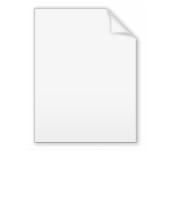
Siemens VAI
Encyclopedia
Siemens VAI Metals Technologies (formerly Voest-Alpine Industrieanlagenbau
) based in Linz, Austria, is an engineering and plant building company for the iron and steel industry, for the flat-rolling sector of the aluminum industry and for open cast mining. It is one of the branches of Siemens Industrial Solutions and focuses on metallurgical services.
continued with the construction, only to pass it on to the German Mining and Metallurgical association (DBHG) after a short time. The large-scale plant, which was originally planned for metallurgical purposes, was then modified for the arms industry.
) (United Iron and Steel Plants).
For the plant’s reconstruction, some divisions were combined into the so-called “New Building Division”, designed to reconstruct the metallurgical plant in Linz. Thus, the most important metallurgical facilities could all be started up again by the year 1949: the coking plant, blast furnaces, SM-steel making plants (plant with Siemens-Martin-furnace, named after inventors) and heavy plate mills (mills producing plates of over 3 mm thickness). Many of the products were scarce commodities after the war. For this reason, the metallurgical plant was able to recover pretty soon, investing largely into the expansion of its own facilities. Due to the shortage of steel scrap, necessary for the operation of SM blast furnaces, the yearly steel mill capacities of 220,000 tons soon proved to be insufficient. The solution was a new manufacturing process: the LD-process (Linz-Donawitz-process), manufactured in house and commissioned in 1952 in Linz, and 1953 in Donawitz. The huge advantages of this process were cost-saving on the one hand (investment costs were only 65% and operation costs only 55% compared to the SM blast furnace), and larger production capacities on the other.
During this time, the number of employees grew to approximately 4,000 people. An additional center of technology was built in Vienna and additional constructors from Austria as well as from other countries were flown in.
In 1973, the two nationalized iron and steel industries VÖEST and ALPINE merged together and became today’s famous voestalpine
. The organization was restructured into the areas of “metallurgical plants” (seven divisions) and “chemical plants” (two divisions).
started in 1974, the metallurgical industry was severely affected in all parts of the world. The consequence was a significant decline in prices within the steel sector, which also affected the construction of plants. Still, the area of technology (industrial plant construction and ready-to-use industry) became increasingly important for the company. Thus, the metallurgical plant’s share of turnover was 80% in 1973 - however, in 1976, the share of the plant construction and ready-to-use industries already amounted to 45%. The company was faced with a lot of restructuring processes and new orientations, but also gained the largest projects ever. In the beginning of the 1980s, first steps were taken towards biotechnology, leading to the construction of a biomass utilization technology center in Linz. In order to adapt to market requirements, the construction of chemical plants also took further measures in the area of environmental protection.
A very important step in this area was the acquisition of Korf Engineering GesmbH as a 100% subsidiary, since it included the rights to the COREX process. Because of the continuous high amount of commissions, the effects of the steel crisis were mitigated. However, in 1985 the crisis exploded and in the previous years, political pressure had already been put on the nationalized company with regard to job security. Therefore, the company, which had meanwhile become a diversified group, suffered a record loss in 1984, amounting to a total of 25 billion Schillings.
Finally, in 1988, VOEST-ALPINE Industrieanlagenbau (VAI) became a proper GesmbH in the framework of the newly established Maschinen- und Anlagenbauholding AG, which belongs to the parent company of ÖIAG.
In 1995, VAI was unhinged from voestalpine AG and became a 100% subsidiary of the new VA Technologie AG (short: VA Tech). VA Tech had emerged from the diversified group of Austrian Industries and was incorporated into the Siemens group in 2005. Werner Auer and Martin Krauss have led the company since 2009.
Siemens VAI specializes in the ready-to-use construction of production plants, technologies, and systems within the metallurgical sector. Solutions are offered throughout all stages of production, from ore to finished product, including mechanical supplies and electrics, automation, complete IT solutions as well as innovative services and modernization packages.
