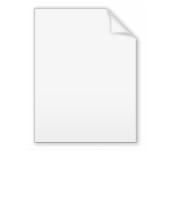
ZAMAK
Encyclopedia
Zamak is a family of alloy
s with a base metal of zinc
and alloying elements of aluminium
, magnesium
and copper
. Zamak alloys are part of the zinc aluminium alloy family
; they are distinguished from the other ZA alloys because of their constant 4% aluminium composition. The name zamak is an acronym of the German
names for the metals of which the alloys are composed: zink (zinc), aluminium, magnesium and kupfer (copper). The New Jersey Zinc Company
developed zamak alloys in 1929. While zinc alloys are popularly referred to as pot metal
or white metal
, zamak is held to higher industrial standards.
The most common zamak alloy is zamak 3, but zamak 2, zamak 5 and zamak 7 are still commercially used. These alloys are most commonly die cast. Zamak alloys (particularly #3 and #5) are frequently used in the spin casting
industry.
A large problem with early zinc die casting materials was zinc pest
, owing to impurities in the alloys. Zamak avoided this by the use of 99.99% pure zinc metal, produced by New Jersey's
use of a reflux
er as part of the smelting
process.
Zamak can be electroplated, wet painted, and chromate conversion coated
well.
.
Zamak goes by many different names based on standard and/or country:
The Short European Designation code breaks down as follows (using ZL0430 as the example):
Zamak 2 is also known as Kirksite when gravity cast as for use a die
. It was originally designed for low volume sheet metal dies. It later gained popularity for making short run injection molding
dies. It is also less commonly used for non-sparking tools and mandrels for metal spinning.
for the zamak series of zinc alloys; all other zinc alloys are compared to this. Zamak 3 has the base composition for the zamak alloys (96% zinc, 4% aluminium). It has excellent castability and long term dimensional stability. More than 70% of all North American zinc die castings are made from zamak 3.
Alloy
An alloy is a mixture or metallic solid solution composed of two or more elements. Complete solid solution alloys give single solid phase microstructure, while partial solutions give two or more phases that may or may not be homogeneous in distribution, depending on thermal history...
s with a base metal of zinc
Zinc
Zinc , or spelter , is a metallic chemical element; it has the symbol Zn and atomic number 30. It is the first element in group 12 of the periodic table. Zinc is, in some respects, chemically similar to magnesium, because its ion is of similar size and its only common oxidation state is +2...
and alloying elements of aluminium
Aluminium
Aluminium or aluminum is a silvery white member of the boron group of chemical elements. It has the symbol Al, and its atomic number is 13. It is not soluble in water under normal circumstances....
, magnesium
Magnesium
Magnesium is a chemical element with the symbol Mg, atomic number 12, and common oxidation number +2. It is an alkaline earth metal and the eighth most abundant element in the Earth's crust and ninth in the known universe as a whole...
and copper
Copper
Copper is a chemical element with the symbol Cu and atomic number 29. It is a ductile metal with very high thermal and electrical conductivity. Pure copper is soft and malleable; an exposed surface has a reddish-orange tarnish...
. Zamak alloys are part of the zinc aluminium alloy family
Zinc aluminium
Zinc-aluminium alloys are alloys whose main constituents are zinc and aluminium. Other alloying elements include magnesium and copper. This type of alloy was originally developed for gravity casting. Noranda, New Jersey Zinc Co. Ltd., St. Joe Mineral Co. and ILZRO were the main companies that...
