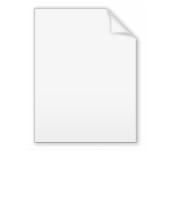
Exoskeletal engine
Encyclopedia
The exoskeletal engine concept represents a paradigm shift
in turbomachinery
design. Current gas turbine
engines have central rotating shafts and discs and are constructed mostly from heavy metals. They require lubricated bearings and need extensive cooling for hot components. They are also subject to severe imbalance (or vibrations) that could wipe out the whole rotor
stage, are prone to high- and low-cycle fatigue, and subject to catastrophic failure due to disc bursts from high tensile loads, consequently requiring heavy containment devices. To address these limitations, the ESE concept turns the conventional configuration inside-out and utilizes a drum-type rotor design for the turbomachinery in which the rotor blades are attached to the inside of a rotating drum instead of radially outwards from a shaft and discs. Multiple drum rotors could be used in a multi-spool design.
Fundamentally, the ESE drum-rotor configuration typically consists of four concentric
open-ended drums or shells:
In the ESE design, the rotating blades are primarily in radial compression as opposed to radial tension, which means that materials that do not possess high-tensile strength, such as ceramic materials
, can be used for their construction. Ceramics behave well in compressive loading situations where brittle fracture
is minimized, and would provide greater operating efficiency through higher operating temperature
s and lighter engine weight when compared to the metal alloy
s that typically are used in turbomachinery components. The ESE design and the use of composite materials could also reduce the part count, reduce or eliminate cooling, and result in increased component life. The use of ceramics would also be a beneficial feature for hypersonic
propulsion
systems, where high stagnation temperature
s can exceed the limits of traditional turbomachinery materials.
The cavity within the inner shell could be exploited in several different ways. In subsonic applications, venting the centre cavity with a free-stream flow could potentially contribute to a large noise reduction; while in supersonic
-hypersonic applications it might be used to house a ramjet
or scramjet
(or other devices such as a pulse-detonation engine) as part of a turbine-based combined-cycle engine. Such an arrangement could reduce the overall length of the propulsion system and thereby reduce weight and drag significantly.
handle the magnitude of velocity encountered in the ESE; foil- and magnetic bearing
s have been suggested as possible solutions to this problem.
Although both systems theoretically meet the requirements of the exoskeletal application, neither technology is currently ready for operation at this size. Developments in foil bearing technology indicate it may take 20 years to achieve foil bearings for this diameter, and magnetic bearings appear to be too heavy for this application and would also face a lengthy technology
development programme.
Paradigm shift
A Paradigm shift is, according to Thomas Kuhn in his influential book The Structure of Scientific Revolutions , a change in the basic assumptions, or paradigms, within the ruling theory of science...
in turbomachinery
Turbomachinery
Turbomachinery, in mechanical engineering, describes machines that transfer energy between a rotor and a fluid, including both turbines and compressors. While a turbine transfers energy from a fluid to a rotor, a compressor transfers energy from a rotor to a fluid...
design. Current gas turbine
Gas turbine
A gas turbine, also called a combustion turbine, is a type of internal combustion engine. It has an upstream rotating compressor coupled to a downstream turbine, and a combustion chamber in-between....
engines have central rotating shafts and discs and are constructed mostly from heavy metals. They require lubricated bearings and need extensive cooling for hot components. They are also subject to severe imbalance (or vibrations) that could wipe out the whole rotor
Turbine
A turbine is a rotary engine that extracts energy from a fluid flow and converts it into useful work.The simplest turbines have one moving part, a rotor assembly, which is a shaft or drum with blades attached. Moving fluid acts on the blades, or the blades react to the flow, so that they move and...
stage, are prone to high- and low-cycle fatigue, and subject to catastrophic failure due to disc bursts from high tensile loads, consequently requiring heavy containment devices. To address these limitations, the ESE concept turns the conventional configuration inside-out and utilizes a drum-type rotor design for the turbomachinery in which the rotor blades are attached to the inside of a rotating drum instead of radially outwards from a shaft and discs. Multiple drum rotors could be used in a multi-spool design.
Fundamentally, the ESE drum-rotor configuration typically consists of four concentric
Concentric
Concentric objects share the same center, axis or origin with one inside the other. Circles, tubes, cylindrical shafts, disks, and spheres may be concentric to one another...
open-ended drums or shells:
- an outer shell (engine casing) that both supports the bearings for the drum-rotor shell and constrains it,
- the drum-rotor shell that rotates within the bearings and carries the compressor- and turbine blades,
- a static statorStatorThe stator is the stationary part of a rotor system, found in an electric generator, electric motor and biological rotors.Depending on the configuration of a spinning electromotive device the stator may act as the field magnet, interacting with the armature to create motion, or it may act as the...
shell that supports the guide vanes, - a hollow static inner shell that provides a flow path through the centre of the engine.
In the ESE design, the rotating blades are primarily in radial compression as opposed to radial tension, which means that materials that do not possess high-tensile strength, such as ceramic materials
Ceramic materials
Ceramic materials are inorganic, non-metallic materials and things made from them. They may be crystalline or partly crystalline. They are formed by the action of heat and subsequent cooling...
