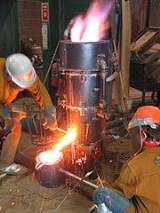
Cupola furnace
Encyclopedia
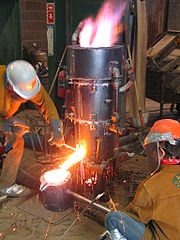
Cast iron
Cast iron is derived from pig iron, and while it usually refers to gray iron, it also identifies a large group of ferrous alloys which solidify with a eutectic. The color of a fractured surface can be used to identify an alloy. White cast iron is named after its white surface when fractured, due...
, ni-resist iron and some bronze
Bronze
Bronze is a metal alloy consisting primarily of copper, usually with tin as the main additive. It is hard and brittle, and it was particularly significant in antiquity, so much so that the Bronze Age was named after the metal...
s. The cupola can be made almost any practical size. The size of a cupola is expressed in diameters and can range from 1.5 to 13 ft (0.4572 to 4 ). The overall shape is cylindrical and the equipment is arranged vertically, usually supported by four legs. The overall look is similar to a large smokestack.
The bottom of the cylinder is fitted with doors which swing down and out to 'drop bottom'. The top where gases escape can be open or fitted with a cap to prevent rain from entering the cupola. To control emissions
Air pollution
Air pollution is the introduction of chemicals, particulate matter, or biological materials that cause harm or discomfort to humans or other living organisms, or cause damage to the natural environment or built environment, into the atmosphere....
a cupola may be fitted with a cap that is designed to pull the gases into a device to cool the gasses and remove particulate matter.
The shell of the cupola, being usually made of steel, has refractory brick and refractory
Refractory
A refractory material is one that retains its strength at high temperatures. ASTM C71 defines refractories as "non-metallic materials having those chemical and physical properties that make them applicable for structures, or as components of systems, that are exposed to environments above...
patching material lining it. The bottom is lined in a similar manner but often a clay and sand mixture ("bod") may be used, as this lining is temporary. Finely divided coal ("sea coal") can be mixed with the clay lining so when heated the coal decomposes and the bod becomes slightly friable, easing the opening up of the tap holes. The bottom lining is compressed or 'rammed' against the bottom doors. Some cupolas are fitted with cooling jackets to keep the sides cool and with oxygen injection to make the coke
Coke (fuel)
Coke is the solid carbonaceous material derived from destructive distillation of low-ash, low-sulfur bituminous coal. Cokes from coal are grey, hard, and porous. While coke can be formed naturally, the commonly used form is man-made.- History :...
fire burn hotter.
History
The first known cupola furnace was made by René-Antoine Ferchault de Réaumur around 1720, though evidence suggests that this technique was in use in China as far back as the 3rd and 2nd centuries BC.Operation
To begin a production run, called a 'cupola campaign', the furnace is filled with layers of coke and ignited with torches. Some smaller cupolas may be ignited with wood to start the coke burning. When the coke is ignited, air is introduced to the coke bed through ports in the sides called tuyeres.When the coke is very hot, solid pieces of metal are charged into the furnace through an opening in the top. The metal is alternated with additional layers of fresh coke. Limestone
Limestone
Limestone is a sedimentary rock composed largely of the minerals calcite and aragonite, which are different crystal forms of calcium carbonate . Many limestones are composed from skeletal fragments of marine organisms such as coral or foraminifera....
is added to act as a flux
Flux (metallurgy)
In metallurgy, a flux , is a chemical cleaning agent, flowing agent, or purifying agent. Fluxes may have more than one function at a time...
. As the heat rises within the stack the metal is melted. It drips down through the coke bed to collect in a pool at the bottom, just above the bottom doors. During the melting proses a thermodynamic reaction takes place between the fuel and the blast air. The carbon
Carbon
Carbon is the chemical element with symbol C and atomic number 6. As a member of group 14 on the periodic table, it is nonmetallic and tetravalent—making four electrons available to form covalent chemical bonds...
in the coke combines with the oxygen in the air to form carbon monoxide
Carbon monoxide
Carbon monoxide , also called carbonous oxide, is a colorless, odorless, and tasteless gas that is slightly lighter than air. It is highly toxic to humans and animals in higher quantities, although it is also produced in normal animal metabolism in low quantities, and is thought to have some normal...
. The carbon monoxide further burns to form carbon dioxide
Carbon dioxide
Carbon dioxide is a naturally occurring chemical compound composed of two oxygen atoms covalently bonded to a single carbon atom...
