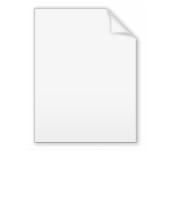
Semi-Solid Metal Casting
Encyclopedia
Semi-solid metal casting (SSM) is a near net shape
variant of die casting
. The process is used with non-ferrous metals, such as aluminium, copper, and magnesium. The process combines the advantages of casting
and forging
. The process is named after the fluid property thixotropy
, which is the phenomenon that allows this process to work. Simply, thixotropic fluids shear when the material flows, but thicken when standing. The potential for this type of process was first recognized in the early 1970s. There are four different processes: thixocasting, rheocasting, thixomolding, and SIMA.
SSM is done at a temperature that puts the metal between its liquidus and solidus
temperature. Ideally, the metal should be 30 to 65% solid. The metal must have a low viscosity to be usable, and to reach this low viscosity the material needs a globular primary surrounded by the liquid phase. The temperature range possible depends on the material and for aluminum alloys is 5-10oC, but for narrow melting range copper alloys can be only several tenths of a degree.
Semi-solid casting is typically used for high-end castings. For aluminum alloys typical parts include engine suspension mounts, air manifold sensor harness, engine blocks and oil pump filter housing.
With magnesium alloys, the most common process is thixomolding.
There are a large number of rheocasting processes that have been proposed over the past ten years or so, and they generally differ in the method used to generate the semi-solid slurry. 18 different rheocasting techniques were documented in a recent publication. The first commercial rheocasting process was the New Rheocasting Process (NRC) developed by Ube Industries
.
Due to the lower pressures and temperatures required to die cast semi-solid metal the die
material does not need to be as exotic. Often graphite
or softer stainless steel
s may be used. Even non-ferrous dies can be used for one time shots. Because of this the process can be applied to rapid prototyping
needs and mass production
. This also allows for the casting of high melting point metals, such as tool steel
and stellite
, if a higher temperature die material is used. Other advantages include: easily automated, consistent, production rates are equal to or better than die casting
rates, no air entrapment, low shrinkage
rates, and a uniform microstructure.
The disadvantages to SSM are: high cost of raw material due to a low number of suppliers, higher die development costs, and operators require a higher level of training. SSM cannot cast as complex or thin of parts as high-pressure die casting, however in thicker walled castings SSM has less porosity.
Near net shape
Near net shape is an industrial manufacturing technique. The name implies that the initial production of the item is very close to the final shape, reducing the need for surface finishing...
variant of die casting
Die casting
Die casting is a metal casting process that is characterized by forcing molten metal under high pressure into a mold cavity. The mold cavity is created using two hardened tool steel dies which have been machined into shape and work similarly to an injection mold during the process...
. The process is used with non-ferrous metals, such as aluminium, copper, and magnesium. The process combines the advantages of casting
Casting
In metalworking, casting involves pouring liquid metal into a mold, which contains a hollow cavity of the desired shape, and then allowing it to cool and solidify. The solidified part is also known as a casting, which is ejected or broken out of the mold to complete the process...
and forging
Forging
Forging is a manufacturing process involving the shaping of metal using localized compressive forces. Forging is often classified according to the temperature at which it is performed: '"cold," "warm," or "hot" forging. Forged parts can range in weight from less than a kilogram to 580 metric tons...
. The process is named after the fluid property thixotropy
Thixotropy
Thixotropy is the property of certain gels or fluids that are thick under normal conditions, but flow over time when shaken, agitated, or otherwise stressed...
, which is the phenomenon that allows this process to work. Simply, thixotropic fluids shear when the material flows, but thicken when standing. The potential for this type of process was first recognized in the early 1970s. There are four different processes: thixocasting, rheocasting, thixomolding, and SIMA.
SSM is done at a temperature that puts the metal between its liquidus and solidus
Solidus
Solidus may refer to:*Solidus , the "⁄" grammatical punctuation character, also used in mathematics*Slash a sign, "/" used as a punctuation mark and for various other purposes...
temperature. Ideally, the metal should be 30 to 65% solid. The metal must have a low viscosity to be usable, and to reach this low viscosity the material needs a globular primary surrounded by the liquid phase. The temperature range possible depends on the material and for aluminum alloys is 5-10oC, but for narrow melting range copper alloys can be only several tenths of a degree.
Semi-solid casting is typically used for high-end castings. For aluminum alloys typical parts include engine suspension mounts, air manifold sensor harness, engine blocks and oil pump filter housing.
Processes
There are a number of different techniques to produce semi-solid castings. For aluminum alloys the more common processes are thixocasting and rheocasting. Other process such as strain induced melt activation (SIMA) and RAP can also be used with aluminum alloys, although are less common commercially.With magnesium alloys, the most common process is thixomolding.