; they are distinguished from the other ZA alloys because of their constant 4% aluminium composition. The name zamak is an acronym of the German
Germany
Germany , officially the Federal Republic of Germany , is a federal parliamentary republic in Europe. The country consists of 16 states while the capital and largest city is Berlin. Germany covers an area of 357,021 km2 and has a largely temperate seasonal climate...
names for the metals of which the alloys are composed: zink (zinc), aluminium, magnesium and kupfer (copper). The New Jersey Zinc Company
New Jersey Zinc Company
The Horsehead Corporation , formerly the New Jersey Zinc Company, is an American producer of zinc and related materials.The New Jersey Zinc Company was for many years the largest producer of zinc and zinc products in the United States. The company thrived in the period from 1897 to 1966, at which...
developed zamak alloys in 1929. While zinc alloys are popularly referred to as pot metal
Pot metal
Pot metal, also known as monkey metal, white metal or die-cast zinc, is a slang term that refers to alloys that consist of inexpensive, low-melting point metals used to make fast, inexpensive castings....
or white metal
White metal
The white metals are any of several light-colored alloys used as a base for plated silverware, ornaments or novelties, as well as any of several lead-base or tin-base alloys used for things like bearings, jewellery, miniature figures, fusible plugs, some medals and metal type.Some of the metals...
, zamak is held to higher industrial standards.
The most common zamak alloy is zamak 3, but zamak 2, zamak 5 and zamak 7 are still commercially used. These alloys are most commonly die cast. Zamak alloys (particularly #3 and #5) are frequently used in the spin casting
Spin casting
Spin casting, also known as centrifugal rubber mold casting , is a method of utilizing centrifugal force to produce castings from a rubber mold. Typically, a disc-shaped mold is spun along its central axis at a set speed. The casting material, usually molten metal or liquid thermoset plastic is...
industry.
A large problem with early zinc die casting materials was zinc pest
Zinc pest
Zinc pest, , is a destructive, intercrystalline corrosion process of zinc alloys containing lead impurities. It was first discovered to be a problem in 1923....
, owing to impurities in the alloys. Zamak avoided this by the use of 99.99% pure zinc metal, produced by New Jersey's
New Jersey Zinc Company
The Horsehead Corporation , formerly the New Jersey Zinc Company, is an American producer of zinc and related materials.The New Jersey Zinc Company was for many years the largest producer of zinc and zinc products in the United States. The company thrived in the period from 1897 to 1966, at which...
use of a reflux
Reflux
Reflux is a technique involving the condensation of vapors and the return of this condensate to the system from which it originated. It is used in industrial and laboratory distillations...
er as part of the smelting
Smelting
Smelting is a form of extractive metallurgy; its main use is to produce a metal from its ore. This includes iron extraction from iron ore, and copper extraction and other base metals from their ores...
process.
Zamak can be electroplated, wet painted, and chromate conversion coated
Chromate conversion coating
Chromate conversion coating is a type of conversion coating used to passivate aluminum, zinc, cadmium, copper, silver, magnesium, and tin alloys. It is primarily used as a corrosion inhibitor, primer, decorative finish, or to retain electrical conductivity. The process is named after the chromate...
well.
Mazak
In the early 1930s Morris Ashby in Britain had licensed the New Jersey zamak alloy. The high-purity refluxer zinc was not available in Britain and so they acquired the right to manufacture the alloy using a locally available electrolytically refined zinc of 99.95% purity. This was given the name Mazak, partly to distinguish it from zamak and partly from the initials of Morris Ashby. In 1933, National Smelting licensed the refluxer patent with the intent of using it to produce 99.99% zinc in their plant at AvonmouthAvonmouth
Avonmouth is a port and suburb of Bristol, England, located on the Severn Estuary, at the mouth of the River Avon.The council ward of Avonmouth also includes Shirehampton and the western end of Lawrence Weston.- Geography :...
.
