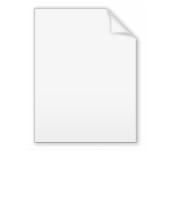
Artificial lift
Encyclopedia
Artificial lift refers to the use of artificial means to increase the flow of liquids, such as crude oil or water, from a production well. Generally this is achieved by the use of a mechanical device inside the well (known as pump
or velocity string) or by decreasing the weight of the hydrostatic column by injecting gas into the liquid some distance down the well. Artificial lift is needed in wells when there is insufficient pressure in the reservoir to lift the produced fluids to the surface, but often used in naturally flowing wells (which do not technically need it) to increase the flow rate above what would flow naturally. The produced fluid can be oil, water or a mix of oil and water, typically mixed with some amount of gas.
Most oil production reservoirs have sufficient potential to naturally produce oil and gas - which are light - during the early phases of production. Water - which is heavier than oil and much heavier than gas - will eventually encroach into production, and reservoir pressure will decrease as the reservoir depletes, naturally causing all wells to stop flowing. At some point, most well operators will implement an artificial lift plan to continue or increase production. Most water-producing wells, by contrast, will need artificial lift from the very beginning of production because they do not benefit from the lighter density of oil and gas.
These systems are very versatile and have been used in shallow depths (1000 ft) to deeper wells (18,000 ft), low rate wells with production in the tens of barrels per day to wells producing in excess of 10000 barrels (1,589.9 m³) per day. Certain substances can be mixed in with the injected fluid to help deal or control with corrosion, paraffin and emulsion problems. Hydraulic pumping systems are also suitable for deviated wells where conventional pumps such as the rod pump
are not feasible.
These systems have also some disadvantages. They are sensitive to solids and are the least efficient lift method.
While typically the cost of deploying these systems has been very high, new coiled tubing
umbilical technologies are in some cases greatly reducing the cost.
Although latest developments are aimed to enhance the ESP capabilities to handle gas and sand, they still need more technological development to avoid gas locks and internal erosion. Until recently, ESPs have come with an often prohibitive price tag due to the cost of deployment which can be in excess of $20,000.
Gas lifted wells are equipped with side pocket mandrels and gas lift injection valves. This arrangement allows a deeper gas injection in the tubing. The gas lift system has some disadvantages. There has to be a source of gas, some flow assurance problems such as hydrates can be triggered by the gas lift.
, PCP, are also widely applied in the oil industry. The PCP consists of a stator
and a rotor
. The rotor is rotated using either a top side motor or a bottom hole motor. The rotation created sequential cavities and the produced fluids are pushed to surface.
The PCP is a flexible system with a wide range of applications in terms of rate( up to 5000 oilbbl/d and 6000 ft (1,828.8 m)). They offer outstanding resistance to abrasives and solids but they are restricted to setting depths and temperatures. Some components of the produced fluids like aromatics can also deteriorate the stator’s elastomer.
Pump
A pump is a device used to move fluids, such as liquids, gases or slurries.A pump displaces a volume by physical or mechanical action. Pumps fall into three major groups: direct lift, displacement, and gravity pumps...
or velocity string) or by decreasing the weight of the hydrostatic column by injecting gas into the liquid some distance down the well. Artificial lift is needed in wells when there is insufficient pressure in the reservoir to lift the produced fluids to the surface, but often used in naturally flowing wells (which do not technically need it) to increase the flow rate above what would flow naturally. The produced fluid can be oil, water or a mix of oil and water, typically mixed with some amount of gas.
Usage
Any liquid-producing reservoir will have a 'reservoir pressure': some level of energy or potential that will force fluid (liquid, gas or both) to areas of lower energy or potential. The concept is similar to that of water pressure in a municipal water system. As soon as the pressure inside a production well is decreased below the reservoir pressure, the reservoir will act to fill the well back up, just like opening a valve on a water system. Depending on the depth of the reservoir and density of the fluid, the reservoir may or may not have enough potential to push the fluid to the surface - a deeper well or a heavier mixture results in a higher pressure requirement.Most oil production reservoirs have sufficient potential to naturally produce oil and gas - which are light - during the early phases of production. Water - which is heavier than oil and much heavier than gas - will eventually encroach into production, and reservoir pressure will decrease as the reservoir depletes, naturally causing all wells to stop flowing. At some point, most well operators will implement an artificial lift plan to continue or increase production. Most water-producing wells, by contrast, will need artificial lift from the very beginning of production because they do not benefit from the lighter density of oil and gas.
