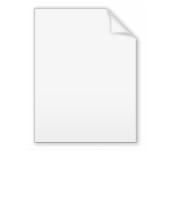
Fluid bearing
Encyclopedia
Fluid bearings are bearings
which support the bearing's loads solely on a thin layer of liquid or gas.
They can be broadly classified as fluid dynamic bearings or hydrostatic bearings. Hydrostatic bearings are externally pressurized fluid bearings, where the fluid is usually oil, water or air, and the pressurization is done by a pump. Hydrodynamic bearings rely on the high speed of the journal self-pressurizing the fluid in a wedge between the faces.
Fluid bearings are frequently used in high load, high speed or high precision applications where ordinary ball bearing
s have short life or high noise and vibration. They are also used increasingly to reduce cost. For example, hard disk
drive motor fluid bearings are both quieter and cheaper than the ball bearings they replace.
between the bearing faces, typically sealed around or under the rotating shaft.
There are two principal ways of getting the fluid into the bearing:
Hydrostatic bearings rely on an external pump. The power required by that pump contributes to system energy loss just as bearing friction otherwise would. Better seals can reduce leak rates and pumping power, but may increase friction.
Hydrodynamic bearings rely on bearing motion to suck fluid into the bearing and may have high friction and short life at speeds lower than design or during starts and stops. An external pump or secondary bearing may be used for startup and shutdown to prevent damage to the hydrodynamic bearing. A secondary bearing may have high friction and short operating life, but good overall service life if bearing starts and stops are infrequent.
Hydrodynamic (Full Film) Lubrication is obtained when two mating surfaces are completely separated by a cohesive film of lubricant.
The thickness of the film thus exceeds the combined roughness of the surfaces. The coefficient of friction is lower than with boundary-layer lubrication. Hydrodynamic lubrication prevents wear in moving parts, and metal to metal contact is prevented.
Hydrodynamic lubrication requires thin, converging fluid films. These fluids can be liquid or gas, so long as they exhibit viscosity. In computer components, like a hard disk
, heads are supported by hydrodynamic lubrication in which the fluid film is the atmosphere.
The scale of these films are on the order of micrometers. Their convergence creates pressures normal to the surfaces they contact, forcing them apart.
3 Types of bearings include:
Conceptually the bearings can be thought of as two major geometric classes: bearing-journal(Anti Friction), and plane-slider(Friction).
The Reynolds equations can be used to derive the governing principles for the fluids. Note that when gases are used, their derivation is much more involved.
The thin films can be thought to have pressure and viscous forces acting on them. Because there is a difference in velocity there will be a difference in the surface traction vectors. Because of mass conservation we can also assume an increase in pressure, making the body forces different.
s with a similar load rating. The bearing can be as simple as two smooth surfaces with seals to keep in the working fluid. In contrast, a conventional rolling-element bearing
may require many high-precision rollers with complicated shapes. Hydrostatic and many gas bearings do have the complication and expense of external pumps.
Most fluid bearings require little or no maintenance, and have almost unlimited life. Conventional rolling-element bearings usually have shorter life and require regular maintenance. Pumped hydrostatic and aerostatic (gas) bearing designs retain low friction down to zero speed and need not suffer start/stop wear, provided the pump does not fail.
Fluid bearings generally have very low friction—far better than mechanical bearings. One source of friction in a fluid bearing is the viscosity
of the fluid. Hydrostatic gas bearings are among the lowest friction bearings. However, lower fluid viscosity also typically means fluid leaks faster from the bearing surfaces, thus requiring increased power for pumps or seals.
When a roller or ball is heavily loaded, fluid bearings have clearances that change less under load (are "stiffer") than mechanical bearings. It might seem that bearing stiffness, as with maximum design load, would be a simple function of average fluid pressure and the bearing surface area. In practice, when bearing surfaces are pressed together, the fluid outflow is constricted. This significantly increases the pressure of the fluid between the bearing faces. As fluid bearing faces can be comparatively larger than rolling surfaces, even small fluid pressure differences cause large restoring forces, maintaining the gap.
However, in lightly loaded bearings, such as disk drives, the typical ball bearing stiffnesses are ~10^7 MN/m. Comparable fluid bearings have stiffness of ~10^6 MN/m. Because of this, some fluid bearings, particularly hydrostatic bearings, are deliberately designed to pre-load the bearing to increase the stiffness.
