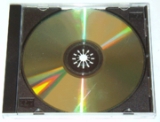
CD manufacturing
Encyclopedia
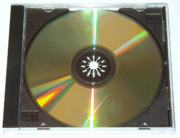
Compact Disc
The Compact Disc is an optical disc used to store digital data. It was originally developed to store and playback sound recordings exclusively, but later expanded to encompass data storage , write-once audio and data storage , rewritable media , Video Compact Discs , Super Video Compact Discs ,...
s (CDs) are replicated in mass quantities using a master version created from a source recording. This may be either in audio form (CD-Audio) or data form (CD-ROM
CD-ROM
A CD-ROM is a pre-pressed compact disc that contains data accessible to, but not writable by, a computer for data storage and music playback. The 1985 “Yellow Book” standard developed by Sony and Philips adapted the format to hold any form of binary data....
). This process is used in the mastering
Master recording
A multitrack recording master tape, disk or computer files on which productions are developed for later mixing, is known as the multi-track master, while the tape, disk or computer files holding a mix is called a mixed master.It is standard practice to make a copy of a master recording, known as...
of read-only compact discs; CD-R
CD-R
A CD-R is a variation of the Compact Disc invented by Philips and Sony. CD-R is a Write Once Read Many optical medium, though the whole disk does not have to be entirely written in the same session....
s, CD-RW
CD-RW
A CD-RW is a rewritable optical disc. It was introduced in 1997, and was known as "CD-Writable" during development. It was preceded by the CD-MO, which was never commercially released....
s, and DVD
DVD
A DVD is an optical disc storage media format, invented and developed by Philips, Sony, Toshiba, and Panasonic in 1995. DVDs offer higher storage capacity than Compact Discs while having the same dimensions....
s are made somewhat differently, though the methods are broadly similar.
A CD can be used to store audio
Sound recording and reproduction
Sound recording and reproduction is an electrical or mechanical inscription and re-creation of sound waves, such as spoken voice, singing, instrumental music, or sound effects. The two main classes of sound recording technology are analog recording and digital recording...
, video
Video
Video is the technology of electronically capturing, recording, processing, storing, transmitting, and reconstructing a sequence of still images representing scenes in motion.- History :...
, and data in various standardized formats defined in the Rainbow Books
Rainbow Books
The Rainbow Books are a collection of standards defining the formats of Compact Discs.Red BookYellow BookThe Rainbow Books are a collection of standards defining the formats of Compact Discs.Red Book...
. CDs are usually manufactured in a class 100 (ISO 5) or better clean room; they can usually be manufactured to quite strict manufacturing tolerances for only a few US cents per disk.
CD mastering differs from burning, as the pits and lands of a mastered CD are moulded into a CD blank, rather than being 'burn marks' in a dye layer (in CD-Rs) or areas with changed physical characteristics (in CD-RWs). In addition, CD burners write data sequentially, while a CD pressing plant 'writes' the entire disk in one physical stamping operation.
Premastering
All CDs are pressed from a digitalDigital
A digital system is a data technology that uses discrete values. By contrast, non-digital systems use a continuous range of values to represent information...
data source, with the most common sources being low error-rate CD-Rs or files from an attached computer
Computer
A computer is a programmable machine designed to sequentially and automatically carry out a sequence of arithmetic or logical operations. The particular sequence of operations can be changed readily, allowing the computer to solve more than one kind of problem...
hard drive containing the finished data (e. g., music or computer data). Some CD pressing systems can use digital
Digital
A digital system is a data technology that uses discrete values. By contrast, non-digital systems use a continuous range of values to represent information...
master tapes, either in Digital Audio Tape
Digital Audio Tape
Digital Audio Tape is a signal recording and playback medium developed by Sony and introduced in 1987. In appearance it is similar to a compact audio cassette, using 4 mm magnetic tape enclosed in a protective shell, but is roughly half the size at 73 mm × 54 mm × 10.5 mm. As...
