 (0.602362204724409 in) | 17 (0.669291338582677 in) |
1400 | 1462 (57.559 in) | - | 17.1 (0.673228346456693 in) | 19 (0.748031496062992 in) |
1500 | 1565 (61.614 in) | - | 18 (0.708661417322835 in) | 20 (0.78740157480315 in) |
1600 | 1668 (65.669 in) | - | 18.9 (0.744094488188976 in) | 51 (2.008 in) |
1800 | 1875 (73.819 in) | - | 20.7 (0.81496062992126 in) | 23 (0.905511811023622 in) |
2000 | 2082 (81.969 in) | - | 22.5 (0.885826771653543 in) | 25 (0.984251968503937 in) |
Australia
Australian and New Zealand pipes are sized to an independent specification, ASStandards Australia
Standards Australia was established in 1922 and is recognised through a Memorandum of Understanding with the Australian government as the peak non-government standards development body in Australia. It is a company limited by guarantee, with 72 members representing groups interested in the...
/NZS 2280, that is not compatible with European pipes even though the same nomenclature is used. Australia adopted at an early point the imperial British cast iron pipe standard BS 78, and when this was retired on British adoption of ISO 2531, rather than similarly harmonizing with Europe, Australia opted for a 'soft' conversion from imperial units to metric, published as AS/NSZ 2280, with the physical outer diameters remaining unchanged, allowing continuity of manufacture and backwards compatibility. Therefore the inner diameters of lined pipe differ widely from the nominal diameter, and hydraulic calculations require some knowledge of the pipe standard.
Nominal Size (DN) | Outside Diameter [mm (in)] |
Nominal Wall Thickness [mm (in)] |
Flange Class | |
---|---|---|---|---|
PN 20 | PN 35 | |||
100 | 122 (4.803 in) | - | 5 (0.196850393700787 in) | 7.0 |
150 | 177 (6.969 in) | - | 5 (0.196850393700787 in) | 8.0 |
200 | 232 (9.134 in) | - | 5 (0.196850393700787 in) | 8.0 |
225 | 259 (10.197 in) | 5 (0.196850393700787 in) | 5.2 (0.204724409448819 in) | 9.0 |
250 | 286 (11.26 in) | 5 (0.196850393700787 in) | 5.6 (0.220472440944882 in) | 9.0 |
300 | 345 (13.583 in) | 5 (0.196850393700787 in) | 6.3 (0.248031496062992 in) | 10.0 |
Nominal Size (DN) | Outside Diameter [mm (in)] |
Nominal Wall Thickness [mm (in)] |
Flange Class | |
---|---|---|---|---|
PN 20 | PN 35 | |||
375 | 426 (16.772 in) | 5.1 (0.200787401574803 in) | 7.3 (0.28740157480315 in) | 10.0 |
450 | 507 (19.961 in) | 5.6 (0.220472440944882 in) | 8.3 (0.326771653543307 in) | 11.0 |
500 | 560 (22.047 in) | 6 (0.236220472440945 in) | 9 (0.354330708661417 in) | 12.0 |
600 | 667 (26.26 in) | 6.8 (0.267716535433071 in) | 310.3 (0.405511811023622 in) | 13.0 |
750 | 826 (32.52 in) | 7.9 (0.311023622047244 in) | 12.2 (0.480314960629921 in) | 15.0 |
Joints
Individual lengths of ductile iron pipe are joined either by flanges, couplings, or some form of spigot and socket arrangement.Flanges
FlangeFlange
A flange is an external or internal ridge, or rim , for strength, as the flange of an iron beam such as an I-beam or a T-beam; or for attachment to another object, as the flange on the end of a pipe, steam cylinder, etc., or on the lens mount of a camera; or for a flange of a rail car or tram wheel...
s are flat rings around the end of pipes which mate with an equivalent flange from another pipe, the two being held together by bolts usually passed through holes drilled through the flanges. A deformable gasket, usually elastomeric, placed between raised faces on the mating flanges provides the seal. Flanges are designed to a large number of specifications that differ because of dimensional variations in pipes sizes and pressure requirements, and because of independent standards development. In the U.S. flanges are either threaded or welded onto the pipe. In the European market flanges are usually welded on to the pipe. In the U.S. flanges are available in a standard 125 lb. bolt pattern as well as a 250 lb (and heavier) bolt pattern (steel bolt pattern). Both are usually rated at 250 psi (1,723.7 kPa). A flanged joint is rigid and can bear both tension and compression as well as a limited degree of shear
Shear stress
A shear stress, denoted \tau\, , is defined as the component of stress coplanar with a material cross section. Shear stress arises from the force vector component parallel to the cross section...
and bending
Bending
In engineering mechanics, bending characterizes the behavior of a slender structural element subjected to an external load applied perpendicularly to a longitudinal axis of the element. The structural element is assumed to be such that at least one of its dimensions is a small fraction, typically...