Fluid bearings often inherently add significant damping. This helps attenuate resonances at the gyroscopic frequencies of journal bearings (sometimes called conical or rocking modes).
It is very difficult to make a mechanical bearing which is atomically smooth and round; and mechanical bearings deform in high-speed operation due to centripetal force
. In contrast, fluid bearings self-correct for minor imperfections.
Fluid bearings are typically quieter and smoother (more consistent friction) than rolling-element bearings. For example, hard disk
s manufactured with fluid bearings have noise ratings for bearings/motors on the order of 20-24 dB
, which is a little more than the background noise of a quiet room. Drives based on rolling-element bearings are typically at least 4 dB noisier.
Fluid bearings can be made with a lower NRRO (non repeatable run out) than a ball or rolling element bearing. This can be critical in modern hard disk drive and ultra precision spindles.
Tilting pad bearings are used as radial bearings for supporting and locating shafts in compressors.
Power consumption and stiffness or damping greatly vary with temperature, which complicates the design and operation of a fluid bearing in wide temperature range situations.
Fluid bearings can catastrophically seize under shock situations. Ball bearings deteriorate more gradually and provide acoustic symptoms.
Like cage frequency vibration in a ball bearing, the half frequency whirl is a bearing instability that generates eccentric precession
which can lead to poor performance and reduced life.
Fluid leakage; keeping fluid in the bearing can be a challenge.
Oil fluid bearings are impractical in environments where oil leakage can be destructive or where maintenance is not economical.
Fluid bearing "pads" often have to be used in pairs or triples to avoid the bearing from tilting and losing the fluid from one side.
s are a type of fluid dynamic air bearing that was introduced in high speed turbine applications in the 1960s by Garrett AiResearch
. They use a gas as the working fluid, usually air and require no external pressurisation system.
s but are arguably fluid bearings. For example, journal bearings in gasoline (petrol) and diesel engines pump oil at low pressure into a large-gap area of the bearing. As the bearing rotates, oil is carried into the working part of the bearing, where it is compressed, with oil viscosity preventing the oil's escape. As a result, the bearing hydroplanes on a layer of oil, rather than on metal-on-metal contact as it may appear.
This is an example of a fluid bearing which does not use a secondary bearing for start/stop. In this application, a large part of the bearing wear occurs during start-up and shutdown, though in engine use, substantial wear is also caused by hard combustion contaminants that bridge the oil film.
) utilizes a thin film of pressurized air to provide an exceedingly low friction load-bearing interface between surfaces. The two surfaces don't touch. Being non-contact, air bearings avoid the traditional bearing-related problems of friction, wear, particulates, and lubricant handling, and offer distinct advantages in precision positioning, such as lacking backlash and stiction, as well as in high-speed applications.
The fluid film of the bearing is air that flows through the bearing itself to the bearing surface. The design of the air bearing is such that, although the air constantly escapes from the bearing gap, the pressure between the faces of the bearing is enough to support the working loads.
is a game based on an aerostatic bearing which suspends the puck and player's paddles to provide low friction and thus fast motion. The bearing uses a flat plane with periodic orifices which deliver air just over ambient pressure. The puck and paddles rest on air.
Another example of a fluid bearing is ice skating
. Ice skates form a hydrodynamic fluid bearing where the skate and ice are separated by a layer of water caused by entropy
(formerly thought to be caused by pressure-induced melting; see ice skating
for details.)
and American tribologist
Albert Kingsbury
. Michell's patent was granted in 1905, while Kingsbury's first patent attempt was 1907. Kingsbury's patent was eventually granted in 1911 after he demonstrated that he had been working on the concept for many years. As stated by Sydney Walker, a long-time employee of Michell's, the granting of Kingsbury's patent was "a blow which Michell found hard to accept".
The bearing has sectional
shoes, or pads on pivots. When the bearing is in operation, the rotating part of the bearing carries fresh oil in to the pad area through viscous drag. Fluid pressure causes the pad to tilt slightly, creating a narrow constriction between the shoe and the other bearing surface. A wedge of pressurised fluid builds behind this constriction, separating the moving parts. The tilt of the pad adaptively changes with bearing load and speed. Various design details ensure continued replenishment of the oil to avoid overheating and pad damage.