The core competences of Siemens VAI are to integrate these elements into large-scale projects (Turnkey
solutions). Products and solutions complying with latest environmental regulations and reducing emissions play an increasingly important role in the industry. Siemens VAI provides these solutions by offering ready-to-use plants complying with latest standards in the areas of electrics, automation and environmental technologies.
More than 500 manufacturers of metallurgical products, representing 70 percent of global steel production, are among the company’s costumers. The company itself is not listed on the stock exchange, since it is a 100% subsidiary of Siemens AG
.
Sintering, smelting reduction, steel production, endless strip production (ESP), cold rolling and hot rolling mills, automation solutions for iron and steel production;
Solutions for metal and mining, support center; solutions for rolling and coke making processes;
Blast furnaces, hot, cold and foil rolling mills;
Wire, rod and section rolling mills, strand guide rollers;
Electric arc furnaces, ladle furnaces, vacuum degassing plants and supplies;
Pickling plants and annealing lines, painting lines, galvanizing and tinning lines;
Wire, rod and section rolling mills, strand guide rollers.
• Integrated mills
• Minimills
• Coking plants
• Sinter and pellet plants
• Blast furnaces
• Corex® and Finex ironmaking plants
• Direct reduction plants
• LD (BOF) steelmaking plants
• Stainless steelmaking plants
• EAF steelmaking plants
• Secondary metallurgical facilities
• Continuous casting plants • Arvedi ESP plants (Endless Strip Production)
• Plate and Steckel mills
• Hot-strip rolling mills
• Cold-rolling mills
• Pickling plants
• Aluminum rolling mills
• Bar, wire rod, section and rail mills
• Strip-processing and finishing lines
• Environmental plants
• Automation systems
• Metallurgical, consulting and financial services
The Intensive Mixing and Granulation System from Siemens VAI, which consists of a high-speed intensive mixer and horizontal granulation drum, allows a thoroughly homogeneous sinter raw mix to be achieved. This is the basis for the production of high sinter quality and a stable sintering process. A much higher portion of ultra-fine ores (pellet feed) can be included in the sinter raw mix than in conventional mixing systems. This solution allows blending beds to be dispensed with altogether, significantly reducing raw material storage and handling costs.
A new intensive-cooling system for hot-strip mills, known as Power Cooling, allows accelerated strip-cooling rates as high as 400 K/s to be achieved. This solution is ideal for the production of high- and highest-strength steels with thicknesses up to approximately one inch (2.5 cm). The Power Cooling system was implemented for the first time in the Hot-Strip Mill No. 2 of ThyssenKrupp
in Duisburg-Beeckerwerth, Germany
in early 2011.
Voest-Alpine Industrieanlagenbau
Voest-Alpine Industrieanlagenbau Gmbh & Co. was an engineering, equipment and construction company based in Linz, Austria and had its American headquarters in Pittsburgh, Pennsylvania...
) based in Linz, Austria, is an engineering and plant building company for the iron and steel industry, for the flat-rolling sector of the aluminum industry and for open cast mining. It is one of the branches of Siemens Industrial Solutions and focuses on metallurgical services.
1938 to 1945
The history of Siemens VAI is closely linked to the first construction of industrial plants. The English company Brassert & Co began to build the metallurgical plant in Linz in 1938. After the beginning of World War II in 1939, the metallurgical division of Reichswerke Hermann GöringReichswerke Hermann Göring
Reichswerke Hermann Göring was an industrial conglomerate of Nazi Germany. It was established in July 1937 to extract and process domestic iron ores from Salzgitter that were deemed uneconomical by the privately held steel mills...
continued with the construction, only to pass it on to the German Mining and Metallurgical association (DBHG) after a short time. The large-scale plant, which was originally planned for metallurgical purposes, was then modified for the arms industry.
1945 to 1956
After the air raids of the allied forces in July 1944, the entire facilities were severely damaged. By the end of the war, production had basically stopped. In July 1945, the “Alpine Montan AG Hermann Göring” plant was renamed to “Vereinigte Österreichische Eisen- und Stahlwerke” (VÖESTVoestalpine
Voestalpine AG is an international steel company based in Linz, Austria. The company is active in steel, automotive, railway systems, profilform and tool steel industries....
