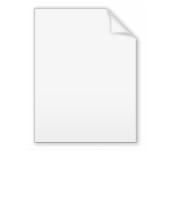
Test Engineer
Encyclopedia
A hardware test engineer is a professional who determines how to create a process that would test a particular product in manufacturing
, quality assurance
or related area like RMA
department, in order to assure that the product meets applicable specifications. Test engineers are also responsible for determining the best way a test can be performed in order to achieve 100% test coverage of all components using different test processes.
Test engineers can have different expertise which depends on what test process they are more familiar with (although many known TE have full familiarity from the PCB
level process like ICT
, JTAG
, and 5DX
) to PCBA and system level process like board functional test (BFT or FT), burn-in test, system level test (ST). Among some known process used in manufacturing where a TE is needed are as follows:
and Marketing Requirements Document (MRD)
-- some of the earliest work done during a new product introduction (NPI).
By working with or as part of the NPI group, a test engineer ensures that a product is designed for both testability and manufacturability. In other words, to make sure that the product can be readily tested and built.
The following are some general rules to ensure testability and manufacturability of a product:
By following the general rules above, test engineers minimize future surprises (like adding extra components, re-layout of the boards, etc) which drives up costs and development delays of the final product.
With this in mind, test engineers always get involved in the following reviews as well:
Data is also consistently gathered after the product gets past mass production stage (or general availability aka GA). These data are usually used to improve the quality of the products. For example, data may prove that common chips doesn't work well all the time with the CPU or design of the product. It may also show that a particular field replaceable unit (FRU)
fails a number of times in the field. Because of those data, a new component or FRU can be qualified by hardware, software and manufacturing team to drive down the errors or eliminate those problems. These data are provided as input also to the next product with similar design.
In addition, yields will show if another process needs to be introduced (i.e. previous process cannot capture certain test errors due to limitation of fixturing or something else). Yields can also decide if an existing test process can be trimmed down (step-wise or time-wise) or even fully eliminated (i.e. if the ESS errors can be captured during the 3rd hour, test time can be cut down from a normal 24 hours down to maybe 4. Or if a process consistently yields 100% during a 15 month period, teams can get together and decide to eliminate that process at all).
, handler, interface board, and test program that drives the ATE, as with the case of the IC
chip testing.
Test automation is a big part of a test engineer's job.
The whole intention of automating the test is as follows:
Overall, this drives manufacturing reliability and quality at the end of the line making sure that all units shipped out to customers are well tested, stressed, filtered out of any errors, and configured properly.
Because of their close involvement with the test line, they monitor the products going through the line and inspect the failed boards to decide if it really failed or if the failure was just caused by some improper test setup. Some examples of these false failures are:
Of course, outsourcing test solutions to the CM has its pros and cons.
Some of the advantages are:
Some of the disadvantages are:
Because it is hard to find a test engineer who knows every aspect of testing methodology (from PCB test like ICT, JTAG test, flying probe test, and 5DX test to PCBA test which includes writing test automation from functional test to FQA test among others), companies usually outsource part of the development of this missing test piece to their CM. For example, if none of the in-house TEs know much about ICT fixtures, they will ask their CM to develop the ICT test solutions for them instead.
Manufacturing
Manufacturing is the use of machines, tools and labor to produce goods for use or sale. The term may refer to a range of human activity, from handicraft to high tech, but is most commonly applied to industrial production, in which raw materials are transformed into finished goods on a large scale...
, quality assurance
Quality Assurance
Quality assurance, or QA for short, is the systematic monitoring and evaluation of the various aspects of a project, service or facility to maximize the probability that minimum standards of quality are being attained by the production process...
or related area like RMA
Return Merchandise Authorization
A Return Merchandise Authorization , sometimes Return Merchandise Agreement or ' product repaired or replaced or in order to receive a refund or credit for another product from the same retailer or corporation within the product's warranty period.The RMA process and the issuance of an RMA is a key...
department, in order to assure that the product meets applicable specifications. Test engineers are also responsible for determining the best way a test can be performed in order to achieve 100% test coverage of all components using different test processes.
Test engineers can have different expertise which depends on what test process they are more familiar with (although many known TE have full familiarity from the PCB
Printed circuit board
A printed circuit board, or PCB, is used to mechanically support and electrically connect electronic components using conductive pathways, tracks or signal traces etched from copper sheets laminated onto a non-conductive substrate. It is also referred to as printed wiring board or etched wiring...
level process like ICT
In-circuit test
In-circuit test is an example of white box testing where an electrical probe tests a populated printed circuit board , checking for shorts, opens, resistance, capacitance, and other basic quantities which will show whether the assembly was correctly fabricated...