Michell/Kingsbury fluid bearings are used in a wider variety of heavy-duty rotating equipment, including in hydroelectric plants to support turbines and generators weighing hundreds of tons. They are also used in very heavy machinery, such as marine
propeller shafts.
The first tilting pad bearing in service was probably that built under A.G.M. Michell's guidance by George Weymoth (Pty) Ltd, for a centrifugal pump
at Cohuna on the Murray River, Victoria, Australia, in 1907, just two years after Michell had published and patented his three-dimensional solution to Reynold's equation
. By 1913, the great merits of the tilting-pad bearing had been recognised for marine applications. The first English ship to be fitted out with the bearing was the cross-channel steamboat
the Paris, but many naval vessels were similarly equipped during the First World War. The practical results were spectacular - the troublesome thrust block
became dramatically smaller and lighter, significantly more efficient, and remarkably free from maintenance troubles. It was estimated that the Royal Navy saved coal to a value of £500,000 in 1918 alone as a result of fitting Michell's tilting-pad bearings.
According to the ASME
(see reference link), the first Michell/Kingsbury fluid bearing in the USA was installed in the Holtwood Hydroelectric Power Plant
(on the Susquehanna River
, near Lancaster, Pennsylvania
, USA) in 1912. The 2.25-tonne bearing supports a water turbine
and electric generator with a rotating mass of about 165 tonnes and water turbine pressure adding another 40 tonnes. The bearing has been in nearly continuous service since 1912, with no parts replaced. The ASME reported it was still in service as of 2000. As of 2002, the manufacturer estimated the bearings at Holtwood should have a maintenance-free life of about 1,300 years.
Bearing (mechanical)
A bearing is a device to allow constrained relative motion between two or more parts, typically rotation or linear movement. Bearings may be classified broadly according to the motions they allow and according to their principle of operation as well as by the directions of applied loads they can...
which support the bearing's loads solely on a thin layer of liquid or gas.
They can be broadly classified as fluid dynamic bearings or hydrostatic bearings. Hydrostatic bearings are externally pressurized fluid bearings, where the fluid is usually oil, water or air, and the pressurization is done by a pump. Hydrodynamic bearings rely on the high speed of the journal self-pressurizing the fluid in a wedge between the faces.
Fluid bearings are frequently used in high load, high speed or high precision applications where ordinary ball bearing
Ball bearing
A ball bearing is a type of rolling-element bearing that uses balls to maintain the separation between the bearing races.The purpose of a ball bearing is to reduce rotational friction and support radial and axial loads. It achieves this by using at least two races to contain the balls and transmit...
s have short life or high noise and vibration. They are also used increasingly to reduce cost. For example, hard disk
Hard disk
A hard disk drive is a non-volatile, random access digital magnetic data storage device. It features rotating rigid platters on a motor-driven spindle within a protective enclosure. Data is magnetically read from and written to the platter by read/write heads that float on a film of air above the...
drive motor fluid bearings are both quieter and cheaper than the ball bearings they replace.
Operation
Fluid bearings use a thin layer of liquid or gas fluidFluid
In physics, a fluid is a substance that continually deforms under an applied shear stress. Fluids are a subset of the phases of matter and include liquids, gases, plasmas and, to some extent, plastic solids....
between the bearing faces, typically sealed around or under the rotating shaft.
There are two principal ways of getting the fluid into the bearing:
- In fluid static, hydrostatic and many gas or air bearings, the fluid is pumped in through an orifice or through a porous material.
- In fluid-dynamic bearings, the bearing rotation sucks the fluid on to the inner surface of the bearing, forming a lubricating wedge under or around the shaft.
Hydrostatic bearings rely on an external pump. The power required by that pump contributes to system energy loss just as bearing friction otherwise would. Better seals can reduce leak rates and pumping power, but may increase friction.
Hydrodynamic bearings rely on bearing motion to suck fluid into the bearing and may have high friction and short life at speeds lower than design or during starts and stops. An external pump or secondary bearing may be used for startup and shutdown to prevent damage to the hydrodynamic bearing. A secondary bearing may have high friction and short operating life, but good overall service life if bearing starts and stops are infrequent.
