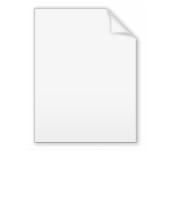
Booster pump
Encyclopedia
A Booster pump is a machine which will increase the pressure
of a gas
. It is similar to a gas compressor
, but generally a simpler mechanism which often has only a single stage of compression, and is used to increase pressure of an already pressurised gas. Two-stage boosters are also made.
Boosters may be used for increasing gas pressure, transferring high pressure gas, charging gas cylinder
s and scavenging.
of the booster is reached, after which no further increase in pressure from the supply pressure is possible. Pressure ratios of boosters may range from 6:1 upwards and are limited by the ratio of swept volume to dead volume.
or plunger type compressors. A single acting, single stage booster is the simplest configuration, and comprises a cylinder, designed to withstand the operating pressures, with a piston which is driven back and forth inside the cylinder. The cylinder head is fitted with supply and discharge ports, to which the supply and discharge hoses or pipes are connected, with a non-return valve on each, constraining flow in one direction from supply to discharge. When the booster is inactive, and the piston is stationary, gas will flow from the inlet hose, through the inlet valve into the space between the cylinder head and the piston. If the pressure in the outlet hose is lower, it will then flow out and to whatever the outlet hose is connected to. This flow will stop when the pressure is equalised, taking valve opening pressures into account.
Once the flow has stopped, the booster is started, and as the piston withdraws along the cylinder, increasing the volume between the cylinder head and the piston crown, the pressure in the cylinder will drop, and gas will flow in fron the inlet port. On the return cycle, the piston moves toward the cylinder head, decreasing the volume of the space and compressing the gas until the pressure is sufficient to overcome the pressure in the outlet line and the opening pressure of the outlet valve. At this point the gas will flow out of the cylinder via the outlet valve and port.
There will always be some compressed gas remaining in the cylinder and cylinder head spaces at the top of the stroke. The gas in this "dead space" will expand during the next induction stroke, and only after it has dropped below the supply gas pressure, more supply gas will flow into the cylinder. The ratio of the volume of the cylinder space with the piston fully withdrawn, to the dead space, is the "compression ratio" of the booster, also termed "boost ratio" in this context. Efficiency of the booster is related to the compression ratio, and gas will only be tranferred while the pressure ratio between supply and discharge gas is less than the boost ratio, and delivery rate will drop as the inlet to delivery pressure ratio increases.
Delivery rate starts at very close to swept volume when there is no pressure difference, and drops steadily until there is no effective transfer when the pressure ratio reaches the maximum boost ratio.
Compression of gas will cause a rise in temperature. The heat is mostly carried out by the compressed gas, but the booster components will also be heated by contact with the hot gas. Some boosters are cooled by water jackets or external fins to increase convectional cooling by the ambient air, but smaller models may have no special cooling facilities at all. Cooling arrangements will improve efficiency, but will cost more to manufacture.
Boosters to be used with oxygen must be made from oxygen compatible materials, and use oxygen compatible lubricants to avoid fire.
, hydraulics
, low or high pressure air or manually by a lever system. Those powered by compressed air
are usually linear actuated systems, where a pneumatic cylinder directly drives the compression piston, often in a common housing, separated by a seal. A high pressure pneumatic drive arrangement may use the same pressure as the output pressure to drive the piston, and a low pressure drive will use a larger diameter piston to multiply the applied force.
and surplus examples are now used by technical divers
as they are relatively inexpensive and are supplied with a comprehensive spares and tool kit.
Pressure
Pressure is the force per unit area applied in a direction perpendicular to the surface of an object. Gauge pressure is the pressure relative to the local atmospheric or ambient pressure.- Definition :...
of a gas
Gas
Gas is one of the three classical states of matter . Near absolute zero, a substance exists as a solid. As heat is added to this substance it melts into a liquid at its melting point , boils into a gas at its boiling point, and if heated high enough would enter a plasma state in which the electrons...
. It is similar to a gas compressor
Gas compressor
A gas compressor is a mechanical device that increases the pressure of a gas by reducing its volume.Compressors are similar to pumps: both increase the pressure on a fluid and both can transport the fluid through a pipe. As gases are compressible, the compressor also reduces the volume of a gas...
, but generally a simpler mechanism which often has only a single stage of compression, and is used to increase pressure of an already pressurised gas. Two-stage boosters are also made.
Boosters may be used for increasing gas pressure, transferring high pressure gas, charging gas cylinder
Gas cylinder
A gas cylinder is a pressure vessel used to store gases at above atmospheric pressure. High pressure gas cylinders are also called bottles. Although they are sometimes colloquially called "tanks", this is technically incorrect, as a tank is a vessel used to store liquids at ambient pressure and...
s and scavenging.