) (United Iron and Steel Plants).
For the plant’s reconstruction, some divisions were combined into the so-called “New Building Division”, designed to reconstruct the metallurgical plant in Linz. Thus, the most important metallurgical facilities could all be started up again by the year 1949: the coking plant, blast furnaces, SM-steel making plants (plant with Siemens-Martin-furnace, named after inventors) and heavy plate mills (mills producing plates of over 3 mm thickness). Many of the products were scarce commodities after the war. For this reason, the metallurgical plant was able to recover pretty soon, investing largely into the expansion of its own facilities. Due to the shortage of steel scrap, necessary for the operation of SM blast furnaces, the yearly steel mill capacities of 220,000 tons soon proved to be insufficient. The solution was a new manufacturing process: the LD-process (Linz-Donawitz-process), manufactured in house and commissioned in 1952 in Linz, and 1953 in Donawitz. The huge advantages of this process were cost-saving on the one hand (investment costs were only 65% and operation costs only 55% compared to the SM blast furnace), and larger production capacities on the other.
1956 to 1961
The invention of the LD process and experiences gained from the complete reconstruction after the war led to the first external large-scale commission in the area of industrial plant construction in Rourkela, India, in 1956. It was a great success. Thereafter, many commissions from different metallurgical plants on almost all continents followed. The construction of industrial plants in the steel mill sector soon grew further, with the addition of hot and cold rolling mills as well as the construction of blast furnaces and metallurgical plants’ additional facilities like granulation plants and dolomite plants.1961 to 1974
Due to the increasing amount of tasks, the New Construction Division had to be changed into “Industrial Construction and Plant Development” with a new focus on turnkey projects. 1964, VÖEST expanded their portfolio once more, this time with the construction of chemical plants, which soon reached a share of more than two thirds of the total turnover. Another milestone was the introduction of the continuous casting technology for the production of slabs. The huge amount of commissions and the increasing expansion of their own facilities led VÖEST to further increase their hot steel production from 2.3 to 3.1 million tons per year.During this time, the number of employees grew to approximately 4,000 people. An additional center of technology was built in Vienna and additional constructors from Austria as well as from other countries were flown in.
In 1973, the two nationalized iron and steel industries VÖEST and ALPINE merged together and became today’s famous voestalpine
Voestalpine
Voestalpine AG is an international steel company based in Linz, Austria. The company is active in steel, automotive, railway systems, profilform and tool steel industries....
. The organization was restructured into the areas of “metallurgical plants” (seven divisions) and “chemical plants” (two divisions).
1974 to 1985
When the oil crisis1973 oil crisis
The 1973 oil crisis started in October 1973, when the members of Organization of Arab Petroleum Exporting Countries or the OAPEC proclaimed an oil embargo. This was "in response to the U.S. decision to re-supply the Israeli military" during the Yom Kippur war. It lasted until March 1974. With the...
started in 1974, the metallurgical industry was severely affected in all parts of the world. The consequence was a significant decline in prices within the steel sector, which also affected the construction of plants. Still, the area of technology (industrial plant construction and ready-to-use industry) became increasingly important for the company. Thus, the metallurgical plant’s share of turnover was 80% in 1973 - however, in 1976, the share of the plant construction and ready-to-use industries already amounted to 45%. The company was faced with a lot of restructuring processes and new orientations, but also gained the largest projects ever. In the beginning of the 1980s, first steps were taken towards biotechnology, leading to the construction of a biomass utilization technology center in Linz. In order to adapt to market requirements, the construction of chemical plants also took further measures in the area of environmental protection.
A very important step in this area was the acquisition of Korf Engineering GesmbH as a 100% subsidiary, since it included the rights to the COREX process. Because of the continuous high amount of commissions, the effects of the steel crisis were mitigated. However, in 1985 the crisis exploded and in the previous years, political pressure had already been put on the nationalized company with regard to job security. Therefore, the company, which had meanwhile become a diversified group, suffered a record loss in 1984, amounting to a total of 25 billion Schillings.
