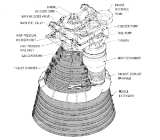
Regenerative cooling
Encyclopedia
Regenerative cooling in rocket
s is where some or all of the propellant
is passed through tubes, channels or otherwise in a jacket around the combustion chamber
or nozzle to cool the engine because the fuel in particular and sometimes the oxidizer are good coolants. The heated propellant is then fed into a special gas generator or injected directly into the main combustion chamber for combustion there.
used regenerative cooling to become the first to statically liquefy hydrogen.
The concept of regenerative cooling was also mentioned in 1903 in an article by Konstantin Tsiolkovsky
. Robert Goddard built the first regeneratively cooled engine in 1923, but rejected the scheme as too complex. A regeneratively cooled engine was built by the Italian researcher, Gaetano Arturo Crocco
in 1930. The first Soviet engines to employ the technique were Fridrikh Tsander's OR-2 tested in March 1933 and the ORM-50, bench tested in November 1933 by Valentin Glushko
. The first German engine of this type was also tested in March 1933 by Klaus Riedel in the VfR
. The Austrian scientist Eugen Sänger
was particularly famous for experiments with engine cooling starting in 1933; however, most of his experimental engines were water-cooled or cooled by an extra circuit of propellant.
The V-2 rocket
engine, the most powerful of its time at 25 tons (245 kN) of thrust, was regeneratively cooled, in a design by Walter Thiel
, by fuel lines coiled around the outside of the combustion chamber. This was an inefficient design that required the burning of diluted alcohol at low chamber pressure to avoid melting the engine. The American Redstone
engine used the same design.
A key innovation in regenerative cooling was the Soviet U-1250 engine designed by Aleksei Mihailovich Isaev
in 1945. Its combustion chamber was lined by a thin copper sheet supported by the corrugated steel wall of the chamber. Fuel flowed through the corrugations and absorbed heat very efficiently. This permitted more energetic fuels and higher chamber pressures, and it is the basic plan used in all Russian engines since. Modern American engines solve this problem by lining the combustion chamber with brazed
copper or nickel alloy tubes (although recent engines like in the Boeing Delta IV have started to use the Russian technique which is cheaper to construct). The American style of lining the engine with copper tubes is called the "spaghetti construction", and the concept is credited to Edward A. Neu at Reaction Motors
Inc. in 1947.
The amount of heat that can flow into the coolant is controlled by many factors including the temperature difference between the chamber and the coolant, the heat transfer coefficient, the thermal conductivity
of the chamber wall, the velocity in the coolant channels and the velocity of the gas flow in the chamber or the nozzle.
Two boundary layer
s form; one in the hot gas in the chamber and the other in the coolant within the channels.
Very typically most of the temperature drop occurs in the gas boundary layer since gases are relatively poor conductors. This boundary layer can be destroyed however by combustion instabilities, and wall failure can follow very soon afterwards.
The boundary layer within the coolant channels can also be disrupted if the coolant is at subcritical pressure and film boils; the gas then forms an insulating layer and the wall temperature climbs very rapidly and soon fails. However, if the coolant engages in nucleate boiling but does not form a film, this helps disrupt the coolant boundary layer and the gas bubbles formed rapidly collapse; this can triple the maximum heat flow. However, many modern engines with turbopumps use supercritical coolants, and these techniques can be seldom used.
Regenerative cooling is seldom used in isolation, film cooling, curtain cooling, transpiration cooling, radiation cooling are very frequently employed as well.
The metal of the inner liner is greatly weakened by the high temperature, and also undergoes significant thermal expansion at the inner surface while the cold-side wall of the liner constrains the expansion. This sets up significant thermal stresses that can cause the inner surface to crack or craze
after multiple firings particularly at the throat.
In addition the thin inner liner requires mechanical support to withstand the compressive loading due to the propellant's pressure, this support is usually provided by the side walls of the cooling channels and the backing plate.
The inner liner is usually constructed of relatively high temperature, high thermal conductivity materials; traditionally copper or nickel based alloys have been used.
Three different construction techniques have been used for regenerative cooling; a corrugated metal sheet is sometime brazed between the inner and outer liner; hundreds of pipes are sometimes brazed into the correct shape, or the inner liner is sometimes milled with cooling channels and an outer liner is used around that.
