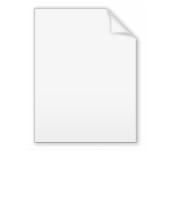
Direct Manufacturing
Encyclopedia
Direct Manufacturing, or DM for short, is one of many available technologies used to produce a three-dimensional (3D) near net shape part or component using an additive layer over layer process, which is commonly referred to as Additive Manufacturing
. DM, however, is the first commercially available, large-scale, fully programmable means of achieving near net shape parts. The DM process, which has been recently marketed as Electron Beam Free Form Fabrication] (EBF3) and [Electron Beam Direct Manufacturing] (EBDM), is based on well-established electron beam welding
technology that has been used for production processing for nearly 50 years.
With the DM process, an electron beam gun provides the energy source used for melting metallic feedstock, which is typically wire. The electron beam is a highly efficient power source that can be both precisely focused and deflected using electromagnetic coils at rates well into thousands of hertz. Typical electron beam welding systems have high power availability, with 30 and 42 kilowatt systems being most common. A major advantage of using metallic components with electron beams is that the process is conducted within a high vacuum environment of 1x10-4 Torr. or greater, providing a contamination-free work zone that does not require the use of additional inert gasses commonly used with laser and arc based processes. With DM, feedstock material is fed into a molten pool created by the electron beam. Through the use of computer numeric controls (CNC), the molten pool is moved about on a substrate plate, adding material just where it is needed to produce the near net shape. This process is repeated in a layer by layer fashion, until the desired 3D shape is produced.
Depending on the part being manufactured, deposition rates can range up to 200 cubic inches per hour. With a light alloy, such as titanium, this translates to a real-time deposition rate of 40 pounds per hour. A wide range of engineering alloys are compatible with the DM process and are readily available in the form of welding wire from an existing supply base. These include, but are not limited to, stainless steels, cobalt alloys, nickel alloys, copper nickel alloys, tantalum, as well as many other high-value materials.
As with many layer-additive processes, the DM process starts with a 3D CAD model of a part that needs to be produced. In conventional manufacturing processes, such as forging, once the part is designed, tooling and dies are typically designed and fabricated prior to the initial part being produced. The DM process is based on using flexible tooling that can virtually eliminate the time spent designing and manufacturing custom tools and dies. Due to the long lead times associated with producing custom forging dies, engineers must typically have the complete part design finished prior to committing to the cost of fabrication tooling. DM allows the engineer the opportunity to be more aggressive with their initial designs, since changing or adding features in a subsequent design will typically have minimal impact on the follow-on DM build cycles. The high energy density of the electron beam allows you to process materials like tantalum and tungsten, which are historically known to be very difficult and expensive materials to work with. By building near net shapes, the overall cost of structures that utilize refractory materials can be significantly decreased.
In the aerospace industry, the “Buy-to-Fly” ratio is routinely used to describe the cost associated with the amount of raw materials required to produce a finished part. With ever-increasing performance requirements being requested of modern aircraft, designers are using more high performance alloys, such as titanium and nickel, to meet the performance demands. Although these super alloys perform well in the final application, this performance comes at a high cost. The raw materials are both expensive and difficult to fabricate using conventional operations, such as forging and machining. The DM process was developed to deposit material only where it is needed to reduce the amount of starting materials required, which also translates into reduced time for machining in follow-on operations.
Additive manufacturing
Additive manufacturing is defined by ASTM as the "process of joining materials to make objects from 3D model data, usually layer upon layer, as opposed to subtractive manufacturing methodologies, such as traditional machining...
. DM, however, is the first commercially available, large-scale, fully programmable means of achieving near net shape parts. The DM process, which has been recently marketed as Electron Beam Free Form Fabrication] (EBF3) and [Electron Beam Direct Manufacturing] (EBDM), is based on well-established electron beam welding
Electron beam welding
Electron beam welding is a fusion welding process in which a beam of high-velocity electrons is applied to the materials being joined. The workpieces melt as the kinetic energy of the electrons is transformed into heat upon impact, and the filler metal, if used, also melts to form part of the weld...
technology that has been used for production processing for nearly 50 years.
With the DM process, an electron beam gun provides the energy source used for melting metallic feedstock, which is typically wire. The electron beam is a highly efficient power source that can be both precisely focused and deflected using electromagnetic coils at rates well into thousands of hertz. Typical electron beam welding systems have high power availability, with 30 and 42 kilowatt systems being most common. A major advantage of using metallic components with electron beams is that the process is conducted within a high vacuum environment of 1x10-4 Torr. or greater, providing a contamination-free work zone that does not require the use of additional inert gasses commonly used with laser and arc based processes. With DM, feedstock material is fed into a molten pool created by the electron beam. Through the use of computer numeric controls (CNC), the molten pool is moved about on a substrate plate, adding material just where it is needed to produce the near net shape. This process is repeated in a layer by layer fashion, until the desired 3D shape is produced.
Depending on the part being manufactured, deposition rates can range up to 200 cubic inches per hour. With a light alloy, such as titanium, this translates to a real-time deposition rate of 40 pounds per hour. A wide range of engineering alloys are compatible with the DM process and are readily available in the form of welding wire from an existing supply base. These include, but are not limited to, stainless steels, cobalt alloys, nickel alloys, copper nickel alloys, tantalum, as well as many other high-value materials.
As with many layer-additive processes, the DM process starts with a 3D CAD model of a part that needs to be produced. In conventional manufacturing processes, such as forging, once the part is designed, tooling and dies are typically designed and fabricated prior to the initial part being produced. The DM process is based on using flexible tooling that can virtually eliminate the time spent designing and manufacturing custom tools and dies. Due to the long lead times associated with producing custom forging dies, engineers must typically have the complete part design finished prior to committing to the cost of fabrication tooling. DM allows the engineer the opportunity to be more aggressive with their initial designs, since changing or adding features in a subsequent design will typically have minimal impact on the follow-on DM build cycles. The high energy density of the electron beam allows you to process materials like tantalum and tungsten, which are historically known to be very difficult and expensive materials to work with. By building near net shapes, the overall cost of structures that utilize refractory materials can be significantly decreased.
In the aerospace industry, the “Buy-to-Fly” ratio is routinely used to describe the cost associated with the amount of raw materials required to produce a finished part. With ever-increasing performance requirements being requested of modern aircraft, designers are using more high performance alloys, such as titanium and nickel, to meet the performance demands. Although these super alloys perform well in the final application, this performance comes at a high cost. The raw materials are both expensive and difficult to fabricate using conventional operations, such as forging and machining. The DM process was developed to deposit material only where it is needed to reduce the amount of starting materials required, which also translates into reduced time for machining in follow-on operations.