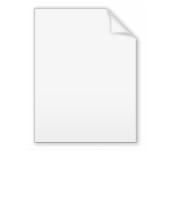
Continuous variable valve timing
Encyclopedia
Continuous variable valve timing offers a unique ability to have independent control of the intake and exhaust valves in an internal combustion engine
. For any engine load criteria, the timing of intake and exhaust can be independently programmed . The main variations of valve timing are: Late intake valve closing, Early Intake valve closing, Early Intake valve opening and early exhaust valve closing. These variations exist on a spectrum, which means engine performance could be optimized under all conditions . Variable Valve Timing has existed since Alfa Romeo implemented it in 1980. The technology took a big step forward with Honda’s VTEC
system in 1987, which consists of two unique cam profiles for each intake/exhaust valve. The engine can then “decide” based on driving conditions which one to use to maximize performance. This certainly allows a greater degree of control over the engine with obvious performance benefits. However, if valve timing could be controlled independent of crankshaft rotation, then a near infinite number of valve timing scenarios could be accommodated which would dramatically improve fuel economy and emission levels of an automobile.
s are designed to optimize efficiency and performance, while minimizing emissions, under a wide variety of driving conditions. The way this is traditionally accomplished is relatively simple: the driver controls the volume of air allowed into the engine by way of a throttle plate linked to the gas pedal. Electronic sensors in the intake stream measure the intake air volume and temperature, and the Powertrain Control Module
(PCM) determines the required fuel amount, as well as the appropriate spark timing to allow the air/fuel mixture to burn optimally and maximize output. Generally, fuel volume and spark timing are pulled off a fuel map – a computer program which looks at various inputs from engine sensors. The intake and exhaust valves are fixed, meaning they are driven by the engine crankshaft, and they open and close at set intervals during the rotational cycle, independent of engine load conditions. When an engine is designed, the inherent inflexibility in the timing of the valve events results in a compromise. Simply, engineers must design the engine to run optimally under a wide variety of driving conditions, but perfectly under none. During most driving, the engine is operating at part load and fuel economy is the priority. At part load, the air-fuel ratio
is kept stoichiometric to enable efficient operation of the catalytic converter
” .
One of the major inefficiencies of the Internal Combustion Engine is the loss of rotational energy caused by the intake stroke. As the piston travels downward during the intake stroke, air is drawn into the cylinder via engine vacuum. The pressure is below atmospheric, which means the engine has to do work to take in the air – at the expense of volumetric efficiency. “These pumping losses depend on the opening and closing of the throttle valve. The losses are high when the throttle valve tends to close and are low at wide open throttle. Thus the pumping losses are inversely proportional with engine load” . If intake air volume were to be controlled by the valvetrain, rather than a throttle plate, the pumping losses could be reduced. “The inlet-valve timing is the most important parameter for optimizing the engine volumetric efficiency, whereas the exhaust-valve timing controls the RGF which reduces exhaust NO emissions. For the engine to operate efficiently and effectively over its entire operating range and conditions, the valve event should be able to vary with speed and load anywhere on the engine map” .
Debuted in the BMW 316ti Compact in 2001, Valvetronic was the first continuous variable valve lift mechanism made into production. The goal of Valvetronic was to reduce fuel consumption, rather than to maximize power. Valvetronic regulates engine output by varying the depth of valve lift according to the position of throttle pedal. This means the conventional throttle butterfly can be disabled which reduces pumping loss. BMW achieved 10% reduction in fuel consumption with Valvetronic . BMW’s Valvetronic adds an electric motor, an eccentric shaft and an intermediate rocker arm at each intake valve. The intake camshaft acts on the intermediate rocker arms through roller bearings. When the driver calls for more power, the electric motor turns the eccentric shaft, which pushes the intermediate rocker arms and in turn pushes the valve to open deeper.
Nissan introduced its Variable Valve Event and Lift (VVEL) in 2007 as the world's second CVVL system. The first application was on the VQ37VHR V6 engine of Skyline Coupe (Infiniti G37). Nissan's system is more compact than BMW’s, involve less parts and energy loss, and is therefore more adaptable to high-performance engines . The VVEL does not use a conventional intake camshaft. Each valve is actuated by a cam which is pivoted on - but not fixed to - the camshaft. While conventional camshafts feature fixed rotating lobes, the cam in VVEL swings up and down; this is why it does not need a symmetric profile. Its movement is driven by the camshaft via a series of component. VVEL varies valve lift by the eccentric control shaft inside the rocker arm. By rotating the eccentric control shaft, the position of rocker arm is shifted, changing the swing angle of cam. The swing angle of cam determines the degree of valve lift .