, JTAG
JTAG
Joint Test Action Group is the common name for what was later standardized as the IEEE 1149.1 Standard Test Access Port and Boundary-Scan Architecture. It was initially devised for testing printed circuit boards using boundary scan and is still widely used for this application.Today JTAG is also...
, and 5DX
5DX
The 5DX is an automated X-ray inspection robot, which belongs to the set of automated test equipment robots and industrial robots utilizing machine vision. The 5DX is manufactured by Agilent Technologies. The 5DX is a non-destructive structural test machine, using laminography to take 3D slices...
) to PCBA and system level process like board functional test (BFT or FT), burn-in test, system level test (ST). Among some known process used in manufacturing where a TE is needed are as follows:
- In-circuit testIn-circuit testIn-circuit test is an example of white box testing where an electrical probe tests a populated printed circuit board , checking for shorts, opens, resistance, capacitance, and other basic quantities which will show whether the assembly was correctly fabricated...
(ICT) - Stand-alone JTAGJTAGJoint Test Action Group is the common name for what was later standardized as the IEEE 1149.1 Standard Test Access Port and Boundary-Scan Architecture. It was initially devised for testing printed circuit boards using boundary scan and is still widely used for this application.Today JTAG is also...
test - Automated x-ray inspectionAutomated x-ray inspectionAutomated inspection is a technology based on the same principles as automated optical inspection . It uses as its source, instead of visible light, to automatically inspect features, which are typically hidden from view....
(5DX/AXI) (also known as X-ray test) - Automated optical inspectionAutomated optical inspectionAutomated optical inspection is an automated visual inspection of a wide range of products, such as printed circuit boards , LCDs, transistors, automotive parts, lids and labels on product packages or agricultural products...
(AOI) test - ContinuityContinuity testIn electronics, a continuity test is the checking of an electric circuit to see if current flows .A continuity test is performed by placing a small voltage across the chosen path...
or flying probeFlying probeFlying probe test systems are often used for only testing basic production, prototypes, and boards that present accessibility problems. Flying probe testing uses electro-mechanically controlled probes to access components on printed circuit assemblies . Commonly used for test of analog components,...
test - (Board) functional test (BFT/FT)
- Burn-in test
- Environmental stress screeningEnvironmental stress screeningEnvironmental stress screening refers to the process of exposing a newly manufactured or repaired product or component to stresses such as thermal cycling and vibration in order to force latent defects to manifest themselves by permanent or catastrophic failure during the screening process...
(ESS) test - Highly Accelerated Life TestHighly Accelerated Life TestA highly accelerated life test , is a stress testing methodology for accelerating product reliability during the engineering development process. It is commonly applied to electronic equipment and is performed to identify and thus help resolve design weaknesses in newly-developed equipment...
(HALT) - Highly accelerated stress screeningHighly accelerated stress screeningHASS Testing is a proven test method developed to find Manufacturing/Production-process induced defects in electronics and electro-mechanical assemblies before those products are released to market...
(HASS) test - Ongoing reliability testOngoing reliability testThe ongoing reliability test is a hardware test process usually used in manufacturing to ensure that quality of the products is still of the same specifications as the day it first went to production or general availability....
(ORT) - System test (ST)
- Final quality audit processFinal Quality Audit ProcessFinal Quality Audit Process, in the hardware manufacturing world, is the last process flow before shipping a product. This process is established to ensure the following:* the unit has gone through all the manufacturing or test process...
(FQA) test
Early project involvement from design phase
Ideally, a test engineer's involvement with a product begins with the very early stages of the design phase. Depending on the culture of the firm, the early stages could refer to Product Requirements Document (PRD)Product requirements document
A product requirements document is a document written by a company that defines a product they are making, or the requirements for one or more new features for an existing product...
and Marketing Requirements Document (MRD)
Marketing Requirements Document
A market requirements document in project management and systems engineering, is a document that expresses the customer's wants and needs for the product or service.It is typically written as a part of product marketing or product management...
-- some of the earliest work done during a new product introduction (NPI).
By working with or as part of the NPI group, a test engineer ensures that a product is designed for both testability and manufacturability. In other words, to make sure that the product can be readily tested and built.
The following are some general rules to ensure testability and manufacturability of a product:
- Making sure the product has correct label specs and placement that would make it possible for the unit to be traceable and programmable. Implementing good label specs results in having correct information programmed correctly into the unit under test (UUT)Device under testDevice under test , also known as unit under test , is a term commonly used to refer to a manufactured product undergoing testing.-In semiconductor testing:...