Standards
Zinc alloy chemical composition standards are defined per country by the standard listed below:Country | Zinc ingot | Zinc casting |
---|---|---|
Europe | EN1774 | EN12844 |
USA | ASTM B240 | ASTM B86 |
Japan | JIS H2201 | JIS H5301 |
Australia | AS 1881 - SAA H63 | AS 1881 - SAA H64 |
China | GB 8738-88 | - |
Canada | CSA HZ3 | CSA HZ11 |
International | ISO 301 | - |
Zamak goes by many different names based on standard and/or country:
Traditional name | Short composition name | Form | Common | ASTM† | Short European designation | JIS | China | UK BS 1004 | France NFA 55-010 | Germany DIN 1743-2 | UNS | Other |
---|---|---|---|---|---|---|---|---|---|---|---|---|
Zamak 2 or Kirksite |
ZnAl4Cu3 | Ingot | Alloy 2 | AG 43A | ZL0430 | - | ZX04 | - | Z-A4U3 | Z430 | Z35540 | ZL2, ZA-2, ZN-002 |
Cast | ZP0430 | - | Z35541 | ZP2, ZA-2, ZN-002 | ||||||||
Zamak 3 | ZnAl4 | Ingot | Alloy 3 | AG 40A | ZL0400 | Ingot type 2 | ZX01 | Alloy A | Z-A4 | Z400 | Z35521 | ZL3, ZA-3, ZN-003 |
Cast | ZP0400 | ZDC2 | - | Z33520 | ZP3, ZA-3, ZN-003 | |||||||
Zamak 4 | Ingot | Used in Asia only | ZA-4, ZN-004 | |||||||||
Zamak 5 | ZnAl4Cu1 | Ingot | Alloy 5 | AG 41A | ZL0410 | Ingot type 1 | ZX03 | Alloy B | Z-A4UI | Z410 | Z35530 | ZL5, ZA-5, ZN-005 |
Cast | ZP0410 | ZDC1 | - | Z35531 | ZP5, ZA-5, ZN-005 | |||||||
Zamak 7 | ZnAl4Ni | Ingot | Alloy 7 | AG 40B | - | - | ZX02 | - | - | - | Z33522 | ZA-7, ZN-007 |
Cast | - | Z33523 | ||||||||||
†color of the cell is the color of the material designated by ASTM B908. |
The Short European Designation code breaks down as follows (using ZL0430 as the example):
- Z is the material (Z=Zinc)
- P is the use (P=Pressure die casting (casting), L=Ingot)
- 04 is the percent aluminium (04= 4% aluminium)
- 3 is the percent copper (3= 3% copper)
Zamak 2
Zamak 2 has the same composition as zamak 3 with the addition of 3% copper in order to increase strength by 20%, which also increases the price. Zamak 2 has the greatest strength out of all the zamak alloys. Over time it retains its strength and hardness better than the other alloys; however, it becomes more brittle, shrinks, and less elastic.Zamak 2 is also known as Kirksite when gravity cast as for use a die
Die (manufacturing)
A die is a specialized tool used in manufacturing industries to cut or shape material using a press. Like molds, dies are generally customized to the item they are used to create...
. It was originally designed for low volume sheet metal dies. It later gained popularity for making short run injection molding
Injection molding
Injection molding is a manufacturing process for producing parts from both thermoplastic and thermosetting plastic materials. Material is fed into a heated barrel, mixed, and forced into a mold cavity where it cools and hardens to the configuration of the cavity...
dies. It is also less commonly used for non-sparking tools and mandrels for metal spinning.
