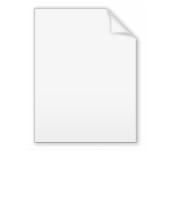
Pelletizing
Encyclopedia
Pelletizing is the process of compressing or molding a material into the shape of a pellet
. A wide range of different materials are pelletized including chemicals, iron ore, animal compound feed
, and more.
Iron ore pellets are spheres of typically 8–18 mm (0.31496062992126–0.708661417322835 in) to be used as raw material for blast furnace
s. They typically contain 67%-72% Fe and various additional material adjusting the chemical composition and the metallurgic properties of the pellets. Typically limestone
, dolostone
and olivine
is added and Bentonite
is used as binder.
The process of pelletizing combines mixing of the raw material, forming the pellet and a thermal treatment baking the soft raw pellet to hard spheres. The raw material is rolled into a ball, then fired in a kiln to sinter the particles into a hard sphere.
The configuration of iron ore pellets as packed spheres in the blast furnace allows air to flow between the pellets, decreasing the resistance to the air that flows up through the layers of material during the sme The configuration of iron ore powder in a blast furnace is more tightly-packed and restricts the air flow. This is the reason that iron ore is preferred in the form of pellets rather than in the form of finer particles.
of the substance ratios, milling, classification, increasing thickness, homogenization of the pulp and filtering.
). The duration of each stage and the temperature that the pellets are subjected to have a strong influence on the final product quality.
Pelletizing of animal feeds
can result in pellets from 1.2 mm (0.047244094488189 in) (shrimp feeds), through to 3–4 mm (0.118110236220472–0.15748031496063 in) (poultry feeds) up to 8–10 mm (0.31496062992126–0.393700787401575 in) (stock feeds). The pelletizing of stock feed is done with the pellet mill
machinery, which is done in a feed mill.
. Once the feed has been prepared to this stage the feed is ready to be pelletized.
, where feed is normally conditioned and thermal treated in the fitted conditioners of a pellet mill. The feed is then pushed through the holes and a pellet die and exit the pellet mill as pelleted feed.
Pellet
Pellet are small particles typically created by compressing an original material. Specific items often termed 'pellet' include:* Pelletizing is the industrial process used to create pellets, using a [pellet mill] or equipment for extrusion and * Spheroids is the process for the manufacture of...
. A wide range of different materials are pelletized including chemicals, iron ore, animal compound feed
Compound feed
Compound feeds are feedstuffs that are blended from various raw materials and additives. These blends are formulated according to the specific requirements of the target animal...
, and more.
Pelletizing of iron ore
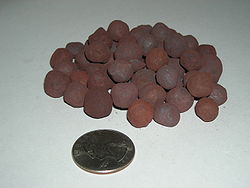
Blast furnace
A blast furnace is a type of metallurgical furnace used for smelting to produce industrial metals, generally iron.In a blast furnace, fuel and ore and flux are continuously supplied through the top of the furnace, while air is blown into the bottom of the chamber, so that the chemical reactions...
s. They typically contain 67%-72% Fe and various additional material adjusting the chemical composition and the metallurgic properties of the pellets. Typically limestone
Limestone
Limestone is a sedimentary rock composed largely of the minerals calcite and aragonite, which are different crystal forms of calcium carbonate . Many limestones are composed from skeletal fragments of marine organisms such as coral or foraminifera....
, dolostone
Dolostone
Dolostone or dolomite rock is a sedimentary carbonate rock that contains a high percentage of the mineral dolomite. In old U.S.G.S. publications it was referred to as magnesian limestone. Most dolostone formed as a magnesium replacement of limestone or lime mud prior to lithification. It is...
and olivine
Olivine
The mineral olivine is a magnesium iron silicate with the formula 2SiO4. It is a common mineral in the Earth's subsurface but weathers quickly on the surface....
is added and Bentonite
Bentonite
Bentonite is an absorbent aluminium phyllosilicate, essentially impure clay consisting mostly of montmorillonite. There are different types of bentonite, each named after the respective dominant element, such as potassium , sodium , calcium , and aluminum . Experts debate a number of nomenclatorial...
is used as binder.
The process of pelletizing combines mixing of the raw material, forming the pellet and a thermal treatment baking the soft raw pellet to hard spheres. The raw material is rolled into a ball, then fired in a kiln to sinter the particles into a hard sphere.
The configuration of iron ore pellets as packed spheres in the blast furnace allows air to flow between the pellets, decreasing the resistance to the air that flows up through the layers of material during the sme The configuration of iron ore powder in a blast furnace is more tightly-packed and restricts the air flow. This is the reason that iron ore is preferred in the form of pellets rather than in the form of finer particles.