, Exabyte
Exabyte (company)
Exabyte Corp. was a manufacturer of magnetic tape data storage products headquartered in Boulder, Colorado, United States. Exabyte Corp. is now defunct, but company's technology is sold by Tandberg Data under both brand names. Prior to the 2006 demise, Exabyte offered tape storage and automation...
or Umatic formats. However such sources are suitable only for production of audio CD
Red Book (audio CD standard)
Red Book is the standard for audio CDs . It is named after one of the Rainbow Books, a series of books that contain the technical specifications for all CD and CD-ROM formats.The first edition of the Red Book was released in 1980 by Philips and Sony; it was adopted by the Digital Audio Disc...
s due to error detection and correction issues. If the source is not a CD, the table of contents
Table of contents
A table of contents, usually headed simply "Contents" and abbreviated informally as TOC, is a list of the parts of a book or document organized in the order in which the parts appear...
for the CD to be pressed must also be prepared and stored on the tape or hard drive. In all cases except CD-R
CD-R
A CD-R is a variation of the Compact Disc invented by Philips and Sony. CD-R is a Write Once Read Many optical medium, though the whole disk does not have to be entirely written in the same session....
sources, the tape must be uploaded to a media mastering system to create the TOC (Table Of Contents) for the CD.
Glass mastering
GlassGlass
Glass is an amorphous solid material. Glasses are typically brittle and optically transparent.The most familiar type of glass, used for centuries in windows and drinking vessels, is soda-lime glass, composed of about 75% silica plus Na2O, CaO, and several minor additives...
mastering is performed in a class 100 (ISO 5) or better clean room or a self-enclosed clean environment within the mastering system. Contaminants introduced during critical stages of manufacturing (e.g., dust
Dust
Dust consists of particles in the atmosphere that arise from various sources such as soil dust lifted up by wind , volcanic eruptions, and pollution...
, pollen
Pollen
Pollen is a fine to coarse powder containing the microgametophytes of seed plants, which produce the male gametes . Pollen grains have a hard coat that protects the sperm cells during the process of their movement from the stamens to the pistil of flowering plants or from the male cone to the...
, hair
Hair
Hair is a filamentous biomaterial, that grows from follicles found in the dermis. Found exclusively in mammals, hair is one of the defining characteristics of the mammalian class....
, or smoke
Smoke
Smoke is a collection of airborne solid and liquid particulates and gases emitted when a material undergoes combustion or pyrolysis, together with the quantity of air that is entrained or otherwise mixed into the mass. It is commonly an unwanted by-product of fires , but may also be used for pest...
) can cause sufficient errors to make a master unusable. Once successfully completed, a CD master will be less susceptible to the effects of these contaminants.
During glass mastering, glass is used as a substrate to hold the CD master image while it is created and processed; hence the name. Glass substrates, noticeably larger than a CD, are round plates of glass approximately 240 mm in diameter and 6 mm thick. They often also have a small, steel
Steel
Steel is an alloy that consists mostly of iron and has a carbon content between 0.2% and 2.1% by weight, depending on the grade. Carbon is the most common alloying material for iron, but various other alloying elements are used, such as manganese, chromium, vanadium, and tungsten...
hub on one side to facilitate handling. The substrates are created specially for CD mastering and one side is polished until it is extremely smooth. Even microscopic scratches in the glass will affect the quality of CDs pressed from the master image. The extra area on the substrate allows for easier handling of the glass master and reduces risk of damage to the pit and land structure when the "father" stamper is removed from the glass substrate.
Once the glass substrate is cleaned using detergents and ultrasonic baths, the glass is placed in a spin coater
Spin coating
Spin coating is a procedure used to apply uniform thin films to flat substrates. In short, an excess amount of a solution is placed on the substrate, which is then rotated at high speed in order to spread the fluid by centrifugal force...
. The spin coater rinses the glass black with a solvent
Solvent
A solvent is a liquid, solid, or gas that dissolves another solid, liquid, or gaseous solute, resulting in a solution that is soluble in a certain volume of solvent at a specified temperature...
and then applies either photoresist or dye-polymer depending on the mastering process. Rotation spreads photoresist or dye-polymer coating evenly across the surface of the glass. The substrate is removed and baked
Baking
Baking is the technique of prolonged cooking of food by dry heat acting by convection, and not by radiation, normally in an oven, but also in hot ashes, or on hot stones. It is primarily used for the preparation of bread, cakes, pastries and pies, tarts, quiches, cookies and crackers. Such items...
to dry the coating and the glass substrate is ready for mastering.