Toyota introduced its Valvematic technology in 2008. Valvematic employs an intermediate shaft to achieve continuous variable valve lift. The intermediate shaft has an actuating member for each cylinder . Each actuating member is made of two finger followers on either side of a roller bearing member. The followers can rotate in relation to the roller member by means of internal gear threads and an electric motor attached to the end of the intermediate shaft. The gear threads of the roller member and finger followers are in opposing directions. This means when the shaft swivels, the roller member and finger followers will move in opposing directions, moving either apart or closer together. In this way, the axle angle between them can be varied infinitely by the electric motor. The intake valve is actuated by camshaft via the intermediate shaft . Specifically, the camshaft acts on the roller member of intermediate shaft, transferring the movement to both finger followers, then towards the roller rocker arms and ultimately to the intake valves. When the angle of the finger followers is narrow with respect to the roller member, valve lift is low. As the angle increases, so does valve lift. In this way, Valvematic can vary valve lift by adjusting the angle of the finger followers in relation to the roller bearing member.
Internal combustion engine
The internal combustion engine is an engine in which the combustion of a fuel occurs with an oxidizer in a combustion chamber. In an internal combustion engine, the expansion of the high-temperature and high -pressure gases produced by combustion apply direct force to some component of the engine...
. For any engine load criteria, the timing of intake and exhaust can be independently programmed . The main variations of valve timing are: Late intake valve closing, Early Intake valve closing, Early Intake valve opening and early exhaust valve closing. These variations exist on a spectrum, which means engine performance could be optimized under all conditions . Variable Valve Timing has existed since Alfa Romeo implemented it in 1980. The technology took a big step forward with Honda’s VTEC
VTEC
VTEC is a valvetrain system developed by Honda to improve the volumetric efficiency of a four-stroke internal combustion engine. The VTEC system uses two camshaft profiles and electronically selects between the profiles. It was invented by Honda R&D engineer Ikuo Kajitani, and was the first system...
system in 1987, which consists of two unique cam profiles for each intake/exhaust valve. The engine can then “decide” based on driving conditions which one to use to maximize performance. This certainly allows a greater degree of control over the engine with obvious performance benefits. However, if valve timing could be controlled independent of crankshaft rotation, then a near infinite number of valve timing scenarios could be accommodated which would dramatically improve fuel economy and emission levels of an automobile.
Traditional internal combustion engines
Traditional Internal Combustion EngineInternal combustion engine
The internal combustion engine is an engine in which the combustion of a fuel occurs with an oxidizer in a combustion chamber. In an internal combustion engine, the expansion of the high-temperature and high -pressure gases produced by combustion apply direct force to some component of the engine...
s are designed to optimize efficiency and performance, while minimizing emissions, under a wide variety of driving conditions. The way this is traditionally accomplished is relatively simple: the driver controls the volume of air allowed into the engine by way of a throttle plate linked to the gas pedal. Electronic sensors in the intake stream measure the intake air volume and temperature, and the Powertrain Control Module
Powertrain Control Module
A Powertrain Control Module, abbreviated PCM, is an automotive component, an electronic control unit , used on motor vehicles. It is generally a combined control unit, consisting of the engine control unit and the transmission control unit. It commonly controls more than 5 factors in the car or...
(PCM) determines the required fuel amount, as well as the appropriate spark timing to allow the air/fuel mixture to burn optimally and maximize output. Generally, fuel volume and spark timing are pulled off a fuel map – a computer program which looks at various inputs from engine sensors. The intake and exhaust valves are fixed, meaning they are driven by the engine crankshaft, and they open and close at set intervals during the rotational cycle, independent of engine load conditions. When an engine is designed, the inherent inflexibility in the timing of the valve events results in a compromise. Simply, engineers must design the engine to run optimally under a wide variety of driving conditions, but perfectly under none. During most driving, the engine is operating at part load and fuel economy is the priority. At part load, the air-fuel ratio
Air-fuel ratio
Air–fuel ratio is the mass ratio of air to fuel present in an internal combustion engine. If exactly enough air is provided to completely burn all of the fuel, the ratio is known as the stoichiometric mixture, often abbreviated to stoich...
is kept stoichiometric to enable efficient operation of the catalytic converter
Catalytic converter
A catalytic converter is a device used to convert toxic exhaust emissions from an internal combustion engine into non-toxic substances. Inside a catalytic converter, a catalyst stimulates a chemical reaction in which noxious byproducts of combustion are converted to less toxic substances by dint...
” .
