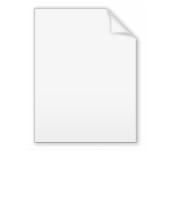
Additive manufacturing
Encyclopedia
Additive manufacturing (AM) is defined by ASTM as the "process of joining materials to make objects from 3D model data, usually layer upon layer, as opposed to subtractive manufacturing methodologies, such as traditional machining
. Synonyms: additive fabrication, additive processes, additive techniques, additive layer manufacturing, layer manufacturing and freeform fabrication".
The term additive manufacturing describes technologies which can be used anywhere throughout the product life cycle from pre-production (i.e. rapid prototyping
) to full scale production (also known as rapid manufacturing) and even for tooling applications or post production customisation.
Examples of AM are fused deposition modeling
and laser sintering.
Additive manufacturing (AM) can be defined as “the manufacture of end-use products using additive manufacturing techniques” or more broadly, the application of layer manufacturing techniques to fabricate end use products. Just three inputs are necessary for AM to take place; materials, energy and a CAD model.
AM is a new method of manufacturing, with many of its processes still unproven. Some of the most promising processes are adaptations of well established RP methods such as laser sintering (LS). However, due to the immaturity of AM itself, these techniques are still very much in their infancy. Advances in RP technology have brought about the ability to use materials that are appropriate for final manufacture. These advances in material use have brought about the prospects of directly manufacturing finished components, however, many obstacles still need to be overcome before AM can be considered as a realistic manufacturing choice.
, direct metal laser sintering
and cladding (metalworking)
for more information on methods and applications.
(EBM) is a type of additive manufacturing for metal parts. It is often classified as a rapid manufacturing method and is also known as layered fabrication. The technology manufactures parts by melting metal powder layer by layer with an electron beam in a high vacuum. Unlike some metal sintering techniques, the parts are fully dense, void-free, and extremely strong.
Electron beam direct manufacturing
(DM) is the first commercially available, large-scale, fully programmable means of achieving near net shape parts.
, and most especially of machining
, subtractive methods have often come first. In fact, the term "subtractive manufacturing" is a retronym
developed in recent years to distinguish traditional methods from the newer additive manufacturing techniques. Although fabrication
has included methods that are essentially "additive" for centuries (such as joining plates, sheets, forgings, and rolled work via riveting, screwing, forge welding, or newer kinds of welding), it did not include the information technology
component of model-based definition; and the province of machining (generating exact shapes with high precision) was generally a subtractive affair, from filing and turning through milling and grinding. For example, an encyclopedia article on threading today mentions both additive and subtractive methods as well as various integrations of the two, whereas an article on the same topic 20 years ago would not have contained the words "additive" and "subtractive" and would probably not have mentioned any additive techniques at all (let alone naming and differentiating them via use of those labels).
Additive manufacturing's earliest applications have been on the toolroom
end of the manufacturing spectrum. For example, rapid prototyping
was one of the earliest additive variants, and its mission was to reduce the lead time
and cost of developing prototypes of new parts and devices, which was earlier only done with subtractive toolroom methods (typically slowly and expensively). However, as the years go by and technology continually advances and disseminates into the business world, additive methods are moving ever further into the production end of manufacturing—sometimes even in ways that the pioneers of the techniques didn't foresee. Parts that formerly were the sole province of subtractive methods can now in some cases be made more profitably via additive ones. However, the real integration of the newer additive technologies into commercial production is essentially a matter of complementing subtractive methods rather than displacing them entirely. Predictions for the future of commercial manufacturing, starting from today's already-begun infancy period, are that manufacturing firms will need to be flexible, ever-improving
users of all available technologies in order to remain competitive.
It is also predicted by some additive manufacturing advocates that this technological development arc will change the nature of commerce, because end users will be able to do much of their own manufacturing rather than engaging in trade to buy products from other people and corporations. For example, for many African and South American countries today, there are various categories of manufactured goods for which most or all of their consumption is met by imports rather than domestic industry. Proponents of RepRaps envision an era when they instead use instant manufacturing (blending additive and subtractive) to make parts and then local labor to do the assembly. In this realm, too (the evolution of commerce), a future of complementary integration seems likelier than absolute displacement, at least for some decades to come.
Machining
Conventional machining is a form of subtractive manufacturing, in which a collection of material-working processes utilizing power-driven machine tools, such as saws, lathes, milling machines, and drill presses, are used with a sharp cutting tool to physical remove material to achieve a desired...
. Synonyms: additive fabrication, additive processes, additive techniques, additive layer manufacturing, layer manufacturing and freeform fabrication".
The term additive manufacturing describes technologies which can be used anywhere throughout the product life cycle from pre-production (i.e. rapid prototyping
Rapid prototyping
Rapid prototyping is the automatic construction of physical objects using additive manufacturing technology. The first techniques for rapid prototyping became available in the late 1980s and were used to produce models and prototype parts. Today, they are used for a much wider range of applications...