. Some of the carbon is picked up by the falling droplets of molten metal which raises the carbon content of the iron. Silicon carbide
Silicon carbide
Silicon carbide , also known as carborundum, is a compound of silicon and carbon with chemical formula SiC. It occurs in nature as the extremely rare mineral moissanite. Silicon carbide powder has been mass-produced since 1893 for use as an abrasive...
and ferromanganese
Ferromanganese
Ferromanganese, a ferroalloy with high content of manganese, is made by heating a mixture of the oxides MnO2 and Fe2O3, with carbon, usually as coal and coke, in either a blast furnace or an electric arc furnace-type system, called a submerged arc furnace. The oxides undergo carbothermal reduction...
briquettes may also be added to the charge materials. The silicon carbide dissociates and carbon and silicon enters into the molten metal. Likewise the ferromanganese melts and is combined into the pool of liquid iron in the 'well' at the bottom of the cupola. Additions to the molten iron such as ferromanganese
Ferromanganese
Ferromanganese, a ferroalloy with high content of manganese, is made by heating a mixture of the oxides MnO2 and Fe2O3, with carbon, usually as coal and coke, in either a blast furnace or an electric arc furnace-type system, called a submerged arc furnace. The oxides undergo carbothermal reduction...
, ferrosilicon
Ferrosilicon
Ferrosilicon, or ferrosilicium, is a ferroalloy, an alloy of iron and silicon with between 15% and 90% silicon. It contains a high proportion of iron silicides. Its melting point is about 1200 °C to 1250 °C with a boiling point of 2355 °C...
, Silicon carbide
Silicon carbide
Silicon carbide , also known as carborundum, is a compound of silicon and carbon with chemical formula SiC. It occurs in nature as the extremely rare mineral moissanite. Silicon carbide powder has been mass-produced since 1893 for use as an abrasive...
and other alloying agents are used to alter the molten iron to conform to the needs of the castings at hand.
The operator of the cupola is known as the 'Cupola Tender' or "Furnace Master".
During the operation of a tapped cupola (cupolas may vary in this regard)the tender observes the amount of iron rising in the well of the cupola. When the metal level is sufficiently high, the cupola tender opens the "tap hole" to let the metal flow into a ladle
Ladle (metallurgy)
In a foundry, a ladle is a vessel used to transport and pour out molten metals. Ladles range in size from small hand carried vessels that resemble a kitchen ladle and hold or to large steelmill ladles that hold up to...
or other container to hold the molten metal. When enough metal is drawn off the "tap hole" is plugged with a refractory plug made of clay.
The cupola tender observes the furnace through the sight glass
Sight glass
A sight glass or water gauge is a transparent tube through which the operator of a tank or boiler can observe the level of liquid contained within.-Liquid in tanks:...
or peep sight in the tuyeres. Slag will rise to the top of the pool of iron being formed. A slag hole, located higher up on the cylinder of the furnace, and usually to the rear or side of the tap hole, is opened to let the slag flow out. The viscosity
Viscosity
Viscosity is a measure of the resistance of a fluid which is being deformed by either shear or tensile stress. In everyday terms , viscosity is "thickness" or "internal friction". Thus, water is "thin", having a lower viscosity, while honey is "thick", having a higher viscosity...
is low (with proper fluxing) and the red hot molten slag will flow easily. Sometimes the slag which runs out the slag hole is collected in a small cup shaped tool, allowed to cool and harden. It is fractured and visually examined. With acid refractory lined cupolas a greenish colored slag means the fluxing is proper and adequate. In basic refractory lined cupolas the slag is brown.
After the cupola has produced enough metal to supply the foundry with its needs, the bottom is opened, or 'dropped' and the remaining materials fall to the floor between the legs. This material is allowed to cool and subsequently removed. The cupola can be used over and over. A 'campaign' may last a few hours, a day, weeks or even months.
When the operation is over, the blast is shut off and the prop under the bottom door is knocked down so that the bottom plates swing open. This enables the cupola remains to drop to the floor or into a bucket. They are then quenched and removed from underneath the cupola.
Quality Control
During the production, samples may be taken from the metal and poured into small molds. A chill wedge is often poured to monitor the iron quality. These small, approx 18 mm (3/4") wide x 38 mm (1-12") tall triangular shaped pieces are allowed to cool until the metal has solidified. They are then extracted from the sand mold and quenched in water, wide end first. After cooling in the manned the wedges are fractured and the metal coloration is assessed. A typical fracture will have a whitish color towards the thin area of the wedge and grayish color towards the wide end. The width of the wedge at the point of demarcation between the white and gray areas is measured and compared to normal results for particular iron tensile strengthTensile strength
Ultimate tensile strength , often shortened to tensile strength or ultimate strength, is the maximum stress that a material can withstand while being stretched or pulled before necking, which is when the specimen's cross-section starts to significantly contract...
s. This visual method serves as a control measurement.