Thixocasting
Thixocasting utilizes a pre-cast billet with a non-dendritic microstructure that is normally produced by vigorously stirring the melt as the bar is being cast. Induction heating is normally used to re-heat the billets to the semi-solid temperature range, and die casting machines are used to inject the semi-solid material into hardened steels dies. Thixocasting is being performed commercially in North America, Europe and Asia. Thixocasting has the ability to produce extremely high quality components due to the product consistency that results from using pre-cast billet that is manufactured under the same ideal continuous processing conditions that are employed to make forging or rolling stock. The main disadvantage is that it is expensive due to the special billets that must be used. Other disadvantages include a limited number of alloys, and scrap cannot be directly reused.Rheocasting
Unlike thixocasting, which re-heats a billet, rheocasting develops the semi-solid slurry from the molten metal produced in a typical die casting furnace/machine. This is a big advantage over thixocasting because it results in less expensive feedstock, in the form of typical die casting alloys, and allows for direct recycling.There are a large number of rheocasting processes that have been proposed over the past ten years or so, and they generally differ in the method used to generate the semi-solid slurry. 18 different rheocasting techniques were documented in a recent publication. The first commercial rheocasting process was the New Rheocasting Process (NRC) developed by Ube Industries
Ube Industries
is a Japanese chemical company.-Chemicals and plastics:*Caprolactam*Polyamide*Synthetic rubber*Ammonia*Acrylonitrile butadiene styrene*Polyethylene-Speciality chemicals and products:*Liquid electrolyte*Diol*dimethyl carbonate*Polyimide...
.
Thixomolding
For magnesium alloys, thixomolding uses a machine similar to injection molding. In a single step process, room temperature magnesium alloy chips are fed into the back end of a heated barrel through a volumetric feeder. The barrel is maintained under an argon atmosphere to prevent oxidation of the magnesium chips. A screw feeder located inside the barrel feeds the magnesium chips forward as they are heated into the semi-solid temperature range. The screw rotation provides the necessary shearing force to generate the globular structure needed for semi-solid casting. Once enough slurry has accumulated, the screw moves forward to inject the slurry into a steel die.SIMA
In the SIMA method the material is first heated to the SMM temperature. As it nears the solidus temperature the grains recrystallize to form a fine grain structure. After the solidus temperature is passed the grain boundaries melt to form the SSM microstructure. For this method to work the material should be extruded or cold rolled in the half-hard tempered state. This method is limited in size to bar diameters smaller than 37 mm (1.5 in); because of this only smaller parts can be cast.Advantages and disadvantages
The advantages of semi-solid casting are as follows:- Complex parts produced net shape
- Porosity free
- Excellent mechanical performance
- Pressure tightness
- Tight tolerances
- Thin walls
- Heat treatable (T4/T5/T6)
Due to the lower pressures and temperatures required to die cast semi-solid metal the die
Die (manufacturing)
A die is a specialized tool used in manufacturing industries to cut or shape material using a press. Like molds, dies are generally customized to the item they are used to create...
material does not need to be as exotic. Often graphite
Graphite
The mineral graphite is one of the allotropes of carbon. It was named by Abraham Gottlob Werner in 1789 from the Ancient Greek γράφω , "to draw/write", for its use in pencils, where it is commonly called lead . Unlike diamond , graphite is an electrical conductor, a semimetal...
or softer stainless steel
Stainless steel
In metallurgy, stainless steel, also known as inox steel or inox from French "inoxydable", is defined as a steel alloy with a minimum of 10.5 or 11% chromium content by mass....
s may be used. Even non-ferrous dies can be used for one time shots. Because of this the process can be applied to rapid prototyping
Rapid prototyping
Rapid prototyping is the automatic construction of physical objects using additive manufacturing technology. The first techniques for rapid prototyping became available in the late 1980s and were used to produce models and prototype parts. Today, they are used for a much wider range of applications...
needs and mass production
Mass production
Mass production is the production of large amounts of standardized products, including and especially on assembly lines...
. This also allows for the casting of high melting point metals, such as tool steel
Tool steel
Tool steel refers to a variety of carbon and alloy steels that are particularly well-suited to be made into tools. Their suitability comes from their distinctive hardness, resistance to abrasion, their ability to hold a cutting edge, and/or their resistance to deformation at elevated temperatures...
and stellite
Stellite
Stellite alloy is a range of cobalt-chromium alloys designed for wear resistance. It may also contain tungsten or molybdenum and a small but important amount of carbon...
, if a higher temperature die material is used. Other advantages include: easily automated, consistent, production rates are equal to or better than die casting
Die casting
Die casting is a metal casting process that is characterized by forcing molten metal under high pressure into a mold cavity. The mold cavity is created using two hardened tool steel dies which have been machined into shape and work similarly to an injection mold during the process...
rates, no air entrapment, low shrinkage
Shrinkage
Shrinkage has multiple meanings, depending on the context.* Shrinkage – the loss of products* Shrinkage – a technique to improve an estimator* Shrinkage – a common problem when doing laundry...
rates, and a uniform microstructure.
The disadvantages to SSM are: high cost of raw material due to a low number of suppliers, higher die development costs, and operators require a higher level of training. SSM cannot cast as complex or thin of parts as high-pressure die casting, however in thicker walled castings SSM has less porosity.