1985 to present
In fall of 1986, the concept of VOEST-ALPINE NEU (VOEST ALPINE NEW) was introduced. This meant that the company now positioned itself as a market oriented technology company, which was based on the knowledge gained previously in the key area of steel. This concept should help the company to recover as quickly as possible. Established strong areas (quality and technology) and creative projects launched by employees were fostered in the construction of plants. Thus, COREX, horizontal continuous casting, and converter and electric furnace processes were further developed, and the electric arc furnace was introduced.Finally, in 1988, VOEST-ALPINE Industrieanlagenbau (VAI) became a proper GesmbH in the framework of the newly established Maschinen- und Anlagenbauholding AG, which belongs to the parent company of ÖIAG.
In 1995, VAI was unhinged from voestalpine AG and became a 100% subsidiary of the new VA Technologie AG (short: VA Tech). VA Tech had emerged from the diversified group of Austrian Industries and was incorporated into the Siemens group in 2005. Werner Auer and Martin Krauss have led the company since 2009.
Operations
Siemens VAI is represented in more than 40 countries and employs approximately 9,000 people. It is currently involved in projects of the iron and steel industry as well as the flat-rolling sector of the aluminum industry in more than 100 countries.Siemens VAI specializes in the ready-to-use construction of production plants, technologies, and systems within the metallurgical sector. Solutions are offered throughout all stages of production, from ore to finished product, including mechanical supplies and electrics, automation, complete IT solutions as well as innovative services and modernization packages.
The core competences of Siemens VAI are to integrate these elements into large-scale projects (Turnkey
Turnkey
A turn-key or a turn-key project is a type of project that is constructed by a developer and sold or turned over to a buyer in a ready-to-use condition.-Common usage:...
solutions). Products and solutions complying with latest environmental regulations and reducing emissions play an increasingly important role in the industry. Siemens VAI provides these solutions by offering ready-to-use plants complying with latest standards in the areas of electrics, automation and environmental technologies.
More than 500 manufacturers of metallurgical products, representing 70 percent of global steel production, are among the company’s costumers. The company itself is not listed on the stock exchange, since it is a 100% subsidiary of Siemens AG
Siemens AG
Siemens AG is a German multinational conglomerate company headquartered in Munich, Germany. It is the largest Europe-based electronics and electrical engineering company....
.
Locations
Apart from the headquarters in Linz, Austria, Siemens VAI has subsidiaries in Erlangen and Willstätt-Legelshurst (Germany), Great Britain, France, Italy and Worcester (MA, USA).- LinzLinzLinz is the third-largest city of Austria and capital of the state of Upper Austria . It is located in the north centre of Austria, approximately south of the Czech border, on both sides of the river Danube. The population of the city is , and that of the Greater Linz conurbation is about...
, Austria (Headquarters)
Sintering, smelting reduction, steel production, endless strip production (ESP), cold rolling and hot rolling mills, automation solutions for iron and steel production;
- ErlangenErlangenErlangen is a Middle Franconian city in Bavaria, Germany. It is located at the confluence of the river Regnitz and its large tributary, the Untere Schwabach.Erlangen has more than 100,000 inhabitants....
, Germany
Solutions for metal and mining, support center; solutions for rolling and coke making processes;
- ChristchurchChristchurch, DorsetChristchurch is a borough and town in the county of Dorset on the south coast of England. The town adjoins Bournemouth in the west and the New Forest lies to the east. Historically in Hampshire, it joined Dorset with the reorganisation of local government in 1974 and is the most easterly borough in...
, SheffieldSheffieldSheffield is a city and metropolitan borough of South Yorkshire, England. Its name derives from the River Sheaf, which runs through the city. Historically a part of the West Riding of Yorkshire, and with some of its southern suburbs annexed from Derbyshire, the city has grown from its largely...