Rocket
A rocket is a missile, spacecraft, aircraft or other vehicle which obtains thrust from a rocket engine. In all rockets, the exhaust is formed entirely from propellants carried within the rocket before use. Rocket engines work by action and reaction...
s is where some or all of the propellant
Propellant
A propellant is a material that produces pressurized gas that:* can be directed through a nozzle, thereby producing thrust ;...
is passed through tubes, channels or otherwise in a jacket around the combustion chamber
Combustion chamber
A combustion chamber is the part of an engine in which fuel is burned.-Internal combustion engine:The hot gases produced by the combustion occupy a far greater volume than the original fuel, thus creating an increase in pressure within the limited volume of the chamber...
or nozzle to cool the engine because the fuel in particular and sometimes the oxidizer are good coolants. The heated propellant is then fed into a special gas generator or injected directly into the main combustion chamber for combustion there.
History
1857 - Siemens introduced the Regenerative cooling concept. On 10 May 1898, James DewarJames Dewar
Sir James Dewar FRS was a Scottish chemist and physicist. He is probably best-known today for his invention of the Dewar flask, which he used in conjunction with extensive research into the liquefaction of gases...
used regenerative cooling to become the first to statically liquefy hydrogen.
The concept of regenerative cooling was also mentioned in 1903 in an article by Konstantin Tsiolkovsky
Konstantin Tsiolkovsky
Konstantin Eduardovich Tsiolkovsky was an Imperial Russian and Soviet rocket scientist and pioneer of the astronautic theory. Along with his followers the German Hermann Oberth and the American Robert H. Goddard, he is considered to be one of the founding fathers of rocketry and astronautics...
. Robert Goddard built the first regeneratively cooled engine in 1923, but rejected the scheme as too complex. A regeneratively cooled engine was built by the Italian researcher, Gaetano Arturo Crocco
Gaetano Arturo Crocco
Gaetano Arturo Crocco was an Italian scientist and aeronautics pioneer, the founder of the Italian Rocket Society, and went on to become Italy's leading space scientist. He was born in Naples....
in 1930. The first Soviet engines to employ the technique were Fridrikh Tsander's OR-2 tested in March 1933 and the ORM-50, bench tested in November 1933 by Valentin Glushko
Valentin Glushko
Valentin Petrovich Glushko or Valentyn Petrovych Hlushko was a Soviet engineer, and the principal Soviet designer of rocket engines during the Soviet/American Space Race.-Biography:...
. The first German engine of this type was also tested in March 1933 by Klaus Riedel in the VfR
VfR
VfR is a German-language acronym that may appear in various contexts:*Verein für Raumschiffahrt, en:Society for Space Travel, a historical amateur rocket club in Germany...
. The Austrian scientist Eugen Sänger
Eugen Sänger
Eugen Sänger was an Austrian-German aerospace engineer best known for his contributions to lifting body and ramjet technology.-Early career:...
was particularly famous for experiments with engine cooling starting in 1933; however, most of his experimental engines were water-cooled or cooled by an extra circuit of propellant.
The V-2 rocket
V-2 rocket
The V-2 rocket , technical name Aggregat-4 , was a ballistic missile that was developed at the beginning of the Second World War in Germany, specifically targeted at London and later Antwerp. The liquid-propellant rocket was the world's first long-range combat-ballistic missile and first known...
engine, the most powerful of its time at 25 tons (245 kN) of thrust, was regeneratively cooled, in a design by Walter Thiel
Walter Thiel
Dr Walter Thiel was a German rocket scientist.He was the third civilian hired by Walter Dornberger for German research at Kummersdorf on November 1, 1932, , and in 1936, transferred to Dornberger's new rocket section...
, by fuel lines coiled around the outside of the combustion chamber. This was an inefficient design that required the burning of diluted alcohol at low chamber pressure to avoid melting the engine. The American Redstone
Redstone (rocket)
The PGM-11 Redstone was the first large American ballistic missile. A short-range surface-to-surface rocket, it was in active service with the U.S. Army in West Germany from June 1958 to June 1964 as part of NATO's Cold War defense of Western Europe...
engine used the same design.