Hydraulic pumping systems
Hydraulic pumping systems transmit energy to the bottom of the well by means of pressurized power fluid that flows down in the wellbore tubular to a subsurface pump. There are two types of hydraulic subsurface pump:- a reciprocating piston pump, where one side is powered by the injected fluid while the other side pumps the produced fluids to surface
- a jet pump, where the injected fluid passes through a nozzle creating a venturi effect pushing the produced fluids to surface.
These systems are very versatile and have been used in shallow depths (1000 ft) to deeper wells (18,000 ft), low rate wells with production in the tens of barrels per day to wells producing in excess of 10000 barrels (1,589.9 m³) per day. Certain substances can be mixed in with the injected fluid to help deal or control with corrosion, paraffin and emulsion problems. Hydraulic pumping systems are also suitable for deviated wells where conventional pumps such as the rod pump
Pumpjack
A pumpjack is the overground drive for a reciprocating piston pump in an oil well....
are not feasible.
These systems have also some disadvantages. They are sensitive to solids and are the least efficient lift method.
While typically the cost of deploying these systems has been very high, new coiled tubing
Coiled tubing
In the oil and gas industries, coiled tubing refers to metal piping, normally 1" to 3.25" in diameter, used for interventions in oil and gas wells and sometimes as production tubing in depleted gas wells, which comes spooled on a large reel. Coiled tubing is often used to carry out operations...
umbilical technologies are in some cases greatly reducing the cost.
ESP
Electric Submersible Pumps consist of a downhole pump (a series of centrifugal pumps), an electrical motor which transforms the electrical power into kinetic energy to turn the pump, a separator or protector to prevent produced fluids from entering the electrical motor, and an electric power cable that connects the motor to the surface control panel. ESP is a very versatile artificial lift method and can be found in operating environments all over the world. They can handle a very wide range of flow rates (from 200 to 90000 barrels (14,308.9 m³) per day) and lift requirements (from virtually zero to 10,000 ft (3,000 m) of lift). They can be modified to handle contaminants commonly found in oil, aggressive corrosive fluids such as H2S and CO2, and exceptionally high downhole temperatures. Increasing water cut has been shown to have no significant detrimental effect on the ESP performance. It is possible to locate them in vertical, deviated, or horizontal wells, but it is recommended to deploy them in a straight section of casing for optimum run life performance.Although latest developments are aimed to enhance the ESP capabilities to handle gas and sand, they still need more technological development to avoid gas locks and internal erosion. Until recently, ESPs have come with an often prohibitive price tag due to the cost of deployment which can be in excess of $20,000.
Gas Lift
Gas lift is another widely used artificial lift method. As the name denotes, gas is injected in the tubing to reduce the weight of the hydrostatic column, thus reducing the back pressure and allowing the reservoir pressure to push the mixture of produce fluids and gas up to the surface. The gas lift can be deployed in a wide range of well conditions (from 30000 oilbbl/d to 15000 ft (4,572 m)). Gas lifts can cope well with abrasive elements and sand, and the cost of workover is minimum.Gas lifted wells are equipped with side pocket mandrels and gas lift injection valves. This arrangement allows a deeper gas injection in the tubing. The gas lift system has some disadvantages. There has to be a source of gas, some flow assurance problems such as hydrates can be triggered by the gas lift.
PCP
Progressing Cavity PumpsProgressive cavity pump
A progressive cavity pump is a type of positive displacement pump and is also known as a progressing cavity pump, eccentric screw pump or even just cavity pump. It transfers fluid by means of the progress, through the pump, of a sequence of small, fixed shape, discrete cavities, as its rotor is...
, PCP, are also widely applied in the oil industry. The PCP consists of a stator
Stator
The stator is the stationary part of a rotor system, found in an electric generator, electric motor and biological rotors.Depending on the configuration of a spinning electromotive device the stator may act as the field magnet, interacting with the armature to create motion, or it may act as the...
and a rotor
Rotor (electric)
The rotor is the non-stationary part of a rotary electric motor, electric generator or alternator, which rotates because the wires and magnetic field of the motor are arranged so that a torque is developed about the rotor's axis. In some designs, the rotor can act to serve as the motor's armature,...
. The rotor is rotated using either a top side motor or a bottom hole motor. The rotation created sequential cavities and the produced fluids are pushed to surface.