Hydrodynamic lubrication
Hydrodynamic (HD) lubrication, also known as fluid film lubrication has essential elements:- A lubricantLubricantA lubricant is a substance introduced to reduce friction between moving surfaces. It may also have the function of transporting foreign particles and of distributing heat...
, which must be a viscous fluid. - Hydrodynamic flow behavior of fluid between bearingBearing (mechanical)A bearing is a device to allow constrained relative motion between two or more parts, typically rotation or linear movement. Bearings may be classified broadly according to the motions they allow and according to their principle of operation as well as by the directions of applied loads they can...
and journal. - The surfaces between which the fluid films move must be convergent.
Hydrodynamic (Full Film) Lubrication is obtained when two mating surfaces are completely separated by a cohesive film of lubricant.
The thickness of the film thus exceeds the combined roughness of the surfaces. The coefficient of friction is lower than with boundary-layer lubrication. Hydrodynamic lubrication prevents wear in moving parts, and metal to metal contact is prevented.
Hydrodynamic lubrication requires thin, converging fluid films. These fluids can be liquid or gas, so long as they exhibit viscosity. In computer components, like a hard disk
Hard disk
A hard disk drive is a non-volatile, random access digital magnetic data storage device. It features rotating rigid platters on a motor-driven spindle within a protective enclosure. Data is magnetically read from and written to the platter by read/write heads that float on a film of air above the...
, heads are supported by hydrodynamic lubrication in which the fluid film is the atmosphere.
The scale of these films are on the order of micrometers. Their convergence creates pressures normal to the surfaces they contact, forcing them apart.
3 Types of bearings include:
- Self-acting: Film exists due to relative motion.
- Squeeze film: Film exists due to relative normal motion.
- Externally pressurized: Film exists due to external pressurization.
Conceptually the bearings can be thought of as two major geometric classes: bearing-journal(Anti Friction), and plane-slider(Friction).
The Reynolds equations can be used to derive the governing principles for the fluids. Note that when gases are used, their derivation is much more involved.
The thin films can be thought to have pressure and viscous forces acting on them. Because there is a difference in velocity there will be a difference in the surface traction vectors. Because of mass conservation we can also assume an increase in pressure, making the body forces different.
Characteristics and principles of operation
Fluid bearings can be relatively cheap compared to other bearingBearing (mechanical)
A bearing is a device to allow constrained relative motion between two or more parts, typically rotation or linear movement. Bearings may be classified broadly according to the motions they allow and according to their principle of operation as well as by the directions of applied loads they can...
s with a similar load rating. The bearing can be as simple as two smooth surfaces with seals to keep in the working fluid. In contrast, a conventional rolling-element bearing
Rolling-element bearing
A rolling-element bearing, also known as a rolling bearing, is a bearing which carries a load by placing round elements between the two pieces...
may require many high-precision rollers with complicated shapes. Hydrostatic and many gas bearings do have the complication and expense of external pumps.
Most fluid bearings require little or no maintenance, and have almost unlimited life. Conventional rolling-element bearings usually have shorter life and require regular maintenance. Pumped hydrostatic and aerostatic (gas) bearing designs retain low friction down to zero speed and need not suffer start/stop wear, provided the pump does not fail.
Fluid bearings generally have very low friction—far better than mechanical bearings. One source of friction in a fluid bearing is the viscosity
Viscosity
Viscosity is a measure of the resistance of a fluid which is being deformed by either shear or tensile stress. In everyday terms , viscosity is "thickness" or "internal friction". Thus, water is "thin", having a lower viscosity, while honey is "thick", having a higher viscosity...
of the fluid. Hydrostatic gas bearings are among the lowest friction bearings. However, lower fluid viscosity also typically means fluid leaks faster from the bearing surfaces, thus requiring increased power for pumps or seals.
When a roller or ball is heavily loaded, fluid bearings have clearances that change less under load (are "stiffer") than mechanical bearings. It might seem that bearing stiffness, as with maximum design load, would be a simple function of average fluid pressure and the bearing surface area. In practice, when bearing surfaces are pressed together, the fluid outflow is constricted. This significantly increases the pressure of the fluid between the bearing faces. As fluid bearing faces can be comparatively larger than rolling surfaces, even small fluid pressure differences cause large restoring forces, maintaining the gap.