Once the glass is ready for mastering, it is placed in a laser beam recorder (LBR). Most LBRs are capable of mastering at greater than 1x speed, but due to the weight of the glass substrate and the requirements of a CD master they are typically mastered at no greater than 8X playback speed. The LBR uses a laser to write the information, with a wavelength and final lens NA (numerical aperture) chosen to produce the required pit size on the master blank. For example, DVD pits are smaller than CD pits, so a shorter wavelength or higher NA (or both) is needed for DVD mastering. LBRs use one of two recording techniques; photo resist and non-photoresist mastering. Photoresist also comes in two variations; positive photoresist and negative photoresist.
Photoresist mastering
Photoresist mastering uses a light-sensitive material (a photoresistPhotoresist
A photoresist is a light-sensitive material used in several industrial processes, such as photolithography and photoengraving to form a patterned coating on a surface.-Tone:Photoresists are classified into two groups: positive resists and negative resists....
) to create the pits and lands on the CD master blank. The laser beam recorder uses a deep blue
Blue laser
A so-called blue laser is a laser that emits electromagnetic radiation at a wavelength of between 360 and 480 nanometres, which the human eye sees as blue or violet. Diode lasers which emit light at 445 nm are becoming popular as handheld lasers. Light of a shorter wavelength than 400 nm is...
or ultraviolet
Ultraviolet
Ultraviolet light is electromagnetic radiation with a wavelength shorter than that of visible light, but longer than X-rays, in the range 10 nm to 400 nm, and energies from 3 eV to 124 eV...
laser
Laser
A laser is a device that emits light through a process of optical amplification based on the stimulated emission of photons. The term "laser" originated as an acronym for Light Amplification by Stimulated Emission of Radiation...
to write the master. When exposed to the laser light, the photoresist undergoes a chemical reaction which hardens it. The exposed area is then soaked in a developer solution which removes the exposed positive photoresist or the unexposed negative photoresist.
Once the mastering is complete, the glass master is removed from the LBR and chemically 'developed'. Once developing is finished, the glass master is metalized
Metallizing
Metallizing is the general name for the technique of coating metal on the surface of non-metallic objects.Techniques for metallization started as early as mirror making. In 1835, Justus von Liebig discovered the process of coating a glass surface with metallic silver, making the glass mirror one of...
to provide a surface for the stamper to be formed onto.
It's then polished with lubrication and wiped down.
Non-photoresist or dye-polymer mastering
When a laser is used to record on the dye-polymer used in non-photoresist (NPR) mastering, the dye-polymer absorbs laser energy focused in a precise spot; this vapourises and forms a pit in the surface of the dye-polymer. This pit can be scanned by a red laser beam that follows the cutting beam, and the quality of the recording can be directly and immediately assessed; for instance, audio signals being recorded can also be played straight from the glass master in real time. The pit geometry and quality of the playback can all be adjusted while the CD is being mastered, as the blue writing laser and the red read laser are typically connected via a feedback system to optimise the recording. This allows the dye-polymer LBR to produce very consistent pits even if there are variations in the dye-polymer layer. Another advantage of this method is that pit depth variation can be programmed during recording to compensate for downstream characteristics of the local production process (e.g., marginal molding performance). This cannot be done with photoresist mastering because the pit depth is set by the PR coating thickness, whereas dye-polymer pits are cut into a coating thicker than the intended pits.This type of mastering is called Direct Read After Write (DRAW) and is the main advantage of some non-photoresist recording systems. Problems with the quality of the glass blank master, such as scratches, or an uneven dye-polymer coating, can be immediately detected. If required the mastering can be halted, saving time and increasing throughput.
Post-mastering
After mastering, the glass master is baked to harden the developed surface material to prepare it for metalisation. Metalisation is a critical step prior to electrogalvanic manufacture (electroplatingElectroplating
Electroplating is a plating process in which metal ions in a solution are moved by an electric field to coat an electrode. The process uses electrical current to reduce cations of a desired material from a solution and coat a conductive object with a thin layer of the material, such as a metal...
).