Preparation of raw materials
Additional materials are added to the iron ore (pellet feed) to meet the requirements of the final pellets. This is done by placing the mixture in the pelletizer, which can hold different types of ores and additives, and mixing to adjust the chemical composition and the metallurgic properties of the pellets. In general, the following stages are included in this period of processing: concentration / separation, homogenizationHomogenization (chemistry)
Homogenization or homogenisation is any of several processes used to make a chemical mixture the same throughout.-Definition:Homogenization is intensive blending of mutually related substances or groups of mutually related substances to form a constant of different insoluble phases to obtain a...
of the substance ratios, milling, classification, increasing thickness, homogenization of the pulp and filtering.
Formation of the raw pellets
The formation of raw iron ore pellets, also known as pelletizing, has the objective of producing pellets in an appropriate band of sizes and with mechanical properties high usefulness during the stresses of transference, transport, and use. Both mechanical force and thermal processes are used to produce the correct pellet properties From equipment point of view there two alternatives for industrial production of iron ore pellets: drum and pelletizing disk.Thermal processing
In order to confer to the pellets high resistance metallurgic mechanics and appropriate characteristics, the pellets are subjected to thermal processing, which involves stages of drying, daily pay burn, burn, after-burn and cooling (in a cooling towerCooling tower
Cooling towers are heat removal devices used to transfer process waste heat to the atmosphere. Cooling towers may either use the evaporation of water to remove process heat and cool the working fluid to near the wet-bulb air temperature or in the case of closed circuit dry cooling towers rely...
). The duration of each stage and the temperature that the pellets are subjected to have a strong influence on the final product quality.
Pelletizing of animal feeds
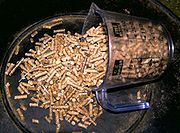
Compound feed
Compound feeds are feedstuffs that are blended from various raw materials and additives. These blends are formulated according to the specific requirements of the target animal...
can result in pellets from 1.2 mm (0.047244094488189 in) (shrimp feeds), through to 3–4 mm (0.118110236220472–0.15748031496063 in) (poultry feeds) up to 8–10 mm (0.31496062992126–0.393700787401575 in) (stock feeds). The pelletizing of stock feed is done with the pellet mill
Pellet mill
A pellet mill, also known as a pellet press, is a type of mill or machine press used to create pellets from powdered material. Pellet mills are unlike grinding mills, in that they combine small materials into a larger, homogeneous mass, rather than break large materials into smaller...
machinery, which is done in a feed mill.
Preparation of raw ingredients
Feed ingredients are normally first hammered to reduce the particle size of the ingredients. Ingredients are then batched, and then combined and mixed thoroughly by a feed mixerFeed mixer
Feed mixers are used in feed mills for the mixing of feed ingredients and premixes. The mixer plays a vital role in the feed production process, with efficient mixing being the key to good feed production. If feed is not mixed properly, ingredients and nutrients will not be properly distributed...
. Once the feed has been prepared to this stage the feed is ready to be pelletized.
Formation of the feed pellets
Pelletizing is done in a pellet millPellet mill
A pellet mill, also known as a pellet press, is a type of mill or machine press used to create pellets from powdered material. Pellet mills are unlike grinding mills, in that they combine small materials into a larger, homogeneous mass, rather than break large materials into smaller...
, where feed is normally conditioned and thermal treated in the fitted conditioners of a pellet mill. The feed is then pushed through the holes and a pellet die and exit the pellet mill as pelleted feed.
After pelleting processes
After pelleting the pellets are cooled with a cooler to bring the temperature of the feed down. Other post pelleting applications include post-pelleting conditioning, sorting via a screen and maybe coating if required.Gallery
See also
- GranuleGranuleGranule is a generic term used for a small particle or grain. The generic term is employed in a variety of specific contexts.* Granule , visible structures in the photosphere of the Sun arising from activity in the Sun's convective zone...
- Blast furnaceBlast furnaceA blast furnace is a type of metallurgical furnace used for smelting to produce industrial metals, generally iron.In a blast furnace, fuel and ore and flux are continuously supplied through the top of the furnace, while air is blown into the bottom of the chamber, so that the chemical reactions...
- Iron ore
- NurdleNurdlePlastic particles are an increasing cause of water pollution. The particles include nurdles, microbeads from cosmetics products and the breakdown products of plastic litter. Nurdles are pre-production plastic resin pellet typically under in diameter found outside of the typical plastics...
- PelletPelletPellet are small particles typically created by compressing an original material. Specific items often termed 'pellet' include:* Pelletizing is the industrial process used to create pellets, using a [pellet mill] or equipment for extrusion and * Spheroids is the process for the manufacture of...
- Pellet millPellet millA pellet mill, also known as a pellet press, is a type of mill or machine press used to create pellets from powdered material. Pellet mills are unlike grinding mills, in that they combine small materials into a larger, homogeneous mass, rather than break large materials into smaller...
- SpheronisationSpheronisationSpheronisation is a trademark of and is the process where pellets are produced from mixtures of solids and liquids by the involvement of forming and shaping forces. Pellets range in size from about 0.5 to 2.0 mm. During this process, extrudates are shaped into rounded or spherical granules...