) to full scale production (also known as rapid manufacturing) and even for tooling applications or post production customisation.
Examples of AM are fused deposition modeling
Fused deposition modeling
Fused deposition modeling is an additive manufacturing technology commonly used for modeling, prototyping, and production applications. The technology was developed by S...
and laser sintering.
Additive manufacturing (AM) can be defined as “the manufacture of end-use products using additive manufacturing techniques” or more broadly, the application of layer manufacturing techniques to fabricate end use products. Just three inputs are necessary for AM to take place; materials, energy and a CAD model.
AM is a new method of manufacturing, with many of its processes still unproven. Some of the most promising processes are adaptations of well established RP methods such as laser sintering (LS). However, due to the immaturity of AM itself, these techniques are still very much in their infancy. Advances in RP technology have brought about the ability to use materials that are appropriate for final manufacture. These advances in material use have brought about the prospects of directly manufacturing finished components, however, many obstacles still need to be overcome before AM can be considered as a realistic manufacturing choice.
Laser processing
Laser based additive manufacturing is accomplished by directing a high power laser at a substrate to create a melt pool. Material is then added to the melt pool. The added material enlarges the melt pool and adds to the part. To create the desired geometry, the laser is rastered across the substrate while material is continuously added. See selective laser sinteringSelective laser sintering
Selective laser sintering is an additive manufacturing technique that uses a high power laser to fuse small particles of plastic, metal , ceramic, or glass powders into a mass that has a desired 3-dimensional shape...
, direct metal laser sintering
Direct metal laser sintering
Direct metal laser sintering is an additive metal fabrication technology developed by EOS out of Munich, Germany, sometimes also referred to by the terms selective laser sintering or selective laser melting . The process involves use of a 3D CAD model whereby a .stl file is created and sent to...
and cladding (metalworking)
Cladding (metalworking)
Cladding is the bonding together of dissimilar metals. It is distinct from welding or gluing as a method to fasten the metals together. Cladding is often achieved by extruding two metals through a die as well as pressing or rolling sheets together under high pressure.The United States Mint uses...
for more information on methods and applications.
Electron beam melting
Electron beam meltingElectron Beam Melting
Electron beam melting is a type of additive manufacturing for metal parts. It is often classified as a rapid manufacturing method. The technology manufactures parts by melting metal powder layer per layer with an electron beam in a high vacuum...
(EBM) is a type of additive manufacturing for metal parts. It is often classified as a rapid manufacturing method and is also known as layered fabrication. The technology manufactures parts by melting metal powder layer by layer with an electron beam in a high vacuum. Unlike some metal sintering techniques, the parts are fully dense, void-free, and extremely strong.
Electron beam direct manufacturing
Direct Manufacturing
Direct Manufacturing, or DM for short, is one of many available technologies used to produce a three-dimensional near net shape part or component using an additive layer over layer process, which is commonly referred to as Additive Manufacturing. DM, however, is the first commercially available,...
(DM) is the first commercially available, large-scale, fully programmable means of achieving near net shape parts.
Aerosol jetting
Aerosol jetting consists of directing a focused stream of atomized particles towards a substrate. The high velocity of the stream causes the particles to impact on the substrate. Thermal post processing is usually required to sinter the particles together to adhere them to the substrate and/or make them conductive.Inkjet
Inkjet works by propelling individual small droplets of ink towards a substrate. The ink is forced through a small orifice by a variety of means including pressure, heat, and vibration. The liquid droplets impact the substrate and wet. To be used for additive manufacturing, the liquid droplets must change phase to solid upon deposition on the substrate when printing a pattern as a layer. Depending on the deposited material, the phase change could be by heat transfer, UV light or chemical reaction. When jetting particle suspension liquids, the deposited pattern is dried for the liquid vehicle to vaporise and the remaining particles could be sintered for layer solidification.Semi-solid freeform fabrication
In the experimental semi-solid freeform fabrication process, a semi-solid slurry of metallic alloy is created by heating the alloy at a specific temperature to give the material a paste-like consistency (i.e., neither liquid or solid) in preparation for deposition. A key part of the whole process is to also maintain shear-stress on the material while it is being deposited. This creates the desired "grain" structure within the material as well as eliminating any stratification, porosity, and other defects in the part being made. Currently, however, some amount of surface machining is required to remove unwanted material post-deposition.Historical development and broadening applications
In the history of manufacturingManufacturing
Manufacturing is the use of machines, tools and labor to produce goods for use or sale. The term may refer to a range of human activity, from handicraft to high tech, but is most commonly applied to industrial production, in which raw materials are transformed into finished goods on a large scale...