The developed glass master is placed in a vapour deposition metaliser which uses a combination of mechanical vacuum pump
Vacuum pump
A vacuum pump is a device that removes gas molecules from a sealed volume in order to leave behind a partial vacuum. The first vacuum pump was invented in 1650 by Otto von Guericke.- Types :Pumps can be broadly categorized according to three techniques:...
s and cryopump
Cryopump
A cryopump is a vacuum pump that traps gases and vapours by condensing them on a cold surface. They are only effective on some gases, depending on the freezing and boiling points of the gas relative to the cryopump's temperature...
s to lower the total vapour pressure inside a chamber to a hard vacuum. A piece of nickel
Nickel
Nickel is a chemical element with the chemical symbol Ni and atomic number 28. It is a silvery-white lustrous metal with a slight golden tinge. Nickel belongs to the transition metals and is hard and ductile...
wire is then heated in a tungsten boat to white hot temperature and the nickel vapour deposited onto the rotating glass master. The glass master is coated with the nickel vapour up to a typical thickness of around 400 nm.
The finished glass masters are inspected for stains, pinholes or incomplete coverage of the nickel coating and passed to the next step in the mastering process.
Electroforming
ElectroformingElectroforming
Electroforming is a metal forming process that forms thin parts through the electroplating process. The part is produced by plating a metal skin onto a base form, known as a mandrel, which is removed after plating...
occurs in "Matrix", the name used for the electroforming process area in many plants; it is also a class 100 (ISO 5) or better clean room. The data (music, computer data, etc.) on the metalised glass master is extremely easy to damage and must be transferred to a tougher form for use in the injection moulding equipment which actually produces the end-product optical disks.
The metalised master is clamped in a conductive plating frame with the data side facing outwards and lowered into a plating tank. The tank contains a nickel
Nickel
Nickel is a chemical element with the chemical symbol Ni and atomic number 28. It is a silvery-white lustrous metal with a slight golden tinge. Nickel belongs to the transition metals and is hard and ductile...
salt
Salt
In chemistry, salts are ionic compounds that result from the neutralization reaction of an acid and a base. They are composed of cations and anions so that the product is electrically neutral...
solution (usually nickel sulfamate) at a particular concentration which may be adjusted slightly in different plants depending on the characteristics of the prior steps. The solution is carefully buffered to maintain its pH
PH
In chemistry, pH is a measure of the acidity or basicity of an aqueous solution. Pure water is said to be neutral, with a pH close to 7.0 at . Solutions with a pH less than 7 are said to be acidic and solutions with a pH greater than 7 are basic or alkaline...
, and detergents are added to maintain a specific surface tension
Surface tension
Surface tension is a property of the surface of a liquid that allows it to resist an external force. It is revealed, for example, in floating of some objects on the surface of water, even though they are denser than water, and in the ability of some insects to run on the water surface...
. If the surface tension is too high, the solution cannot flow around the very small features (i.e., the pits and lands) on the surface of the glass master sufficiently well to deposit metal properly. The bath is heated to approximately 40 °C.
The glass master is rotated in the plating tank while a pump circulates the plating solution over the surface of the master. As the electroforming progresses, nickel is galvanically drawn out of the solution and must be replenished to maintain a constant concentration in the plating bath. This is achieved using high purity nickel pellets (99.99% pure) suspended in the solution in non-conductive polypropylene
Polypropylene
Polypropylene , also known as polypropene, is a thermoplastic polymer used in a wide variety of applications including packaging, textiles , stationery, plastic parts and reusable containers of various types, laboratory equipment, loudspeakers, automotive components, and polymer banknotes...
bags called anode
Anode
An anode is an electrode through which electric current flows into a polarized electrical device. Mnemonic: ACID ....
bags. The plating solution flows through the bag and over the glass master. The anode bags stop sediment formed during the nickel decomposition from reaching the solution and perhaps being plated onto to a master's surface. The nickel is packed firmly into the bag and forms part of the electric circuit.
A DC current applied to the glass master is the source of the galvanic potential which forces nickel from the anode pellets in the bags into solution as ions and ultimately onto the master's surface as an electrically neutral metallic layer. The electron
Electron
The electron is a subatomic particle with a negative elementary electric charge. It has no known components or substructure; in other words, it is generally thought to be an elementary particle. An electron has a mass that is approximately 1/1836 that of the proton...
s flow in the opposite direction to the current, from the cathode
Cathode
A cathode is an electrode through which electric current flows out of a polarized electrical device. Mnemonic: CCD .Cathode polarity is not always negative...
to the anode via the solution. Electrons are stripped from the nickel in the anode bag, travel through the external circuit before combining with nickel ion
Ion
An ion is an atom or molecule in which the total number of electrons is not equal to the total number of protons, giving it a net positive or negative electrical charge. The name was given by physicist Michael Faraday for the substances that allow a current to pass between electrodes in a...
s in the solution at the cathode end thus forming metallic nickel on the surface of the glass master.