One of the major inefficiencies of the Internal Combustion Engine is the loss of rotational energy caused by the intake stroke. As the piston travels downward during the intake stroke, air is drawn into the cylinder via engine vacuum. The pressure is below atmospheric, which means the engine has to do work to take in the air – at the expense of volumetric efficiency. “These pumping losses depend on the opening and closing of the throttle valve. The losses are high when the throttle valve tends to close and are low at wide open throttle. Thus the pumping losses are inversely proportional with engine load” . If intake air volume were to be controlled by the valvetrain, rather than a throttle plate, the pumping losses could be reduced. “The inlet-valve timing is the most important parameter for optimizing the engine volumetric efficiency, whereas the exhaust-valve timing controls the RGF which reduces exhaust NO emissions. For the engine to operate efficiently and effectively over its entire operating range and conditions, the valve event should be able to vary with speed and load anywhere on the engine map” .
Late intake valve closing
The first variation of continuous variable valve timing involves holding the intake valve open slightly longer than a traditional engine. This results in the piston actually pushing air out of the cylinder and back into the intake manifold during the compression stroke. The air which is expelled fills the manifold with higher pressure, and on subsequent intake strokes the air which is taken in is at a higher pressure. Late intake valve closing has shown to reduce pumping losses by 40% during partial load conditions, as well as decreasing NO emissions by 24%. Peak engine torque showed only a 1% decline, and Hydrocarbon emissions were unchanged .Early intake valve closing
Another way to decrease the pumping losses associated with low engine speed, high vacuum conditions is by closing the intake valve earlier than normal. This involves closing the intake valve midway through the intake stroke. Air/fuel demands are so low at low-load conditions and the work required to fill the cylinder is relatively high, so Early intake valve closing greatly reduces pumping losses . Studies have shown early intake valve closing to reduce pumping losses by 40%, as well as to increase fuel economy by 7%. It also has reduced NO emissions by 24% at partial load conditions. A possible downside to early intake valve closing is that it significantly lowers the temperature of the combustion chamber, which can increase hydrocarbon emissions .Early intake valve opening
Early intake valve opening is another variation that has significant potential to reduce emissions. In a traditional engine, a process called valve overlap is used to aid in controlling the cylinder temperature. By opening the intake valve early, some of the inert/combusted exhaust gas will back flow out of the cylinder, via the intake valve, where it cools momentarily in the intake manifold. This inert gas then fills the cylinder in the subsequent intake stroke, which aids in controlling the temperature of the cylinder and NO emissions. It also improves volumetric efficiency, because there is less exhaust gas to be expelled on the exhaust stroke .Early/late exhaust valve closing
Early and late exhaust valve closing can also reduce emissions. Traditionally, the exhaust valve opens, and exhaust gas is pushed out of the cylinder and into the exhaust manifold by the piston as it travels upward. By manipulating the timing of the exhaust valve, engineers can control how much exhaust gas is left in the cylinder. By holding the exhaust valve open slightly longer, the cylinder is more emptied and ready to be filled with a bigger air/fuel charge on the intake stroke. By closing the valve slightly early, more exhaust gas remains in the cylinder which increases fuel efficiency. This allows for more efficient operation under all conditions.Drawbacks
The main factor preventing this technology from wide use in production automobiles is the ability to produce a cost effective means of controlling the valve timing under the conditions internal to an engine. An engine cruising at 70 mi/h will be doing approximately 3000 revolutions per minute. Every second, the crankshaft rotates 50 times, so the valve timing events have to occur at precise times to offer performance benefits. Problems which need to be overcome before this technology becomes widespread include “dynamic performance in the high engine speed range, power consumption, long term durability and repeatability” . Electromagnetic valve actuators offer the greatest control of precise valve timing, but are not cost effective for production vehicles at this time. Currently, automakers use a variety of different mechanical techniques to continuously vary valve timing.Cam Phasing Variable Valve Timing
Cam-phasing VVT is the simplest, cheapest and most commonly used mechanism at this time. This system varies the valve timing by shifting the phase angle of the camshafts. For example, at high engine speeds, the intake camshaft will be rotated to advance the intake valve timing. This movement is controlled by the engine management system according to need, and actuated by hydraulic cam gears. It is important to note that cam-phasing variable valve timing cannot vary the duration of valve opening. It simply allows earlier or later valve opening. Earlier opening results in earlier closing, of course. It also cannot vary the valve lift. Cam-phasing variable valve timing is the simplest and cheapest method because each camshaft needs only one hydraulic actuator, unlike other systems that employ individual mechanism for every cylinder. “The greatest degree of variability in the valvetrain is achieved when each individual valve has its own timing system, enabling it to be opened and closed as and when required” . Obviously, actuating each valve individually offers the most precise control over the valve timing, but the cost is often prohibitive.Applications
Automakers have been testing this technology for years, as its benefits are obvious. Several automakers have begun implementing this technology in recent years, but its widespread use is still to come. Several automakers, including BMW, Nissan, and Toyota currently offer models with some form of continuous variable valve timing.Debuted in the BMW 316ti Compact in 2001, Valvetronic was the first continuous variable valve lift mechanism made into production. The goal of Valvetronic was to reduce fuel consumption, rather than to maximize power. Valvetronic regulates engine output by varying the depth of valve lift according to the position of throttle pedal. This means the conventional throttle butterfly can be disabled which reduces pumping loss. BMW achieved 10% reduction in fuel consumption with Valvetronic . BMW’s Valvetronic adds an electric motor, an eccentric shaft and an intermediate rocker arm at each intake valve. The intake camshaft acts on the intermediate rocker arms through roller bearings. When the driver calls for more power, the electric motor turns the eccentric shaft, which pushes the intermediate rocker arms and in turn pushes the valve to open deeper.