, and most especially of machining
Machining
Conventional machining is a form of subtractive manufacturing, in which a collection of material-working processes utilizing power-driven machine tools, such as saws, lathes, milling machines, and drill presses, are used with a sharp cutting tool to physical remove material to achieve a desired...
, subtractive methods have often come first. In fact, the term "subtractive manufacturing" is a retronym
Retronym
A retronym is a type of neologism that provides a new name for an object or concept to differentiate the original form or version of it from a more recent form or version. The original name is most often augmented with an adjective to account for later developments of the object or concept itself...
developed in recent years to distinguish traditional methods from the newer additive manufacturing techniques. Although fabrication
Fabrication (metal)
Fabrication as an industrial term refers to building metal structures by cutting, bending, and assembling. The cutting part of fabrication is via sawing, shearing, or chiseling ; torching with handheld torches ; and via CNC cutters...
has included methods that are essentially "additive" for centuries (such as joining plates, sheets, forgings, and rolled work via riveting, screwing, forge welding, or newer kinds of welding), it did not include the information technology
Information technology
Information technology is the acquisition, processing, storage and dissemination of vocal, pictorial, textual and numerical information by a microelectronics-based combination of computing and telecommunications...
component of model-based definition; and the province of machining (generating exact shapes with high precision) was generally a subtractive affair, from filing and turning through milling and grinding. For example, an encyclopedia article on threading today mentions both additive and subtractive methods as well as various integrations of the two, whereas an article on the same topic 20 years ago would not have contained the words "additive" and "subtractive" and would probably not have mentioned any additive techniques at all (let alone naming and differentiating them via use of those labels).
Additive manufacturing's earliest applications have been on the toolroom
Toolroom
The term toolroom can refer to three related concepts. The concepts have evolved over the past two centuries as technology itself has evolved.- Storing tools :...
end of the manufacturing spectrum. For example, rapid prototyping
Rapid prototyping
Rapid prototyping is the automatic construction of physical objects using additive manufacturing technology. The first techniques for rapid prototyping became available in the late 1980s and were used to produce models and prototype parts. Today, they are used for a much wider range of applications...
was one of the earliest additive variants, and its mission was to reduce the lead time
Lead time
A lead time is the latency between the initiation and execution of a process. For example, the lead time between the placement of an order and delivery of a new car from a manufacturer may be anywhere from 2 weeks to 6 months...
and cost of developing prototypes of new parts and devices, which was earlier only done with subtractive toolroom methods (typically slowly and expensively). However, as the years go by and technology continually advances and disseminates into the business world, additive methods are moving ever further into the production end of manufacturing—sometimes even in ways that the pioneers of the techniques didn't foresee. Parts that formerly were the sole province of subtractive methods can now in some cases be made more profitably via additive ones. However, the real integration of the newer additive technologies into commercial production is essentially a matter of complementing subtractive methods rather than displacing them entirely. Predictions for the future of commercial manufacturing, starting from today's already-begun infancy period, are that manufacturing firms will need to be flexible, ever-improving
Continuous Improvement Process
A continuous improvement process is an ongoing effort to improve products, services, or processes. These efforts can seek "incremental" improvement over time or "breakthrough" improvement all at once...
users of all available technologies in order to remain competitive.
It is also predicted by some additive manufacturing advocates that this technological development arc will change the nature of commerce, because end users will be able to do much of their own manufacturing rather than engaging in trade to buy products from other people and corporations. For example, for many African and South American countries today, there are various categories of manufactured goods for which most or all of their consumption is met by imports rather than domestic industry. Proponents of RepRaps envision an era when they instead use instant manufacturing (blending additive and subtractive) to make parts and then local labor to do the assembly. In this realm, too (the evolution of commerce), a future of complementary integration seems likelier than absolute displacement, at least for some decades to come.
See also
- 3D printing3D printing3D printing is a form of additive manufacturing technology where a three dimensional object is created by laying down successive layers of material. 3D printers are generally faster, more affordable, and easier to use than other additive manufacturing technologies. However, the term 3D printing is...
- Desktop manufacturing
- Digital fabricator
- Direct digital manufacturing
- Instant manufacturing, also known as "direct manufacturing" or "on-demand manufacturing"
- Solid freeform fabrication
- Additive Manufacturing File FormatAdditive Manufacturing File FormatAdditive Manufacturing File Format is an open standard for describing objects for additive manufacturing processes such as 3D printing. The official ASTM F2915standard is an XML-based format designed to allow any computer-aided design software to describe the shape and composition of any 3D object...
- Laser claddingCladding (metalworking)Cladding is the bonding together of dissimilar metals. It is distinct from welding or gluing as a method to fasten the metals together. Cladding is often achieved by extruding two metals through a die as well as pressing or rolling sheets together under high pressure.The United States Mint uses...