. It also can be dismantled after assembly. Due to the rigid nature of the joint and the risk of excessive bending moment being imposed, it is advised that flanged pipework is not buried.
Current flange standards used in the water industry are ANSI B16.1 in the USA, EN 1092 in Europe, and AS/NZS 4087 in Australia and New Zealand.
Spigot and socket
Spigot and sockets involve a normal pipe end, the spigot, being inserted into the socket or bell of another pipe or fitting with a seal being made between the two within the socket. Normal spigot and socket joints do not allow direct metal to metal contact with all forces being transmitted through the elastomeric seal. They can consequently flex and allow some degree of rotation, allowing pipes to shift and relieve stresses imposed by soil movement. The corollary is that unrestrained spigot and socket joints transmit essentially no compression or tension along the axis of the pipe and little shear. Any bends, tees or valves therefore require either a restrained joint or, more commonly, thrust blocks, which transmit the forces as compression into the surrounding soil.A large number of different socket and seals exist. The most modern is the 'push-joint' or 'slip-joint', whereby the socket and rubber seal is designed to allow the pipe spigot to be, after lubrication, simply pushed into the socket. Push joints remain proprietary designs. Also available are locking gasket systems. These locking gasket systems allow the pipe to be pushed together but do not allow the joint to come apart without using a special tool or torch on the gasket.
The earliest spigot and socket cast iron pipes were jointed by filling the socket with a mixture of water, sand, iron filings and sal-ammoniac (ammonium chloride
Ammonium chloride
Ammonium chloride NH4Cl is an inorganic compound with the formula NH4Cl. It is a white crystalline salt that is highly soluble in water. Solutions of ammonium chloride are mildly acidic. Sal ammoniac is a name of natural, mineralogical form of ammonium chloride...
.) A gaskin ring was pushed into te socket round the spigot to contain the mixture which was pounded into the socket with a caulking tool and then pointed off. This took several weeks to set and produced a completely rigid joint. Such pipe systems are often to be seen in nineteenth century churches in the heating system.
Manufacture
Ductile iron pipe is produced by a technique known as centrifugal casting, originally developed for cast iron pipe in 1918. The molten ductile iron is poured into a rapidly spinning water-cooled mold. Centrifugal force results in an even spread of iron around the circumference.Internal coatings
Ductile iron pipe is somewhat resistant to internal corrosion in potable water and less aggressive forms of sewage. However, even where pipe material loss and consequently pipe wall reduction is slow, the deposition of corrosion products on the internal pipe wall can dramatically reduce the effective internal diameter and effectively choke flow, increasing pumping costs and lowering system pressure, long before the pipe itself is at risk of failure. A variety of linings are available to reduce or eliminate corrosion, including cement mortar, polyurethane and polyethylene. Of these, cement mortar lining is by far the most common.Cement mortar
The predominant form of lining for water applications is cement mortar centrifugally applied during manufacturing. The cement mortar comprises a mixture of cement and sand to a ratio of between 1:2 and 1:3.5. For potable water, portland cementPortland cement
Portland cement is the most common type of cement in general use around the world because it is a basic ingredient of concrete, mortar, stucco and most non-specialty grout...
is used; for sewage it is common to use sulfate resisting or high alumina cement.
Cement mortar linings have been found to dramatically reduce internal corrosion. A DIPRA survey has demonstrated that the Hazen-Williams factor of cement lining remains between 130 and 151 with only slight reduction with age.