Alloying elements | Impurities | |||||||||||
---|---|---|---|---|---|---|---|---|---|---|---|---|
Standard | Limit | Al | Cu | Mg | Pb | Cd | Sn | Fe | Ni | Si | In | Tl |
ASTM B240 (Ingot) | min | 3.9 | 2.6 | 0.025 | - | - | - | - | - | - | - | - |
max | 4.3 | 2.9 | 0.05 | 0.004 | 0.003 | 0.002 | 0.075 | - | - | - | - | |
ASTM B86 (Cast) | min | 3.5 | 2.6 | 0.025 | - | - | - | - | - | - | - | - |
max | 4.3 | 2.9 | 0.05 | 0.005 | 0.004 | 0.003 | 0.1 | - | - | - | - | |
EN1774 (Ingot) | min | 3.8 | 2.7 | 0.035 | - | - | - | - | - | - | - | - |
max | 4.2 | 3.3 | 0.06 | 0.003 | 0.003 | 0.001 | 0.02 | 0.001 | 0.02 | - | - | |
EN12844 (Cast) | min | 3.7 | 2.7 | 0.025 | - | - | - | - | - | - | - | - |
max | 4.3 | 3.3 | 0.06 | 0.005 | 0.005 | 0.002 | 0.05 | 0.02 | 0.03 | - | - | |
GB8738-88 | min | 3.9 | 2.6 | 0.03 | - | - | - | - | - | - | - | - |
max | 4.3 | 3.1 | 0.06 | 0.004 | 0.003 | 0.0015 | 0.035 | - | - | - | - |
Property | Metric value | English value |
---|---|---|
Mechanical properties | ||
Ultimate tensile strength | 397 MPa (331 MPa aged) | 58,000 psi |
Yield strength (0.2% offset) | 361 MPa | 52,000 psi |
Impact strength | 38 J (7 J aged) | 28 ft-lbf (5 ft-lbf aged) |
Elongation at Fmax | 3% (2% aged) | |
Elongation at fracture | 6% | |
Shear strength | 317 MPa | 46,000 psi |
Compressive yield strength | 641 MPa | 93,000 psi |
Fatigue strength (reverse bending 5x108 cycles) | 59 MPa | 8,600 psi |
Hardness | 130 Brinell (98 Brinell aged) | |
Modulus of elasticity | 96 GPa | 14,000,000 psi |
Physical properties | ||
Solidification range (melting range) | 379—390 °C | 714—734 °F |
Density | 6.8 kg/dm3 | 0.25 lb/in3 |
Coefficient of thermal expansion | 27.8 μm/m-°C | 15.4 μin/in-°F |
Thermal conductivity | 105 W/m-K | 729 BTU-in/hr-ft2-°F |
Electrical resistivity | 6.85 μΩ-cm at 20 °C | 2.70 μΩ-in at 68 °F |
Latent heat (heat of fusion) | 110 J/g | 4.7x10−5 BTU/lb |
Specific heat capacity | 419 J/kg-°C | 0.100 BTU/lb-°F |
Coefficient of friction | 0.08 |
KS
The KS alloy was developed for spin casting decorative parts. It has the same composition as zamak 2, except with more magnesium in order to produce finer grains and reduce the orange peel effect.Alloying elements | Impurities | |||||||||||
---|---|---|---|---|---|---|---|---|---|---|---|---|
Standard | Limit | Al | Cu | Mg | Pb | Cd | Sn | Fe | Ni | Si | In | Tl |
Nyrstar | min | 3.8 | 2.5 | 0.4 | - | - | - | - | - | - | - | - |
max | 4.2 | 3.5 | 0.6 | 0.003 | 0.003 | 0.001 | 0.020 | - | - | - | - | |
Property | Metric value | English value |
---|---|---|
Mechanical properties | ||
Ultimate tensile strength | < 200 MPa | < 29,000 psi |
Yield strength (0.2% offset) | < 200 MPa | < 29,000 psi |
Elongation | < 2% | |
Hardness | 150 Brinell max | |
Physical properties | ||
Solidification range (melting range) | 380—390 °C | 716—734 °F |
Density | 6.6 g/cm3 | 0.25 lb/in3 |
Coefficient of thermal expansion | 28.0 μm/m-°C | 15.4 μin/in-°F |
Thermal conductivity | 105 W/m-K | 729 BTU-in/hr-ft2-°F |
Electrical conductivity | 25% IACS | |
Specific heat capacity | 419 J/kg-°C | 0.100 BTU/lb-°F |
Coefficient of friction | 0.08 |
Zamak 3
Zamak 3 is the de facto standardDe facto standard
A de facto standard is a custom, convention, product, or system that has achieved a dominant position by public acceptance or market forces...
for the zamak series of zinc alloys; all other zinc alloys are compared to this. Zamak 3 has the base composition for the zamak alloys (96% zinc, 4% aluminium). It has excellent castability and long term dimensional stability. More than 70% of all North American zinc die castings are made from zamak 3.