Nissan introduced its Variable Valve Event and Lift (VVEL) in 2007 as the world's second CVVL system. The first application was on the VQ37VHR V6 engine of Skyline Coupe (Infiniti G37). Nissan's system is more compact than BMW’s, involve less parts and energy loss, and is therefore more adaptable to high-performance engines . The VVEL does not use a conventional intake camshaft. Each valve is actuated by a cam which is pivoted on - but not fixed to - the camshaft. While conventional camshafts feature fixed rotating lobes, the cam in VVEL swings up and down; this is why it does not need a symmetric profile. Its movement is driven by the camshaft via a series of component. VVEL varies valve lift by the eccentric control shaft inside the rocker arm. By rotating the eccentric control shaft, the position of rocker arm is shifted, changing the swing angle of cam. The swing angle of cam determines the degree of valve lift .
Toyota introduced its Valvematic technology in 2008. Valvematic employs an intermediate shaft to achieve continuous variable valve lift. The intermediate shaft has an actuating member for each cylinder . Each actuating member is made of two finger followers on either side of a roller bearing member. The followers can rotate in relation to the roller member by means of internal gear threads and an electric motor attached to the end of the intermediate shaft. The gear threads of the roller member and finger followers are in opposing directions. This means when the shaft swivels, the roller member and finger followers will move in opposing directions, moving either apart or closer together. In this way, the axle angle between them can be varied infinitely by the electric motor. The intake valve is actuated by camshaft via the intermediate shaft . Specifically, the camshaft acts on the roller member of intermediate shaft, transferring the movement to both finger followers, then towards the roller rocker arms and ultimately to the intake valves. When the angle of the finger followers is narrow with respect to the roller member, valve lift is low. As the angle increases, so does valve lift. In this way, Valvematic can vary valve lift by adjusting the angle of the finger followers in relation to the roller bearing member.
Implementations
- Alfa RomeoAlfa RomeoAlfa Romeo Automobiles S.p.A. is an Italian manufacturer of cars. Founded as A.L.F.A. on June 24, 1910, in Milan, the company has been involved in car racing since 1911, and has a reputation for building expensive sports cars...
- Double continuous variable valve timing. CVVT is used on inlet and exhaust valves. - BMWBMWBayerische Motoren Werke AG is a German automobile, motorcycle and engine manufacturing company founded in 1916. It also owns and produces the Mini marque, and is the parent company of Rolls-Royce Motor Cars. BMW produces motorcycles under BMW Motorrad and Husqvarna brands...
- Double VANOSVANOSVANOS is an automobile variable valve timing technology developed by BMW in close collaboration with Continental Teves. VANOS varies the timing of the valves by moving the position of the camshafts in relation to the drive gear...
. - BMWBMWBayerische Motoren Werke AG is a German automobile, motorcycle and engine manufacturing company founded in 1916. It also owns and produces the Mini marque, and is the parent company of Rolls-Royce Motor Cars. BMW produces motorcycles under BMW Motorrad and Husqvarna brands...
/PSA Peugeot CitroënPSA Peugeot CitroënPSA Peugeot Citroën is a French manufacturer of automobiles and motorcycles sold under the Peugeot and Citroën marques. Headquartered in the 16th arrondissement of Paris, PSA is the second largest automaker based in Europe and the number eight in the world.-History:In December 1974 Peugeot S.A....