External coatings
Unprotected ductile iron, similarly to cast iron, is intrinsically resistant to corrosion in most, although not all, soils. Nonetheless, because of frequent lack of information on soil aggressiveness and to extend the installed life of buried pipe, ductile iron pipe is commonly protected by one or more external coatings. In the U.S. and Australia, loose polyethylene sleeving is preferred. In Europe, standards recommend a more sophisticated system of directly bonded zinc coatings overlaid by a finishing layer be used in conjunction with polyethylene sleeving.Polyethylene
Polyethylene sleeving was first developed by CIPRA (since 1979, DIPRA) in the U.S. in 1951 for use in highly corrosive soil in Birmingham, AlabamaBirmingham, Alabama
Birmingham is the largest city in Alabama. The city is the county seat of Jefferson County. According to the 2010 United States Census, Birmingham had a population of 212,237. The Birmingham-Hoover Metropolitan Area, in estimate by the U.S...
. It was employed more widely in the U.S. in the late 1950s and first employed in the UK in 1965 and Australia in the mid-1960s.
Polyethylene sleeving comprises a loose sleeve of polyethylene sheet that completely wraps the pipe, including the bells of any joints. Sleeving inhibits corrosion by a number of mechanisms. It physically separates the pipe from soil particles, preventing direct galvanic corrosion. By providing an impermeable barrier to ground water, the sleeve also inhibits the diffusion of oxygen to the ductile iron surface and limits the availability of electrolytes that would accelerate corrosion. It provides a homogeneous environment along the pipe surface so that corrosion occurs evenly over the pipe. The sleeve also restricts the availability of nutrients which could support sulfate-reducing bacteria
Sulfate-reducing bacteria
Sulfate-reducing bacteria are those bacteria and archaea that can obtain energy by oxidizing organic compounds or molecular hydrogen while reducing sulfate to hydrogen sulfide...
, inhibiting microbially induced corrosion
Microbial corrosion
Microbial corrosion, also called bacterial corrosion, bio-corrosion, microbiologically-influenced corrosion, or microbially-induced corrosion , is corrosion caused or promoted by microorganisms, usually chemoautotrophs...
. Sleeving is not designed to be completely water-tight but rather to greatly restrict the movement of water to and from the pipe surface. Water present beneath the sleeve and in contact with the pipe surface is rapidly deoxygenated and depleted of nutrients and forms a stable environment in which limited further corrosion occurs. An improperly installed sleeve that continues to allow the free flow of ground water is not effective in inhibiting corrosion.
Polyethylene sleeves are available in a number of materials. The most common contemporary compositions are linear low-density polyethylene film which requires an 8 mil or 200 µm thickness and high-density cross-laminated polyethylene film which requires only a 4 mil or 100 µm thickness. The latter may or may not be reinforced with a scrim layer.
Polyethylene sleeving does have limitations. In European practice, its use in the absence of additional zinc and epoxy protective coatings is discouraged where natural soil resistivity
Resistivity
Electrical resistivity is a measure of how strongly a material opposes the flow of electric current. A low resistivity indicates a material that readily allows the movement of electric charge. The SI unit of electrical resistivity is the ohm metre...
is below 750 ohm/cm, where resistivity is below 1500 ohm/cm and where the pipe is installed at or below the water table
Water table
The water table is the level at which the submarine pressure is far from atmospheric pressure. It may be conveniently visualized as the 'surface' of the subsurface materials that are saturated with groundwater in a given vicinity. However, saturated conditions may extend above the water table as...
, where there are additional artificial soil contaminants or where there are stray currents. Because of the vulnerability of polyethylene to UV degradation, sleeving, or sleeved pipe should not be stored in sunlight, although carbon pigments included in the sleeving can provide some limited protection.
Polyethylene sleeving is standardised according to ISO 8180 internationally, AWWA C105 in the U.S., BS 6076 in the UK and AS 3680 and AS 3681 in Australia.
Zinc
In Europe, ductile iron pipe is typically manufactured with a zinc coating overlaid by either a bituminous, polymer, or epoxy finishing layer. EN 545/598 mandates a minimum zinc content of 200 g/m2 (with local minima of 110 g/m2 at 99.99% purity) and a minimum average finishing layer thickness of 70 µm (with local minima of 50 µm).No current AWWA standards are available for bonded coatings (zinc, coal tar epoxy, tape-wrap systems as seen on steel pipe) for ductile iron pipe, DIPRA does not endorse bonded coatings, and AWWA M41 generally views them unfavourably, recommending they be used only in conjunction with cathodic protection
Cathodic protection
Cathodic protection is a technique used to control the corrosion of a metal surface by making it the cathode of an electrochemical cell. The simplest method to apply CP is by connecting the metal to be protected with another more easily corroded "sacrificial metal" to act as the anode of the...
.