However, in lightly loaded bearings, such as disk drives, the typical ball bearing stiffnesses are ~10^7 MN/m. Comparable fluid bearings have stiffness of ~10^6 MN/m. Because of this, some fluid bearings, particularly hydrostatic bearings, are deliberately designed to pre-load the bearing to increase the stiffness.
Fluid bearings often inherently add significant damping. This helps attenuate resonances at the gyroscopic frequencies of journal bearings (sometimes called conical or rocking modes).
It is very difficult to make a mechanical bearing which is atomically smooth and round; and mechanical bearings deform in high-speed operation due to centripetal force
Centripetal force
Centripetal force is a force that makes a body follow a curved path: it is always directed orthogonal to the velocity of the body, toward the instantaneous center of curvature of the path. The mathematical description was derived in 1659 by Dutch physicist Christiaan Huygens...
. In contrast, fluid bearings self-correct for minor imperfections.
Fluid bearings are typically quieter and smoother (more consistent friction) than rolling-element bearings. For example, hard disk
Hard disk
A hard disk drive is a non-volatile, random access digital magnetic data storage device. It features rotating rigid platters on a motor-driven spindle within a protective enclosure. Data is magnetically read from and written to the platter by read/write heads that float on a film of air above the...
s manufactured with fluid bearings have noise ratings for bearings/motors on the order of 20-24 dB
Decibel
The decibel is a logarithmic unit that indicates the ratio of a physical quantity relative to a specified or implied reference level. A ratio in decibels is ten times the logarithm to base 10 of the ratio of two power quantities...
, which is a little more than the background noise of a quiet room. Drives based on rolling-element bearings are typically at least 4 dB noisier.
Fluid bearings can be made with a lower NRRO (non repeatable run out) than a ball or rolling element bearing. This can be critical in modern hard disk drive and ultra precision spindles.
Tilting pad bearings are used as radial bearings for supporting and locating shafts in compressors.
Disadvantages
Overall power consumption is typically higher compared to ball bearings.Power consumption and stiffness or damping greatly vary with temperature, which complicates the design and operation of a fluid bearing in wide temperature range situations.
Fluid bearings can catastrophically seize under shock situations. Ball bearings deteriorate more gradually and provide acoustic symptoms.
Like cage frequency vibration in a ball bearing, the half frequency whirl is a bearing instability that generates eccentric precession
Precession
Precession is a change in the orientation of the rotation axis of a rotating body. It can be defined as a change in direction of the rotation axis in which the second Euler angle is constant...
which can lead to poor performance and reduced life.
Fluid leakage; keeping fluid in the bearing can be a challenge.
Oil fluid bearings are impractical in environments where oil leakage can be destructive or where maintenance is not economical.
Fluid bearing "pads" often have to be used in pairs or triples to avoid the bearing from tilting and losing the fluid from one side.
Foil bearings
Foil bearingFoil bearing
Foil bearings, also known as foil-air bearings, are a type of air bearing. A shaft is supported by a compliant, spring-loaded foil journal lining. Once the shaft is spinning quickly enough, the working fluid pushes the foil away from the shaft so that there is no more contact...
s are a type of fluid dynamic air bearing that was introduced in high speed turbine applications in the 1960s by Garrett AiResearch
Garrett AiResearch
Garrett AiResearch was a manufacturer of turboprop engines and turbochargers, and a pioneer in numerous aerospace technologies. It was previously known as Aircraft Tool and Supply Company, Garrett Supply Company, AiResearch Manufacturing Company, or simply AiResearch...
. They use a gas as the working fluid, usually air and require no external pressurisation system.
Journal bearings
Pressure-oiled journal bearings appear to be plain bearingPlain bearing
A plain bearing, also known as a plane bearing or a friction bearing is the simplest type of bearing, comprising just a bearing surface and no rolling elements. Therefore the journal slides over the bearing surface. The simplest example of a plain bearing is a shaft rotating in a hole...
s but are arguably fluid bearings. For example, journal bearings in gasoline (petrol) and diesel engines pump oil at low pressure into a large-gap area of the bearing. As the bearing rotates, oil is carried into the working part of the bearing, where it is compressed, with oil viscosity preventing the oil's escape. As a result, the bearing hydroplanes on a layer of oil, rather than on metal-on-metal contact as it may appear.