- Continuous variable valve timing (CVVT) - Chrysler - dual Variable Valve Timing (dual VVT). Used on Chrysler GEMAGlobal Engine Manufacturing AllianceThe Global Engine Manufacturing Alliance LLC, or GEMA, is a manufacturing arm of Global Engine Alliance LLC, which was a joint venture of Chrysler, Mitsubishi Motors, and Hyundai Motor Company for developing a line of shared engines...
"World" engine. - Daihatsu - Dynamic variable valve timing (DVVT)
- Ford - Variable valve timing (VVT)
- General Motors - Variable valve timing (VVT) provides continuous variable valve timing.
- Geely - Continuous variable valve timing (CVVT)
- KiaKia MotorsKia Motors , headquartered in Seoul, is South Korea's second-largest automobile manufacturer, following the Hyundai Motor Company, with sales of over 1.4 million vehicles in 2010...
- Continuous variable valve timing (CVVT) - HondaHondais a Japanese public multinational corporation primarily known as a manufacturer of automobiles and motorcycles.Honda has been the world's largest motorcycle manufacturer since 1959, as well as the world's largest manufacturer of internal combustion engines measured by volume, producing more than...
- The i-VTEC system uses VTC (Variable Timing Control) to provide continuous timing variation of the intake camshaftCamshaftA camshaft is a shaft to which a cam is fastened or of which a cam forms an integral part.-History:An early cam was built into Hellenistic water-driven automata from the 3rd century BC. The camshaft was later described in Iraq by Al-Jazari in 1206. He employed it as part of his automata,...
on DOHC i-VTEC engines. On the VTEC-E engines, an SOHC 3 valve, an oil pressure actuated solenoid activated when certain conditions are met and the second of the two intake valves opens and closes with the first. - HyundaiHyundaiHyundai ) is a global conglomerate company, part of the Korean chaebol, that was founded in South Korea by one of the most famous businessmen in Korean history: Chung Ju-yung...
- Continuous variable valve timing (CVVT) - provides continuous variable valve timing on IntakeIntakeAn intake , or especially for aircraft inlet, is an air intake for an engine. Because the modern internal combustion engine is in essence a powerful air pump, like the exhaust system on an engine, the intake must be carefully engineered and tuned to provide the greatest efficiency and power...
, Fuel System and ExhaustExhaust systemAn exhaust system is usually tubing used to guide reaction exhaust gases away from a controlled combustion inside an engine or stove. The entire system conveys burnt gases from the engine and includes one or more exhaust pipes...
all independently controlled - MazdaMazdais a Japanese automotive manufacturer based in Fuchū, Aki District, Hiroshima Prefecture, Japan.In 2007, Mazda produced almost 1.3 million vehicles for global sales...
- S-VT - The ECUEngine control unitAn engine control unit is a type of electronic control unit that determines the amount of fuel, ignition timing and other parameters an internal combustion engine needs to keep running...
calculates intake timing and actuates an oil control valve to modulate oil pressure. - MitsubishiMitsubishiThe Mitsubishi Group , Mitsubishi Group of Companies, or Mitsubishi Companies is a Japanese multinational conglomerate company that consists of a range of autonomous businesses which share the Mitsubishi brand, trademark and legacy...
- MIVECMIVECMIVEC is the brand name of a variable valve timing engine technology developed by Mitsubishi Motors...
system for the 4B1 engine family - intake and exhaust cam timing is continuously and independently controlled - MG Rover - Variable Valve Control (VVC)
- Nissan - Continuous Variable Valve Timing Control System (CVTCS). The ECU adjusts the engine's timing continuously to prevent detonation/pinging and optimize gas mileage.
- PorschePorschePorsche Automobil Holding SE, usually shortened to Porsche SE a Societas Europaea or European Public Company, is a German based holding company with investments in the automotive industry....
- VarioCamVarioCamVarioCam is an automobile variable valve timing technology developed by Porsche. VarioCam varies the timing of the intake valves by adjusting the tension on the timing chain connecting the intake and exhaust camshafts...
and VarioCam Plus. - Proton (carmaker) - Cam Profile Switching (CPS).
- Toyota - Variable Valve Timing with intelligence (VVT-iVVT-iVVT-i, or Variable Valve Timing with intelligence, is an automobile variable valve timing technology developed by Toyota, similar in performance to the BMW's VANOS. The Toyota VVT-i system replaces the Toyota VVT offered starting in 24 December 1991 on the 5-valve per cylinder 4A-GE engine. The...
), Variable Valve Timing with Lift and Intelligence (VVTL-i). - VolvoVolvoAB Volvo is a Swedish builder of commercial vehicles, including trucks, buses and construction equipment. Volvo also supplies marine and industrial drive systems, aerospace components and financial services...
- Continuous variable valve timing (CVVT)