(sometimes called DUT or device under test). To make this possible, the test engineers enforce those labels location and are all readable and scannable, thus eliminating the need for a manual typing of information into the unit. Automatic placing of identification codes into the part during test and making them available for verification at later processing steps can help minimize these types of errors. Manual typing can introduce problems related to inaccurate information being programmed due to human errors. Also, without the test engineers input during PRD design phase, the hardware engineer in charge of designing of the silk-screen for the PCB may put those labels below some attachable board which will then later renders the labels useless (i.e. in a motherboard/daughterboard design and also a board that has a pluggable module, a label would be visible on the main board by itself but would be obstructed by the other boards that needs to be integrated). This information are often indicated in both PRD and MRD. - Making sure that all components required to test and debug the UUT, which includes the console/serial port, are all accessible from the early part of the manufacturing process up to the last part which is often the final quality audit/assurance (FQA) process. This also includes making sure those components are available even after the units are returned by the customers for troubleshooting or repair. By following this guidelines, the team will eliminate unnecessary opening of the UUT just to access those components which may result in introducing errors into the unit (i.e. knocking off some capacitors or resistors when opening/sliding out the cover, dropping the tool inside the PCBA after opening, forgetting some other cables to reconnect before closing the unit for manufacturing process flow continuation, etc).
- Making sure that all components needed to test the unit are added into the cost matrix of the final product. This components may include the UART/RS232 chips for talking to the UUT, ethernet ports for upgrading the firmware, JTAG connectors, etc.
- Defining what manufacturing test process is needed based from the product definition.
- Verifying that the currently available test equipment is adequate for testing the proposed design. If new equipment is needed, budgetary concerns have been addressed and sufficient lead time exists for new equipment installation and verification. Also, new test equipment may require training for test equipment operators and supervisors.
By following the general rules above, test engineers minimize future surprises (like adding extra components, re-layout of the boards, etc) which drives up costs and development delays of the final product.
Working with cross platform teams, hardware and software team
Often people take shortcuts to be able to deliver final products. Problem is, because of these shortcuts, the product's manufacturability and testability becomes complicated (inability to read and write information, creating deviation from the process, etc) which impacts the manufacturing complexity of a product. Because of this complexity, bottlenecks in the manufacturing and delivery schedule delays are introduced.With this in mind, test engineers always get involved in the following reviews as well:
- Schematics review - to make sure all components and data/electrical paths are accessible and testable
- Board layout review - to make sure all labels and components are accessible. No components are near the edges, covers, movable parts, etc. that would result into higher probability of a components being knocked off the board.
- Electrical specifications review - to make sure all we can drive the needed power into the board with any fixture needed in any of the process (ICT fixture needs to make sure it can supply the appropriate power to the board without external power supplies, the Burn-In and ESS chamber can provide the required voltage and current to a number of fixtures and at the same time without modifying the chambers specs so it can mix with other products)
- Diagnostics specifications review - to make sure command output formats are followed for simplification of whatever test automation tools will be develop. Also, to make sure that commands itself are available to test all components.
Yield gathering
Data gathering plays a very important part during the products' lifespan. In early stages, these data or test yields drive the product to see if it is mature enough to go into mass production. Most companies set specific yield targets for each process that measures what is the yields expected and/or acceptable.Data is also consistently gathered after the product gets past mass production stage (or general availability aka GA). These data are usually used to improve the quality of the products. For example, data may prove that common chips doesn't work well all the time with the CPU or design of the product. It may also show that a particular field replaceable unit (FRU)
Field Replaceable Unit
This article is primarily about FRUs in computers.A field replaceable unit is a circuit board, part or assembly that can be quickly and easily removed from a personal computer or other piece of electronic equipment, and replaced by the user or a technician without having to send the entire product...
fails a number of times in the field. Because of those data, a new component or FRU can be qualified by hardware, software and manufacturing team to drive down the errors or eliminate those problems. These data are provided as input also to the next product with similar design.
In addition, yields will show if another process needs to be introduced (i.e. previous process cannot capture certain test errors due to limitation of fixturing or something else). Yields can also decide if an existing test process can be trimmed down (step-wise or time-wise) or even fully eliminated (i.e. if the ESS errors can be captured during the 3rd hour, test time can be cut down from a normal 24 hours down to maybe 4. Or if a process consistently yields 100% during a 15 month period, teams can get together and decide to eliminate that process at all).
Test automation
Test automation refers to the automation of the process to test a product through the use of machines. Depending on the product, the machines that we are referring to could mean a combination of Automatic Test Equipment (ATE)Automatic test equipment
Automatic or Automated Test Equipment is any apparatus that performs tests on a device, known as the Device Under Test , using automation to quickly perform measurements and evaluate the test results...
, handler, interface board, and test program that drives the ATE, as with the case of the IC
Integrated circuit
An integrated circuit or monolithic integrated circuit is an electronic circuit manufactured by the patterned diffusion of trace elements into the surface of a thin substrate of semiconductor material...
chip testing.
Test automation is a big part of a test engineer's job.
The whole intention of automating the test is as follows:
- Enforce test steps to be followed within specifications and correct timing.
