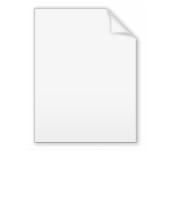
Machine fault diagnosis
Encyclopedia
Machine fault diagnosis is a field of Mechanical Engineering
concerned with finding faults arising in machines. A particularly well developed part of it applies specifically to rotating machinery, one of the most common types encountered. To identify the most probable faults leading to failure, many methods are used for data collection, including vibration
monitoring, thermal imaging, oil particle analysis, etc. Then these data are processed utilizing methods like spectral analysis
, wavelet analysis, waveform analysis (in the time domain, because spectral analysis usually concerns only frequency distribution and not phase information) and others. The results of this analysis are used in a root cause failure analysis in order to determine the original cause of the fault. For example, if a bearing fault is diagnosed, then it is likely that the bearing was not itself damaged at installation, but rather as the consequence of another installation error (e.g., misalignment) which then led to bearing damage. Diagnosing the bearing's damaged state is not enough for precision maintenance purposes. The root cause needs to be identified and remedied. If this is not done, the replacement bearing will soon wear out for the same reason and the machine will suffer more damage, remaining dangerous. Of course, the cause may also be visible as a result of the spectral analysis undertaken at the data-collection stage, but this may not always be the case.
measurement, thermal imaging, oil particle analysis and others.
sensors on all the machinery in a factory or to check enough samples from all machinery on a regular basis would be forbidding.
As a result, using fault diagnostics to meet industrial needs in a cost effective way, and to reduce maintenance costs without requiring more investments than the cost of what is to be avoided in the first place, requires an effective scheme of applying them. This is the subject of maintenance, repair and operations
; the different strategies include:
Mechanical engineering
Mechanical engineering is a discipline of engineering that applies the principles of physics and materials science for analysis, design, manufacturing, and maintenance of mechanical systems. It is the branch of engineering that involves the production and usage of heat and mechanical power for the...
concerned with finding faults arising in machines. A particularly well developed part of it applies specifically to rotating machinery, one of the most common types encountered. To identify the most probable faults leading to failure, many methods are used for data collection, including vibration
Vibration
Vibration refers to mechanical oscillations about an equilibrium point. The oscillations may be periodic such as the motion of a pendulum or random such as the movement of a tire on a gravel road.Vibration is occasionally "desirable"...
monitoring, thermal imaging, oil particle analysis, etc. Then these data are processed utilizing methods like spectral analysis
Spectral analysis
Spectral analysis or Spectrum analysis may refer to:* Spectrum analysis in chemistry and physics, a method of analyzing the chemical properties of matter from bands in their visible spectrum...
, wavelet analysis, waveform analysis (in the time domain, because spectral analysis usually concerns only frequency distribution and not phase information) and others. The results of this analysis are used in a root cause failure analysis in order to determine the original cause of the fault. For example, if a bearing fault is diagnosed, then it is likely that the bearing was not itself damaged at installation, but rather as the consequence of another installation error (e.g., misalignment) which then led to bearing damage. Diagnosing the bearing's damaged state is not enough for precision maintenance purposes. The root cause needs to be identified and remedied. If this is not done, the replacement bearing will soon wear out for the same reason and the machine will suffer more damage, remaining dangerous. Of course, the cause may also be visible as a result of the spectral analysis undertaken at the data-collection stage, but this may not always be the case.
Data collection methods
Methods used to collect data include vibrationVibration
Vibration refers to mechanical oscillations about an equilibrium point. The oscillations may be periodic such as the motion of a pendulum or random such as the movement of a tire on a gravel road.Vibration is occasionally "desirable"...
measurement, thermal imaging, oil particle analysis and others.
Data analysis methods
Spectral Analysis, Wavelet Analysis, Time-domain Waveform Analysis, others.Common faults diagnosed
When the machinery to be diagnosed includes rotating components, the most commonplace problems found are:- ImbalanceBalance- Equipment :* Balance beam, a piece of gymnastics apparatus.* Balance board, a piece of training equipment.* Balancing machine, a machine that balances mechanical rotating parts to lessen vibration.* Balance wheel, a watch component....
(Unbalance) - Bent shaft
- Shaft misalignment
- EccentricityEccentric (mechanism)In mechanical engineering, an eccentric is a circular disk solidly fixed to a rotating axle with its centre offset from that of the axle ....