Operation
A booster pump may be used to pressurise gas cylinders to a higher pressure than would be otherwise possible when decanting from other cylinders. The gas would be decanted through the booster, which has non-return valves allowing flow when not activated, and when the pressures in the supply and destination cylinders have equalised, the booster is operated and pumps more gas through until either the desired pressure is reached, or the pressure ratioPressure ratio
Articles on Pressure ratio include:* Compression ratio, for piston engines* Overall pressure ratio, for gas turbine engines* Pressure ratio may also refer to the compression ratio of a gas compressor...
of the booster is reached, after which no further increase in pressure from the supply pressure is possible. Pressure ratios of boosters may range from 6:1 upwards and are limited by the ratio of swept volume to dead volume.
Construction and function
Booster pumps are usually pistonReciprocating compressor
A reciprocating compressor or piston compressor is a positive-displacement compressor that uses pistons driven by a crankshaft to deliver gases at high pressure....
or plunger type compressors. A single acting, single stage booster is the simplest configuration, and comprises a cylinder, designed to withstand the operating pressures, with a piston which is driven back and forth inside the cylinder. The cylinder head is fitted with supply and discharge ports, to which the supply and discharge hoses or pipes are connected, with a non-return valve on each, constraining flow in one direction from supply to discharge. When the booster is inactive, and the piston is stationary, gas will flow from the inlet hose, through the inlet valve into the space between the cylinder head and the piston. If the pressure in the outlet hose is lower, it will then flow out and to whatever the outlet hose is connected to. This flow will stop when the pressure is equalised, taking valve opening pressures into account.
Once the flow has stopped, the booster is started, and as the piston withdraws along the cylinder, increasing the volume between the cylinder head and the piston crown, the pressure in the cylinder will drop, and gas will flow in fron the inlet port. On the return cycle, the piston moves toward the cylinder head, decreasing the volume of the space and compressing the gas until the pressure is sufficient to overcome the pressure in the outlet line and the opening pressure of the outlet valve. At this point the gas will flow out of the cylinder via the outlet valve and port.
There will always be some compressed gas remaining in the cylinder and cylinder head spaces at the top of the stroke. The gas in this "dead space" will expand during the next induction stroke, and only after it has dropped below the supply gas pressure, more supply gas will flow into the cylinder. The ratio of the volume of the cylinder space with the piston fully withdrawn, to the dead space, is the "compression ratio" of the booster, also termed "boost ratio" in this context. Efficiency of the booster is related to the compression ratio, and gas will only be tranferred while the pressure ratio between supply and discharge gas is less than the boost ratio, and delivery rate will drop as the inlet to delivery pressure ratio increases.
Delivery rate starts at very close to swept volume when there is no pressure difference, and drops steadily until there is no effective transfer when the pressure ratio reaches the maximum boost ratio.
Compression of gas will cause a rise in temperature. The heat is mostly carried out by the compressed gas, but the booster components will also be heated by contact with the hot gas. Some boosters are cooled by water jackets or external fins to increase convectional cooling by the ambient air, but smaller models may have no special cooling facilities at all. Cooling arrangements will improve efficiency, but will cost more to manufacture.
Boosters to be used with oxygen must be made from oxygen compatible materials, and use oxygen compatible lubricants to avoid fire.
Power sources
Boosters may be driven by an electric motorElectric motor
An electric motor converts electrical energy into mechanical energy.Most electric motors operate through the interaction of magnetic fields and current-carrying conductors to generate force...
, hydraulics
Hydraulics
Hydraulics is a topic in applied science and engineering dealing with the mechanical properties of liquids. Fluid mechanics provides the theoretical foundation for hydraulics, which focuses on the engineering uses of fluid properties. In fluid power, hydraulics is used for the generation, control,...
, low or high pressure air or manually by a lever system. Those powered by compressed air
Compressed air
Compressed air is air which is kept under a certain pressure, usually greater than that of the atmosphere. In Europe, 10 percent of all electricity used by industry is used to produce compressed air, amounting to 80 terawatt hours consumption per year....
are usually linear actuated systems, where a pneumatic cylinder directly drives the compression piston, often in a common housing, separated by a seal. A high pressure pneumatic drive arrangement may use the same pressure as the output pressure to drive the piston, and a low pressure drive will use a larger diameter piston to multiply the applied force.
Manufacturers
Boosters are manufactured by Haskel, Draeger and others. Rugged and unsophisticated models (KN-3 and KN-4) were manufactured for the Soviet Armed ForcesSoviet Armed Forces
The Soviet Armed Forces, also called the Armed Forces of the Union of Soviet Socialist Republics and Armed Forces of the Soviet Union refers to the armed forces of the Russian SFSR , and Soviet Union from their beginnings in the...
and surplus examples are now used by technical divers
Technical diving
Technical diving is a form of scuba diving that exceeds the scope of recreational diving...
as they are relatively inexpensive and are supplied with a comprehensive spares and tool kit.