The current must start off quite low and be increased slowly and evenly to prevent the metalised surface from overheating damage. As the thickness of the nickel on the glass master increases, the current can be increased. The electroplating step is finished after approximately 1 hour. Typical stampers are 0.300 mm thick. The part is removed from the tank and the metal layer peeled off the glass substrate. The metal part, now called a "father", has the desired data as a series of bumps rather than pits; it is a negative master. The father is washed with deionised water and other chemicals such as sodium hydroxide or acetone
Acetone
Acetone is the organic compound with the formula 2CO, a colorless, mobile, flammable liquid, the simplest example of the ketones.Acetone is miscible with water and serves as an important solvent in its own right, typically as the solvent of choice for cleaning purposes in the laboratory...
to remove all trace of resist or other contaminants. The glass master can be sent for reclamation, cleaning and checking before reuse. If defects are detected, it will be discarded or recycled
Recycling
Recycling is processing used materials into new products to prevent waste of potentially useful materials, reduce the consumption of fresh raw materials, reduce energy usage, reduce air pollution and water pollution by reducing the need for "conventional" waste disposal, and lower greenhouse...
.
Once cleaned of any loose nickel and resist, the father is electrolysed, washed and clamped
back into a frame and returned to the plating tank. This time the metal part that is grown is the mirror image of the father and is called a "mother"; this is a 'positive' master. All the stampers used to manufacture the CDs are made from a mother. Mothers can sometimes be regrown from fathers if they become damaged, however if handled correctly, 10 - 20 stampers can be grown from a single mother before the quality of the stamper is reduced unacceptably. Mothers are regrown from the father if it still exists, otherwise a new glass master is made.
If the CD is to be part of a long production run, the father may be archive
Archive
An archive is a collection of historical records, or the physical place they are located. Archives contain primary source documents that have accumulated over the course of an individual or organization's lifetime, and are kept to show the function of an organization...
d, however it is generally cut down with a hyper-accurate hydraulic punch and used as a stamper for moulding runs. Stampers and fathers are the same (negative) "polarity", the information surface is made up of a series of bumps. Mothers are the reverse and have pits on their surfaces.
A father, mother, and a collection of stampers (sometimes called "sons") are known collectively as a "family". Fathers and mothers are the same size as a glass substrate, typically 300 μm in thickness. Stampers do not require the extra space around the outside of the program area and they are punched to remove the excess nickel from outside and inside the information area in order to fit the mould of the injection moulding machine (IMM). The physical dimensions of the mould vary somewhat from machine to machine.
Replication
CD moulding machines are specifically designed high temperature polycarbonatePolycarbonate
PolycarbonatePhysical PropertiesDensity 1.20–1.22 g/cm3Abbe number 34.0Refractive index 1.584–1.586FlammabilityV0-V2Limiting oxygen index25–27%Water absorption – Equilibrium0.16–0.35%Water absorption – over 24 hours0.1%...
injection moulders. They have an average throughput of 550-900 discs per hour, per moulding line. Clear polycarbonate pellets are first dried at around 130 degrees Celsius for three hours (nominal; this depends on which optical grade resin is in use) and are fed via vacuum transport into one end of the injection moulder's barrel (i.e., the feed throat) and are moved to the injection chamber via a large screw inside the barrel. The barrel, wrapped with heater bands ranging in temperature from ca 210 to 320 degrees Celsius melts the polycarbonate. When the mould is closed the screw moves forward to inject molten plastic into the mould cavity. When the mould is full, cool water running through mould halves, outside the cavity, cools the plastic so it somewhat solid
Solid
Solid is one of the three classical states of matter . It is characterized by structural rigidity and resistance to changes of shape or volume. Unlike a liquid, a solid object does not flow to take on the shape of its container, nor does it expand to fill the entire volume available to it like a...
ifies. The entire process from the mould closing, injection and opening again takes approximately 3 to 5 seconds.