A key innovation in regenerative cooling was the Soviet U-1250 engine designed by Aleksei Mihailovich Isaev
Aleksei Mihailovich Isaev
Aleksei Mikhailovich Isaev was a Russian rocket engineer.Aleksei Isaev began work under Leonid Dushkin during World War II, on an experimental rocket-powered interceptor plane. In 1944 he formed his own design bureau to engineer liquid-propellant engines...
in 1945. Its combustion chamber was lined by a thin copper sheet supported by the corrugated steel wall of the chamber. Fuel flowed through the corrugations and absorbed heat very efficiently. This permitted more energetic fuels and higher chamber pressures, and it is the basic plan used in all Russian engines since. Modern American engines solve this problem by lining the combustion chamber with brazed
Brazing
Brazing is a metal-joining process whereby a filler metal is heated above and distributed between two or more close-fitting parts by capillary action. The filler metal is brought slightly above its melting temperature while protected by a suitable atmosphere, usually a flux...
copper or nickel alloy tubes (although recent engines like in the Boeing Delta IV have started to use the Russian technique which is cheaper to construct). The American style of lining the engine with copper tubes is called the "spaghetti construction", and the concept is credited to Edward A. Neu at Reaction Motors
Reaction Motors
Reaction Motors Inc. was an early American maker of liquid-fueled rocket engines, located in New Jersey. RMI engines with thrust powered the Bell X-1 rocket aircraft that first broke the sound barrier in 1947, and later successors including the X-1A, X1E, and the D558-2 Douglas Skyrocket...
Inc. in 1947.
Heat flow and temperature
The heat flow through the chamber wall is very high indeed, 1-20 MW/m2 is not uncommon.The amount of heat that can flow into the coolant is controlled by many factors including the temperature difference between the chamber and the coolant, the heat transfer coefficient, the thermal conductivity
Thermal conductivity
In physics, thermal conductivity, k, is the property of a material's ability to conduct heat. It appears primarily in Fourier's Law for heat conduction....
of the chamber wall, the velocity in the coolant channels and the velocity of the gas flow in the chamber or the nozzle.
Two boundary layer
Boundary layer
In physics and fluid mechanics, a boundary layer is that layer of fluid in the immediate vicinity of a bounding surface where effects of viscosity of the fluid are considered in detail. In the Earth's atmosphere, the planetary boundary layer is the air layer near the ground affected by diurnal...
s form; one in the hot gas in the chamber and the other in the coolant within the channels.
Very typically most of the temperature drop occurs in the gas boundary layer since gases are relatively poor conductors. This boundary layer can be destroyed however by combustion instabilities, and wall failure can follow very soon afterwards.
The boundary layer within the coolant channels can also be disrupted if the coolant is at subcritical pressure and film boils; the gas then forms an insulating layer and the wall temperature climbs very rapidly and soon fails. However, if the coolant engages in nucleate boiling but does not form a film, this helps disrupt the coolant boundary layer and the gas bubbles formed rapidly collapse; this can triple the maximum heat flow. However, many modern engines with turbopumps use supercritical coolants, and these techniques can be seldom used.
Regenerative cooling is seldom used in isolation, film cooling, curtain cooling, transpiration cooling, radiation cooling are very frequently employed as well.
Mechanical considerations
With regenerative cooling, the pressure in the cooling channels is significantly above the chamber pressure hence the inner liner is under compression, while the outer wall of the engine is under significant hoop stresses.The metal of the inner liner is greatly weakened by the high temperature, and also undergoes significant thermal expansion at the inner surface while the cold-side wall of the liner constrains the expansion. This sets up significant thermal stresses that can cause the inner surface to crack or craze
Crazing
Crazing is a network of fine cracks on the surface of a material, for example in a glaze layer.Crazing is a phenomenon that frequently precedes fracture in some glassy thermoplastic polymers. Crazing occurs in regions of high hydrostatic tension, or in regions of very localized yielding, which...
after multiple firings particularly at the throat.
In addition the thin inner liner requires mechanical support to withstand the compressive loading due to the propellant's pressure, this support is usually provided by the side walls of the cooling channels and the backing plate.
The inner liner is usually constructed of relatively high temperature, high thermal conductivity materials; traditionally copper or nickel based alloys have been used.
Three different construction techniques have been used for regenerative cooling; a corrugated metal sheet is sometime brazed between the inner and outer liner; hundreds of pipes are sometimes brazed into the correct shape, or the inner liner is sometimes milled with cooling channels and an outer liner is used around that.