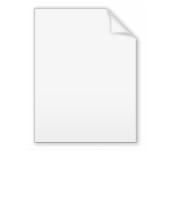
Fault detection and isolation
Encyclopedia
Fault detection and isolation is a subfield of control engineering
which concerns itself with monitoring a system, identifying when a fault
has occurred, and pinpointing the type of fault and its location. Two approaches can be distinguished: A direct pattern recognition of sensor readings that indicate a fault and an analysis of the discrepancy between the sensor readings and expected values, derived from some model. In the latter case, it is typical that a fault is said to be detected if the discrepancy or residual goes above a certain threshold. It is then the task of fault isolation to categorize the type of fault and its location in the machinery. Fault detection and isolation (FDI) techniques can be broadly classified into two categories. These include Model-based FDI and Signal processing based FDI.
, or knowledge based. Some of the model-based FDI techniques include observer-based approach, parity-space approach, and parameter identification based methods.
The example shown in the figure on the right illustrates a model-based FDI technique for an aircraft elevator reactive controller through the use of a truth table and a state chart. The truth table defines how the controller reacts to detected faults, and the state chart defines how the controller switches between the different modes of operation (passive, active, standby, off, and isolated) of each actuator. For example, if a fault is detected in hydraulic system 1, then the truth table sends an event to the state chart that the left inner actuator should be turned off. One of the benefits of this model-based FDI technique is that this reactive controller can also be connected to a continuous-time model of the actuator hydraulics, allowing the study of switching transients.
A good example of signal processing based FDI is Time Domain Reflectometry where a signal is sent down a cable or electrical line and the reflected signal is compared mathematically to original signal to identify faults. Spread Spectrum Time Domain Reflectometry, for instance, involves sending down a spread spectrum signal down a wire line to detect wire faults.
Control engineering
Control engineering or Control systems engineering is the engineering discipline that applies control theory to design systems with predictable behaviors...
which concerns itself with monitoring a system, identifying when a fault
Fault (technology)
In document ISO/CD 10303-226, a fault is defined as an abnormal condition or defect at the component, equipment, or sub-system level which may lead to a failure....
has occurred, and pinpointing the type of fault and its location. Two approaches can be distinguished: A direct pattern recognition of sensor readings that indicate a fault and an analysis of the discrepancy between the sensor readings and expected values, derived from some model. In the latter case, it is typical that a fault is said to be detected if the discrepancy or residual goes above a certain threshold. It is then the task of fault isolation to categorize the type of fault and its location in the machinery. Fault detection and isolation (FDI) techniques can be broadly classified into two categories. These include Model-based FDI and Signal processing based FDI.
Model-based FDI
In model-based FDI techniques some model of the system is used to decide about the occurrence of fault. The system model may be mathematicalMathematical model
A mathematical model is a description of a system using mathematical concepts and language. The process of developing a mathematical model is termed mathematical modeling. Mathematical models are used not only in the natural sciences and engineering disciplines A mathematical model is a...
, or knowledge based. Some of the model-based FDI techniques include observer-based approach, parity-space approach, and parameter identification based methods.
The example shown in the figure on the right illustrates a model-based FDI technique for an aircraft elevator reactive controller through the use of a truth table and a state chart. The truth table defines how the controller reacts to detected faults, and the state chart defines how the controller switches between the different modes of operation (passive, active, standby, off, and isolated) of each actuator. For example, if a fault is detected in hydraulic system 1, then the truth table sends an event to the state chart that the left inner actuator should be turned off. One of the benefits of this model-based FDI technique is that this reactive controller can also be connected to a continuous-time model of the actuator hydraulics, allowing the study of switching transients.
Signal processing based FDI
In signal processing based FDI, some mathematical or statistical operations are performed on the measurements, or some neural network is trained using measurements to extract the information about the fault.A good example of signal processing based FDI is Time Domain Reflectometry where a signal is sent down a cable or electrical line and the reflected signal is compared mathematically to original signal to identify faults. Spread Spectrum Time Domain Reflectometry, for instance, involves sending down a spread spectrum signal down a wire line to detect wire faults.
See also
- Spread-spectrum time-domain reflectometrySpread-spectrum time-domain reflectometrySpread-spectrum time-domain reflectometry is a measurement technique to identify faults, usually in electrical wires, by observing reflected spread spectrum signals. SSTDR is a type of time-domain reflectometry that can be advantageous to other systems due to the ability to use SSTDR in high-noise...
- Control TheoryControl theoryControl theory is an interdisciplinary branch of engineering and mathematics that deals with the behavior of dynamical systems. The desired output of a system is called the reference...
- Predictive maintenancePredictive maintenancePredictive maintenance techniques help determine the condition of in-service equipment in order to predict when maintenance should be performed...
- Fault-tolerant systemFault-tolerant systemFault-tolerance or graceful degradation is the property that enables a system to continue operating properly in the event of the failure of some of its components. A newer approach is progressive enhancement...
- Condition monitoringCondition monitoringCondition monitoring is the process of monitoring a parameter of condition in machinery, such that a significant change is indicative of a developing failure. It is a major component of predictive maintenance. The use of conditional monitoring allows maintenance to be scheduled, or other actions...
- Control reconfigurationControl reconfigurationControl reconfiguration is an active approach in control theory to achieve fault-tolerant control for dynamic systems . It is used when severe faults, such as actuator or sensor outages, cause a break-up of the control loop, which must be restructured to prevent failure at the system level...
- System identificationSystem identificationIn control engineering, the field of system identification uses statistical methods to build mathematical models of dynamical systems from measured data...