Alloying elements | Impurities | |||||||||||
---|---|---|---|---|---|---|---|---|---|---|---|---|
Standard | Limit | Al | Cu† | Mg | Pb | Cd | Sn | Fe | Ni | Si | In | Tl |
ASTM B240 (Ingot) | min | 3.9 | - | 0.025 | - | - | - | - | - | - | - | - |
max | 4.3 | 0.1 | 0.05 | 0.004 | 0.003 | 0.002 | 0.075 | - | - | - | - | |
ASTM B86 (Cast) | min | 3.5 | - | 0.025 | - | - | - | - | - | - | - | - |
max | 4.3 | 0.25 | 0.05 | 0.005 | 0.004 | 0.003 | 0.1 | - | - | - | - | |
EN1774 (Ingot) | min | 3.8 | - | 0.035 | - | - | - | - | - | - | - | - |
max | 4.2 | 0.03 | 0.06 | 0.003 | 0.003 | 0.001 | 0.02 | 0.001 | 0.02 | - | - | |
EN12844 (Cast) | min | 3.7 | - | 0.025 | - | - | - | - | - | - | - | - |
max | 4.3 | 0.1 | 0.06 | 0.005 | 0.005 | 0.002 | 0.05 | 0.02 | 0.03 | - | - | |
JIS H2201 (Ingot) | min | 3.9 | - | 0.03 | - | - | - | - | - | - | - | - |
max | 4.3 | 0.03 | 0.06 | 0.003 | 0.002 | 0.001 | 0.075 | - | - | - | - | |
JIS H5301 (Cast) | min | 3.5 | - | 0.02 | - | - | - | - | - | - | - | - |
max | 4.3 | 0.25 | 0.06 | 0.005 | 0.004 | 0.003 | 0.01 | - | - | - | - | |
AS1881 | min | 3.9 | - | 0.04 | - | - | - | - | - | - | - | - |
max | 4.3 | 0.03 | 0.06 | 0.003 | 0.003 | 0.001 | 0.05 | - | 0.001 | 0.0005 | 0.001 | |
GB8738-88 | min | 3.9 | - | 0.03 | - | - | - | - | - | - | - | - |
max | 4.3 | 0.1 | 0.06 | 0.004 | 0.003 | 0.0015 | 0.035 | - | - | - | - | |
†Impurity |
Property | Metric value | English value |
---|---|---|
Mechanical properties | ||
Ultimate tensile strength | 268 MPa | 38,900 psi |
Yield strength (0.2% offset) | 208 MPa | 30,200 psi |
Impact strength | 46 J (56 J aged) | 34 ft-lbf (41 ft-lbf aged) |
Elongation at Fmax | 3% | |
Elongation at fracture | 6.3% (16% aged) | |
Shear strength | 214 MPa | 31,000 psi |
Compressive yield strength | 414 MPa | 60,000 psi |
Fatigue strength (reverse bending 5x108 cycles) | 48 MPa | 7,000 psi |
Hardness | 97 Brinell | |
Modulus of elasticity | 96 GPa | 14,000,000 psi |
Physical properties | ||
Solidification range (melting range) | 381—387 °C | 718—729 °F |
Density | 6.7 g/cm3 | 0.24 lb/in3 |
Coefficient of thermal expansion | 27.4 μm/m-°C | 15.2 μin/in-°F |
Thermal conductivity | 113 W/mK | 784 BTU-in/hr-ft2-°F |
Electrical resistivity | 6.37 μΩ-cm at 20 °C | 2.51 μΩ-in at 68 °F |
Latent heat (heat of fusion) | 110 J/g | 4.7x10−5 BTU/lb |
Specific heat capacity | 419 J/kg-°C | 0.100 BTU/lb-°F |
Coefficient of friction | 0.07 |
Zamak 4
Zamak 4 was developed for the Asian markets to reduce the effects of die soldering while maintaining the ductility of zamak 3. This was achieved by using half the amount of copper from the zamak 5 composition.Alloying elements | Impurities | |||||||||||
---|---|---|---|---|---|---|---|---|---|---|---|---|
Standard | Limit | Al | Cu | Mg | Pb | Cd | Sn | Fe | Ni | Si | In | Tl |
Ningbo Jinyi Alloy Material Co. | min | 3.9 | 0.3 | 0.03 | - | - | - | - | - | - | - | - |