The moulded "disc" (referred to as a 'green' disc, lacking final processing) is removed from the mould by vacuum
Vacuum
In everyday usage, vacuum is a volume of space that is essentially empty of matter, such that its gaseous pressure is much less than atmospheric pressure. The word comes from the Latin term for "empty". A perfect vacuum would be one with no particles in it at all, which is impossible to achieve in...
handling; high-speed robot arms with vacuum suction caps. They are moved onto the finishing line infeed conveyor, or cooling station, in preparation for metallisation. At this point the discs are clear and contain all the digital information desired; however they cannot be played because there is no reflective layer.
The discs pass, one at a time, into the metaliser, a small chamber at approximately 10−3 Torr
Torr
The torr is a non-SI unit of pressure with the ratio of 760 to 1 standard atmosphere, chosen to be roughly equal to the fluid pressure exerted by a millimetre of mercury, i.e., a pressure of 1 torr is approximately equal to 1 mmHg...
(130 mPa) vacuum. The process is called 'sputtering'. The metaliser contains a metal "target" — almost always an alloy of (mostly) aluminium and small amounts of other metals. There is a load-lock system (similar to an airlock
Airlock
An airlock is a device which permits the passage of people and objects between a pressure vessel and its surroundings while minimizing the change of pressure in the vessel and loss of air from it...
) so the process chamber can be kept at high vacuum as the discs are exchanged. When the disc is rotated into the processing position by a swivel arm in the vacuum chamber, a small dose of argon gas is injected into the process chamber and a 700 volt DC electrical current at up to 20 kW is applied to the target. This produces a plasma from the target, and the plasma vapor is deposited onto the disc; it is an anode - cathode transfer. The metal coats the data side of the disc (upper surface), covering the pit and lands. This metal layer is the reflective surface which can be seen on the reverse (non label side) of a CD. This thin layer of metal is subject to corrosion from various contaminants and so is protected by a thin layer of lacquer.
After metalisation, the discs pass on to a spin-coater, where UV curable lacquer is dispensed onto the newly metallized layer. By rapid spinning, the lacquer coats the entire disc with a very thin layer (approx. 70 nm). After the lacquer is applied, the disks pass under a high intensity UV lamp which cures the lacquer rapidly. The lacquer also provides a surface for a label, generally screen printed or offset printed
Offset printing
Offset printing is a commonly used printing technique in which the inked image is transferred from a plate to a rubber blanket, then to the printing surface...
. The printing ink(s) must be chemically compatible with the lacquer used. Markers used by consumers to write on blank surfaces are not always, which can lead to breaks in the protective lacquer layer, to corrosion of the reflective layer, and failure of the CD.
Testing
For quality controlQuality control
Quality control, or QC for short, is a process by which entities review the quality of all factors involved in production. This approach places an emphasis on three aspects:...
, both the stamper and the moulded discs are tested before a production run. Samples of the disc (test pressings) are taken during long production runs and tested for quality consistency. Pressed discs are analyzed on a signal analysis machine. The metal stamper can also be tested on a signal analysis machine which has been specially adapted (larger diameter, more fragile, ...). The machine will "play" the disc or stamper and measure various physical and electrical parameters. Errors can be introduced at every step of production, but the moulding process is the least subject to adjustment. Sources of errors are more readily identified and compensated for during mastering. If the errors are too severe then the stamper is rejected and a replacement installed. An experienced machine operator can interpret the report from the analysis system and optimise the moulding process to make a disc that meets the required Rainbow Book specification (e.g. Red Book for Audio from the Rainbow Books
Rainbow Books
The Rainbow Books are a collection of standards defining the formats of Compact Discs.Red BookYellow BookThe Rainbow Books are a collection of standards defining the formats of Compact Discs.Red Book...
series).
If no defects are found, the CD continues to printing so a label
Label
A label is a piece of paper, polymer, cloth, metal, or other material affixed to a container or article, on which is printed a legend, information concerning the product, addresses, etc. A label may also be printed directly on the container or article....
can be screen or offset printed on the top surface of the disc. Thereafter, disks are counted, packaged, and shipped.
External links
- Diagram of a compact disc: http://www.digitalworks-inc.com/content/index.asp?page=12#cd
- How compact discs are made -- Explained by a layman for the laymen