, StocktonStockton, WarwickshireStockton is a village and civil parish, in the Stratford-on-Avon district of Warwickshire, England. In the 2001 census it had a population of 1,391. The village is located just to the east of the A426 road two miles north-east of Southam, and eight miles south-west of Rugby.Stockton's name was...
, United Kingdom
Blast furnaces, hot, cold and foil rolling mills;
- MarnateMarnateMarnate is a comune in the Province of Varese in the Italian region Lombardy, located about 30 km northwest of Milan and about 20 km south of Varese...
, Italy
Wire, rod and section rolling mills, strand guide rollers;
- Willstätt-LegelshurstWillstättWillstätt is a town in the district of Ortenau in Baden-Württemberg in Germany....
, DuisburgDuisburg- History :A legend recorded by Johannes Aventinus holds that Duisburg, was built by the eponymous Tuisto, mythical progenitor of Germans, ca. 2395 BC...
, Germany
Electric arc furnaces, ladle furnaces, vacuum degassing plants and supplies;
- MontbrisonMontbrison, LoireMontbrison is a commune in the Loire department in central France.The commune gives its name to the popular blue cheese Fourme de Montbrison which has been made in the region for centuries.-History:...
, Montigny-le-BretonneuxMontigny-le-BretonneuxMontigny-le-Bretonneux is a commune in the Yvelines department in the Île-de-France region in north-central France. It is located in the south-western suburbs of Paris from the center, in the "new town" of Saint-Quentin-en-Yvelines, of which it is the central and most populated...
, France
Pickling plants and annealing lines, painting lines, galvanizing and tinning lines;
- Worcester, MassachusettsWorcester, MassachusettsWorcester is a city and the county seat of Worcester County, Massachusetts, United States. Named after Worcester, England, as of the 2010 Census the city's population is 181,045, making it the second largest city in New England after Boston....
, USA
Wire, rod and section rolling mills, strand guide rollers.
Products and technologies
The following procedures and techniques are among the core competences of Siemens VAI Metals and Technologies.• Integrated mills
• Minimills
• Coking plants
• Sinter and pellet plants
• Blast furnaces
• Corex® and Finex ironmaking plants
• Direct reduction plants
• LD (BOF) steelmaking plants
• Stainless steelmaking plants
• EAF steelmaking plants
• Secondary metallurgical facilities
• Continuous casting plants • Arvedi ESP plants (Endless Strip Production)
• Plate and Steckel mills
• Hot-strip rolling mills
• Cold-rolling mills
• Pickling plants
• Aluminum rolling mills
• Bar, wire rod, section and rail mills
• Strip-processing and finishing lines
• Environmental plants
• Automation systems
• Metallurgical, consulting and financial services
Cokemaking
A new camera-based coke-oven monitoring system, referred to as Pumas (PUshing MAnagement System), contributes to improved productivity and safety in cokemaking. Various coke-oven criteria and parameters are measured, analyzed and documented during the coke-oven pushing sequence. The system also includes an optimized battery-machine positioning and interlocking system.Ironmaking/sintering
The Siemens VAI Selective Waste-Gas Recirculation system allows approximately 30% to 40% of the sinter offgas to recirculated back to the sintering process. The heat and CO content of the recirculated waste gas help reduce solid-fuel consumption. In addition to the positive impact on the sintering operations, the offgas volume directed to the stack is also lowered. This means that the dimensions of the downstream offgas-cleaning facilities can be reduced, leading to a decrease in the related installation and operational costs.The Intensive Mixing and Granulation System from Siemens VAI, which consists of a high-speed intensive mixer and horizontal granulation drum, allows a thoroughly homogeneous sinter raw mix to be achieved. This is the basis for the production of high sinter quality and a stable sintering process. A much higher portion of ultra-fine ores (pellet feed) can be included in the sinter raw mix than in conventional mixing systems. This solution allows blending beds to be dispensed with altogether, significantly reducing raw material storage and handling costs.