The PCP is a flexible system with a wide range of applications in terms of rate( up to 5000 oilbbl/d and 6000 ft (1,828.8 m)). They offer outstanding resistance to abrasives and solids but they are restricted to setting depths and temperatures. Some components of the produced fluids like aromatics can also deteriorate the stator’s elastomer.
Rod pumps
Rod pumps are long slender cylinders with both fixed and moveable elements inside. The pump is designed to be inserted inside the tubing of a well and its main purpose is to gather fluids from beneath it and lift them to the surface. The most important components are: the barrel, valves (traveling and fixed) and the piston. It also has another 18 to 30 components which are called "fittings".Components
Every part of the pump is important for its correct operation. The most commonly used parts are described below:- Barrel: The barrel is a long cylinderHydraulic cylinderA Hydraulic cylinder is a mechanical actuator that is used to give a unidirectional force through a unidirectional stroke. It has many applications, notably in engineering vehicles.- Operation :...
, which can be from 10 to 36 feet (11 m) long, with a diameter of 1.25 inches (31.8 mm) to 3.75 inches (95.3 mm). After experience with several materials for its construction, the API (American Petroleum Institute) standardized the use of two materials or compositions for this part: carbon steel and brassBrassBrass is an alloy of copper and zinc; the proportions of zinc and copper can be varied to create a range of brasses with varying properties.In comparison, bronze is principally an alloy of copper and tin...
, both with an inside coating of chromeChrome platingChrome plating, often referred to simply as chrome, is a technique of electroplating a thin layer of chromium onto a metal object. The chromed layer can be decorative, provide corrosion resistance, ease cleaning procedures, or increase surface hardness.-Process:A component to be chrome plated will...
. The advantage of brass against the harder carbon steel is its 100% resistance to corrosionCorrosionCorrosion is the disintegration of an engineered material into its constituent atoms due to chemical reactions with its surroundings. In the most common use of the word, this means electrochemical oxidation of metals in reaction with an oxidant such as oxygen...
. - PistonPistonA piston is a component of reciprocating engines, reciprocating pumps, gas compressors and pneumatic cylinders, among other similar mechanisms. It is the moving component that is contained by a cylinder and is made gas-tight by piston rings. In an engine, its purpose is to transfer force from...
/PlungerPlunger liftA plunger lift is an artificial lift method of deliquifying a natural gas well. A plunger is used to remove contaminants from productive natural gas wells, such as water , sand, oil and wax....
: This is a nickel-metal sprayed steel cylinder that goes inside the barrel. Its main purpose is to create a sucking effect that lifts the fluids beneath it and then, with the help of the valves, take the fluids above it, progressively, out of the well. It achieves this with a reciprocating up and down movement. - Valves: The valves have two components - the seat and the ball - which create a complete seal when closed. The most commonly used seats are made of carbon nitride and the ball is often made of silicon nitride. In the past, balls of iron, ceramic and titanium were used. Titanium balls are still being used but only where crude oil is extremely dense and/or the quantity of fluid to be lifted is large. The most common configuration of a rod pump requires two valves, called the traveling valve and the fixed (or static or standing) valve.
- Piston rodPiston rodIn a piston engine, a piston rod joins a piston to a connecting rod.Many internal combustion engines, and in particular all current automobile engines, do not have true piston rods, and the term piston rod is often used as a synonym for connecting rod in the context of these engines.All engines...
: This is a rod that connects the piston with the outside of the pump. Its main purpose is to transfer the up/down reciprocating energy produced by the "Nodding Donkey" (pumping unitPumpjackA pumpjack is the overground drive for a reciprocating piston pump in an oil well....
) installed above ground. - Fittings: The rest of the parts of the pump are called fittings and are, basically, small pieces designed to keep everything hold together in the right place. Most of these parts are designed to let the fluids pass uninterrupted.
- FilterFilter (oil)An oil filter is a filter designed to remove contaminants from engine oil, transmission oil, lubricating oil, or hydraulic oil. Oil filters are used in many different types of hydraulic machinery. A chief use of the oil filter is in internal-combustion engines in on- and off-road motor vehicles,...
/Strainer: The job of the filter, as guessed, is to stop big parts of rock, rubber or any other garbage that might be loose in the well from being sucked into the pump. There are several types of filters, with the most common being an iron cylinder with enough holes in it to permit the entrance of the amount of fluid the pump needs.