max | 4.3 | 0.5 | 0.06 | 0.003 | 0.002 | 0.002 | 0.075 | - | - | - | - | |
Genesis Alloys Ltd. | min | 3.9 | 0.3 | 0.04 | - | - | - | - | - | - | - | - |
max | 4.2 | 0.4 | 0.05 | 0.003 | 0.002 | 0.001 | 0.02 | 0.001 | 0.02 | 0.0005 | 0.001 |
Property | Metric value | English value |
---|---|---|
Mechanical properties | ||
Ultimate tensile strength | 317 MPa | 46,000 psi |
Yield strength (0.2% offset) | 221—269 MPa | 32,000—39,000 psi |
Impact strength | 61 J (7 J aged) | 45 ft-lbf (5 ft-lbf aged) |
Elongation | 7% | |
Shear strength | 214—262 MPa | 31,000—38,000 psi |
Compressive yield strength | 414—600 MPa | 60,000—87,000 psi |
Fatigue strength (rotary bending 5x108 cycles) | 48—57 MPa | 7,000—8,300 psi |
Hardness | 91 Brinell | |
Physical properties | ||
Solidification range (melting range) | 380—386 °C | 716—727 °F |
Density | 6.6 g/cm3 | 0.24 lb/in3 |
Coefficient of thermal expansion | 27.4 μm/m-°C | 15.2 μin/in-°F |
Thermal conductivity | 108.9—113.0 W/m-K @ 100 °C | 755.6—784.0 BTU-in/hr-ft2-°F @ 212 °F |
Electrical conductivity | 26-27% IACS | |
Specific heat capacity | 418.7 J/kg-°C | 0.100 BTU/lb-°F |
Zamak 5
Zamak 5 has the same composition as zamak 3 with the addition of 1% copper in order to increase strength (by approximately 10%), hardness and corrosive resistance, but reduces ductility. It also has less dimensional accuracy. Zamak 5 is more commonly used in Europe.Alloying elements | Impurities | |||||||||||
---|---|---|---|---|---|---|---|---|---|---|---|---|
Standard | Limit | Al | Cu | Mg | Pb | Cd | Sn | Fe | Ni | Si | In | Tl |
ASTM B240 (Ingot) | min | 3.9 | 0.75 | 0.03 | - | - | - | - | - | - | - | - |
max | 4.3 | 1.25 | 0.06 | 0.004 | 0.003 | 0.002 | 0.075 | - | - | - | - | |
ASTM B86 (Cast) | min | 3.5 | 0.75 | 0.03 | - | - | - | - | - | - | - | - |
max | 4.3 | 1.25 | 0.06 | 0.005 | 0.004 | 0.003 | 0.1 | - | - | - | - | |
EN1774 (Ingot) | min | 3.8 | 0.7 | 0.035 | - | - | - | - | - | - | - | - |
max | 4.2 | 1.1 | 0.06 | 0.003 | 0.003 | 0.001 | 0.02 | 0.001 | 0.02 | - | - | |
EN12844 (Cast) | min | 3.7 | 0.7 | 0.025 | - | - | - | - | - | - | - | - |
max | 4.3 | 1.2 | 0.06 | 0.005 | 0.005 | 0.002 | 0.05 | 0.02 | 0.03 | - | - | |
JIS H2201 (Ingot) | min | 3.9 | 0.75 | 0.03 | - | - | - | - | - | - | - | - |
max | 4.3 | 1.25 | 0.06 | 0.003 | 0.002 | 0.001 | 0.075 | - | - | - | - | |
JIS H5301 (Cast) | min | 3.5 | 0.75 | 0.02 | - | - | - | - | - | - | - | - |
max | 4.3 | 1.25 | 0.06 | 0.005 | 0.004 | 0.003 | 0.01 | - | - | - | - | |
AS1881 | min | 3.9 | 0.75 | 0.04 | - | - | - | - | - | - | - | - |
max | 4.3 | 1.25 | 0.06 | 0.003 | 0.003 | 0.001 | 0.05 | - | 0.001 | 0.0005 | 0.001 | |
GB8738-88 | min | 3.9 | 0.7 | 0.03 | - | - | - | - | - | - | - | - |
max | 4.3 | 1.1 | 0.06 | 0.004 | 0.003 | 0.0015 | 0.035 | - | - | - | - |
Property | Metric value | English value |
---|---|---|
Mechanical properties | ||