This is an example of a fluid bearing which does not use a secondary bearing for start/stop. In this application, a large part of the bearing wear occurs during start-up and shutdown, though in engine use, substantial wear is also caused by hard combustion contaminants that bridge the oil film.
Air bearings
Unlike contact-roller bearings, an air bearing (or air casterAir caster
An air caster is a pneumatic lifting device used to move heavy loads on flat, non-porous surfaces. Its operation is similar to a hovercraft, as it uses a thin layer of air as a way to float a very small distance off the ground...
) utilizes a thin film of pressurized air to provide an exceedingly low friction load-bearing interface between surfaces. The two surfaces don't touch. Being non-contact, air bearings avoid the traditional bearing-related problems of friction, wear, particulates, and lubricant handling, and offer distinct advantages in precision positioning, such as lacking backlash and stiction, as well as in high-speed applications.
The fluid film of the bearing is air that flows through the bearing itself to the bearing surface. The design of the air bearing is such that, although the air constantly escapes from the bearing gap, the pressure between the faces of the bearing is enough to support the working loads.
Examples
Air hockeyAir hockey
Air hockey is a game for two competing players trying to score points in the opposing player's goal.-Equipment:Air hockey requires an air-hockey table, two player-held mallets, and a puck....
is a game based on an aerostatic bearing which suspends the puck and player's paddles to provide low friction and thus fast motion. The bearing uses a flat plane with periodic orifices which deliver air just over ambient pressure. The puck and paddles rest on air.
Another example of a fluid bearing is ice skating
Ice skating
Ice skating is moving on ice by using ice skates. It can be done for a variety of reasons, including leisure, traveling, and various sports. Ice skating occurs both on specially prepared indoor and outdoor tracks, as well as on naturally occurring bodies of frozen water, such as lakes and...
. Ice skates form a hydrodynamic fluid bearing where the skate and ice are separated by a layer of water caused by entropy
Entropy
Entropy is a thermodynamic property that can be used to determine the energy available for useful work in a thermodynamic process, such as in energy conversion devices, engines, or machines. Such devices can only be driven by convertible energy, and have a theoretical maximum efficiency when...
(formerly thought to be caused by pressure-induced melting; see ice skating
Ice skating
Ice skating is moving on ice by using ice skates. It can be done for a variety of reasons, including leisure, traveling, and various sports. Ice skating occurs both on specially prepared indoor and outdoor tracks, as well as on naturally occurring bodies of frozen water, such as lakes and...
for details.)
Michell/Kingsbury tilting-pad fluid bearings
Michell/Kingsbury fluid dynamic tilting-pad bearings were invented independently and almost simultaneously by both British-born Australian, Anthony George Maldon MichellAnthony Michell
Anthony George Maldon Michell FRS was an Australian mechanical engineer of the early 20th century.-Early life:...
and American tribologist
Tribology
Tribology is the science and engineering of interacting surfaces in relative motion. It includes the study and application of the principles of friction, lubrication and wear...
Albert Kingsbury
Albert Kingsbury
Albert Kingsbury [1] was an American engineer, inventor and entrepreneur. He was responsible for over fifty patents obtained between the years 1902 to 1930. [2] Kingsbury is most famous for his tilting pad thrust bearing which uses a thin film of oil to support weights of up to 220 tons...
. Michell's patent was granted in 1905, while Kingsbury's first patent attempt was 1907. Kingsbury's patent was eventually granted in 1911 after he demonstrated that he had been working on the concept for many years. As stated by Sydney Walker, a long-time employee of Michell's, the granting of Kingsbury's patent was "a blow which Michell found hard to accept".
The bearing has sectional
Circle
A circle is a simple shape of Euclidean geometry consisting of those points in a plane that are a given distance from a given point, the centre. The distance between any of the points and the centre is called the radius....
shoes, or pads on pivots. When the bearing is in operation, the rotating part of the bearing carries fresh oil in to the pad area through viscous drag. Fluid pressure causes the pad to tilt slightly, creating a narrow constriction between the shoe and the other bearing surface. A wedge of pressurised fluid builds behind this constriction, separating the moving parts. The tilt of the pad adaptively changes with bearing load and speed. Various design details ensure continued replenishment of the oil to avoid overheating and pad damage.
