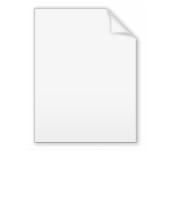
Space Shuttle Solid Rocket Booster
Overview
Solid rocket booster
Solid rocket boosters or Solid Rocket Motors, SRM, are used to provide thrust in spacecraft launches from the launchpad up to burnout of the SRBs. Many launch vehicles include SRBs, including the Ariane 5, Atlas V , and the NASA Space Shuttle...
used by the United States' NASA Space Shuttle
Space Shuttle
The Space Shuttle was a manned orbital rocket and spacecraft system operated by NASA on 135 missions from 1981 to 2011. The system combined rocket launch, orbital spacecraft, and re-entry spaceplane with modular add-ons...
during the first two minutes of powered flight. Together they provided about 83% of liftoff thrust for the Space Shuttle. They were located on either side of the rusty or orange-colored external propellant tank
Space Shuttle external tank
A Space Shuttle External Tank is the component of the Space Shuttle launch vehicle that contains the liquid hydrogen fuel and liquid oxygen oxidizer. During lift-off and ascent it supplies the fuel and oxidizer under pressure to the three Space Shuttle Main Engines in the orbiter...
. Each SRB produced 80% more liftoff thrust than one F-1
F-1 (rocket engine)
The F-1 is a rocket engine developed by Rocketdyne and used in the Saturn V. Five F-1 engines were used in the S-IC first stage of each Saturn V, which served as the main launch vehicle in the Apollo program. The F-1 is still the most powerful single-chamber liquid-fueled rocket engine ever...
engine, the most powerful single-chamber liquid-fueled rocket engine ever flown — five of which powered the first stage of the Saturn V
Saturn V
The Saturn V was an American human-rated expendable rocket used by NASA's Apollo and Skylab programs from 1967 until 1973. A multistage liquid-fueled launch vehicle, NASA launched 13 Saturn Vs from the Kennedy Space Center, Florida with no loss of crew or payload...
"moon rocket".