, can be used for their construction. Ceramics behave well in compressive loading situations where brittle fracture
Fracture
A fracture is the separation of an object or material into two, or more, pieces under the action of stress.The word fracture is often applied to bones of living creatures , or to crystals or crystalline materials, such as gemstones or metal...
is minimized, and would provide greater operating efficiency through higher operating temperature
Operating temperature
An operating temperature is the temperature at which an electrical or mechanical device operates. The device will operate effectively within a specified temperature range which varies based on the device function and application context, and ranges from the minimum operating temperature to the...
s and lighter engine weight when compared to the metal alloy
Alloy
An alloy is a mixture or metallic solid solution composed of two or more elements. Complete solid solution alloys give single solid phase microstructure, while partial solutions give two or more phases that may or may not be homogeneous in distribution, depending on thermal history...
s that typically are used in turbomachinery components. The ESE design and the use of composite materials could also reduce the part count, reduce or eliminate cooling, and result in increased component life. The use of ceramics would also be a beneficial feature for hypersonic
Hypersonic
In aerodynamics, a hypersonic speed is one that is highly supersonic. Since the 1970s, the term has generally been assumed to refer to speeds of Mach 5 and above...
propulsion
Vehicle propulsion
Vehicle propulsion refers to the act of moving an artificial carrier of people or goods over any distance. The power plant used to drive the vehicles can vary widely. Originally, humans or animals would have provided the propulsion system, later being supplemented by wind power...
systems, where high stagnation temperature
Stagnation temperature
In thermodynamics and fluid mechanics, stagnation temperature is the temperature at a stagnation point in a fluid flow. At a stagnation point the speed of the fluid is zero and all of the kinetic energy has been converted to internal energy and is added to the local static enthalpy...
s can exceed the limits of traditional turbomachinery materials.
The cavity within the inner shell could be exploited in several different ways. In subsonic applications, venting the centre cavity with a free-stream flow could potentially contribute to a large noise reduction; while in supersonic
Supersonic
Supersonic speed is a rate of travel of an object that exceeds the speed of sound . For objects traveling in dry air of a temperature of 20 °C this speed is approximately 343 m/s, 1,125 ft/s, 768 mph or 1,235 km/h. Speeds greater than five times the speed of sound are often...
-hypersonic applications it might be used to house a ramjet
Ramjet
A ramjet, sometimes referred to as a stovepipe jet, or an athodyd, is a form of airbreathing jet engine using the engine's forward motion to compress incoming air, without a rotary compressor. Ramjets cannot produce thrust at zero airspeed and thus cannot move an aircraft from a standstill...
or scramjet
Scramjet
A scramjet is a variant of a ramjet airbreathing jet engine in which combustion takes place in supersonic airflow...
(or other devices such as a pulse-detonation engine) as part of a turbine-based combined-cycle engine. Such an arrangement could reduce the overall length of the propulsion system and thereby reduce weight and drag significantly.
Summarized potential advantages
From Chamis and Blankson:- Eliminate disk and bore stresses
- Utilize low-stress bearings
- Increase rotor speed
- Reduce airfoil thickness
- Increase flutter boundaries
- Minimize/eliminate containment requirements
- Increase high mass flow rate
- Reduce weight by 50 percent
- Decrease turbine temperature for same thrust
- Decrease emissions
- Provide higher thrust-to-weight ratioThrust-to-weight ratioThrust-to-weight ratio is a ratio of thrust to weight of a rocket, jet engine, propeller engine, or a vehicle propelled by such an engine. It is a dimensionless quantity and is an indicator of the performance of the engine or vehicle....
- Improve specific fuel consumption
- Increase blade low-cycle and high-cycle fatigue lives
- Reduce engine diameter
- Reduce parts count
- Decrease maintenance cost
- Minimize/eliminate sealing and cooling requirements
- Minimize/eliminate blade-flow losses, blade and case wear
- Free core for combined turboram jet cycles
- Reduce noise
- Expedite aircraft/engine integration
- Minimize/eliminate notch-sensitiveCharpy impact testThe Charpy impact test, also known as the Charpy v-notch test, is a standardized high strain-rate test which determines the amount of energy absorbed by a material during fracture. This absorbed energy is a measure of a given material's toughness and acts as a tool to study temperature-dependent...
material issues
Challenges
One of the major challenges is in bearing design as there are no known lubricated systems that canhandle the magnitude of velocity encountered in the ESE; foil- and magnetic bearing
Magnetic bearing
A magnetic bearing is a bearing which supports a load using magnetic levitation. Magnetic bearings support moving machinery without physical contact; for example, they can levitate a rotating shaft and permit relative motion with very low friction and no mechanical wear...
s have been suggested as possible solutions to this problem.
- Foil bearings are noncontacting and ride on a thin film of air, which is generated hydrodynamicallyFluid dynamicsIn physics, fluid dynamics is a sub-discipline of fluid mechanics that deals with fluid flow—the natural science of fluids in motion. It has several subdisciplines itself, including aerodynamics and hydrodynamics...
by the rotational speed, to suspend and centre the shaft. Drawbacks for the foil system include the high start-up torque, the need for set-down/lift-off mechanical bearings and associated positioning hardware, and the high temperatures generated by this system. - For the large-diameter magnetic bearing system required in the ESE, stiffness and radial growth after spin-up are problems that would be encountered. Radial growth of sufficient magnitude would result in stability problems, and a magnet pole positioning system would be required to maintain the appropriate clearances for the operation of the system. This positioning system would require high-speed sensing and positioning. A passive magnetic laminate and its mounting hardware would require high structural integrity to resist the extremely high inertial forces and would most likely drive an increase in weight.
Although both systems theoretically meet the requirements of the exoskeletal application, neither technology is currently ready for operation at this size. Developments in foil bearing technology indicate it may take 20 years to achieve foil bearings for this diameter, and magnetic bearings appear to be too heavy for this application and would also face a lengthy technology
development programme.