Ultimate tensile strength | 331 MPa (270 MPa aged) | 48,000 psi (39,000 psi aged) |
Yield strength (0.2% offset) | 295 MPa | 43,000 psi |
Impact strength | 52 J (56 J aged) | 38 ft-lbf (41 ft-lbf aged) |
Elongation at Fmax | 2% | |
Elongation at fracture | 3.6% (13% aged) | |
Shear strength | 262 MPa | 38,000 psi |
Compressive yield strength | 600 MPa | 87,000 psi |
Fatigue strength (reverse bending 5x108 cycles) | 57 MPa | 8,300 psi |
Hardness | 114 Brinell | |
Modulus of elasticity | 96 GPa | 14,000,000 psi |
Physical properties | ||
Solidification range (melting range) | 380—386 °C | 716—727 °F |
Density | 6.7 kg/dm3 | 0.24 lb/in3 |
Coefficient of thermal expansion | 27.4 μm/m-°C | 15.2 μin/in-°F |
Thermal conductivity | 109 W/mK | 756 BTU-in/hr-ft2-°F |
Electrical resistivity | 6.54 μΩ-cm at 20 °C | 2.57 μΩ-in at 68 °F |
Latent heat (heat of fusion) | 110 J/g | 4.7x10−5 BTU/lb |
Specific heat capacity | 419 J/kg-°C | 0.100 BTU/lb-°F |
Coefficient of friction | 0.08 |
Zamak 7
Zamak 7 has less magnesium than zamak 3 to increase fluidity and ductility, which is especially useful when casting thin wall components. In order to reduce inter-granular corrosion a small amount of nickel is added and impurities are more strictly controlled.Alloying elements | Impurities | |||||||||||
---|---|---|---|---|---|---|---|---|---|---|---|---|
Standard | Limit | Al | Cu† | Mg | Pb | Cd | Sn | Fe | Ni‡ | Si | In | Tl |
ASTM B240 (Ingot) | min | 3.9 | - | 0.01 | - | - | - | - | - | - | - | - |
max | 4.3 | 0.1 | 0.02 | 0.002 | 0.002 | 0.001 | 0.075 | - | - | - | - | |
ASTM B86 (Cast) | min | 3.5 | - | 0.005 | - | - | - | - | 0.005 | - | - | - |
max | 4.3 | 0.25 | 0.02 | 0.003 | 0.002 | 0.001 | 0.075 | 0.02 | - | - | - | |
GB8738-88 | min | 3.9 | - | 0.01 | - | - | - | - | 0.005 | - | - | - |
max | 4.3 | 0.1 | 0.02 | 0.002 | 0.002 | 0.001 | 0.075 | 0.02 | - | - | - | |
†Impurity ‡Alloying element |
Property | Metric value | English value |
---|---|---|
Mechanical properties | ||
Ultimate tensile strength | 285 MPa | 41,300 psi |
Yield strength (0.2% offset) | 285 MPa | 41,300 psi |
Impact strength | 58.0 J | 42.8 ft-lbf |
Elongation at fracture | 14% | |
Shear strength | 214 MPa | 31,000 psi |
Compressive yield strength | 414 MPa | 60,000 psi |
Fatigue strength (reverse bending 5x108 cycles) | 47.0 MPa | 6,820 psi |
Hardness | 80 Brinell | |
Physical properties | ||
Solidification range (melting range) | 381—387 °C | 718—729 °F |
Coefficient of thermal expansion | 27.4 μm/m-°C | 15.2 μin/in-°F |
Thermal conductivity | 113 W/m-K | 784 BTU-in/hr-ft2-°F |
Electrical resistivity | 6.4 μΩ-cm | 2.5 μΩ-in |
Specific heat capacity | 419 J/kg-°C | 0.100 BTU/lb-°F |
Casting temperature | 395—425 °C | 743—797 °F |
Uses
Common uses for zamak alloys include:- Blenders
- MirrorMirrorA mirror is an object that reflects light or sound in a way that preserves much of its original quality prior to its contact with the mirror. Some mirrors also filter out some wavelengths, while preserving other wavelengths in the reflection...