- Eliminate manual command and data inputs.
- Automate data gathering.
- Enforce test process flow.
Overall, this drives manufacturing reliability and quality at the end of the line making sure that all units shipped out to customers are well tested, stressed, filtered out of any errors, and configured properly.
Defining standard test documents
Following are some of the documents that the test engineers maintain or define:- Test methodTest methodA test method is a definitive procedure that produces a test result.A test can be considered as technical operation that consists of determination of one or more characteristics of a given product, process or service according to a specified procedure. Often a test is part of an experiment.The test...
- Diagnostic design specificationDiagnostic design specificationDiagnostic design specification is a document indicating how the diagnostics will be implemented on an upcoming/new products that will be developed by the company. It describes the behavior of the diagnostics like how the test will execute, how the output messages are formatted, and how the final...
- Manufacturing test requirement design specificationManufacturing test requirement design specificationManufacturing test requirement design specification is a document which specifies how the test is going to be implemented on a new/upcoming product...
- Design for testability (DFT)Design For TestDesign for Test is a name for design techniques that add certain testability features to a microelectronic hardware product design. The premise of the added features is that they make it easier to develop and apply manufacturing tests for the designed hardware...
- Design for manufacturability (DFM)Design for manufacturability (PCB)Design for manufacturability is a design methodology intended to ease the manufacturing process of a given product. In the PCB design process DFM leads to a set design guidelines that attempt to ensure manufacturability...
- Test plan
Contract manufacturer TE
A contract manufacturer (CM) also provides a test engineer for their customers. The function of this test engineers varies depending on the level of support they provide for their customers: providing "interactive and first level of defense"-only support or providing partial or ground up solutions.Providing interactive and first level of defense support
Providing "interactive and first level of defense"-only support is the usual job of the CM TE. Here are some typical job functions for a CM test engineer:- Reviewing test solutions with their partnering test engineers from the customer side.
- Analyzing if the infrastructure meets the requirements (from floor/line setup, network access to workstations and/or servers, operator manpower, etc).
- Getting familiar with the customer products' technology.
- Being able to manage, train and support operators who performs the actual testing.
- Being able to debug and isolate problems.
- Gathering information to feedback to their partners.
Because of their close involvement with the test line, they monitor the products going through the line and inspect the failed boards to decide if it really failed or if the failure was just caused by some improper test setup. Some examples of these false failures are:
- Forgot to connect the cable to talk to the UUT (or misplacing the cable or putting it loose). This will cause the test automation to time out for any response from the UUT.
- Forgot to connect the loopback cables when testing a UUT with any networking interface (ethernet/optical/etc ports). This will cause the traffic test to fail.
- Skipped some test process. Some test process will configure the UUT to load some firmware or put it in some state (i.e preparing it to run in burn-in mode) so when the test automation starts, whatever known state it is expecting will not be satisfied and thus fail.
- Skipped to implement some deviations that would require hardware/software changes to the UUT.
- Forgot to power up the unit right away when the test automation started. This will result to the same problem as the first item of this list.
- Forgot to attach any other test fixture components.
Providing partial or ground up solutions
There is a small number of companies who prefer to outsource their test engineering work to their corresponding CM. In that case, the CM TEs will be in charge of providing the test automation solution, test fixture design, yield gathering plus the usual interactive and first level of defense for their customers.Of course, outsourcing test solutions to the CM has its pros and cons.
Some of the advantages are:
- Cheaper cost. Especially if the CM resides in a country where labor is at minimum.
- Beneficial if the company itself doesn't have or cannot find any TE that matches the company's requirements.
Some of the disadvantages are:
- Getting tied up to a single CM. It is hard to find a CM that is willing to share information to another CM.
- CM TEs are seldom involved with product design stage/phase.
- Time constraints. They only get handed out the specs of the product during late NPI stage. Because of this, test solutions are rushed and quality are often compromised.
- Conflict of interest. Company needs to know every level of information that goes through the product line in order to monitor potential problems that would one day snowball. But CM doesn't provide this level of details, they only give out how many units passed or fail for the day. A unit could have failed 5 times before it passes which may relates to some timing issues of some components of the product like the CPU or oscillators for example. The cleaner the first passed yield data that the CM provides, the better quality the unit went through the assembly line. This means that the CM would be enticed to provide the final result as their first passed yield data instead so it will reflect their higher quality side.
Because it is hard to find a test engineer who knows every aspect of testing methodology (from PCB test like ICT, JTAG test, flying probe test, and 5DX test to PCBA test which includes writing test automation from functional test to FQA test among others), companies usually outsource part of the development of this missing test piece to their CM. For example, if none of the in-house TEs know much about ICT fixtures, they will ask their CM to develop the ICT test solutions for them instead.