Michell/Kingsbury fluid bearings are used in a wider variety of heavy-duty rotating equipment, including in hydroelectric plants to support turbines and generators weighing hundreds of tons. They are also used in very heavy machinery, such as marine
Marine (ocean)
Marine is an umbrella term. As an adjective it is usually applicable to things relating to the sea or ocean, such as marine biology, marine ecology and marine geology...
propeller shafts.
The first tilting pad bearing in service was probably that built under A.G.M. Michell's guidance by George Weymoth (Pty) Ltd, for a centrifugal pump
Centrifugal pump
A centrifugal pump is a rotodynamic pump that uses a rotating impeller to create flow by the addition of energy to a fluid. Centrifugal pumps are commonly used to move liquids through piping...
at Cohuna on the Murray River, Victoria, Australia, in 1907, just two years after Michell had published and patented his three-dimensional solution to Reynold's equation
Reynolds-averaged Navier-Stokes equations
The Reynolds-averaged Navier–Stokes equations are time-averagedequations of motion for fluid flow. The idea behind the equations is Reynolds decomposition, whereby an instantaneous quantity is decomposed into its time-averaged and fluctuating quantities, an idea first proposed by Osborne Reynolds...
. By 1913, the great merits of the tilting-pad bearing had been recognised for marine applications. The first English ship to be fitted out with the bearing was the cross-channel steamboat
Steamboat
A steamboat or steamship, sometimes called a steamer, is a ship in which the primary method of propulsion is steam power, typically driving propellers or paddlewheels...
the Paris, but many naval vessels were similarly equipped during the First World War. The practical results were spectacular - the troublesome thrust block
Thrust block
A thrust block, also known as a thrust box, is a specialised form of thrust bearing used in ships, to resist the thrust of the propellor shaft and transmit it to the hull.- Early thrust boxes :...
became dramatically smaller and lighter, significantly more efficient, and remarkably free from maintenance troubles. It was estimated that the Royal Navy saved coal to a value of £500,000 in 1918 alone as a result of fitting Michell's tilting-pad bearings.
According to the ASME
American Society of Mechanical Engineers
The American Society of Mechanical Engineers is a professional body, specifically an engineering society, focused on mechanical engineering....
(see reference link), the first Michell/Kingsbury fluid bearing in the USA was installed in the Holtwood Hydroelectric Power Plant
Holtwood Dam
Holtwood Dam is the oldest of three major dams built across the lower Susquehanna River, and the middle location of the three. It was constructed as the McCalls Ferry Dam between 1905 and 1910 by the Pennsylvania Water & Power Company...
(on the Susquehanna River
Susquehanna River
The Susquehanna River is a river located in the northeastern United States. At long, it is the longest river on the American east coast that drains into the Atlantic Ocean, and with its watershed it is the 16th largest river in the United States, and the longest river in the continental United...
, near Lancaster, Pennsylvania
Lancaster Township, Lancaster County, Pennsylvania
Lancaster Township is a civil township of Lancaster County, Pennsylvania, in the United States. It is in the central area and it immediately surrounds Lancaster City...
, USA) in 1912. The 2.25-tonne bearing supports a water turbine
Water turbine
A water turbine is a rotary engine that takes energy from moving water.Water turbines were developed in the 19th century and were widely used for industrial power prior to electrical grids. Now they are mostly used for electric power generation. They harness a clean and renewable energy...
and electric generator with a rotating mass of about 165 tonnes and water turbine pressure adding another 40 tonnes. The bearing has been in nearly continuous service since 1912, with no parts replaced. The ASME reported it was still in service as of 2000. As of 2002, the manufacturer estimated the bearings at Holtwood should have a maintenance-free life of about 1,300 years.
External links
- ASME History Brochure about Kingsbury's Susquehanna Bearing
- A 91-page 10.6MB NASA technical handbook Lubrication of Machine Elements, NASA-RP-1126 by B.J.Hamrock, 1984 here.
- Kinematic Models for Design Digital Library (KMODDL) - Movies and photos of hundreds of working mechanical-systems models at Cornell University. Also includes an e-book library of classic texts on mechanical design and engineering.