Meros
Meros (Maximized Emission Reduction Of Sintering) is a technology for the treatment of offgas from the sinter plant. In a series of process steps, dust, acidic gases and harmful metallic and organic components present in the sinter offgas are reduced to levels previously unattained in conventional offgas-treatment systems.Ironmaking/blast furnace
The new Simetal Gimbal Top is a burden-distribution system for blast furnaces.Ironmaking/Corex
In the Corex Process, non-coking coal is primarily used as the energy source and ore reductant for the production of liquid hot metal, substituting expensive coking coal. Operating costs and the environmental impact are therefore far lower compared to the conventional coke-oven, sinter-plant and blast-furnace production route.Ironmaking/Finex
The Finex Process, jointly developed by Posco and Siemens VAI, is a further development of the Corex Process. Hot metal is produced on the basis of low-cost iron-ore fines and non-coking coal. Production costs can be reduced by approximately 15% in comparison with the blast-furnace route. Environmental emissions are lower than in the conventional blast-furnace route because coking and sintering plants are not required.Steelmaking/electric steelmaking
The Ultimate EAF incorporates all of the latest performance-enhancement solutions from Siemens VAI to maximize furnace output and productivity. Tap-to-tap times are possible down to nearly 30 minutes.Steelmaking/LD (BOF) steelmaking
Vaicon Compact Link is a new converter suspension system from Siemens VAI which features two horizontal links and eight vertical lamellas to accommodate thermal deformations of the LD (BOF) converter and trunnion ring, is ideal where restricted space conditions prevail on the converter platform.Steelmaking and continuous casting
LiquiRob is a robotic system specifically developed by Siemens VAI to improve industrial safety in a steelworks environment, especially under dangerous conditions where liquid metal is being handled or processed . A wide variety of tasks, including temperature measurements and sampling of liquid steel in both EAF and LD (BOF) steel mills is automatically performed by LiquiRob and carefully monitored from the safety of the control room, thus considerably enhancing personnel safety.Continuous casting
To date, Siemens VAI has implemented two ultra-thick slab casters capable of casting slabs in thicknesses up to 400 mm at Qinhuangdao Shouqin Metal Material Co., Ltd., China, and at Posco Pohang Works in Korea. The installation of a wide range of advanced technological packages is the basis for the reliable production of sophisticated steel grades used in high-end downstream product applications.Plate rolling
With Mulpic plate-cooling technology, the capability for both accelerated cooling and direct quench cooling over a wide plate-thickness range is provided in a single on-line system. This reduces or eliminates the need for offline heat treatment.Casting-rolling
The Arvedi ESP (endless strip production) process at Acciaieria Arvedi SpA in Cremona, Italy features the production of hot-rolled strip directly from liquid steel in a continuous and uninterrupted process from thin-slab casting to product coiling. The decisive benefits include major energy savings achieved in rolling, the highly compact line length (180 m) and the high quality of the thin-gauge rolled products.Hot-strip mills
The Siroll Power Coiler is a new generation of downcoilers developed by Siemens VAI that allows high-strength steels to be accurately and efficiently coiled over a wide range of strip thicknesses – from 1.2 mm up to 25.4 mm – at strip widths up to 2,800 mm.A new intensive-cooling system for hot-strip mills, known as Power Cooling, allows accelerated strip-cooling rates as high as 400 K/s to be achieved. This solution is ideal for the production of high- and highest-strength steels with thicknesses up to approximately one inch (2.5 cm). The Power Cooling system was implemented for the first time in the Hot-Strip Mill No. 2 of ThyssenKrupp
ThyssenKrupp
ThyssenKrupp AG is a German multinational conglomerate corporation headquartered in Duisburg Essen, Germany. The corporation consists of 670 companies worldwide. While ThyssenKrupp is one of the world's largest steel producers, the company also provides components and systems for the automotive...
in Duisburg-Beeckerwerth, Germany
Germany
Germany , officially the Federal Republic of Germany , is a federal parliamentary republic in Europe. The country consists of 16 states while the capital and largest city is Berlin. Germany covers an area of 357,021 km2 and has a largely temperate seasonal climate...
in early 2011.