- RubRUBRUB may stand for* RUB, Russian ruble currency code* Ruhr-Universität Bochum* Royal University of BhutanRub may refer to:* The Kuliak languages of Uganda...
- ResonanceResonanceIn physics, resonance is the tendency of a system to oscillate at a greater amplitude at some frequencies than at others. These are known as the system's resonant frequencies...
- Soft footSoft FootSoft Foot is a common term used for machine frame distortion. The distortion is caused when one or more feet of a machine differ in height from the others. This in turn may be due to differences when the machine was manufactured, a squishy footage with oil film etc. between foot and base, a bent...
- Looseness
- Beat (acoustics)Beat (acoustics)In acoustics, a beat is an interference between two sounds of slightly different frequencies, perceived as periodic variations in volume whose rate is the difference between the two frequencies....
- Sleeve bearing faults
- Belt problems
- Rolling-bearing faults
- Gear faults
- Machining vibrationsMachining vibrationsMachining vibrations, also called chatter, correspond to the relative movement between the workpiece and the cutting tool. The vibrations result in waves on the machined surface. This affects typical machining processes, such as turning, milling and drilling, and atypical machining processes, such...
Schemes of applying diagnostics
Fault diagnostics in usual industrial practice need to be applied according to guidelines. This need arises from the fact that diagnostics on their own may be capable of saving a single machine if monitoring is adequate, but it is impossible to apply them to all the equipment. The investment needed to either install continuous condition monitoringCondition monitoring
Condition monitoring is the process of monitoring a parameter of condition in machinery, such that a significant change is indicative of a developing failure. It is a major component of predictive maintenance. The use of conditional monitoring allows maintenance to be scheduled, or other actions...
sensors on all the machinery in a factory or to check enough samples from all machinery on a regular basis would be forbidding.
As a result, using fault diagnostics to meet industrial needs in a cost effective way, and to reduce maintenance costs without requiring more investments than the cost of what is to be avoided in the first place, requires an effective scheme of applying them. This is the subject of maintenance, repair and operations
Maintenance, Repair and Operations
Maintenance, repair, and operations or maintenance, repair, and overhaul involves fixing any sort of mechanical or electrical device should it become out of order or broken...
; the different strategies include:
- Condition-based maintenance
- Planned Preventative Maintenance
- Preventive maintenancePreventive maintenancePreventive maintenance has the following meanings:#The care and servicing by personnel for the purpose of maintaining equipment and facilities in satisfactory operating condition by providing for systematic inspection, detection, and correction of incipient failures either before they occur or...
- Corrective maintenanceCorrective maintenanceCorrective maintenance can be defined as a maintenance task performed to identify, isolate, and rectify a fault so that the failed equipment, machine, or system can be restored to an operational condition within the tolerances or limits established for in-service operations...
(does not use diagnostics)
See also
- Accident analysisAccident AnalysisAccident analysis is carried out in order to determine the cause or causes of an accident or series of accidents so as to prevent further incidents of a similar kind. It is also known as accident investigation. It may be performed by a range of experts, including forensic scientists, forensic...
- Condition monitoringCondition monitoringCondition monitoring is the process of monitoring a parameter of condition in machinery, such that a significant change is indicative of a developing failure. It is a major component of predictive maintenance. The use of conditional monitoring allows maintenance to be scheduled, or other actions...
- DiagnosisDiagnosisDiagnosis is the identification of the nature and cause of anything. Diagnosis is used in many different disciplines with variations in the use of logics, analytics, and experience to determine the cause and effect relationships...
- Maintenance testingMaintenance testingMaintenance testing is that testing which is performed to either identify equipment problems, diagnose equipment problems or to confirm that repair measures have been effective...
- Reliability centered maintenanceReliability Centered MaintenanceReliability Centered Maintenance, often known as RCM, is a process to ensure that assets continue to do what their users require in their present operating context....
- Failure AnalysisFailure analysisFailure analysis is the process of collecting and analyzing data to determine the cause of a failure. It is an important discipline in many branches of manufacturing industry, such as the electronics industry, where it is a vital tool used in the development of new products and for the improvement...
- FailureFailureFailure refers to the state or condition of not meeting a desirable or intended objective, and may be viewed as the opposite of success. Product failure ranges from failure to sell the product to fracture of the product, in the worst cases leading to personal injury, the province of forensic...
- Fault detection and isolationFault detection and isolationFault detection and isolation is a subfield of control engineering which concerns itself with monitoring a system, identifying when a fault has occurred, and pinpointing the type of fault and its location...