frames - Plumbing fittings
- Zippers
- Bathroom fixtures (faucets and shower heads)
- RickenbackerRickenbackerRickenbacker International Corporation, also known as Rickenbacker, is an electric and bass guitar manufacturer based in Santa Ana, California...
guitar "R" tailpieces - GibsonGibsonGibson may refer to:* Gibson Amphitheatre* Gibson Appliance* Gibson Girl* Gibson Guitar Corporation* Gibson * Gibson Generating Station-Places:In the United States:* Gibson, Arkansas* Gibson, Georgia* Gibson, Iowa* Gibson, Louisiana...
Tune-o-Matic bridge and stopbar tailpiece - StaplerStaplerA stapler is a mechanical device that joins sheets of paper or similar material by driving a thin metal staple through the sheets and folding the ends. Staplers are widely used in government, business, offices, and schools....
s - HandlesHandle (grip)A handle is a part of, or attachment to, an object that can be moved or used by hand. The design of each type of handle involves substantial ergonomic issues, even where these are dealt with intuitively or by following tradition...
- LocksLock (device)A lock is a mechanical or electronic fastening device that is released by a physical object or secret information , or combination of more than one of these....
- Die-cast toys
- Sheet metalSheet metalSheet metal is simply metal formed into thin and flat pieces. It is one of the fundamental forms used in metalworking, and can be cut and bent into a variety of different shapes. Countless everyday objects are constructed of the material...
tooling - Automotive parts
- Ceiling fans
- Golf clubsGolf club (equipment)A golf club is used to hit a golf ball in a game of golf. Each club is composed of a shaft with a grip and a clubhead. Woods are mainly used for long-distance fairway or tee shots; irons, the most versatile class, are used for a variety of shots; Hybrids that combine design elements of woods and...
- Fishing reels
- GyrojetGyrojetThe Gyrojet is a family of unique firearms developed in the 1960s named for the method of gyroscopically stabilizing its projectiles. Gyrojets fire small rockets, rather than inert bullets, which have little recoil and do not require a heavy barrel to resist the pressure of the combustion gases. ...
- Hi-Point FirearmsHi-Point FirearmsHi-Point Firearms, also known as Beemiller , is a firearms manufacturer based in Mansfield, Ohio. However only the CF.380, C9 9 mm, & the carbines are made in Mansfield...
- Wheel balancing weights (especially prominent in the European UnionEuropean UnionThe European Union is an economic and political union of 27 independent member states which are located primarily in Europe. The EU traces its origins from the European Coal and Steel Community and the European Economic Community , formed by six countries in 1958...
)