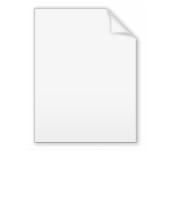
Preventive maintenance
Encyclopedia
Preventive maintenance has the following meanings:
The main difference of subgroups is determination of maintenance time
, or determination of moment when maintenance should be performed.
While preventive maintenance is generally considered to be worthwhile, there are risks such as equipment failure or human error
involved when performing preventive maintenance, just as in any maintenance operation. Preventive maintenance as scheduled overhaul or scheduled replacement provides two of the three proactive failure management policies available to the maintenance engineer. Common methods of determining what Preventive (or other) failure management policies should be applied are; OEM
recommendations, requirements of codes and legislation within a jurisdiction, what an "expert" thinks ought to be done, or the maintenance that's already done to similar equipment, and most important measured values and performance indications.
To make it simple:
The primary goal of maintenance is to avoid or mitigate the consequences of failure of equipment. This may be by preventing the failure before it actually occurs which Planned Maintenance and Condition Based Maintenance help to achieve. It is designed to preserve and restore equipment reliability by replacing worn components before they actually fail. Preventive maintenance activities include partial or complete overhauls at specified periods, oil changes, lubrication and so on. In addition, workers can record equipment deterioration so they know to replace or repair worn parts before they cause system failure. The ideal preventive maintenance program would prevent all equipment failure before it occurs.
There is a controversy of sorts regarding the propriety of the usage “preventative.” The consensus of internet entries concerning the respective usages seems to indicate that “preventive” is the preferred term.
While Preventive Maintenance - evaluation of particles in suspension in a lubricant, sound and vibration analysis of a machine.
It is easy to describe the difference between preventive vs predictive maintenance.
Look at the below example.
You have bought a incandescent light bulb. The manufacturing company is telling you that the life span of the bulb is 3 years. So just before expiring 3 years you have decided to replace the bulb with a new one and scheduled for a maintenance. This is called preventive maintenance.
However, everyday you have the opportunity to observe the bulb operation. After two years, the bulb starts flickering. So you are predicting at that time that the bulb is going to fail very soon and deciding to change with a new one and scheduled for a just-in time maintenance. This is called predictive maintenance.
- The care and servicing by personnel for the purpose of maintaining equipment and facilities in satisfactory operating condition by providing for systematic inspection, detectionFault detection and isolationFault detection and isolation is a subfield of control engineering which concerns itself with monitoring a system, identifying when a fault has occurred, and pinpointing the type of fault and its location...
, and correction of incipient failures either before they occur or before they develop into major defects. - MaintenanceMaintenance, Repair and OperationsMaintenance, repair, and operations or maintenance, repair, and overhaul involves fixing any sort of mechanical or electrical device should it become out of order or broken...
, including tests, measurements, adjustments, and parts replacement, performed specifically to prevent faults from occurring.
Subgroups
Preventive maintenance can be described as maintenance of equipment or systems before fault occurs. It can be divided into two subgroups:- Planned maintenance
- and condition-based maintenance.
The main difference of subgroups is determination of maintenance time
Time
Time is a part of the measuring system used to sequence events, to compare the durations of events and the intervals between them, and to quantify rates of change such as the motions of objects....
, or determination of moment when maintenance should be performed.
While preventive maintenance is generally considered to be worthwhile, there are risks such as equipment failure or human error
Human reliability
Human reliability is related to the field of human factors engineering and ergonomics, and refers to the reliability of humans in fields such as manufacturing, transportation, the military, or medicine...
involved when performing preventive maintenance, just as in any maintenance operation. Preventive maintenance as scheduled overhaul or scheduled replacement provides two of the three proactive failure management policies available to the maintenance engineer. Common methods of determining what Preventive (or other) failure management policies should be applied are; OEM
Original Equipment Manufacturer
An original equipment manufacturer, or OEM, manufactures products or components that are purchased by a company and retailed under that purchasing company's brand name. OEM refers to the company that originally manufactured the product. When referring to automotive parts, OEM designates a...
recommendations, requirements of codes and legislation within a jurisdiction, what an "expert" thinks ought to be done, or the maintenance that's already done to similar equipment, and most important measured values and performance indications.
To make it simple:
- Preventive maintenance is conducted to keep equipment working and/or extend the life of the equipment.
- Corrective maintenance, sometimes called "repair," is conducted to get equipment working again.
The primary goal of maintenance is to avoid or mitigate the consequences of failure of equipment. This may be by preventing the failure before it actually occurs which Planned Maintenance and Condition Based Maintenance help to achieve. It is designed to preserve and restore equipment reliability by replacing worn components before they actually fail. Preventive maintenance activities include partial or complete overhauls at specified periods, oil changes, lubrication and so on. In addition, workers can record equipment deterioration so they know to replace or repair worn parts before they cause system failure. The ideal preventive maintenance program would prevent all equipment failure before it occurs.
There is a controversy of sorts regarding the propriety of the usage “preventative.” The consensus of internet entries concerning the respective usages seems to indicate that “preventive” is the preferred term.
Difference Between Preventive and Predictive Maintenance
Predictive maintenance tends to include direct measurement of the item. Example, an infrared picture of a circuit board to determine hot spots.While Preventive Maintenance - evaluation of particles in suspension in a lubricant, sound and vibration analysis of a machine.
It is easy to describe the difference between preventive vs predictive maintenance.
Look at the below example.
You have bought a incandescent light bulb. The manufacturing company is telling you that the life span of the bulb is 3 years. So just before expiring 3 years you have decided to replace the bulb with a new one and scheduled for a maintenance. This is called preventive maintenance.
However, everyday you have the opportunity to observe the bulb operation. After two years, the bulb starts flickering. So you are predicting at that time that the bulb is going to fail very soon and deciding to change with a new one and scheduled for a just-in time maintenance. This is called predictive maintenance.
See also
- PrognosticsPrognosticsPrognostics is an engineering discipline focused on predicting the time at which a system or a component will no longer perform its intended function . This lack of performance is most often a failure beyond which the system can no longer be used to meet desired performance...
- Reliability centered maintenanceReliability Centered MaintenanceReliability Centered Maintenance, often known as RCM, is a process to ensure that assets continue to do what their users require in their present operating context....
- Corrective maintenanceCorrective maintenanceCorrective maintenance can be defined as a maintenance task performed to identify, isolate, and rectify a fault so that the failed equipment, machine, or system can be restored to an operational condition within the tolerances or limits established for in-service operations...
- Operational maintenanceOperational maintenanceOperational maintenance is the care and minor maintenance of equipment using procedures that do not require detailed technical knowledge of equipment’s or system’s function and design. This category of operational maintenance normally consists of inspecting, cleaning, servicing,...
- Department of Defense Dictionary of Military and Associated TermsDepartment of Defense Dictionary of Military and Associated TermsThe Department of Defense Dictionary of Military and Associated Terms is a compendium of terminology used by the United States Department of Defense ....
- Predictive maintenancePredictive maintenancePredictive maintenance techniques help determine the condition of in-service equipment in order to predict when maintenance should be performed...
- Value driven maintenanceValue driven maintenanceVDM - Value Driven Maintenance is a maintenance management methodology.VDM was developed by Mark Haarman and Guy Delahay. Both former chairmen of the Dutch Maintenance Association and authors of the book entitled “Value Driven Maintenance, New Faith in Maintenance”.-Value drivers in...
External links
- Maintenance of Hydraulic Systems
- International Facility Management Association
- The Center for Advanced Life Cycle Engineering (CALCE) at the University of Maryland, College ParkUniversity of Maryland, College ParkThe University of Maryland, College Park is a top-ranked public research university located in the city of College Park in Prince George's County, Maryland, just outside Washington, D.C...
has a PHM group dedicated to providing a research and knowledge base to support the advancement of preventive and predictive maintenance with a focus on electronics.